What Is Milling

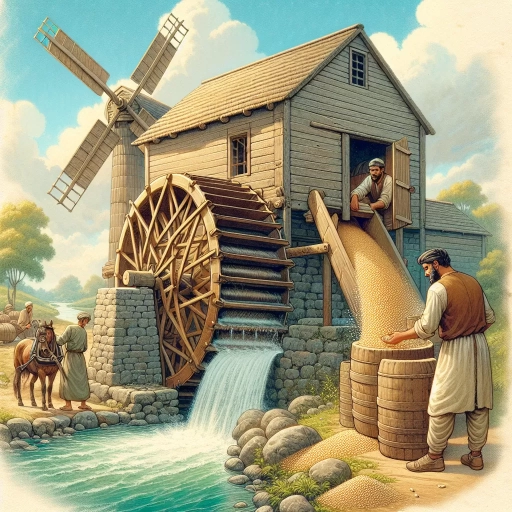
Milling, a fundamental process in various industries, involves the removal of material from a workpiece using rotary cutters. This versatile technique is crucial for shaping and refining materials to precise specifications, making it an indispensable part of manufacturing, engineering, and construction. The article delves into the multifaceted world of milling, beginning with an **Introduction to Milling**, where we explore the basic principles and historical development of this process. We then examine **Milling Techniques and Technologies**, highlighting the advancements and innovations that have transformed the field. Finally, we discuss **Applications and Benefits of Milling**, revealing how this process contributes to diverse sectors and enhances product quality. By understanding these aspects, readers will gain a comprehensive insight into the significance and functionality of milling. Let us start by diving into the foundational aspects of this critical process with an **Introduction to Milling**.
Introduction to Milling
Milling, a fundamental process in manufacturing and engineering, has been a cornerstone of industrial development for centuries. This versatile technique involves the removal of material from a workpiece using rotating cutting tools, resulting in precise and intricate designs. To fully appreciate the significance of milling, it is essential to delve into its rich history and evolution, which will be explored in the **Definition and History of Milling** section. Understanding the origins and development of milling provides a solid foundation for grasping its current applications. Additionally, milling encompasses various processes, each tailored to specific needs and materials, as detailed in the **Types of Milling Processes** section. These diverse methods highlight the adaptability and efficiency of milling in different contexts. Furthermore, the importance of milling extends across multiple industries, from aerospace to automotive and beyond, as discussed in the **Importance in Various Industries** section. By examining these aspects, we can gain a comprehensive understanding of how milling continues to shape modern manufacturing. Let us begin by exploring the **Definition and History of Milling**, which sets the stage for understanding the breadth and depth of this critical industrial process.
Definition and History of Milling
**Definition and History of Milling** Milling, a fundamental process in various industries, involves the mechanical cutting of a material using a rotating cutting tool to remove material by advancing a cutter into a workpiece. This precise and controlled method allows for the creation of complex shapes and surfaces with high accuracy. The history of milling dates back to ancient civilizations, where primitive forms of milling were used to shape and polish stones and metals. In ancient Egypt around 1300 BCE, evidence suggests that early forms of milling were employed to craft intricate stone carvings and tools. Similarly, in ancient Greece and Rome, milling techniques were refined to produce more sophisticated metalwork and architectural elements. However, these early methods were labor-intensive and lacked the precision that modern milling offers. The Industrial Revolution marked a significant turning point in the evolution of milling. With the invention of the first practical milling machine by Eli Whitney in 1818, milling became a cornerstone of industrial manufacturing. Whitney's machine, designed to produce interchangeable parts for muskets, introduced the concept of mass production and standardized components. This innovation paved the way for more advanced milling machines that could handle a variety of materials and operations. Throughout the 19th and 20th centuries, advancements in milling technology continued to accelerate. The introduction of CNC (Computer Numerical Control) milling machines in the mid-20th century revolutionized the field by enabling precise automation and programmable operations. CNC milling allowed for complex geometries and high-precision parts to be produced with minimal human intervention, significantly enhancing productivity and accuracy. Today, milling is a ubiquitous process across various sectors including aerospace, automotive, medical devices, and consumer goods. Modern milling machines are equipped with advanced features such as multi-axis capabilities, high-speed spindles, and sophisticated control systems. These advancements have expanded the scope of milling to include not only traditional metalworking but also the processing of plastics, composites, and other materials. The definition of milling has also evolved to encompass different types such as face milling, end milling, and slot milling, each designed for specific applications. Face milling involves cutting flat surfaces while end milling is used for creating slots or pockets. Slot milling focuses on making narrow grooves or slots in workpieces. These specialized techniques ensure that milling remains a versatile and essential tool in modern manufacturing. In conclusion, the history of milling is a testament to human ingenuity and technological progress. From its humble beginnings in ancient civilizations to its current status as a cornerstone of modern industry, milling continues to play a vital role in shaping our world. Understanding its definition and historical development provides a solid foundation for appreciating its significance and potential applications in contemporary manufacturing processes.
