What Is A Gasket

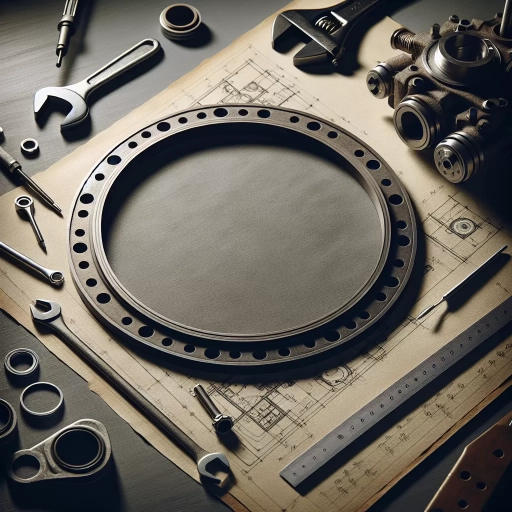
In the realm of engineering and manufacturing, few components are as crucial yet often overlooked as the humble gasket. A gasket is a vital seal that ensures the integrity and performance of various mechanical systems, from industrial machinery to automotive engines. But what exactly is a gasket, and how does it function? This article delves into the fundamental nature of gaskets, exploring their definition and construction in the section "What is a Gasket?" It then examines how gaskets operate to provide a tight seal in different applications, as detailed in "How Gaskets Function." Finally, it highlights the importance and benefits of gaskets in maintaining system efficiency, safety, and longevity, discussed in "Importance and Benefits of Gaskets." By understanding these aspects, readers will gain a comprehensive insight into the role gaskets play in modern technology. Let's begin by answering the most basic yet essential question: What is a Gasket?
What is a Gasket?
In the realm of engineering and manufacturing, precision and reliability are paramount, and one crucial component that ensures these standards are met is the gasket. A gasket is a vital seal that prevents leaks and maintains the integrity of various systems, from industrial machinery to automotive engines. To fully understand the significance of gaskets, it is essential to delve into their definition and purpose, which highlights their role in maintaining system efficiency and safety. Additionally, exploring the diverse types of gaskets available reveals how they are tailored to meet specific needs across different industries. Finally, examining the materials used in gasket construction provides insight into their durability and performance under various conditions. By understanding these aspects, we can appreciate the critical function gaskets play in modern technology. So, what is a gasket?
Definition and Purpose
A gasket is a critical component in various mechanical and industrial applications, serving as a seal between two or more mating surfaces to prevent leakage of fluids, gases, or other substances. The **definition** of a gasket is straightforward: it is a ring or sheet of material, typically made from rubber, metal, or composite materials, designed to fill the microscopic irregularities on the surfaces it contacts. This ensures a tight seal that maintains the integrity of the system, whether it be in automotive engines, industrial pipelines, or even household appliances. The **purpose** of a gasket is multifaceted and essential for the proper functioning of many systems. Primarily, it acts as a barrier to prevent the escape or entry of substances such as oils, fuels, gases, and chemicals. This not only maintains system efficiency but also ensures safety by preventing potential hazards like leaks of toxic substances or flammable gases. Additionally, gaskets help in reducing noise and vibration by providing a cushioning effect between moving parts, thereby enhancing the overall performance and longevity of the machinery. In engineering terms, gaskets are often classified based on their material composition and application. For instance, rubber gaskets are commonly used in low-pressure applications due to their flexibility and sealing properties, while metal gaskets are preferred in high-pressure environments where durability and strength are paramount. Composite gaskets, combining different materials like graphite and stainless steel, offer a balance between flexibility and strength, making them versatile for various industrial uses. The importance of gaskets extends beyond their functional role; they also play a significant part in cost savings and environmental protection. By preventing leaks, gaskets help in conserving resources and reducing waste. For example, in oil refineries, gaskets ensure that valuable petroleum products are not lost during processing, thereby optimizing production efficiency. Similarly, in environmental contexts, gaskets help in containing hazardous materials within designated systems, preventing contamination of soil and water. In summary, the definition and purpose of a gasket underscore its critical role in maintaining system integrity, ensuring safety, and optimizing performance across diverse applications. Whether in industrial settings or everyday devices, gaskets are indispensable components that contribute significantly to operational reliability and efficiency. Understanding the definition and purpose of gaskets is crucial for engineers, technicians, and users alike to appreciate their importance and select the appropriate type for specific needs.
