What Is A Spanner

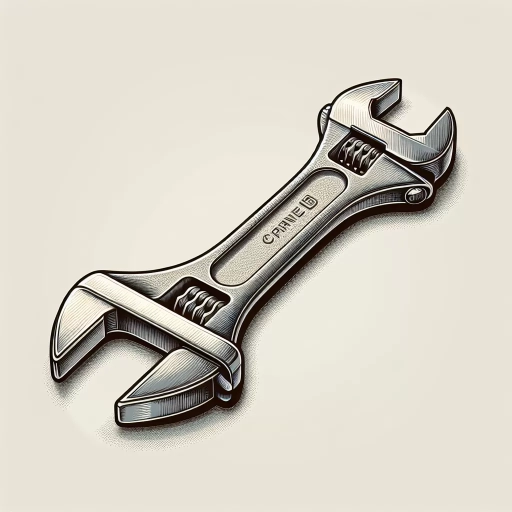
A spanner, also known as a wrench, is a versatile and essential tool in various industries and everyday life. This article delves into the world of spanners, providing a comprehensive overview of their significance, design, and applications. We begin by introducing the concept of spanners, exploring their history and evolution to understand their importance in modern toolkits. Next, we dissect the components and design of spanners, highlighting the different types and how their unique features cater to specific tasks. Finally, we examine the diverse uses and applications of spanners across different sectors, from automotive and construction to DIY projects. By understanding these aspects, readers will gain a deeper appreciation for the role spanners play in facilitating efficient and precise work. Let's start with an **Introduction to Spanners**, where we uncover the fundamental principles behind this indispensable tool.
Introduction to Spanners
Spanners, also known as wrenches, are indispensable tools in various industries and everyday life, serving as the backbone of mechanical work. This article delves into the multifaceted world of spanners, providing a comprehensive introduction that covers their definition and purpose, historical development, and common types. Firstly, understanding the definition and purpose of spanners is crucial for appreciating their role in mechanics. Spanners are designed to apply torque to bolts and nuts, facilitating the tightening or loosening of these fasteners. This fundamental function makes them essential for tasks ranging from simple DIY projects to complex industrial operations. Secondly, the historical development of spanners is a fascinating narrative that reflects technological advancements and human ingenuity. From primitive tools used in ancient civilizations to the sophisticated, precision-engineered spanners of today, this evolution highlights how these tools have adapted to meet changing needs and technological advancements. Lastly, recognizing the common types of spanners is vital for selecting the right tool for the job. Whether it's an adjustable spanner, a socket wrench, or a specialized tool like a basin wrench, each type has its unique characteristics and applications. By exploring these aspects, we gain a deeper understanding of how spanners have become an integral part of our toolkit. Let's begin by examining the definition and purpose of spanners, which form the foundation of their utility and importance.
Definition and Purpose
In the realm of tools and machinery, the spanner (or wrench) stands as a fundamental instrument, indispensable for various tasks involving bolts, nuts, and other fasteners. **Definition and Purpose** are crucial aspects that underscore the significance of this tool. A spanner is defined as a handheld device used to apply torque to an object, typically a bolt or nut, facilitating its tightening or loosening. This definition encapsulates the primary function of a spanner: to provide mechanical advantage, allowing users to exert greater force with less effort. The purpose of a spanner is multifaceted and far-reaching. At its core, it serves as a lever that amplifies the user's force, making it easier to manipulate fasteners in tight spaces or when significant torque is required. This makes spanners essential in numerous industries, including automotive, construction, and engineering. For instance, in the automotive sector, spanners are used to change oil filters, loosen stubborn bolts, and perform routine maintenance tasks. In construction, they are vital for assembling and disassembling heavy machinery and structural components. Beyond their practical applications, spanners also play a critical role in ensuring safety and efficiency. By providing a secure grip on fasteners, they reduce the risk of accidents caused by slipping tools or over-tightening. Additionally, spanners come in various types—such as adjustable spanners, socket spanners, and basin wrenches—each designed for specific tasks, thereby enhancing precision and reducing the time spent on a job. Moreover, the design of spanners has evolved over time to accommodate different needs. Modern spanners often feature ergonomic handles that reduce fatigue and improve grip, while materials like chrome vanadium steel ensure durability and resistance to wear. These advancements underscore the ongoing importance of spanners in modern toolkits. In summary, understanding the definition and purpose of a spanner is pivotal for appreciating its role in various professional and DIY contexts. As an integral part of any toolkit, the spanner's ability to apply torque efficiently makes it an indispensable asset for anyone working with fasteners. Its versatility, safety benefits, and continuous innovation solidify its position as a cornerstone tool in multiple industries. This foundational knowledge sets the stage for exploring the diverse types and uses of spanners in greater detail, highlighting their significance in everyday applications.