Types of Milling Processes
Milling, a fundamental process in manufacturing, involves the removal of material from a workpiece using rotating cutting tools. This versatile technique is essential for shaping and refining various materials, including metals, plastics, and wood. There are several types of milling processes, each tailored to specific applications and offering unique advantages. **1. Face Milling:** Face milling is one of the most common types of milling processes. It involves cutting the surface of a workpiece using a face mill, which has cutting edges on its periphery and sometimes on its face. This method is ideal for machining flat surfaces, such as the top or bottom of a part, and can be performed using either a horizontal or vertical milling machine. **2. Peripheral Milling:** Peripheral milling, also known as plain milling, uses the cutting edges on the periphery of the milling cutter to remove material. This process is widely used for machining flat surfaces, slots, and grooves. It can be further divided into up-milling and down-milling, depending on the direction of the cutter rotation relative to the feed direction. **3. End Milling:** End milling involves using an end mill cutter, which has cutting edges on both its periphery and end face. This allows for machining complex shapes such as pockets, slots, and contours. End milling is particularly useful in CNC machining due to its precision and versatility. **4. Slot Milling:** Slot milling is a specialized form of peripheral milling used to create narrow slots or grooves in a workpiece. It typically employs a slot drill or a slot cutter with cutting edges only on its periphery. **5. Gear Milling:** Gear milling is a precise process used to manufacture gears and other toothed components. It involves using specialized cutters designed to cut the teeth of gears accurately. This process can be performed using either a hobbing machine or a milling machine equipped with gear-cutting tools. **6. Form Milling:** Form milling involves using a custom-made cutter to produce complex shapes that cannot be achieved with standard cutters. This process is often used in aerospace and automotive industries where unique profiles are required. **7. Helical Milling:** Helical milling combines elements of both face and peripheral milling to create helical surfaces such as threads or helical grooves. This process requires precise control over the cutter's movement to achieve the desired helix angle. **8. CNC Milling:** Computer Numerical Control (CNC) milling leverages advanced technology to automate the milling process. CNC machines use pre-programmed instructions to guide the cutting tool, enabling high precision, repeatability, and efficiency in producing complex parts. Each type of milling process offers distinct benefits and is chosen based on the specific requirements of the project, including the material being machined, the desired surface finish, and the complexity of the part. Understanding these different types of milling processes is crucial for optimizing manufacturing operations and achieving high-quality results in various industrial applications. By selecting the appropriate milling technique, manufacturers can ensure efficient production while maintaining precision and quality standards.
