What Is A Skid

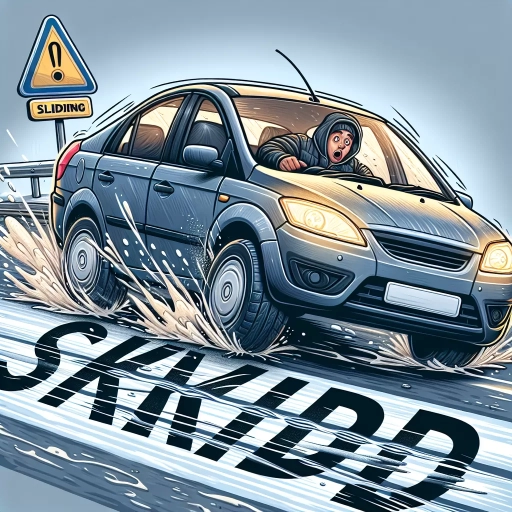
In the realm of industrial and mechanical engineering, the term "skid" refers to a self-contained, pre-assembled unit that houses various components necessary for a specific process or function. These units are designed to be compact, efficient, and easily transportable, making them invaluable in numerous industries such as oil and gas, chemical processing, and power generation. To fully appreciate the significance and functionality of a skid, it is essential to delve into its fundamental aspects. This article will explore three critical dimensions of skids: **Understanding the Basics of a Skid**, which lays the groundwork for comprehending what a skid is and its primary applications; **Components and Design of a Skid**, which examines the intricate details and engineering that go into constructing these units; and **Operational and Maintenance Aspects of a Skid**, which discusses how these systems are operated and maintained to ensure optimal performance. By starting with **Understanding the Basics of a Skid**, we will establish a solid foundation for grasping the complexities and benefits associated with these versatile industrial tools.
Understanding the Basics of a Skid
In the realm of industrial and logistical operations, the term "skid" often surfaces as a crucial component, yet its significance and versatility are frequently underappreciated. A skid, in its most basic form, is a platform or pallet designed to facilitate the efficient movement and storage of goods. However, delving deeper into the concept reveals a multifaceted tool that serves various purposes and comes in different types. To fully grasp the utility of a skid, it is essential to understand its definition and purpose, which underscores its role in streamlining processes and enhancing operational efficiency. Additionally, recognizing the diverse types of skids available can help in selecting the most appropriate one for specific tasks. Lastly, exploring common applications of skids highlights their widespread use across different industries, from manufacturing to transportation. By examining these aspects, we can gain a comprehensive understanding of what makes a skid an indispensable asset in modern operations. This article aims to provide an in-depth look at these key elements, ultimately leading to a deeper understanding of the basics of a skid.
Definition and Purpose
Understanding the basics of a skid begins with a clear definition and an appreciation of its purpose. A skid, in the context of material handling and logistics, is a platform or pallet used to support and transport goods. It typically consists of a flat base and vertical supports, often made from wood, plastic, or metal, designed to facilitate easy loading, unloading, and movement of items. The primary purpose of a skid is to streamline the process of handling and transporting goods by providing a stable and efficient means of managing inventory. At its core, the skid serves several critical functions. Firstly, it enhances safety by elevating goods off the ground, reducing the risk of damage from moisture or pests and making it easier to handle heavy loads without straining workers. Secondly, it improves efficiency by allowing forklifts and other material handling equipment to easily lift and move items around warehouses, distribution centers, and manufacturing facilities. This not only speeds up the logistics process but also minimizes the physical effort required by workers. Moreover, skids are versatile and can be customized to meet specific needs. For instance, they can be designed with additional features such as runners for easier sliding onto trucks or shelves, or they can be made from durable materials to withstand heavy use in industrial settings. The use of skids also promotes better inventory management by enabling goods to be stacked neatly and securely, maximizing storage space and reducing clutter. In addition to these practical benefits, skids play a crucial role in maintaining product integrity during transit. By providing a solid base that prevents items from shifting or falling, skids help protect goods from damage caused by movement or impact. This is particularly important for fragile or sensitive products that require careful handling to ensure they reach their destination in pristine condition. Overall, understanding the definition and purpose of a skid is essential for anyone involved in logistics, warehousing, or manufacturing. By recognizing the role that skids play in enhancing safety, efficiency, and product protection, businesses can optimize their operations and improve overall performance. Whether used in everyday warehouse operations or specialized industrial applications, the humble skid remains an indispensable tool in modern supply chain management.
