What Is Pps

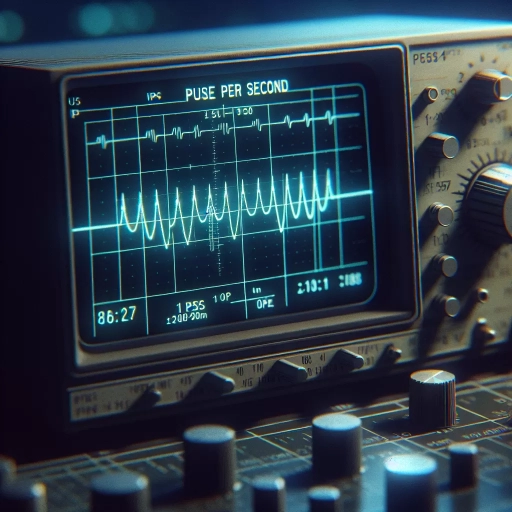
Polyphenylsulfone (PPS) is a high-performance engineering plastic known for its exceptional thermal stability, chemical resistance, and mechanical strength. This versatile material has garnered significant attention across various industries due to its unique properties and wide range of applications. To fully appreciate the value of PPS, it is essential to delve into its fundamental aspects. Understanding the basics of PPS provides a foundation for grasping its technical intricacies and practical uses. This article will explore the technical aspects of PPS, including its molecular structure and manufacturing processes, as well as its practical applications and benefits in fields such as aerospace, automotive, and medical devices. By examining these facets, readers will gain a comprehensive understanding of why PPS stands out as a material of choice for demanding environments. Let's begin by understanding the basics of PPS.
Understanding the Basics of PPS
Understanding the basics of PPS (Pulse Positioning System) is crucial for grasping its significance and utility in various fields. To delve into this topic, it is essential to explore three key aspects: the definition and acronym expansion, historical context and development, and primary uses and applications. Firstly, defining what PPS stands for and understanding its components is fundamental. This involves breaking down the acronym to comprehend the technology behind it. Secondly, examining the historical context and development of PPS provides insight into how this technology evolved over time, influenced by technological advancements and practical needs. Lastly, understanding the primary uses and applications of PPS highlights its relevance in modern-day scenarios, from navigation systems to industrial automation. By starting with a clear definition and acronym expansion, we lay the groundwork for a deeper exploration of PPS's historical development and its diverse applications, ensuring a comprehensive understanding of this vital technology. Therefore, let us begin by expanding on the definition and acronym expansion of PPS.
Definition and Acronym Expansion
**Understanding the Basics of PPS: Definition and Acronym Expansion** PPS, or Pay-Per-Sale, is a fundamental concept in affiliate marketing and online advertising. To grasp the basics of PPS, it's essential to understand its definition and how it operates. **Pay-Per-Sale** refers to a compensation model where an affiliate marketer earns a commission only when a customer completes a purchase through their unique referral link. This model contrasts with other popular models like Pay-Per-Click (PPC) and Pay-Per-Lead (PPL), where affiliates are paid for each click or lead generated, respectively. In the PPS model, the affiliate's earnings are directly tied to the conversion rate of their referrals. For instance, if an affiliate promotes a product and a customer buys it using their link, the affiliate receives a percentage of the sale amount as their commission. This approach incentivizes affiliates to focus on promoting high-quality products that have a strong potential for sales, as their earnings are contingent upon successful transactions. The acronym expansion of PPS highlights its core mechanism: **Pay** (the compensation received by the affiliate), **Per** (the basis of payment), and **Sale** (the specific action that triggers the payment). This clarity is crucial for both affiliates and advertisers, as it sets clear expectations about how revenue will be shared. Understanding PPS is vital for anyone involved in affiliate marketing because it influences marketing strategies, content creation, and audience engagement. Affiliates must carefully select products that align with their audience's interests and needs to maximize their chances of earning commissions. Advertisers, on the other hand, benefit from this model by ensuring they only pay for tangible results—actual sales—rather than mere clicks or leads. In summary, PPS is a performance-based marketing model where affiliates are compensated solely for sales generated through their efforts. This definition underscores the importance of effective marketing tactics and product selection in driving successful outcomes in affiliate marketing. By grasping the nuances of PPS, both affiliates and advertisers can optimize their strategies to achieve better results and foster more profitable partnerships.