Importance in Various Industries
Milling, a fundamental process in various industries, plays a pivotal role in shaping the modern manufacturing landscape. Its importance extends across multiple sectors, each leveraging milling's precision and versatility to achieve high-quality products. In the aerospace industry, milling is crucial for crafting intricate components such as engine parts, aircraft frames, and other critical structural elements. The precision required to ensure safety and performance in these components makes milling an indispensable tool. In the automotive sector, milling is used to produce complex engine components, gearboxes, and other mechanical parts that demand precise tolerances. This ensures optimal performance, fuel efficiency, and reliability in vehicles. The medical industry also relies heavily on milling for creating surgical instruments, implants, and diagnostic equipment. Here, the ability to mill materials with high accuracy is essential for patient safety and treatment efficacy. The construction industry benefits from milling in the production of architectural features, custom fixtures, and specialized tools. For instance, milling allows for the creation of intricate stone carvings and custom metalwork that enhance building aesthetics while maintaining structural integrity. In electronics manufacturing, milling is used to fabricate circuit boards, connectors, and other components that require precise dimensions to function correctly. Furthermore, in the energy sector, milling is vital for producing components for wind turbines, solar panels, and nuclear reactors. These components must be manufactured with exacting standards to ensure efficiency and safety in energy production. Additionally, the aerospace and defense industries utilize milling for producing armaments, ammunition casings, and other military hardware where precision is paramount. In consumer goods manufacturing, milling aids in the production of high-quality kitchen appliances, sporting goods, and other durable products. For example, milling allows for the creation of complex shapes in cookware that enhance heat distribution and durability. In the field of research and development, milling enables scientists to fabricate custom experimental equipment and prototypes with precise specifications. The importance of milling also extends to the field of art and design where artists use milling machines to create intricate sculptures and custom designs. This application highlights the versatility of milling beyond industrial uses, showcasing its potential in creative endeavors. In summary, milling's significance spans a wide array of industries due to its ability to deliver precision, consistency, and versatility. Whether it's crafting critical components for aerospace or producing intricate designs for consumer goods, milling remains an essential process that underpins modern manufacturing excellence. Its role in ensuring product quality, safety, and performance underscores its importance as a foundational technique in contemporary industrial practices.
Milling Techniques and Technologies
Milling techniques and technologies have evolved significantly over the years, transforming from traditional methods to highly sophisticated processes. The journey of milling encompasses a broad spectrum of advancements, each contributing uniquely to the field. This article delves into three key areas: **Traditional Milling Methods**, which laid the foundational principles; **Modern CNC Milling Techniques**, which revolutionized precision and efficiency; and **Specialized Milling Processes**, such as micro-milling and high-speed milling, which push the boundaries of what is possible. By understanding these different facets, we can appreciate the comprehensive evolution of milling and its current state. Starting with the roots of milling, we explore **Traditional Milling Methods**, which set the stage for all subsequent innovations. These early techniques, though rudimentary by today's standards, were crucial in establishing the fundamental principles that would later be refined and enhanced by modern technologies. Transitioning from these historical methods, we will examine how traditional milling paved the way for the sophisticated techniques that followed.
Traditional Milling Methods
Traditional milling methods have been a cornerstone of food processing and material refinement for centuries, offering a blend of simplicity, effectiveness, and cultural significance. These techniques, often passed down through generations, rely on manual or mechanical processes to grind, crush, or pulverize various materials such as grains, spices, and minerals. One of the most iconic traditional milling methods is the use of stone mills, where two stones are used to grind grains into flour. This method, still practiced in many parts of the world, ensures a high-quality product with minimal heat generation, preserving the nutritional value of the grains. Another traditional method is the mortar and pestle, which involves manually grinding substances using a pestle to crush against the mortar's surface. This technique is particularly effective for small-scale production and is often used in culinary practices for preparing spices and herbs. In addition to these methods, water mills and windmills have historically played significant roles in milling processes. Water mills, powered by flowing water, were instrumental in medieval Europe for grinding grains into flour. Similarly, windmills harnessed wind energy to perform milling tasks, especially in regions with abundant wind resources. These mechanical mills not only increased efficiency but also reduced manual labor, making them crucial for large-scale production. Traditional milling methods also encompass various cultural and regional practices. For instance, in many Asian cultures, rice is milled using traditional rice mills that separate the bran from the grain to produce white rice. In Africa, traditional grain mills are often simple yet effective tools made from local materials like wood or stone. These community-based milling practices not only provide essential food products but also serve as social hubs where people gather to share stories and community news. Despite the advent of modern milling technologies, traditional methods continue to hold value for several reasons. Firstly, they offer a unique flavor profile and texture that is often lost in industrial processing. Secondly, these methods are environmentally friendly as they rely on natural energy sources or manual effort, reducing carbon footprints. Lastly, traditional milling preserves cultural heritage and community traditions, ensuring that historical practices are not forgotten. In conclusion, traditional milling methods are more than just historical relics; they are vibrant components of our culinary and industrial heritage. These techniques not only provide high-quality products but also underscore the importance of sustainability, community engagement, and cultural preservation. As we move forward with advanced milling technologies, it is essential to appreciate and integrate these traditional methods into our modern practices to ensure a balanced approach that respects both tradition and innovation.
