What Does Cfm Mean

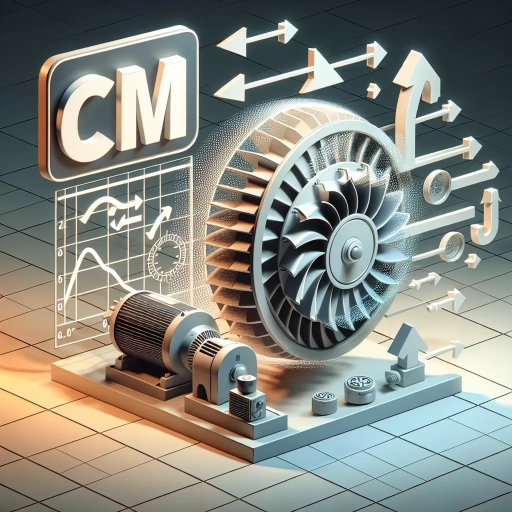
CFM, or Cubic Feet per Minute, is a crucial measurement in various industries, including HVAC, automotive, and industrial manufacturing. Understanding what CFM means is essential for optimizing performance, efficiency, and safety in these fields. This article delves into the multifaceted aspects of CFM, starting with a foundational exploration of its definition and basic principles. We will then dive into the technical aspects of measuring and calculating CFM, highlighting the methodologies and tools used to determine airflow rates. Finally, we will examine the practical uses and importance of CFM in different industries, illustrating how this metric impacts everyday operations and outcomes. By grasping these concepts, readers will gain a comprehensive understanding of CFM's significance. Let's begin by understanding CFM: Definition and Basics.
Understanding CFM: Definition and Basics
Understanding CFM, or Cubic Feet per Minute, is a crucial concept in various fields, including engineering, HVAC, and industrial processes. To grasp the full significance of CFM, it is essential to delve into its definition, historical context, and common applications. This article will explore these aspects in detail, starting with the fundamental question: What CFM Stands For. By understanding what CFM represents, we can better appreciate its historical development and the diverse applications where it plays a vital role. The historical context of CFM reveals how this measurement has evolved over time to become a standard unit in many industries. Additionally, examining the common applications of CFM will highlight its importance in real-world scenarios, from ventilation systems to industrial manufacturing. By breaking down these components, we can gain a comprehensive understanding of CFM and its integral role in modern technology. Let's begin by defining what CFM stands for, as this foundational knowledge is key to appreciating its broader implications.
What CFM Stands For
CFM stands for Cubic Feet per Minute, a unit of measurement used to quantify the volume of air or gas that flows through a given space in one minute. This metric is crucial in various fields such as HVAC (Heating, Ventilation, and Air Conditioning), industrial processes, and automotive systems. In HVAC, CFM helps determine the airflow rate required to maintain comfortable indoor air quality and temperature. For instance, a fan rated at 500 CFM can move 500 cubic feet of air per minute. In industrial settings, CFM is used to measure the airflow in ducts and vents, ensuring proper ventilation and safety standards are met. In automotive contexts, CFM is relevant for engine performance, particularly in terms of air intake systems where it measures the volume of air an engine can draw in per minute. Understanding CFM is essential for designing efficient systems, ensuring optimal performance, and maintaining safety standards across these diverse applications. By knowing the CFM rating of a device or system, users can make informed decisions about its suitability for specific tasks and environments. This fundamental concept underpins many engineering and design principles, making it a key piece of knowledge for professionals and enthusiasts alike.