Types of Gaskets
Gaskets are versatile sealing components used in various industries to prevent leaks and ensure the integrity of joints and connections. There are several types of gaskets, each designed to meet specific requirements based on the application, environment, and materials involved. **Metal Gaskets** are robust and often used in high-pressure and high-temperature applications. They can be further categorized into spiral-wound gaskets, which combine a metal strip with a filler material, and ring-type joint gaskets, which are solid metal rings used in oil and gas pipelines. **Non-Metallic Gaskets**, on the other hand, are made from materials such as rubber, Teflon, or graphite. These gaskets are more flexible and suitable for lower pressure applications but offer excellent chemical resistance and are easier to install. **Compressed Fiber Gaskets** are another common type, made from compressed fibers like asbestos or synthetic materials. They are widely used due to their good balance of cost and performance but may not be suitable for high-temperature or high-pressure environments. **Cork Gaskets** are known for their compressibility and are often used in automotive and industrial applications where a soft seal is required. **Graphite Gaskets** are highly resistant to heat and chemicals, making them ideal for use in power plants and chemical processing facilities. **Teflon Gaskets** offer superior chemical resistance and are commonly used in pharmaceutical and food processing industries where purity is critical. **Spiral-Wound Gaskets** combine a metal strip with a filler material, providing a strong seal that can withstand high pressures and temperatures. These gaskets are versatile and can be used in a wide range of applications, from petrochemical plants to power generation facilities. **Kammprofile Gaskets** feature a serrated metal core with a soft filler material, offering a balance between the strength of metal and the sealing capabilities of non-metallic materials. They are particularly useful in applications requiring a high level of sealing integrity. In addition to these types, **Sheet Gaskets** are made from flat sheets of material such as rubber or Teflon and are cut to size for specific applications. They are easy to install and can be used in various industries including plumbing and HVAC systems. **O-Ring Gaskets** are circular in shape and made from elastomers like rubber or silicone; they are widely used in hydraulic systems and other applications requiring a reliable seal under pressure. Each type of gasket has its unique characteristics, advantages, and limitations, making it crucial to select the right gasket for the specific needs of an application to ensure optimal performance and longevity. Understanding the different types of gaskets allows engineers and technicians to make informed decisions that enhance the efficiency and safety of their systems.
Materials Used
When discussing what a gasket is, it is crucial to delve into the materials used in their construction, as these materials significantly influence the gasket's performance, durability, and suitability for various applications. Gaskets are typically made from a variety of materials, each chosen for its unique properties that cater to different operational conditions. **Rubber** is one of the most common materials used due to its excellent sealing capabilities, flexibility, and resistance to compression. Natural rubber and synthetic rubbers like nitrile, EPDM (ethylene propylene diene monomer), and silicone are popular choices, with each offering distinct advantages such as chemical resistance, temperature tolerance, and ozone resistance. **Graphite** gaskets are another prevalent option, particularly in high-temperature applications. Graphite's non-reactive nature and ability to maintain its integrity under extreme heat make it ideal for use in steam engines, turbines, and other high-temperature environments. **Metallic gaskets**, often made from materials like stainless steel or copper, are used in high-pressure and high-temperature applications where the sealing requirements are stringent. These gaskets can be further classified into types such as spiral wound gaskets and metal jacketed gaskets, each designed to handle specific pressure and temperature ranges. **Compressed fiber gaskets**, composed of a mixture of fibers (like aramid or cellulose) bound together with a rubber or synthetic binder, offer a balance between flexibility and durability. These gaskets are versatile and can be used in a wide range of industries including automotive, aerospace, and industrial machinery. **PTFE (Polytetrafluoroethylene) gaskets** are known for their chemical inertness and non-stick properties, making them suitable for applications involving corrosive substances. Additionally, **Ceramic gaskets** are used in extreme environments where other materials would fail due to their high thermal resistance and chemical stability. The choice of material for a gasket depends on the specific requirements of the application, including factors such as operating temperature, pressure, chemical compatibility, and the need for flexibility or rigidity. Understanding these material properties is essential for selecting the right gasket to ensure reliable sealing performance and longevity in various industrial settings. By leveraging the unique characteristics of different materials, gaskets can effectively seal joints and prevent leaks in everything from simple plumbing systems to complex industrial machinery. This versatility underscores the importance of material selection in gasket design and highlights why gaskets remain an indispensable component across diverse industries.