Modern CNC Milling Techniques
Modern CNC milling techniques have revolutionized the manufacturing industry by offering unparalleled precision, efficiency, and versatility. At the heart of these advancements is Computer Numerical Control (CNC) technology, which enables machines to execute complex milling operations with high accuracy and speed. One of the key features of modern CNC milling is the use of advanced software and algorithms that allow for intricate designs and simulations before actual machining begins. This pre-machining phase significantly reduces errors and optimizes the milling process, ensuring that the final product meets stringent quality standards. Another significant development in modern CNC milling is the integration of high-speed machining (HSM) techniques. HSM involves operating at higher spindle speeds and feed rates than traditional methods, which not only accelerates production but also improves surface finish and reduces tool wear. This is particularly beneficial for industries requiring high-volume production with minimal downtime, such as aerospace and automotive manufacturing. The advent of 5-axis CNC milling machines has further expanded the capabilities of modern milling. These machines can move in five different axes simultaneously, allowing for the machining of complex geometries and shapes that were previously impossible to achieve with traditional 3-axis machines. This capability is crucial for producing parts with intricate features, such as those found in medical devices, aerospace components, and precision engineering applications. In addition to hardware advancements, modern CNC milling also leverages advanced materials and coatings to enhance tool performance. For instance, the use of carbide and diamond-coated tools extends tool life and improves cutting efficiency, especially when working with hard-to-machine materials like titanium and stainless steel. Furthermore, advancements in coolant systems and lubrication technologies have improved thermal management during machining, reducing heat distortion and improving overall part quality. The integration of Industry 4.0 technologies into CNC milling operations has also transformed the manufacturing landscape. Real-time monitoring and data analytics enable operators to track machine performance, detect anomalies, and predict maintenance needs, thereby minimizing downtime and optimizing production schedules. This connectivity also facilitates remote monitoring and control, allowing for more flexible and responsive manufacturing processes. Moreover, modern CNC milling techniques often incorporate additive manufacturing (3D printing) and subtractive manufacturing (traditional machining) in hybrid processes. This hybrid approach allows for the creation of complex parts that combine the strengths of both methods—such as printing a base structure and then machining it to precise tolerances. This fusion of technologies opens up new possibilities for innovative product design and rapid prototyping. In conclusion, modern CNC milling techniques represent a significant leap forward in manufacturing technology. By combining advanced software, high-speed machining, multi-axis capabilities, improved tool materials, and Industry 4.0 integration, these techniques offer unprecedented levels of precision, efficiency, and flexibility. As these technologies continue to evolve, they will play an increasingly critical role in driving innovation across various industries, from aerospace to healthcare, and beyond.
Specialized Milling Processes (e.g., Micro-Milling, High-Speed Milling)
Specialized milling processes have revolutionized the manufacturing industry by offering precision, efficiency, and versatility that traditional milling techniques cannot match. Among these advanced methods, micro-milling and high-speed milling stand out for their unique capabilities and applications. **Micro-Milling** is a highly precise process designed for creating miniature features and components. This technique involves using extremely small cutting tools, often with diameters in the range of 0.1 to 1 mm, to mill intricate details on workpieces. Micro-milling is crucial in industries such as aerospace, medical devices, and electronics where miniaturization is key. For instance, in the production of micro-electromechanical systems (MEMS), micro-milling allows for the fabrication of tiny mechanical components with high accuracy and surface finish. The process requires specialized machinery and control systems to manage the tiny tool movements and maintain stability, ensuring that the delicate operations are performed without damage to either the tool or the workpiece. **High-Speed Milling**, on the other hand, leverages advanced machine tools and cutting tools to achieve significantly higher spindle speeds and feed rates compared to conventional milling. This process is particularly beneficial for machining hard materials like steel, titanium, and advanced composites. High-speed milling reduces machining time substantially while maintaining or even improving surface quality and dimensional accuracy. It is widely used in automotive and aerospace manufacturing for producing complex parts such as engine components, aircraft structures, and molds for plastic injection. The high-speed nature of this process generates less heat and reduces tool wear due to the shorter contact time between the tool and workpiece, leading to longer tool life and lower production costs. Both micro-milling and high-speed milling require sophisticated machine tools equipped with advanced control systems, high-precision spindles, and robust structures to handle the unique demands of these processes. Additionally, these specialized milling techniques necessitate skilled operators who understand the nuances of each process to optimize performance and ensure quality outcomes. The integration of these advanced milling processes into modern manufacturing workflows has significantly enhanced productivity, precision, and innovation across various industries, making them indispensable tools in the arsenal of contemporary machining technologies. By leveraging these specialized techniques, manufacturers can produce complex parts with unprecedented accuracy and efficiency, driving innovation and competitiveness in an increasingly demanding global market.