Historical Context and Development
The historical context and development of PPS (Pay-Per-Click) advertising are deeply intertwined with the evolution of the internet and digital marketing. In the early 1990s, as the World Wide Web began to expand, online advertising emerged as a viable means for businesses to reach their target audiences. One of the pioneers in this field was OpenText Index, which introduced a pay-per-click model in 1996. However, it was GoTo.com (later renamed Overture Services) that popularized PPC in 1998 by allowing advertisers to bid on keywords to secure top placement on search engine results pages. Google entered the scene in 2000 with AdWords, which revolutionized PPC by introducing a quality score system that ensured relevance and user experience. This innovation shifted the focus from merely bidding on keywords to creating high-quality ads that aligned with user intent. Over time, Google's dominance in search led to AdWords becoming the industry standard for PPC advertising. The early 2000s saw significant advancements in PPC technology, including the introduction of contextual advertising by Google's AdSense program. This allowed publishers to monetize their content by displaying relevant ads on their websites, further expanding the reach of PPC campaigns. As mobile devices became ubiquitous, PPC strategies had to adapt to accommodate new user behaviors and screen sizes. Google's introduction of Enhanced Campaigns in 2013 was a major step in this direction, enabling advertisers to manage bids across different devices from a single campaign. Today, PPC continues to evolve with advancements in machine learning and artificial intelligence. Platforms like Google Ads and Microsoft Advertising leverage these technologies to offer more sophisticated targeting options, automated bidding strategies, and detailed analytics. These developments have made PPC a cornerstone of digital marketing strategies for businesses of all sizes, providing measurable ROI and granular control over ad spend. Understanding the historical context and development of PPC is crucial for grasping its current capabilities and future potential. It highlights how continuous innovation has transformed PPC from a simple bidding system into a complex ecosystem that balances advertiser needs with user experience. This evolution underscores the importance of staying updated with industry trends and best practices to maximize the effectiveness of PPC campaigns.
Primary Uses and Applications
**Primary Uses and Applications** Polyphenylsulfone (PPS) is a high-performance engineering thermoplastic known for its exceptional thermal stability, chemical resistance, and mechanical strength. The primary uses and applications of PPS are diverse and widespread, reflecting its versatility and reliability in various industries. 1. **Automotive Industry**: In the automotive sector, PPS is used in components that require high heat resistance and durability, such as fuel system components, ignition components, and exhaust gas recirculation (EGR) systems. Its ability to withstand extreme temperatures makes it an ideal material for these applications. 2. **Electrical and Electronics**: PPS is utilized in electrical connectors, switches, and other electronic components due to its excellent insulation properties and resistance to high temperatures. It is also used in the manufacture of printed circuit boards (PCBs) and other electronic devices. 3. **Aerospace**: The aerospace industry leverages PPS for its lightweight yet robust properties. It is used in aircraft and spacecraft components where high thermal stability and resistance to chemicals are crucial. 4. **Medical Devices**: In the medical field, PPS is valued for its biocompatibility and sterilization resistance. It is used in medical devices such as surgical instruments, implantable devices, and diagnostic equipment that require repeated sterilization without compromising material integrity. 5. **Industrial Applications**: PPS finds extensive use in industrial settings for manufacturing parts that are exposed to harsh environments. This includes pumps, valves, and other machinery components that need to withstand corrosive chemicals and high temperatures. 6. **Consumer Goods**: In consumer products, PPS is often used in kitchen appliances like cookware handles and other components that require heat resistance. It is also found in household items such as hair dryers and irons due to its ability to maintain structural integrity at elevated temperatures. 7. **Filter Media**: The chemical resistance of PPS makes it suitable for use in filter media for various industrial processes, including water filtration systems and air purification systems. 8. **Coatings and Adhesives**: PPS can be formulated into coatings and adhesives that provide excellent thermal stability and chemical resistance, making them useful for protective coatings on metals and other substrates. In summary, the primary uses of PPS span across multiple industries where its unique combination of thermal stability, chemical resistance, and mechanical strength are essential. Its versatility ensures that it remains a critical material in modern engineering applications.