How Gaskets Function
Gaskets are crucial components in various mechanical and industrial systems, playing a vital role in ensuring the integrity and efficiency of operations. These versatile seals are designed to fill the microscopic gaps between two mating surfaces, preventing leaks and maintaining pressure. The functionality of gaskets hinges on several key aspects. First, their sealing mechanism is fundamental to their performance, as it determines how effectively they can prevent fluid or gas leakage. Second, gaskets must possess robust pressure and temperature resistance to withstand the harsh conditions of their operating environments. Finally, their diverse applications span across multiple industries, from automotive and aerospace to chemical processing and construction. Understanding these facets is essential for appreciating the importance of gaskets in modern engineering. In this article, we will delve into the intricacies of how gaskets function, exploring their sealing mechanism, pressure and temperature resistance, and common applications. But before we dive into these details, let's start with the basics: **What is a Gasket?**
Sealing Mechanism
The sealing mechanism of a gasket is a critical component in ensuring the integrity and functionality of various mechanical systems. At its core, a gasket functions by creating a tight seal between two surfaces, preventing the leakage of fluids, gases, or other substances. This is achieved through a combination of material properties and design features. When a gasket is compressed between two mating surfaces, it undergoes deformation, allowing it to fill in microscopic irregularities on the surfaces. This deformation ensures that the gasket material conforms closely to the surface topography, thereby creating an effective barrier against leakage. The material chosen for the gasket must have sufficient compressibility and resilience to maintain this seal over time and under varying conditions such as temperature and pressure fluctuations. The sealing mechanism also relies on the principle of surface contact pressure. As the gasket is compressed, it generates a significant contact pressure at the interface with the mating surfaces. This pressure helps to ensure that any potential pathways for leakage are sealed off effectively. Additionally, some gaskets incorporate specialized features like serrations or embossments that enhance the sealing performance by increasing the surface area in contact and providing additional mechanical interlocking. Moreover, the choice of gasket material plays a pivotal role in determining its sealing efficacy. Materials such as rubber, silicone, and various types of polymers are commonly used due to their excellent elasticity and resistance to chemicals. For high-temperature applications, metallic gaskets or those made from advanced composites may be employed to withstand extreme conditions without compromising the seal. In dynamic systems where movement or vibration is present, the sealing mechanism must also account for these factors. Here, gaskets with built-in flexibility or those designed with specific geometries can adapt to changing conditions while maintaining their sealing integrity. In summary, the sealing mechanism of a gasket is a sophisticated interplay of material science, design engineering, and mechanical principles. By understanding how gaskets function through their ability to deform, generate contact pressure, and adapt to various conditions, engineers can select and implement gaskets that provide reliable seals in a wide range of applications. This ensures optimal performance, safety, and efficiency in everything from industrial machinery to automotive systems and beyond.