Historical Context of CFM
The historical context of CFM, or Cubic Feet per Minute, is deeply intertwined with the evolution of industrial and engineering practices. The concept of measuring airflow dates back to the early 19th century when industrialization was gaining momentum. As factories and machinery became more complex, the need to quantify and control airflow for ventilation, cooling, and powering machinery grew. In the late 1800s, engineers began using various units to measure airflow, but these were often inconsistent and lacked standardization. The term "CFM" emerged as a standard unit of measurement in the early 20th century, particularly in the United States. It was adopted widely in industries such as HVAC (Heating, Ventilation, and Air Conditioning), aerospace, and automotive manufacturing. The development of more sophisticated tools and instruments for measuring airflow, such as anemometers and flow meters, further solidified CFM as a critical metric. By the mid-20th century, CFM had become an essential parameter in designing systems for air conditioning, heating, and ventilation, ensuring efficient and safe operation of buildings and machinery. The post-World War II era saw significant advancements in technology and engineering, leading to more precise methods of measuring CFM. This period also witnessed the establishment of regulatory bodies and standards organizations like ASHRAE (American Society of Heating, Refrigerating, and Air-Conditioning Engineers) and ISO (International Organization for Standardization), which helped standardize CFM measurements across different industries. Today, CFM is a fundamental metric used globally in various fields, from residential HVAC systems to large-scale industrial applications, ensuring that air flow is optimized for efficiency, safety, and performance. Understanding the historical context of CFM highlights its importance as a tool for engineers and technicians to design, operate, and maintain complex systems efficiently. It underscores how the need for precise measurement has driven technological innovation and standardization over time. This historical backdrop provides a solid foundation for grasping the definition and basics of CFM, making it easier to appreciate its role in modern engineering practices.
Common Applications of CFM
CFM, or Cubic Feet per Minute, is a crucial measurement in various industries, reflecting the volume of air or gas that flows through a given space in one minute. Here are some common applications of CFM: 1. **HVAC Systems**: In heating, ventilation, and air conditioning (HVAC) systems, CFM is essential for determining the airflow needed to maintain comfortable indoor temperatures and air quality. It helps in sizing fans, blowers, and ducts to ensure efficient air circulation. 2. **Industrial Ventilation**: In industrial settings, CFM is used to calculate the ventilation rates required to remove hazardous fumes, dust, and other airborne contaminants. This ensures a safe working environment by maintaining adequate air exchange rates. 3. **Aerospace and Automotive**: In these industries, CFM is critical for designing and testing air intake systems, fuel injection systems, and exhaust systems. It helps engineers optimize performance, efficiency, and safety. 4. **Medical Equipment**: Medical devices such as ventilators and anesthesia machines rely on precise CFM measurements to deliver controlled amounts of air or gases to patients. This ensures accurate treatment and patient safety. 5. **Dust Collection Systems**: In woodworking, metalworking, and other manufacturing processes, CFM is used to design dust collection systems that effectively capture particulate matter, improving air quality and reducing health risks. 6. **Agricultural Ventilation**: In agricultural settings like barns and greenhouses, CFM helps in maintaining optimal air circulation to regulate temperature and humidity levels, which is vital for animal health and crop growth. 7. **Fire Suppression Systems**: CFM calculations are crucial in designing fire suppression systems that require specific airflow rates to distribute fire retardants effectively. 8. **Laboratory Settings**: Laboratories use CFM to ensure proper ventilation in fume hoods and other equipment, protecting researchers from hazardous chemicals and ensuring compliance with safety standards. 9. **Construction and Building Design**: Architects and builders use CFM to design ventilation systems for new buildings, ensuring that they meet building codes and provide a healthy indoor environment. 10. **Environmental Monitoring**: CFM is used in environmental monitoring to measure airflow in pollution control devices such as scrubbers and electrostatic precipitators, helping to assess their efficiency in reducing emissions. Understanding CFM is fundamental across these diverse applications because it directly impacts the performance, safety, and efficiency of various systems and processes. By accurately measuring and applying CFM values, professionals can ensure optimal operation, compliance with regulations, and enhanced safety standards.
Technical Aspects of CFM: Measurement and Calculation
Understanding the technical aspects of Cubic Feet per Minute (CFM) is crucial for various industrial and engineering applications. CFM, a measure of airflow, is essential for ensuring the efficiency and safety of ventilation systems, HVAC units, and other air-handling equipment. This article delves into the key technical aspects of CFM, starting with **How CFM is Measured**, which explains the methods and techniques used to determine airflow rates accurately. It then explores **Formulas for Calculating CFM**, providing the mathematical frameworks necessary for precise calculations. Finally, it discusses **Tools Used for Measuring CFM**, highlighting the specialized instruments and devices that facilitate these measurements. By grasping these fundamental concepts, professionals can optimize system performance, troubleshoot issues effectively, and ensure compliance with regulatory standards. Let's begin by examining the practical methods involved in **How CFM is Measured**.