Types of Skids
Understanding the various types of skids is crucial for grasping the fundamentals of skid dynamics, which are essential in driving, especially under adverse conditions. There are primarily three types of skids: **tire skid**, **brake skid**, and **power skid**, each with distinct characteristics and causes. A **tire skid** occurs when the tires lose traction with the road surface, often due to excessive speed, poor road conditions, or inadequate tire quality. This type of skid can be further divided into **understeer** and **oversteer**. Understeer happens when the vehicle's front tires lose grip, causing the car to continue straight despite steering input. Oversteer, on the other hand, occurs when the rear tires lose traction, resulting in the rear of the vehicle swinging outward. A **brake skid** is triggered by applying the brakes too aggressively, causing the wheels to lock up and lose contact with the road. This can lead to a loss of control and is particularly dangerous on slippery surfaces. Modern vehicles often come equipped with anti-lock braking systems (ABS) to mitigate this risk by rapidly pulsing the brakes to maintain tire contact. The **power skid**, also known as wheelspin or wheelslip, happens when the driver applies too much power to the wheels, causing them to spin without gaining traction. This is common in rear-wheel drive vehicles during acceleration from a standstill or on slippery surfaces. Each type of skid requires a different response to regain control safely. For instance, in an understeer situation, easing off the accelerator and making gentle steering corrections can help realign the vehicle. In an oversteer situation, taking your foot off the accelerator and making subtle steering inputs in the direction of the skid can stabilize the vehicle. For a brake skid, releasing pressure on the brake pedal momentarily allows the wheels to regain traction. Understanding these types of skids not only enhances driving skills but also underscores the importance of vehicle maintenance, such as ensuring proper tire pressure and condition, and using appropriate driving techniques for different road conditions. By recognizing the signs of each type of skid and knowing how to respond effectively, drivers can significantly reduce their risk of being involved in an accident. This knowledge is fundamental to safe and competent driving, making it an essential component of any comprehensive driving education.
Common Applications
When delving into the basics of a skid, it's crucial to understand its common applications, as these uses underscore the versatility and importance of skids in various industries. A skid, essentially a self-contained unit that houses equipment or machinery, is widely utilized across different sectors due to its modular design and ease of transportation. In the **oil and gas industry**, skids are often employed for processing and treating hydrocarbons. These skids can include components such as separators, pumps, and compressors, all integrated into a single unit that can be easily transported to remote drilling sites. This modularity allows for quick setup and operation, significantly reducing the time and cost associated with traditional installation methods. In **chemical processing**, skids are used to handle hazardous materials safely and efficiently. They can be customized to include specific reactors, mixers, and control systems necessary for chemical reactions, ensuring that all operations are contained within a single, manageable unit. This containment is particularly important for safety reasons, as it minimizes the risk of chemical spills and exposure. The **power generation sector** also relies heavily on skids. For instance, generator skids are used to provide temporary or backup power solutions. These skids can be quickly deployed to areas affected by power outages or natural disasters, offering a reliable source of electricity until permanent solutions are implemented. Additionally, skids are used in renewable energy applications such as wind farms and solar installations, where they house inverters and other critical components necessary for converting raw energy into usable electricity. In **water treatment**, skid-mounted systems are essential for providing clean water solutions. These systems can include filtration units, pumps, and disinfection equipment, all packaged together to ensure efficient water purification processes. This is particularly beneficial in remote or emergency situations where access to clean water is limited. Furthermore, **food processing** industries utilize skids to maintain high standards of hygiene and efficiency. Skid-mounted equipment such as pasteurizers, sterilizers, and packaging machinery are designed to be easily cleaned and maintained, reducing downtime and ensuring compliance with stringent food safety regulations. In **construction and mining**, skids are used for various support functions such as air compressors, generators, and hydraulic power units. These units provide the necessary power and support for heavy machinery operations, enhancing productivity and reducing logistical challenges. Understanding the diverse applications of skids highlights their adaptability and the significant role they play in streamlining operations across multiple industries. Whether it's for processing raw materials, generating power, treating water, or supporting construction activities, skids offer a practical solution that combines efficiency with reliability. By recognizing these common applications, one can better appreciate the fundamental importance of skids in modern industrial practices.