Historical Development
The historical development of spanners, or wrenches, is a fascinating narrative that spans centuries and reflects the evolution of human ingenuity and technological advancement. The earliest known tools resembling spanners date back to ancient civilizations, where primitive forms were crafted from stone, wood, and bone. These early tools were simple levers used to apply torque and manipulate objects, laying the groundwork for more sophisticated designs. As metalworking techniques improved during the Bronze Age, around 3000 BCE, tools began to be fashioned from copper and bronze. The ancient Greeks and Romans further refined these tools, creating more versatile and durable instruments. The Roman "gladius" wrench, for example, was a multi-purpose tool that could be used for various tasks beyond just tightening or loosening bolts. The Middle Ages saw the introduction of iron and steel, which significantly enhanced the strength and durability of spanners. Blacksmiths during this period crafted tools that were more robust and capable of handling heavier loads. The development of the first adjustable wrench in the 18th century marked a significant milestone; this innovation allowed users to adapt the tool to different sizes of bolts and nuts, greatly increasing its utility. The Industrial Revolution brought about a surge in technological advancements that transformed the manufacturing process of spanners. Mass production techniques enabled the widespread availability of standardized tools, while new materials like chrome vanadium steel improved their performance and longevity. This era also saw the invention of specialized spanners such as socket wrenches and ratchets, which further expanded the capabilities of these tools. In the 20th century, advancements in materials science led to the creation of high-strength alloys and synthetic materials that enhanced the durability and resistance of spanners to wear and tear. Modern manufacturing processes, including precision engineering and computer-aided design (CAD), have resulted in highly accurate and efficient tools tailored to specific tasks. Today’s spanners are not only stronger but also ergonomically designed for comfort and ease of use. Throughout their historical development, spanners have played a crucial role in various industries such as construction, automotive repair, and engineering. Their evolution reflects human ingenuity in solving practical problems and adapting to new technologies. From humble beginnings as simple levers to the sophisticated precision tools of today, spanners continue to be indispensable in our daily lives and industrial processes. Understanding this rich history provides a deeper appreciation for the importance of these tools in our modern world.
Common Types of Spanners
When delving into the world of spanners, it becomes evident that these versatile tools are not one-size-fits-all solutions. Instead, they come in various types, each designed to cater to specific needs and applications. One of the most common types is the **adjustable spanner**, which features a movable jaw that allows it to fit different sizes of bolts and nuts. This adaptability makes it a staple in many toolboxes, particularly for tasks where multiple sizes need to be accommodated. Another frequently used type is the **combination spanner**, which combines a fixed jaw with an adjustable jaw. This dual functionality offers both precision and flexibility, making it ideal for professionals who require both exact fitments and the ability to handle various sizes. The **socket spanner** is another essential tool, characterized by its use of interchangeable sockets that fit onto a ratchet handle. This setup allows for efficient torque application and is widely used in automotive and industrial settings. For more precise work, **ring spanners** and **open-ended spanners** are preferred. Ring spanners have a closed loop at one end, providing a secure grip on bolts and nuts, while open-ended spanners feature an open jaw that allows for easier access in tight spaces. Both types are available in metric and imperial sizes and are often used in applications where high torque is required. The **basin wrench** is a specialized type of spanner designed for plumbing tasks. It features a long handle and a curved or angled jaw, allowing users to reach and turn bolts in confined spaces such as under sinks or around pipes. This tool is indispensable for plumbers and DIY enthusiasts tackling bathroom and kitchen repairs. In addition to these, **impact spanners** are used in heavy-duty applications where high torque is necessary. These tools are designed to be used with impact wrenches or pneumatic tools, making them crucial in industries like construction and manufacturing. Lastly, **locking spanners** or **locking wrenches** are used to ensure that bolts or nuts remain securely in place after tightening. These tools feature a mechanism that locks onto the bolt or nut, preventing it from coming loose over time due to vibration or other external forces. Each type of spanner has its unique advantages and is suited for specific tasks, making it important for users to understand their differences and applications. Whether you are a professional mechanic, a plumber, or a DIY enthusiast, having the right spanner for the job can significantly enhance efficiency and ensure that tasks are completed safely and effectively. By understanding the common types of spanners available, individuals can better equip themselves with the tools necessary to tackle a wide range of projects with confidence.