How CFM is Measured
Measuring CFM (Cubic Feet per Minute) is a critical process in various industrial and residential applications, including HVAC systems, ventilation systems, and pneumatic tools. The measurement of CFM involves determining the volume of air that flows through a given space or system over a specified period. Here are the key methods and tools used to measure CFM: 1. **Anemometers**: These devices measure air velocity, which can then be used to calculate CFM. There are several types of anemometers, including vane anemometers, hot wire anemometers, and pitot tubes. Each type has its own application and accuracy level. 2. **Flow Hoods**: Flow hoods are used to measure airflow in ducts and vents. They work by capturing the airflow and measuring the pressure difference across the hood, which is then converted into CFM. 3. **Pitot Tubes**: These are inserted into ducts to measure the differential pressure between the static and dynamic pressures of the airflow. This pressure difference is then used to calculate the air velocity and subsequently the CFM. 4. **Thermal Anemometers**: These devices measure the cooling effect of airflow on a heated element, which correlates directly with air velocity and can be used to calculate CFM. 5. **Differential Pressure Sensors**: These sensors measure the pressure drop across a known resistance in the airflow path, such as a venturi or orifice plate, to determine the flow rate. 6. **Volumetric Flow Meters**: These meters directly measure the volume of air flowing through them over a given time period, providing a direct reading of CFM. To calculate CFM from measured data, you typically need to know the cross-sectional area of the duct or vent and the air velocity. The formula for calculating CFM is: \[ \text{CFM} = \text{Area (in square feet)} \times \text{Velocity (in feet per minute)} \] For example, if you measure an air velocity of 100 feet per minute in a duct with a cross-sectional area of 2 square feet, the CFM would be: \[ \text{CFM} = 2 \text{ sq ft} \times 100 \text{ ft/min} = 200 \text{ CFM} \] In summary, measuring CFM involves selecting the appropriate tool based on the application and then using the measured data to calculate the airflow rate. Accurate measurement is crucial for ensuring efficient operation of systems and maintaining optimal performance.
Formulas for Calculating CFM
Calculating CFM (Cubic Feet per Minute) is a crucial aspect of various engineering and technical fields, including HVAC, industrial processes, and ventilation systems. The formula for calculating CFM depends on the specific context and available data. Here are the key formulas: 1. **Using Air Velocity and Duct Area:** \[ \text{CFM} = \text{Velocity (ft/min)} \times \text{Area (sq ft)} \] This formula is widely used in HVAC systems where air velocity can be measured using an anemometer, and the cross-sectional area of the duct is known. 2. **Using Pressure Drop and Duct Characteristics:** For more complex systems, CFM can be calculated using the pressure drop across a duct or system component. The formula involves the use of the Darcy-Weisbach equation: \[ \Delta P = f \cdot \frac{L}{D} \cdot \frac{\rho \cdot v^2}{2} \] Here, \( \Delta P \) is the pressure drop, \( f \) is the friction factor, \( L \) is the length of the duct, \( D \) is the diameter of the duct, \( \rho \) is the air density, and \( v \) is the air velocity. By rearranging this equation to solve for velocity and then using it in conjunction with duct area, CFM can be determined. 3. **Using Fan Performance Curves:** In many cases, especially with fans and blowers, CFM can be read directly from performance curves provided by manufacturers. These curves plot CFM against static pressure or total pressure for different fan speeds. 4. **Using Pitot Tube Measurements:** For field measurements, a pitot tube can be used to measure dynamic pressure. The formula to calculate CFM from pitot tube readings involves converting dynamic pressure to velocity: \[ v = \sqrt{\frac{2 \cdot \Delta P}{\rho}} \] Here, \( v \) is the velocity, \( \Delta P \) is the dynamic pressure measured by the pitot tube, and \( \rho \) is air density. Once velocity is determined, it can be multiplied by duct area to find CFM. 5. **Using Standard Formulas for Specific Applications:** - **For rectangular ducts:** \[ \text{CFM} = v \times w \times h \] where \( v \) is velocity, \( w \) is width, and \( h \) is height of the duct. - **For circular ducts:** \[ \text{CFM} = v \times \pi \times r^2 \] where \( v \) is velocity and \( r \) is radius of the duct. Understanding these formulas allows engineers and technicians to accurately measure and calculate CFM in various scenarios, ensuring efficient system design and operation. Each method has its own set of assumptions and limitations, so selecting the appropriate formula depends on the specific application and available data.