Components and Design of a Skid
In the realm of industrial engineering and process systems, a skid is a crucial piece of equipment that integrates various components into a single, self-contained unit. These modular systems are designed to streamline operations, enhance efficiency, and reduce the footprint of industrial processes. Understanding the components and design of a skid is essential for optimizing performance and ensuring compliance with industry standards. This article delves into the key components and their functions, highlighting the critical roles each part plays in the overall operation of the skid. It also explores design considerations and standards, providing insights into the best practices and regulatory requirements that guide skid design. Additionally, we will examine customization options, discussing how skids can be tailored to meet specific needs and applications. By grasping these fundamental aspects, readers will gain a comprehensive understanding of the intricacies involved in creating and utilizing skids, ultimately leading to a deeper appreciation of the basics of skid design and operation. Transitioning seamlessly into the next section, we will begin by understanding the basics of a skid.
Key Components and Their Functions
When discussing the components and design of a skid, it is crucial to delve into the key components and their functions, as these elements are pivotal in ensuring the skid's efficiency, safety, and overall performance. A skid, essentially a self-contained unit that houses various pieces of equipment, is designed to be modular and transportable, making it an essential tool in industries such as oil and gas, chemical processing, and power generation. 1. **Base Frame**: The base frame serves as the structural foundation of the skid. It provides the necessary support and stability for all the equipment mounted on it. Typically made from heavy-duty steel, the base frame is engineered to withstand the weight and operational stresses of the components. 2. **Pumps and Compressors**: These are among the primary functional components of a skid. Pumps are responsible for moving fluids through the system, while compressors handle gas compression. Both are critical for maintaining process flow and pressure within the system. 3. **Valves and Actuators**: Valves control the flow of fluids or gases, allowing for precise regulation of process parameters. Actuators, which can be pneumatic, hydraulic, or electric, operate these valves to ensure smooth and reliable operation. 4. **Instrumentation and Control Systems**: This includes sensors, transmitters, and control panels that monitor and regulate various process variables such as pressure, temperature, flow rate, and level. These systems are vital for maintaining optimal operating conditions and ensuring safety. 5. **Piping and Tubing**: The piping and tubing network connects various components on the skid, facilitating the flow of fluids and gases. Proper design and material selection are essential to prevent leaks and ensure durability. 6. **Electrical Systems**: Electrical components such as motors, starters, and distribution panels power the equipment on the skid. Proper electrical design ensures safe and efficient operation of all electrical devices. 7. **Safety Features**: Safety features like relief valves, fire suppression systems, and emergency shutdown systems are integrated into the skid design to protect personnel and equipment from potential hazards. 8. **Mounting Hardware**: This includes brackets, clamps, and other fastening devices that secure the equipment to the base frame. Proper mounting ensures that all components remain stable during operation and transportation. In summary, each component of a skid plays a unique role in its overall functionality. The base frame provides structural integrity; pumps and compressors handle fluid and gas movement; valves and actuators control flow; instrumentation and control systems monitor and regulate processes; piping and tubing facilitate fluid flow; electrical systems power the equipment; safety features protect against hazards; and mounting hardware secures all components in place. Understanding these key components and their functions is essential for designing and operating an efficient, safe, and reliable skid system.