Components and Design of Spanners
When it comes to the components and design of spanners, several key elements come into play to ensure these tools are both effective and user-friendly. A high-quality spanner is not just about its ability to apply torque; it also involves careful consideration of its handle and grip design, jaw and socket configurations, and the materials used in its construction. The handle and grip design are crucial for comfort and control, allowing users to apply force without straining their hands. The jaw and socket configurations determine the versatility and precision of the spanner, enabling it to fit various bolt sizes and shapes. Lastly, the materials used in construction impact the durability and strength of the tool, ensuring it can withstand heavy use over time. By understanding these components, users can select the right spanner for their needs and maximize their efficiency. Let's start by examining one of these critical aspects: the handle and grip design, which sets the foundation for a tool that is both comfortable and functional.
Handle and Grip Design
**Handle and Grip Design** The handle and grip of a spanner are crucial components that significantly impact its usability, comfort, and overall performance. A well-designed handle ensures that the tool is easy to maneuver, reducing fatigue and improving control during use. The material selection for the handle is paramount; common choices include steel, aluminum, and fiberglass, each offering different strengths such as durability, weight reduction, and resistance to corrosion. For instance, fiberglass handles are often preferred in electrical applications due to their non-conductive properties, while steel handles provide robustness and longevity. The grip design is another critical aspect that enhances user experience. Ergonomic grips are designed to fit comfortably in the hand, distributing the force evenly and minimizing slippage. Materials like rubber, polyurethane, and thermoplastic elastomers are commonly used for grips because they offer a secure hold even when hands are wet or greasy. Some grips feature textured patterns or ridges to further improve traction. Additionally, ergonomic design principles are applied to ensure that the grip aligns with the natural contours of the hand, reducing strain on the wrist and fingers during prolonged use. Innovative handle designs also incorporate features such as shock absorption and vibration damping to protect users from the impact of sudden torque changes or repetitive use. This is particularly important for spanners used in heavy-duty applications where high forces are involved. Furthermore, some modern spanners feature adjustable handles that allow users to customize the length and angle of the tool according to their preference, enhancing versatility and adaptability. Moreover, safety considerations play a significant role in handle and grip design. For example, some spanners have handles with built-in safety features like slip-resistant coatings or warning colors to indicate when the tool is being used incorrectly. The color coding can also help in quick identification of different sizes or types of spanners in a toolbox. In summary, the design of handles and grips in spanners is a multifaceted process that balances functionality, comfort, safety, and durability. By leveraging advanced materials and ergonomic principles, manufacturers can create tools that not only perform effectively but also provide a superior user experience. This attention to detail in handle and grip design contributes significantly to the overall quality and usability of spanners, making them indispensable tools in various industries and DIY projects.