Tools Used for Measuring CFM
When it comes to measuring Cubic Feet per Minute (CFM), several tools are essential for accurate and reliable readings. The primary tools used include **anemometers**, **pitot tubes**, **ventilation meters**, and **flow hoods**. 1. **Anemometers**: These devices measure air velocity directly. There are different types such as vane anemometers, hot wire anemometers, and laser Doppler anemometers. Vane anemometers are the most common and use spinning blades to measure air speed, while hot wire anemometers detect changes in electrical resistance due to airflow. 2. **Pitot Tubes**: These tools measure the differential pressure between the static and dynamic pressures in a duct or pipe. By using Bernoulli's principle, the pressure difference can be converted into air velocity, which then allows for the calculation of CFM. 3. **Ventilation Meters**: These meters are designed specifically for measuring airflow in ventilation systems. They often combine multiple sensors to provide comprehensive data on air flow rates, temperatures, and sometimes even humidity levels. 4. **Flow Hoods**: Also known as capture hoods, these devices enclose the area where air is being exhausted or supplied and measure the total airflow by creating a controlled environment. They are particularly useful for measuring CFM in HVAC systems and industrial settings. Each of these tools has its own set of applications and advantages. For instance, anemometers are versatile and can be used in various environments, while pitot tubes are more suited for precise measurements within ducts. Ventilation meters offer a holistic view of system performance, and flow hoods provide direct measurements of total airflow. By selecting the appropriate tool based on the specific requirements of the measurement task, professionals can ensure accurate CFM readings that are crucial for optimizing ventilation systems, ensuring safety standards, and maintaining efficiency in industrial processes.
Practical Uses and Importance of CFM in Various Industries
Cubic Feet per Minute (CFM) is a crucial metric that plays a pivotal role in various industries, ensuring efficiency, safety, and optimal performance. In the realm of Heating, Ventilation, and Air Conditioning (HVAC) systems, CFM is essential for determining airflow rates, which directly impact indoor air quality and comfort. Beyond HVAC, CFM is equally vital in automotive systems, where it influences engine performance and fuel efficiency by measuring airflow through intake systems. Additionally, in industrial processes, CFM is used to monitor and control airflow in manufacturing environments, ensuring proper ventilation and process optimization. Understanding the practical uses and importance of CFM across these sectors is paramount for maintaining high standards of operation. This article delves into the significance of CFM in these industries, starting with its critical role in HVAC systems, where precise airflow measurements are indispensable for maintaining a healthy and comfortable indoor environment.
