What Is Polyamide

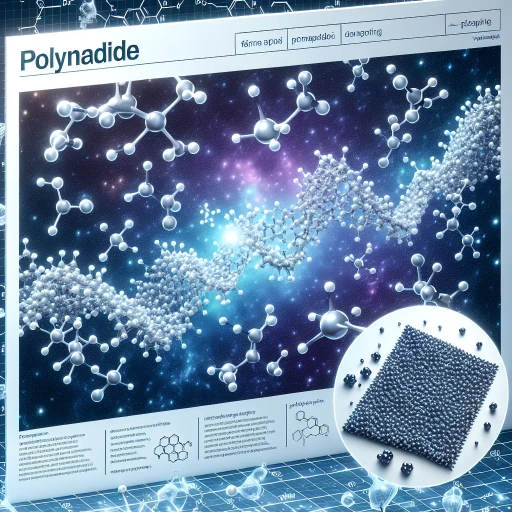
Polyamide, a versatile and widely used synthetic polymer, has become an integral part of modern technology and everyday life. Known for its exceptional strength, durability, and resistance to various environmental factors, polyamide finds applications in diverse industries ranging from textiles and automotive to medical devices and consumer goods. This article delves into the multifaceted nature of polyamide, exploring its fundamental properties and characteristics that make it such a valuable material. We will examine the unique attributes that set polyamide apart from other polymers, including its mechanical strength, thermal stability, and chemical resistance. Additionally, we will discuss the manufacturing and processing techniques that allow for the production of polyamide in various forms and grades. By understanding these aspects, readers will gain a comprehensive insight into what makes polyamide so indispensable. To begin, let us first introduce the basics of polyamide and its historical context in the **Introduction to Polyamide** section.
Introduction to Polyamide
Polyamide, a versatile and widely used synthetic polymer, has become an integral part of modern technology and everyday life. This article provides a comprehensive introduction to polyamide, delving into its fundamental aspects and practical applications. We begin by exploring the **Definition and Chemical Structure** of polyamide, understanding its molecular composition and the properties that make it so valuable. Next, we delve into the **Historical Development and Discovery** of polyamide, tracing its origins and the key milestones that have shaped its evolution. Finally, we examine the **Common Applications and Uses** of polyamide, highlighting its role in industries ranging from textiles and automotive to medical devices and consumer goods. By understanding these facets, readers will gain a thorough appreciation for the significance of polyamide and its diverse impact on various sectors. This introduction sets the stage for a detailed exploration of polyamide, offering insights that will enhance your understanding of this crucial material. Transitioning seamlessly into the heart of our discussion, we invite you to join us on this journey into the world of polyamide. **Introduction to Polyamide**.
Definition and Chemical Structure
Polyamides, commonly known as nylons, are a class of synthetic polymers characterized by the presence of amide linkages in their molecular structure. The definition of polyamide revolves around its chemical composition, which involves the repetition of amide groups (-CONH-) along the polymer chain. This unique structural feature is crucial for understanding the properties and applications of polyamides. Chemically, polyamides are formed through a condensation reaction between a dicarboxylic acid and a diamine, or through the ring-opening polymerization of lactams. The general chemical structure of a polyamide can be represented as [NH-(CH₂)ₙ-CO]ₘ, where 'n' and 'm' are integers that vary depending on the specific type of polyamide. For instance, nylon 6,6 is synthesized from adipic acid and hexamethylene diamine, resulting in a polymer chain with alternating amide linkages and methylene groups. In contrast, nylon 6 is derived from caprolactam, a cyclic amide that opens to form the polymer chain. The amide linkages in polyamides contribute significantly to their physical and mechanical properties. These linkages are polar, allowing for hydrogen bonding between adjacent polymer chains. This intermolecular interaction enhances the strength, stiffness, and thermal stability of polyamides, making them highly versatile materials for various applications. Additionally, the presence of these linkages can influence the crystallinity of the polymer, which in turn affects its melting point, solubility, and resistance to chemicals. Understanding the chemical structure of polyamides is essential for appreciating their diverse uses. From textiles and carpets to engineering plastics and biomedical devices, polyamides are chosen for their excellent mechanical properties, resistance to abrasion, and ability to withstand high temperatures. The specific type of polyamide used often depends on its molecular weight, crystallinity, and the presence of additives or copolymers that can modify its performance characteristics. In summary, the definition and chemical structure of polyamides are foundational to their unique properties and widespread applications. The amide linkages that define these polymers not only dictate their synthesis but also influence their physical behavior, making them indispensable in modern technology and everyday life. As we delve deeper into the world of polyamides, it becomes clear that their versatility stems directly from their well-defined chemical architecture.