Pressure and Temperature Resistance
Pressure and temperature resistance are crucial factors in the functionality and longevity of gaskets, which are essential components in various mechanical and industrial applications. Gaskets are designed to seal gaps between two surfaces, preventing the escape of fluids or gases and ensuring the integrity of the system. The ability of a gasket to withstand pressure and temperature variations is paramount for maintaining this seal. **Pressure Resistance:** Gaskets must be capable of withstanding the pressure exerted by the fluids or gases they are sealing. This involves resisting both static and dynamic pressures. Static pressure is the constant force exerted on the gasket when the system is at rest, while dynamic pressure fluctuates due to operational conditions such as flow rates and system vibrations. Materials like rubber, PTFE (Teflon), and graphite are commonly used for gaskets because they offer excellent compressibility and resilience, allowing them to maintain their sealing properties under varying pressures. For high-pressure applications, gaskets may be reinforced with metal or fiber inserts to enhance their strength and durability. **Temperature Resistance:** Temperature resistance is equally important as it affects the material properties of the gasket. Different materials have different temperature limits beyond which they may degrade or lose their sealing capabilities. For instance, rubber gaskets are suitable for temperatures up to around 200°C (392°F), while PTFE gaskets can handle temperatures up to 250°C (482°F). Graphite gaskets, on the other hand, can withstand even higher temperatures, often used in high-temperature applications such as steam engines and chemical processing equipment. The choice of material depends on the specific operating conditions of the system, ensuring that the gasket remains effective across the entire temperature range. **Combined Effects:** In many applications, gaskets are subjected to both pressure and temperature variations simultaneously. This combined stress can significantly impact the performance and lifespan of the gasket. For example, in automotive engines, gaskets must seal combustion chambers where pressures are high and temperatures can exceed 500°C (932°F). Here, specialized materials like metal gaskets with graphite or mica inserts are used due to their superior thermal stability and mechanical strength. Similarly, in chemical plants, gaskets may need to resist corrosive substances at elevated temperatures, necessitating the use of chemically inert materials like PTFE or fluorinated elastomers. **Conclusion:** The ability of a gasket to resist pressure and temperature is fundamental to its function. By selecting materials that are appropriate for the specific operating conditions, engineers can ensure reliable sealing performance over time. This not only maintains system integrity but also prevents leaks that could lead to safety hazards, environmental damage, or equipment failure. Understanding these factors is essential for designing and selecting gaskets that meet the demands of various industrial and mechanical applications.
Common Applications
Gaskets are versatile components that find widespread application across various industries due to their critical role in sealing and ensuring the integrity of mechanical systems. In the automotive sector, gaskets are essential for maintaining the performance and longevity of engines. For instance, head gaskets seal the combustion chamber, preventing coolant and oil leaks that could lead to engine failure. Similarly, intake manifold gaskets ensure proper airflow and fuel mixture, while exhaust gaskets prevent harmful emissions from escaping into the environment. In industrial settings, gaskets are used in piping systems to seal flanges and prevent fluid leaks, which is crucial for maintaining safety and efficiency in processes involving chemicals, gases, and high-pressure fluids. In the aerospace industry, gaskets play a vital role in sealing critical components such as fuel tanks, hydraulic systems, and engine compartments. Here, they must withstand extreme temperatures and pressures, making them a key factor in ensuring the reliability and safety of aircraft operations. In construction and HVAC (heating, ventilation, and air conditioning) systems, gaskets are used to seal joints in ductwork and piping, preventing air leaks that could compromise system efficiency and indoor air quality. Additionally, in medical devices and equipment, gaskets are used to create sterile environments by sealing components that come into contact with bodily fluids or pharmaceuticals. The marine industry also relies heavily on gaskets to seal engines, pumps, and other machinery exposed to corrosive seawater environments. These gaskets must be made from materials resistant to corrosion and able to withstand the constant exposure to moisture. Furthermore, in consumer products such as refrigerators and washing machines, gaskets help maintain internal pressures and prevent leaks that could lead to product failure or safety hazards. The diversity of applications underscores the importance of selecting the right type of gasket material for each specific use case. Different materials like rubber, silicone, Teflon, and metal-reinforced gaskets offer varying degrees of durability, chemical resistance, and thermal stability. Understanding these properties is crucial for engineers and technicians to ensure that gaskets function optimally under different operating conditions. Overall, the widespread use of gaskets highlights their indispensable role in maintaining system integrity across a broad spectrum of industries and applications.