Jaw and Socket Configurations
When discussing the components and design of spanners, one crucial aspect to consider is the jaw and socket configurations. These configurations are fundamental in determining the versatility, effectiveness, and safety of a spanner. The jaw configuration refers to the shape and structure of the gripping end of an adjustable spanner or wrench, while the socket configuration pertains to the design of the socket in a socket wrench set. For adjustable spanners, the jaw configuration typically includes a movable jaw that can be adjusted to fit various bolt or nut sizes. This adjustability is often achieved through a screw or lever mechanism that allows users to set the jaw width precisely. The jaws themselves may be flat, curved, or have specialized shapes for specific applications such as gripping pipes or rounded bolts. High-quality adjustable spanners often feature jaws with fine teeth or serrations to enhance grip and prevent slippage, ensuring that the tool does not damage the workpiece. On the other hand, socket wrench sets rely on a variety of socket configurations to accommodate different bolt and nut sizes. Sockets come in various drive sizes (e.g., 1/4", 3/8", 1/2") and may be either shallow or deep to reach bolts in confined spaces. The socket's internal shape can also vary; common types include six-point (hexagonal), twelve-point (dodecagonal), and impact sockets designed for use with impact wrenches. Six-point sockets provide a secure grip on bolts but can round them if over-tightened, whereas twelve-point sockets offer more versatility but may slip off if not aligned correctly. Impact sockets are made from hardened steel and are designed to withstand the high torque generated by impact wrenches. The material used in both jaw and socket configurations is also critical. High-strength steel alloys like chrome vanadium or chrome molybdenum are commonly used due to their durability and resistance to wear and tear. These materials ensure that the spanner can withstand heavy use without compromising its performance or safety. Additionally, some spanners may feature coatings such as chrome plating or powder coating to enhance corrosion resistance and improve tool longevity. In summary, the jaw and socket configurations of spanners are pivotal in ensuring that these tools are effective, safe, and versatile. Understanding these configurations helps users select the right tool for their specific needs, whether it's an adjustable spanner for general-purpose use or a specialized socket wrench set for more complex tasks. By choosing spanners with appropriate jaw and socket designs, users can achieve better results while minimizing the risk of damage to both the tool and the workpiece. This attention to detail in tool design underscores the importance of considering all components when evaluating what makes a spanner reliable and efficient.
Materials Used in Construction
In the realm of construction, the choice of materials is paramount for ensuring the durability, safety, and aesthetic appeal of a structure. This selection process is akin to the meticulous consideration given to the components and design of spanners, where each element must serve a specific purpose to achieve optimal functionality. For instance, in building construction, steel is a cornerstone material due to its high strength-to-weight ratio, making it ideal for structural frames and reinforcement. Concrete, another fundamental material, offers excellent compressive strength and is widely used in foundations, walls, and floors. The combination of steel and concrete creates a robust and durable structure that can withstand various environmental conditions. Wood, particularly engineered wood products like laminated veneer lumber (LVL) and glued-laminated timber (Glulam), has seen a resurgence in popularity due to its sustainability and aesthetic appeal. These materials are often used in residential construction for framing, flooring, and roofing. In contrast, aluminum and other metals are favored for their corrosion resistance and are commonly used in roofing, cladding, and structural components where weight is a concern. Ceramic and glass materials are also integral in modern construction, primarily for their thermal insulation properties and visual appeal. Ceramic tiles are a staple in flooring and wall coverings due to their durability and ease of maintenance, while glass is used extensively in windows, facades, and decorative elements. The use of sustainable materials such as bamboo, recycled plastics, and low-carbon concrete is gaining traction as the industry shifts towards more environmentally friendly practices. The selection of materials is not just about functionality but also about compliance with building codes and regulations. For example, fire-resistant materials like gypsum board and fire-treated wood are essential for ensuring safety standards are met. Similarly, the design of spanners must adhere to specific standards to ensure they can handle the torque required without failing, much like how construction materials must meet the structural demands of a building. Innovative materials such as fiber-reinforced polymers (FRP) and advanced composites are being increasingly incorporated into construction projects for their superior strength, lightweight properties, and resistance to corrosion. These materials are particularly useful in rehabilitation projects where traditional materials may not be feasible due to weight or space constraints. Ultimately, the careful selection and integration of these diverse materials in construction mirror the precision and thoughtfulness that go into designing the components of a spanner. Each material serves a unique purpose, contributing to the overall integrity and performance of the structure, just as each component of a spanner works together to provide the necessary leverage and control for various tasks. This synergy between material choice and design underscores the importance of meticulous planning in both construction and tool engineering.