Design Considerations and Standards
When designing a skid, several critical design considerations and standards must be meticulously addressed to ensure the system's efficiency, safety, and compliance with industry regulations. **Modularity** is a key design principle, allowing for easier installation, maintenance, and future upgrades. This involves compartmentalizing different components into separate modules that can be easily accessed and replaced without disrupting the entire system. **Space Optimization** is another crucial factor; skids are often used in confined spaces, so careful planning is necessary to maximize the use of available space while ensuring all components are accessible for maintenance. **Material Selection** plays a significant role in skid design. The choice of materials should be based on the operating conditions, including temperature, pressure, and exposure to corrosive substances. For instance, stainless steel or fiberglass-reinforced plastic (FRP) might be preferred over carbon steel in environments where corrosion resistance is paramount. **Structural Integrity** must also be considered to ensure the skid can support the weight of all components and withstand external forces such as seismic activity or transportation stresses. **Safety Standards** are paramount and must adhere to relevant industry regulations such as those set by OSHA (Occupational Safety and Health Administration) or API (American Petroleum Institute). This includes incorporating safety features like emergency shutdown systems, fire suppression systems, and proper ventilation to mitigate risks associated with hazardous materials. **Electrical Design** should comply with standards like NEC (National Electric Code) or IEC (International Electrotechnical Commission), ensuring that all electrical components are safely integrated and protected against overloads and short circuits. **Environmental Considerations** are also vital, particularly in industries where skids are exposed to harsh weather conditions or sensitive ecosystems. Designers must consider factors such as weatherproofing, insulation, and environmental impact assessments to ensure the skid operates efficiently without causing harm to the environment. **Operational Efficiency** is another key consideration; designers should aim to minimize energy consumption and optimize performance through the use of energy-efficient components and smart control systems. Finally, **Documentation and Testing** are essential steps in the design process. Detailed documentation of the skid's design, including schematics, manuals, and maintenance schedules, helps in ensuring that the system is properly installed, operated, and maintained. Thorough testing under simulated operational conditions before deployment ensures that the skid meets all performance and safety standards. By carefully addressing these design considerations and adhering to relevant industry standards, engineers can create skids that are not only functional but also safe, efficient, and compliant with regulatory requirements.
Customization Options
When it comes to the components and design of a skid, one of the most critical aspects is the array of customization options available. A skid, essentially a self-contained unit designed to house various equipment and systems, can be tailored to meet specific industrial needs. This flexibility is paramount in ensuring that the skid integrates seamlessly into existing operations, enhances efficiency, and optimizes performance. Customization begins with the selection of materials and construction methods. Depending on the application, skids can be fabricated from stainless steel, carbon steel, or even fiberglass-reinforced plastic (FRP), each offering unique benefits such as corrosion resistance or cost-effectiveness. The structural design can also be modified to accommodate different load capacities and environmental conditions. For instance, skids intended for harsh environments may include additional reinforcement or specialized coatings to withstand extreme temperatures or corrosive substances. Another key area of customization is the layout and configuration of the skid. This involves careful planning to ensure that all components are accessible for maintenance and operation while maximizing space efficiency. Engineers can design skids with modular configurations, allowing for easy expansion or reconfiguration as operational needs evolve. Additionally, the placement of control panels, valves, and other critical components can be optimized to reduce labor time and enhance safety. The integration of various systems within the skid is another significant customization option. This might include electrical systems, piping networks, instrumentation, and control systems. Each system can be tailored to meet specific requirements such as voltage compatibility, flow rates, and data transmission protocols. For example, a skid designed for oil and gas applications might include advanced automation and control systems to monitor and regulate processes in real-time. Furthermore, customization extends to the inclusion of safety features and regulatory compliance. Skids can be equipped with safety valves, fire suppression systems, and emergency shutdown mechanisms to ensure operational safety. Compliance with industry standards such as API, ASME, or OSHA can also be integrated into the design process to avoid legal and operational risks. In conclusion, the customization options for skids are vast and multifaceted. By leveraging these options effectively, industries can create highly specialized units that not only meet but exceed their operational requirements. Whether it's material selection, structural design, system integration, or safety features, each aspect of customization plays a crucial role in enhancing the functionality and efficiency of a skid. This tailored approach ensures that the skid operates reliably and efficiently over its lifespan, contributing significantly to the overall success of industrial operations.