Importance and Benefits of Gaskets
In the realm of industrial and mechanical engineering, gaskets play a pivotal role in ensuring the integrity and performance of various systems. These versatile components are crucial for preventing leaks, enhancing operational efficiency, and reducing maintenance costs. The importance of gaskets cannot be overstated, as they provide a reliable seal between two surfaces, safeguarding against potential hazards and optimizing system performance. By preventing leaks, gaskets contribute significantly to safety protocols, protecting both personnel and equipment from damage. Additionally, their ability to maintain optimal pressure and temperature conditions enhances the overall efficiency of machinery, leading to improved productivity. Furthermore, gaskets help in reducing maintenance needs and associated costs by minimizing the risk of system failures and downtime. Understanding the multifaceted benefits of gaskets is essential for any industry relying on sealed systems. So, what exactly is a gasket?
Leak Prevention and Safety
Leak prevention and safety are paramount in various industrial, automotive, and residential applications, where the integrity of seals is crucial for maintaining operational efficiency, ensuring environmental protection, and safeguarding human health. Gaskets play a pivotal role in this context by providing a reliable seal between two surfaces, thereby preventing the escape of fluids, gases, or other substances. The importance of leak prevention cannot be overstated; leaks can lead to significant economic losses due to wasted resources, increased maintenance costs, and potential downtime. Moreover, leaks involving hazardous materials can pose serious environmental and health risks. For instance, in chemical processing plants, a leak could result in the release of toxic substances into the atmosphere or waterways, causing harm to both human populations and ecosystems. In addition to economic and environmental concerns, safety is a critical factor. Leaks in high-pressure systems or those involving flammable gases can lead to catastrophic failures, including explosions or fires. In such scenarios, gaskets serve as the first line of defense against these risks by ensuring that all connections are secure and leak-free. The benefits of using high-quality gaskets extend beyond mere functionality; they also contribute to compliance with regulatory standards and industry best practices. For example, in the aerospace industry, gaskets must meet stringent specifications to ensure the safety and reliability of aircraft systems. The selection of appropriate gasket materials is also vital for effective leak prevention. Different materials offer varying degrees of resistance to chemicals, temperature extremes, and pressure conditions. For instance, silicone gaskets are often used in applications requiring high temperature resistance, while PTFE (polytetrafluoroethylene) gaskets are chosen for their excellent chemical inertness. By choosing the right gasket material for a specific application, users can significantly reduce the risk of leaks and associated safety hazards. Furthermore, regular inspection and maintenance of gaskets are essential components of a comprehensive leak prevention strategy. Over time, gaskets can deteriorate due to wear and tear, exposure to harsh conditions, or improper installation. Periodic checks help identify potential issues before they escalate into major problems. This proactive approach not only enhances safety but also optimizes system performance and extends the lifespan of equipment. In conclusion, leak prevention and safety are interwoven with the importance and benefits of gaskets. By providing a reliable seal, gaskets safeguard against economic losses, environmental damage, and safety risks. Their role in maintaining operational integrity underscores their critical importance across diverse industries. As such, investing in high-quality gaskets and adhering to best practices in their selection, installation, and maintenance is indispensable for ensuring robust leak prevention measures that protect both people and the environment.