Applications and Benefits of Milling
Milling, a fundamental process in various industries, offers a multitude of applications and benefits that underscore its importance in modern manufacturing. At its core, milling is a machining process that involves the use of rotary cutters to remove material from a workpiece, thereby achieving the desired shape and size. This versatile technique is pivotal in manufacturing and production, where it enables the creation of complex parts with high precision. Additionally, milling stands out for its ability to deliver precision and accuracy, making it an indispensable tool in sectors requiring meticulous craftsmanship. Beyond its technical advantages, milling also presents significant economic and environmental benefits, such as reduced material waste and lower energy consumption compared to other machining methods. By exploring these facets—milling in manufacturing and production, its role in achieving precision and accuracy, and its economic and environmental benefits—we can fully appreciate the comprehensive value that milling brings to various industries. Let us begin by examining how milling integrates into the heart of manufacturing and production processes.
Milling in Manufacturing and Production
Milling, a fundamental process in manufacturing and production, plays a crucial role in shaping and refining raw materials into precise components. This versatile machining technique involves the use of rotating tools, known as milling cutters, to remove material from a workpiece. The applications of milling are diverse and widespread, making it an indispensable tool across various industries. In the automotive sector, milling is used to produce complex engine components such as cylinder blocks, crankshafts, and gearboxes. The precision achieved through milling ensures that these parts fit together seamlessly, enhancing the overall performance and efficiency of the vehicle. Similarly, in aerospace manufacturing, milling is employed to create intricate parts like aircraft engine components and structural elements, where accuracy and durability are paramount. The construction industry also heavily relies on milling for producing architectural features such as custom moldings, decorative trim, and precision-cut lumber. This allows for the creation of detailed designs that would be challenging or impossible to achieve with other methods. Additionally, milling is essential in the production of medical devices, where it is used to craft precise surgical instruments and implants that require high levels of accuracy and surface finish. One of the key benefits of milling is its ability to handle a wide range of materials, from metals like aluminum and steel to plastics and even wood. This versatility makes it a go-to process for prototyping and small batch production as well as large-scale manufacturing. Moreover, advancements in computer numerical control (CNC) technology have significantly enhanced the precision and speed of milling operations. CNC milling machines can execute complex operations with minimal human intervention, reducing errors and increasing productivity. Another significant advantage of milling is its capacity for producing complex geometries and shapes that would be difficult or impossible to achieve with other machining techniques. This capability is particularly valuable in industries where custom designs are common, such as in the production of molds and dies for injection molding and casting processes. Furthermore, milling offers considerable economic benefits by reducing material waste and optimizing production time. By allowing for the precise removal of material, milling minimizes scrap rates compared to other methods like sawing or drilling. Additionally, modern milling machines are designed with energy efficiency in mind, reducing operational costs over time. In conclusion, milling stands as a cornerstone of modern manufacturing due to its precision, versatility, and efficiency. Its widespread applications across various sectors underscore its importance in producing high-quality components that meet stringent standards. As technology continues to evolve, the benefits of milling are likely to expand further, solidifying its position as an essential tool in the world of manufacturing and production.