Technical Aspects of PPS
Polyphenylsulfone (PPS) is a high-performance engineering plastic renowned for its exceptional technical attributes, making it a versatile material in various industrial applications. To fully appreciate the capabilities of PPS, it is essential to delve into three critical aspects: its chemical composition and properties, the manufacturing process and production methods, and its material characteristics and durability. Understanding the chemical composition of PPS reveals its inherent strengths, such as high thermal stability and resistance to chemicals. The manufacturing process and production methods highlight the precision and quality control involved in producing this material, ensuring consistent performance. Finally, examining the material characteristics and durability underscores PPS's ability to withstand harsh environments and maintain its integrity over time. By exploring these facets, we can gain a comprehensive understanding of why PPS is a preferred choice in demanding industries. Let us begin by examining the foundational aspect of PPS: its chemical composition and properties.
Chemical Composition and Properties
Polyphenylene sulfide (PPS) is a high-performance engineering plastic known for its exceptional chemical composition and properties, which make it an ideal material for various technical applications. Chemically, PPS is composed of a linear polymer chain with repeating units of benzene rings and sulfur atoms, forming a strong and stable molecular structure. This unique composition imparts PPS with outstanding resistance to chemicals, including acids, bases, and organic solvents, making it suitable for use in harsh environments. The properties of PPS are equally impressive. It exhibits high thermal stability, with a melting point around 280°C and a continuous use temperature up to 200°C, allowing it to perform reliably in extreme heat conditions. PPS also possesses excellent mechanical properties, such as high tensile strength, stiffness, and impact resistance, which are crucial for applications requiring durability and reliability. Additionally, PPS has low moisture absorption and excellent dimensional stability, ensuring that it maintains its shape and integrity over time. From an electrical perspective, PPS is an excellent insulator with high dielectric strength and low dielectric constant, making it suitable for electrical components and connectors. Its flame retardancy is another significant advantage; PPS meets stringent fire safety standards without the need for additional flame retardants. Furthermore, PPS can be compounded with various fillers and additives to enhance its properties further, such as improving its thermal conductivity or reducing its cost. In terms of processing, PPS can be molded using conventional injection molding techniques as well as more specialized methods like extrusion and compression molding. Its ability to be easily machined and fabricated into complex shapes adds to its versatility. The combination of these chemical and physical properties makes PPS a preferred choice in industries such as aerospace, automotive, electronics, and industrial manufacturing where high performance and reliability are paramount. Overall, the chemical composition and properties of PPS underscore its position as a premier engineering plastic capable of meeting the demanding requirements of modern technology. Its robust chemical resistance, thermal stability, mechanical strength, and electrical insulation properties make it an indispensable material in a wide range of technical applications.
Manufacturing Process and Production Methods
In the realm of technical aspects of Polyphenylsulfone (PPS), the manufacturing process and production methods play a crucial role in determining the material's properties and applications. PPS is a high-performance engineering plastic known for its exceptional thermal stability, chemical resistance, and mechanical strength. The manufacturing process typically involves a combination of polymerization and compounding steps. **Polymerization:** The synthesis of PPS begins with the polymerization of 1,4-dichlorobenzene and sodium sulfide in a polar solvent. This reaction is usually conducted under high-temperature conditions to facilitate the formation of the polymer chain. The resulting polymer is then precipitated, washed, and dried to remove any impurities. **Compounding:** After polymerization, the raw PPS resin undergoes compounding to enhance its properties. This involves blending the resin with various additives such as fillers (e.g., glass fibers, carbon fibers), impact modifiers, and stabilizers. These additives can significantly improve the material's mechanical strength, impact resistance, and thermal stability. **Production Methods:** PPS can be processed using several production methods, each suited to different applications: 1. **Injection Molding:** This is one of the most common methods for producing PPS parts. It involves injecting molten PPS into a mold where it cools and solidifies into the desired shape. Injection molding is ideal for producing complex geometries with high precision. 2. **Extrusion:** Extrusion is used to create continuous profiles such as rods, tubes, and sheets. The PPS resin is melted and forced through a die to form the desired shape. 3. **Compression Molding:** This method is often used for producing large or thick parts. It involves placing the PPS material in a mold and applying pressure to ensure uniform distribution and consolidation. 4. **Blow Molding:** Used primarily for hollow objects like bottles and containers, blow molding involves inflating a molten PPS tube (parison) inside a mold until it takes the shape of the mold. 5. **3D Printing:** Advanced manufacturing techniques such as 3D printing are also being explored for PPS. This allows for the creation of complex geometries that would be difficult or impossible to achieve with traditional methods. **Quality Control:** Throughout these production methods, stringent quality control measures are essential to ensure that the final product meets the required specifications. This includes monitoring parameters such as molecular weight, crystallinity, and additive content to guarantee consistent performance across different batches. In summary, the manufacturing process and production methods for PPS are critical in tailoring its properties for various industrial applications. By understanding these technical aspects, manufacturers can optimize their processes to produce high-quality PPS products that meet demanding performance criteria.