Enhanced Performance and Efficiency
Enhanced performance and efficiency are pivotal benefits that gaskets provide in various industrial and mechanical applications. By ensuring a tight seal between two surfaces, gaskets prevent leaks and maintain the integrity of systems, which is crucial for optimal functioning. In high-pressure environments such as those found in chemical processing, oil and gas, and power generation, gaskets play a critical role in preventing fluid or gas leaks that could lead to system failures, safety hazards, and environmental damage. The precision sealing offered by gaskets also helps in maintaining consistent pressure levels, which is essential for efficient operation of machinery and equipment. For instance, in automotive engines, gaskets ensure that combustion chambers are sealed properly, enhancing fuel efficiency and reducing emissions. Similarly, in HVAC systems, gaskets help in maintaining the desired temperature by preventing air leaks, thereby improving the overall efficiency of heating and cooling processes. Moreover, the use of high-quality gaskets can significantly extend the lifespan of equipment by protecting against corrosion and wear. By creating a barrier between two surfaces, gaskets prevent direct contact that could lead to friction and subsequent damage. This not only reduces maintenance costs but also minimizes downtime, allowing for continuous operation without interruptions. Additionally, gaskets made from advanced materials such as silicone, PTFE, or graphite offer superior resistance to extreme temperatures, chemicals, and other harsh conditions, further enhancing their performance and durability. The versatility of gaskets also allows them to be customized for specific applications, ensuring that they meet the unique demands of different industries. For example, in food processing, gaskets must comply with stringent hygiene standards to prevent contamination, while in aerospace, they must withstand extreme temperatures and pressures. In summary, the enhanced performance and efficiency provided by gaskets are indispensable in modern industrial settings. By ensuring tight seals, preventing leaks, and protecting against wear and corrosion, gaskets contribute significantly to the reliability and longevity of machinery and systems. Their ability to operate under diverse conditions makes them an essential component across various sectors, driving operational efficiency and safety while reducing costs associated with maintenance and downtime. As technology continues to evolve, the development of advanced gasket materials and designs will further enhance their performance capabilities, making them even more critical for achieving optimal efficiency in industrial operations.
Maintenance and Cost Savings
**Maintenance and Cost Savings** The importance of gaskets extends beyond their primary function of sealing and protecting equipment; they also play a crucial role in maintenance and cost savings. Properly installed and maintained gaskets can significantly reduce downtime, extend the lifespan of machinery, and lower operational expenses. For instance, a well-sealed gasket prevents leaks, which can lead to costly repairs and replacements if left unchecked. Leaks not only result in the loss of valuable resources such as fluids or gases but also pose safety risks and environmental hazards. By ensuring that gaskets are in good condition, industries can avoid these issues, thereby reducing the need for frequent maintenance interventions. Moreover, gaskets contribute to energy efficiency. In applications like HVAC systems or industrial processes, gaskets help maintain optimal operating conditions by preventing heat or cold loss. This efficiency translates into lower energy consumption, which directly impacts the bottom line by reducing utility bills. Additionally, the use of high-quality gaskets minimizes the risk of equipment failure due to overheating or overcooling, further reducing maintenance costs. Regular inspection and replacement of gaskets are key to maintaining optimal performance. Scheduled maintenance programs that include gasket checks can help identify potential issues before they escalate into major problems. This proactive approach not only saves money on emergency repairs but also ensures that production processes remain uninterrupted, thereby preserving productivity and revenue. In terms of cost savings, the longevity of gaskets is another significant factor. High-quality gaskets made from durable materials can withstand harsh operating conditions for extended periods, reducing the frequency of replacements. This longevity not only saves on the direct cost of new gaskets but also minimizes labor costs associated with replacement procedures. Furthermore, the selection of the right type of gasket for specific applications can optimize performance and reduce costs. For example, using a gasket material that is resistant to chemical corrosion in chemical processing plants can prevent premature failure and the associated maintenance costs. Similarly, in high-temperature applications, selecting a gasket that can withstand extreme temperatures ensures continuous operation without frequent replacements. In summary, gaskets are not just passive components; they are integral to maintaining efficient, safe, and cost-effective operations across various industries. By ensuring that gaskets are properly installed, maintained, and replaced as needed, businesses can achieve significant cost savings while enhancing overall operational reliability and efficiency. This underscores the importance of gaskets as a critical component in any mechanical system, highlighting their role in supporting both immediate and long-term financial health.