Uses and Applications of Spanners
Spanners, also known as wrenches, are versatile tools that play a crucial role in various sectors due to their ability to apply torque and facilitate the loosening or tightening of bolts and nuts. The uses and applications of spanners are diverse and widespread, making them indispensable in different settings. In **Automotive and Mechanical Repairs**, spanners are essential for diagnosing and fixing vehicle issues, from routine maintenance tasks like oil changes to complex repairs involving engine components. They are also vital in **Industrial and Construction Settings**, where heavy machinery and equipment require regular maintenance and repair. Additionally, **DIY and Home Maintenance** projects often rely on spanners for tasks such as assembling furniture, fixing plumbing issues, or performing minor repairs around the house. Given their importance across these domains, it is clear that spanners are not just tools but critical enablers of efficiency and productivity. Let's delve deeper into their role in **Automotive and Mechanical Repairs**, where their precision and reliability are paramount.
Automotive and Mechanical Repairs
In the realm of automotive and mechanical repairs, spanners are indispensable tools that play a crucial role in ensuring the efficiency and safety of various operations. These versatile instruments are designed to apply torque to bolts and nuts, facilitating the tightening or loosening of fasteners in a wide range of applications. For instance, in automotive repair shops, spanners are used to perform routine maintenance tasks such as oil changes, tire rotations, and brake pad replacements. Mechanics rely on spanners to secure or remove components like spark plugs, exhaust systems, and suspension parts, where precise control over torque is essential to avoid damage or ensure proper fitment. The use of spanners extends beyond routine maintenance to more complex repairs. In engine overhauls, for example, spanners are critical for disassembling and reassembling engine components such as cylinder heads, crankshafts, and camshafts. The ability to apply specific amounts of torque helps prevent damage to delicate parts and ensures that all components are securely fastened to withstand the stresses of operation. Additionally, in transmission repairs, spanners are used to remove and install gear sets, bearings, and other internal components that require precise alignment and torque specifications. In mechanical repairs outside the automotive sector, spanners are equally vital. In industrial settings, they are used for machinery maintenance and repair, where large bolts and nuts need to be manipulated. For instance, in manufacturing plants, spanners help technicians service heavy machinery like presses, pumps, and conveyor systems. In construction equipment maintenance, spanners are essential for tasks such as replacing tracks on bulldozers or adjusting hydraulic systems on cranes. The variety of spanner types available further underscores their importance in mechanical repairs. Adjustable spanners offer flexibility when dealing with different sizes of bolts and nuts, while ratcheting spanners provide ease of use in tight spaces. Impact wrenches, which can be considered a type of powered spanner, are used for high-torque applications where manual effort would be impractical or unsafe. The precision and reliability of these tools make them indispensable in any workshop or garage. Moreover, the safety aspect of using spanners cannot be overstated. Properly tightening fasteners prevents accidents caused by loose parts failing under stress. This is particularly critical in vehicles where loose bolts could lead to catastrophic failures on the road. Similarly, in industrial settings, ensuring that machinery is properly secured helps prevent workplace injuries and equipment damage. In conclusion, spanners are fundamental tools in automotive and mechanical repairs due to their versatility, precision, and necessity. Whether it's routine maintenance or complex overhauls, these instruments ensure that tasks are completed efficiently and safely. Their widespread use across various industries highlights their importance as essential components of any toolkit, underscoring the critical role they play in maintaining the integrity and performance of mechanical systems.