Operational and Maintenance Aspects of a Skid
In the realm of industrial operations, skids play a crucial role in streamlining processes and enhancing efficiency. These self-contained units, often housing complex systems such as pumps, valves, and control panels, require meticulous attention to ensure optimal performance. The operational and maintenance aspects of a skid are multifaceted and critical, involving several key stages. This article delves into the essential components of skid management, starting with the **Installation and Commissioning** phase, where proper setup and initial testing are vital for future reliability. It then explores **Operational Best Practices**, highlighting the routines and protocols that maintain peak functionality. Finally, it addresses **Maintenance and Troubleshooting**, providing insights into regular upkeep and resolving common issues. By understanding these aspects, operators can ensure their skids operate smoothly and efficiently. Transitioning from these detailed discussions, it is clear that grasping these concepts is fundamental to **Understanding the Basics of a Skid**, a foundational knowledge that underpins successful industrial operations.
Installation and Commissioning
**Installation and Commissioning** The installation and commissioning of a skid are critical phases that ensure the system operates efficiently and safely. These processes involve meticulous planning, precise execution, and thorough testing to guarantee that all components function as intended. **Installation:** 1. **Site Preparation:** Before the skid arrives, the site must be prepared to accommodate it. This includes ensuring the foundation is level, secure, and meets the manufacturer's specifications. Any necessary utilities such as power, water, and gas should be readily available. 2. **Unloading and Placement:** The skid is carefully unloaded from the transport vehicle and placed on the prepared site. This step requires specialized equipment to avoid damage to the skid or its components. 3. **Connection to Utilities:** Once in place, the skid is connected to the necessary utilities. This includes electrical connections, piping for fluids or gases, and any other required services. 4. **Integration with Existing Systems:** The skid must be integrated with existing systems such as control rooms, monitoring systems, and other equipment to ensure seamless operation. **Commissioning:** 1. **Pre-Commissioning Checks:** Before starting the commissioning process, a series of pre-commissioning checks are performed to ensure all connections are secure, and there are no leaks or other issues. 2. **System Testing:** Each component of the skid is tested individually and then as part of the overall system to verify that it operates within specified parameters. 3. **Performance Validation:** The entire skid is run through various operational scenarios to validate its performance against design specifications. This includes testing under different load conditions and simulating potential operational challenges. 4. **Training and Documentation:** During commissioning, operators are trained on how to operate and maintain the skid. Comprehensive documentation of the installation and commissioning process is also compiled for future reference. **Safety Considerations:** - **Risk Assessment:** A thorough risk assessment is conducted to identify potential hazards associated with the installation and commissioning process. - **Safety Protocols:** Strict safety protocols are followed to protect personnel and equipment during these phases. - **Compliance:** All activities must comply with relevant industry standards and regulatory requirements. **Operational Readiness:** - **Final Inspections:** After successful commissioning, a final inspection is conducted to ensure everything is in working order. - **Handover:** The skid is formally handed over to the operations team, marking the transition from installation and commissioning to ongoing operation and maintenance. In summary, the installation and commissioning of a skid are complex processes that demand careful planning, precise execution, and rigorous testing to ensure optimal performance and safety. These steps are crucial for transitioning the skid from a manufactured unit to a fully operational system ready for ongoing maintenance and operation.