CFM in HVAC Systems
In HVAC (Heating, Ventilation, and Air Conditioning) systems, CFM (Cubic Feet per Minute) is a critical metric that measures the volume of air moved by a fan or blower. It quantifies the airflow rate, which is essential for ensuring proper ventilation, heating, and cooling within buildings. Here’s why CFM is vital in HVAC systems: 1. **Ventilation Efficiency**: CFM helps determine if an HVAC system can adequately exchange stale air with fresh air. Proper ventilation is crucial for maintaining indoor air quality, reducing moisture buildup, and preventing the accumulation of pollutants. 2. **Heating and Cooling Performance**: The CFM rating of an HVAC system's fan affects its ability to distribute heated or cooled air evenly throughout a space. Higher CFM ratings typically indicate better air distribution, leading to more consistent temperatures and improved comfort levels. 3. **System Design and Installation**: During the design phase, engineers use CFM to calculate the required airflow for different areas of a building. This ensures that ductwork and vents are sized correctly to handle the necessary airflow without causing undue pressure drops or energy losses. 4. **Energy Efficiency**: Proper CFM ensures that HVAC systems operate efficiently. If the CFM is too low, the system may work harder to achieve desired temperatures, leading to increased energy consumption. Conversely, if it's too high, it could result in wasted energy due to over-ventilation. 5. **Noise Levels**: The CFM of an HVAC fan can also impact noise levels. Fans operating at higher CFMs often produce more noise, which can be a consideration in residential or commercial settings where quiet operation is preferred. 6. **Maintenance and Troubleshooting**: Knowing the CFM rating helps technicians diagnose issues with airflow. Low CFM readings might indicate clogged filters, blocked ducts, or malfunctioning fans, allowing for targeted maintenance and repairs. 7. **Compliance with Standards**: Many building codes and standards specify minimum CFM requirements for ventilation in various types of buildings. Ensuring compliance with these standards is crucial for safety and regulatory purposes. In summary, CFM is a fundamental parameter in HVAC systems that influences ventilation efficiency, heating and cooling performance, system design, energy efficiency, noise levels, maintenance practices, and compliance with regulatory standards. Its accurate measurement and application are essential for creating comfortable, safe, and energy-efficient indoor environments.
CFM in Automotive Systems
In automotive systems, CFM (Cubic Feet per Minute) is a critical metric that measures the airflow rate, which is essential for various components such as air filters, intake systems, and exhaust systems. The CFM rating indicates how much air can be moved through these components in one minute, directly impacting engine performance, efficiency, and overall vehicle health. For instance, a high-performance air filter with a higher CFM rating can allow more air to reach the engine, enhancing power output and fuel efficiency. Conversely, a low CFM air filter may restrict airflow, leading to decreased engine performance and potentially causing issues like poor fuel economy or even engine damage over time. In the context of turbochargers and superchargers, CFM plays a pivotal role in determining how much boost pressure can be generated. These forced induction systems rely on airflow to compress air before it enters the engine's combustion chamber, and their CFM ratings are crucial for matching them with the appropriate engine size and type to ensure optimal performance. Moreover, exhaust systems also benefit from understanding CFM. An exhaust system with an appropriate CFM rating ensures that gases are expelled efficiently, reducing backpressure and improving engine efficiency. Incorrect CFM ratings can lead to decreased horsepower and torque, as well as increased emissions. Additionally, in modern vehicles equipped with advanced technologies like direct fuel injection and variable valve timing, precise airflow control is vital. Here, CFM measurements help engineers optimize these systems for better fuel efficiency, lower emissions, and enhanced drivability. Overall, CFM in automotive systems is not just a technical specification but a key factor in ensuring that vehicles operate at their best potential. It influences everything from raw power output to fuel economy and emissions control, making it an indispensable metric in the design, tuning, and maintenance of automotive engines. By understanding and optimizing CFM in various automotive components, manufacturers can create vehicles that are more powerful, efficient, and environmentally friendly.
CFM in Industrial Processes
In industrial processes, CFM (Cubic Feet per Minute) is a critical metric that measures the volume of air or gas flowing through a system. This measurement is essential for ensuring efficient and safe operations across various industries. For instance, in manufacturing, CFM helps in maintaining optimal ventilation systems to remove hazardous fumes and particles, thereby protecting worker health and safety. In HVAC systems, CFM is crucial for determining the appropriate fan size and airflow rates to maintain comfortable indoor air quality and temperature. In chemical processing, precise CFM measurements are vital for controlling the flow of reactants and products, which directly impacts the efficiency and safety of chemical reactions. Additionally, in power generation, CFM is used to optimize combustion processes in boilers and turbines, enhancing energy output while minimizing emissions. The importance of CFM extends to food processing as well, where it ensures that drying, cooling, and ventilation systems operate effectively to preserve product quality. Furthermore, in automotive manufacturing, CFM is used in paint booths to control airflow, reducing the risk of paint defects and ensuring a smooth finish. Overall, accurate CFM measurements are indispensable for optimizing performance, safety, and compliance in industrial settings, making it a fundamental aspect of process engineering and facility management.