Milling for Precision and Accuracy
Milling for precision and accuracy is a cornerstone of modern manufacturing, enabling the production of intricate and complex components with unparalleled reliability. This process involves the use of milling machines, which are equipped with rotating tools that remove material from a workpiece to achieve the desired shape and dimensions. The precision in milling is achieved through several key factors: first, the use of high-quality cutting tools designed to maintain their edge and performance over extended periods. These tools are often made from advanced materials such as tungsten carbide or diamond-coated inserts, which offer superior hardness and wear resistance. Second, modern milling machines are equipped with advanced control systems, including CNC (Computer Numerical Control) technology. CNC milling allows for precise control over the cutting process, enabling the execution of complex operations with minimal human intervention. This automation ensures consistency and reduces the likelihood of human error, thereby enhancing overall accuracy. Additionally, CNC systems can be programmed to perform repetitive tasks with high precision, making them ideal for mass production scenarios. Third, the integration of advanced metrology and inspection techniques further enhances the precision of milling operations. Real-time monitoring and feedback systems allow for immediate adjustments to be made during the machining process, ensuring that the final product meets stringent quality standards. This includes the use of coordinate measuring machines (CMMs) and other inspection tools that verify the dimensions and surface finish of the milled parts. The benefits of precision milling are multifaceted. It enables the creation of parts with tight tolerances, which is crucial in industries such as aerospace, automotive, and medical device manufacturing where safety and performance are paramount. For instance, in aerospace engineering, precision-milled components are used in critical applications such as engine parts and structural elements, where failure could have catastrophic consequences. Similarly, in the automotive sector, precision-milled parts contribute to improved engine efficiency and reduced emissions. Moreover, precision milling supports the development of innovative products by allowing designers to create complex geometries that would be impossible to achieve with traditional manufacturing methods. This capability fosters innovation and drives technological advancements across various sectors. For example, in the field of medical devices, precision-milled implants and surgical instruments are designed to meet exacting standards, ensuring optimal performance and patient safety. In conclusion, milling for precision and accuracy is a vital component of modern manufacturing processes. By leveraging advanced cutting tools, CNC technology, and rigorous inspection protocols, manufacturers can produce high-quality components that meet stringent specifications. The applications of precision milling span a wide range of industries, each benefiting from the enhanced reliability, performance, and innovation that this process offers. As technology continues to evolve, the role of precision milling will remain central to the development of sophisticated products that underpin our daily lives.
Economic and Environmental Benefits of Milling
Milling, a fundamental process in various industries, offers a multitude of economic and environmental benefits that underscore its importance. Economically, milling enhances the efficiency and productivity of manufacturing processes. By transforming raw materials into precise shapes and sizes, milling reduces waste and minimizes the need for additional processing steps, thereby lowering production costs. This precision also allows for the creation of complex components with high accuracy, which is crucial in industries such as aerospace, automotive, and electronics where quality and reliability are paramount. Furthermore, the ability to mill a wide range of materials—from metals and plastics to wood and composites—makes it a versatile tool that can be adapted to different market demands, fostering innovation and competitiveness. From an environmental perspective, milling contributes significantly to sustainable practices. Modern milling technologies are designed with energy efficiency in mind, reducing the carbon footprint associated with manufacturing. For instance, advanced CNC (Computer Numerical Control) milling machines optimize cutting paths and speeds to minimize energy consumption while maintaining high precision. Additionally, the precision achieved through milling reduces material waste, which is a critical factor in reducing the environmental impact of industrial activities. This reduction in waste also translates into lower disposal costs and less strain on landfills. Moreover, milling can be used to recycle and repurpose materials, further aligning with circular economy principles that aim to minimize resource depletion and promote sustainability. The environmental benefits extend beyond the immediate production process as well. High-quality components produced through milling can lead to longer product lifetimes, reducing the need for frequent replacements and thus lowering the overall demand for raw materials. This longevity also means fewer products end up in landfills prematurely, contributing to a more sustainable consumption cycle. In sectors like renewable energy, milling plays a critical role in the production of components for wind turbines and solar panels, which are essential for transitioning to cleaner energy sources and mitigating climate change. In summary, the economic and environmental benefits of milling are substantial. By enhancing efficiency, reducing waste, and promoting sustainability, milling not only supports economic growth but also contributes to a more environmentally conscious industrial landscape. As technology continues to evolve, the role of milling in driving innovation and sustainability will only become more pronounced, making it an indispensable process in modern manufacturing.