Industrial and Construction Settings
In industrial and construction settings, spanners are indispensable tools that play a crucial role in ensuring the efficiency, safety, and quality of various operations. These versatile instruments are used for tightening and loosening bolts, nuts, and other fasteners, which are essential components in machinery, structures, and equipment. In construction sites, spanners are vital for assembling and disassembling scaffolding, cranes, and other heavy machinery. For instance, a ratchet spanner can be used to secure bolts on scaffolding frames quickly and effectively, while an adjustable spanner can handle different sizes of nuts and bolts without the need for multiple tools. In industrial environments such as manufacturing plants and workshops, spanners are used to maintain and repair machinery. For example, a socket spanner set is often employed to work on engines, pumps, and other complex machinery where access is limited. The precision and leverage provided by these tools allow technicians to apply the necessary torque without causing damage to the equipment or surrounding components. Additionally, spanners are crucial in the assembly line process where they help in the rapid and accurate fitting of parts together. The safety aspect of using spanners in these settings cannot be overstated. Properly fitted bolts and nuts prevent accidents caused by loose or over-tightened fasteners. For instance, in the aerospace industry, the use of high-quality spanners ensures that aircraft components are securely fastened, thereby safeguarding against potential failures during flight. Similarly, in automotive manufacturing, spanners are used to ensure that vehicle parts are assembled correctly to meet stringent safety standards. Moreover, the durability of spanners makes them a cost-effective option for long-term use in demanding environments. Unlike other tools that may wear out quickly under heavy use, well-maintained spanners can last for years with minimal maintenance. This reduces downtime and the need for frequent replacements, thereby enhancing productivity and reducing operational costs. In summary, spanners are fundamental tools in industrial and construction settings due to their versatility, precision, and durability. They facilitate efficient operations by enabling quick and accurate tightening and loosening of fasteners, ensuring safety through proper fitting of components, and providing long-term reliability that minimizes maintenance needs. As such, they remain an essential part of any toolkit in these sectors.
DIY and Home Maintenance
When it comes to DIY projects and home maintenance, having the right tools is crucial for efficiency and effectiveness. Among these essential tools, spanners stand out as versatile and indispensable. A spanner, also known as a wrench, is designed to apply torque to an object, making it easier to tighten or loosen bolts and nuts. In the realm of DIY and home maintenance, spanners are used in a myriad of applications that range from simple tasks like assembling furniture to more complex projects such as plumbing and automotive repairs. For instance, when assembling furniture, a spanner can be used to secure bolts and screws quickly and accurately. This is particularly useful for tasks that require precision, such as aligning parts or ensuring that all components are securely fastened. In plumbing, spanners are vital for tightening and loosening pipe fittings, valves, and other fixtures. Whether you're fixing a leaky faucet or installing a new water heater, having the right spanner can make the job much easier and less time-consuming. In automotive maintenance, spanners are essential for tasks like changing oil filters, loosening lug nuts on wheels, and adjusting brake pads. The variety of spanner types—such as adjustable spanners, socket spanners, and basin wrenches—ensures that you have the perfect tool for any specific job. For example, an adjustable spanner can be adjusted to fit different sizes of bolts and nuts, making it a handy addition to any DIY toolkit. Moreover, spanners are not just limited to these specific tasks; they are also useful in general home repairs. Whether you're hanging a picture frame or repairing a broken door hinge, a spanner can provide the necessary leverage to get the job done efficiently. Additionally, knowing how to use a spanner correctly can prevent damage to tools and surfaces. For instance, using a spanner with a rubber grip can help prevent slipping and scratching surfaces. Incorporating spanners into your DIY toolkit also promotes self-sufficiency and cost savings. By being able to perform routine maintenance tasks yourself, you avoid the need for professional services which can be expensive. Furthermore, having a well-stocked toolkit with various types of spanners encourages creativity and confidence in tackling more complex projects over time. In conclusion, spanners are an integral part of any DIY enthusiast's or homeowner's toolkit due to their versatility and utility across various applications. From assembling furniture to performing automotive repairs, these tools offer precision, leverage, and convenience that make home maintenance easier and more manageable. By understanding the uses and applications of spanners in different contexts, individuals can enhance their DIY skills and ensure that their homes remain well-maintained with minimal effort.