Operational Best Practices
Operational best practices are crucial for the efficient and safe operation of a skid, ensuring optimal performance, longevity, and compliance with regulatory standards. At the heart of these practices lies a robust maintenance schedule, which includes regular inspections to identify potential issues before they escalate into major problems. This proactive approach involves checking critical components such as valves, pumps, and control systems for signs of wear or malfunction. Additionally, adherence to manufacturer guidelines for maintenance intervals and procedures is essential to prevent premature wear and ensure that all parts are functioning within specified parameters. Training personnel is another key aspect of operational best practices. Operators should be thoroughly educated on the skid's design, operation, and troubleshooting techniques to handle any unexpected issues promptly. This includes understanding safety protocols and emergency shutdown procedures to mitigate risks. Continuous training programs can also help in staying updated with the latest technologies and best practices, enhancing overall operational efficiency. Effective documentation is vital for maintaining transparency and accountability. Detailed records of maintenance activities, operational logs, and any repairs or modifications should be kept meticulously. These records not only help in tracking the history of the skid but also provide valuable insights for future improvements and troubleshooting. Moreover, implementing a culture of safety is paramount. This involves ensuring that all personnel follow strict safety guidelines, use appropriate personal protective equipment (PPE), and are aware of potential hazards associated with skid operations. Regular safety audits and drills can further reinforce this culture by identifying vulnerabilities and preparing staff for emergency situations. Incorporating technology such as automation and monitoring systems can significantly enhance operational efficiency. Real-time monitoring allows for immediate detection of anomalies, enabling swift corrective actions. Automation can streamline processes, reduce manual errors, and optimize resource allocation. Finally, fostering a collaborative environment where feedback is encouraged can lead to continuous improvement. Encouraging operators to report any issues or suggestions for improvement helps in identifying areas that may need adjustment or innovation. This collaborative approach ensures that operational best practices are dynamic and responsive to evolving needs and challenges. By integrating these operational best practices into daily routines, organizations can ensure their skids operate reliably, efficiently, and safely, thereby maximizing productivity while minimizing downtime and risks.
Maintenance and Troubleshooting
**Maintenance and Troubleshooting** Effective maintenance and troubleshooting are crucial for the optimal performance and longevity of a skid, ensuring it operates efficiently and safely. Regular maintenance involves a systematic approach to inspect, repair, and replace components before they fail. This includes routine checks on fluid levels, filter conditions, and the integrity of connections and seals. Operators should also monitor performance metrics such as pressure, temperature, and flow rates to identify any deviations from normal operating parameters. Scheduled maintenance tasks might include cleaning or replacing filters, lubricating moving parts, and performing functional tests on control systems. Troubleshooting, on the other hand, is a methodical process aimed at identifying and resolving issues when they arise. It begins with gathering detailed information about the problem, including symptoms, error messages, and any recent changes or maintenance activities. Operators should consult the skid's documentation and manufacturer guidelines for troubleshooting procedures specific to the equipment. Common issues such as leaks, clogs, or malfunctioning sensors can often be resolved by following step-by-step diagnostic protocols. Advanced troubleshooting may involve using specialized tools like pressure gauges or thermal imaging cameras to pinpoint the source of the problem. Training is essential for both maintenance and troubleshooting; operators should be well-versed in the skid's design, operation, and potential failure modes. This knowledge enables them to anticipate and prevent problems, reducing downtime and enhancing overall reliability. Additionally, maintaining a detailed log of maintenance activities and troubleshooting efforts helps in tracking the skid's history, facilitating future repairs and improving preventive maintenance strategies. Incorporating predictive maintenance technologies such as condition monitoring sensors and data analytics can further enhance the reliability of the skid. These tools provide real-time insights into the operational health of the equipment, allowing for proactive interventions before critical failures occur. By combining regular maintenance with advanced troubleshooting techniques and leveraging modern technologies, operators can ensure their skid operates at peak performance, minimizing disruptions and maximizing productivity. This holistic approach to maintenance and troubleshooting is vital for optimizing the operational efficiency of a skid, making it an indispensable aspect of its overall lifecycle management.