Material Characteristics and Durability
Material characteristics and durability are crucial aspects to consider when evaluating the technical aspects of Polyphenylene Sulfide (PPS), a high-performance engineering plastic. PPS is renowned for its exceptional mechanical properties, thermal stability, and chemical resistance. One of its key characteristics is its high melting point, typically around 280°C, which makes it suitable for applications in extreme temperature environments. This thermal stability also contributes to its excellent dimensional stability, ensuring that PPS components retain their shape and integrity under various thermal conditions. The material's durability is further enhanced by its inherent resistance to chemicals and solvents. PPS exhibits excellent resistance to acids, bases, and organic solvents, making it an ideal choice for use in harsh chemical environments. Additionally, PPS has a low coefficient of friction, which reduces wear and tear on moving parts, thereby extending the lifespan of components in mechanical systems. From a mechanical standpoint, PPS boasts high tensile strength and stiffness, coupled with good impact resistance. These properties make it a reliable material for structural components that require strength and rigidity. Moreover, PPS can be reinforced with fillers such as glass fibers or carbon fibers to further enhance its mechanical performance, allowing it to meet the demands of high-stress applications. Another significant aspect of PPS is its electrical properties. It is an excellent insulator with high dielectric strength and low dielectric loss, making it suitable for use in electrical and electronic components. This combination of mechanical, thermal, and electrical properties makes PPS a versatile material that can be used in a wide range of industries, including automotive, aerospace, industrial machinery, and consumer electronics. In terms of durability, PPS also offers excellent resistance to fatigue and creep. This means that components made from PPS can withstand repeated stress cycles without failing, ensuring long-term reliability in dynamic applications. Furthermore, PPS has a low moisture absorption rate, which helps maintain its physical properties over time, even in humid environments. Overall, the material characteristics and durability of PPS make it a preferred choice for demanding applications where high performance and reliability are critical. Its unique blend of thermal stability, chemical resistance, mechanical strength, and electrical insulation properties ensures that PPS components can withstand the rigors of various operational conditions, thereby extending their service life and reducing maintenance needs. This makes PPS an indispensable material in modern engineering and manufacturing.
Practical Applications and Benefits of PPS
Polyphenylsulfone (PPS) is a high-performance engineering plastic renowned for its versatility and robust properties, making it a cornerstone in various industrial sectors. This article delves into the practical applications and benefits of PPS, highlighting its industrial uses, advantages over other materials, and its environmental impact. In the realm of industrial uses, PPS is employed in diverse sectors such as automotive, aerospace, and electronics due to its exceptional thermal stability, chemical resistance, and mechanical strength. The material's superiority over other polymers is evident in its ability to withstand extreme conditions, making it a preferred choice for critical applications. Additionally, PPS offers a sustainable alternative with a lower environmental footprint compared to traditional materials, contributing to a more eco-friendly manufacturing process. By exploring these facets, we can better understand the multifaceted benefits of PPS and its pivotal role in modern industry. Let us begin by examining the industrial uses of PPS in various sectors.
Industrial Uses in Various Sectors
Polyphenylsulfone (PPS) is a high-performance engineering plastic that finds extensive use across various industrial sectors due to its unique combination of properties. In the **automotive industry**, PPS is utilized for components such as fuel system parts, engine mounts, and electrical connectors because of its excellent chemical resistance, high temperature stability, and mechanical strength. Its ability to withstand harsh environments makes it an ideal material for applications where reliability and durability are critical. In **aerospace**, PPS is used in aircraft and spacecraft components due to its lightweight yet robust nature, resistance to extreme temperatures, and compatibility with advanced manufacturing techniques like 3D printing. The material's low outgassing properties also make it suitable for use in vacuum environments. The **medical sector** benefits from PPS's biocompatibility and sterilizability, making it a preferred choice for medical devices such as surgical instruments, implantable devices, and diagnostic equipment. Its resistance to chemicals and high temperatures allows for repeated sterilization without compromising its integrity. In **industrial processing**, PPS is used in pumps, valves, and other equipment due to its resistance to corrosive chemicals and high-temperature fluids. This ensures prolonged equipment life and reduced maintenance costs. The **electronics industry** leverages PPS for connectors, switches, and other electrical components because of its excellent electrical insulation properties and ability to withstand soldering temperatures without degrading. Additionally, **construction materials** like roofing membranes and insulation materials incorporate PPS for its durability and resistance to environmental factors such as UV radiation and moisture. Overall, the versatility of PPS makes it a valuable material across diverse industrial sectors, offering practical applications that enhance performance, reliability, and cost-effectiveness. Its unique blend of mechanical strength, chemical resistance, and thermal stability positions it as a go-to material for demanding applications where other plastics may fall short.
Advantages Over Other Materials
Polyphenylsulfone (PPS) stands out among various engineering plastics due to its unique combination of properties, offering several advantages over other materials. One of the primary benefits of PPS is its exceptional thermal stability, allowing it to maintain its structural integrity and performance even at high temperatures, often exceeding 200°C. This makes PPS an ideal choice for applications in harsh environments, such as in automotive and aerospace industries where components are exposed to extreme heat. Another significant advantage of PPS is its chemical resistance. It exhibits excellent resistance to a wide range of chemicals, including acids, bases, and organic solvents, which is crucial in industries like chemical processing and pharmaceuticals where exposure to corrosive substances is common. Additionally, PPS has inherent flame retardancy, meeting stringent safety standards without the need for additional flame retardants, making it a preferred material for electrical and electronic components. PPS also boasts superior mechanical properties, including high tensile strength and impact resistance. This durability ensures that components made from PPS can withstand rigorous operational conditions without compromising their performance or longevity. Furthermore, PPS has a low coefficient of friction, which reduces wear and tear on moving parts, thereby extending the lifespan of machinery and reducing maintenance costs. In terms of processing, PPS is highly versatile and can be molded using various techniques such as injection molding, extrusion, and compression molding. Its ability to be easily colored and compounded with other materials enhances its aesthetic appeal and functional capabilities. This flexibility in manufacturing processes makes PPS a cost-effective solution for producing complex geometries and high-volume production runs. Moreover, PPS has excellent dimensional stability and minimal moisture absorption, which are critical factors in precision engineering applications. This stability ensures that components maintain their precise dimensions over time, even in varying environmental conditions, which is particularly important in industries like medical devices and precision instruments. Overall, the combination of thermal stability, chemical resistance, mechanical strength, flame retardancy, and processing versatility makes PPS a superior choice over other materials for a wide range of practical applications. Its unique set of properties ensures reliable performance under demanding conditions, making it an indispensable material in various industrial sectors.
Environmental Impact and Sustainability
The environmental impact and sustainability of Polyphenylsulfone (PPS) are critical considerations in its practical applications. PPS, a high-performance engineering plastic, offers several advantages that contribute to its sustainable profile. Firstly, PPS is known for its exceptional durability and resistance to chemicals, heat, and wear, which extends the lifespan of products made from it. This longevity reduces the need for frequent replacements, thereby minimizing waste generation and the environmental footprint associated with manufacturing new materials. Additionally, PPS can be recycled, further enhancing its sustainability by reducing the amount of plastic waste that ends up in landfills and oceans. In terms of energy efficiency, PPS components often require less material due to their high strength-to-weight ratio, which can lead to lighter products that consume less energy during transportation and use. For instance, in automotive applications, lighter PPS parts contribute to improved fuel efficiency, reducing greenhouse gas emissions. Moreover, PPS can be used in various industrial processes that require high temperatures and corrosive environments without degrading, which means fewer resources are needed for maintenance and replacement. The use of PPS also supports sustainable practices in water treatment and filtration systems. Its chemical resistance makes it an ideal material for filters and membranes that can withstand harsh conditions without compromising their performance. This ensures cleaner water with minimal maintenance, reducing the environmental impact of water treatment processes. Furthermore, PPS is used in renewable energy technologies such as wind turbines and solar panels. Its ability to withstand extreme weather conditions and high temperatures makes it a reliable choice for these applications, contributing to the efficient generation of clean energy. By supporting the infrastructure of renewable energy sources, PPS plays a role in reducing global reliance on fossil fuels and mitigating climate change. In summary, the practical applications of PPS not only leverage its technical benefits but also contribute significantly to environmental sustainability. Its durability, recyclability, energy efficiency, and role in renewable energy technologies make it a valuable material for reducing waste, conserving resources, and promoting cleaner production processes. As industries continue to seek more sustainable solutions, the unique properties of PPS position it as a key material in achieving these goals.