Historical Development and Discovery
The historical development and discovery of polyamides are deeply intertwined with the evolution of synthetic polymers in the early 20th century. The journey began in the 1930s when Wallace Carothers, an American chemist working at DuPont, embarked on a mission to create synthetic fibers that could rival natural fibers like silk and wool. Carothers' groundbreaking work led to the synthesis of the first polyamide, nylon, in 1935. This pioneering achievement was not just a chemical breakthrough but also marked the beginning of a new era in materials science. Carothers' method involved condensation polymerization, where he combined adipic acid and hexamethylene diamine to form a strong, flexible, and resistant polymer. The initial application of nylon was in toothbrush bristles, but its potential soon expanded to include textiles, particularly stockings, which were first introduced at the 1939 World's Fair in New York. The impact was immediate; nylon stockings became a sensation due to their durability and aesthetic appeal. Following Carothers' death in 1937, his colleague Julian Hill continued his work, leading to further innovations. However, it was during World War II that polyamides truly came into their own. With silk and other natural fibers in short supply, nylon became a crucial material for military applications such as parachutes, ropes, and even aircraft parts. This wartime demand accelerated research and development, paving the way for broader industrial and consumer uses post-war. In the decades that followed, other types of polyamides were developed, each with unique properties tailored for specific applications. For instance, polyamide 6 (PA6) and polyamide 66 (PA66) became widely used in textiles, engineering plastics, and industrial components due to their high strength-to-weight ratio and resistance to abrasion and chemicals. These advancements were facilitated by improvements in manufacturing processes and the discovery of new monomers. The discovery and development of polyamides have had a profound impact on modern society. From clothing and textiles to automotive parts and medical devices, polyamides have become ubiquitous materials that enhance performance and durability across various industries. Their versatility has also led to ongoing research into new applications, such as biodegradable polyamides and nanocomposites, ensuring that this class of polymers continues to play a vital role in technological innovation well into the future. The legacy of Wallace Carothers and his team serves as a testament to the transformative power of scientific inquiry and its ability to shape our daily lives through groundbreaking discoveries.
Common Applications and Uses
Polyamides, commonly known as nylons, are versatile polymers with a wide range of applications across various industries due to their unique combination of mechanical, thermal, and chemical properties. One of the most significant uses of polyamides is in the textile industry, where they are used to produce durable and resistant fabrics. Nylon fibers are often used in clothing, particularly in outdoor gear such as hiking boots, jackets, and camping equipment because of their strength, elasticity, and resistance to abrasion and moisture. Additionally, polyamides are integral in the production of carpets and upholstery due to their high wear resistance and ease of maintenance. In the automotive sector, polyamides play a crucial role in the manufacture of components that require high performance and durability. They are used in engine parts, fuel lines, and electrical connectors due to their excellent heat resistance and chemical stability. The use of polyamides in these applications helps reduce weight while maintaining structural integrity, contributing to improved fuel efficiency and overall vehicle performance. Polyamides also find extensive use in the medical field. They are biocompatible and can be sterilized, making them ideal for medical devices such as catheters, surgical meshes, and implantable devices like pacemakers. Their flexibility and resistance to chemicals make them suitable for use in medical tubing and other equipment that requires high purity and reliability. Furthermore, polyamides are widely used in the packaging industry. They are employed in the production of film wraps for food packaging due to their barrier properties against oxygen, carbon dioxide, and moisture. This helps preserve food freshness and extends shelf life. Additionally, polyamides are used in beverage bottles and containers because they offer a balance of strength, flexibility, and resistance to chemicals. In construction and building materials, polyamides are used as additives to improve the performance of concrete and other building materials. They enhance the durability and strength of these materials by improving their resistance to environmental factors such as weathering and chemical exposure. Lastly, polyamides have significant applications in electronics. They are used in the manufacture of connectors, switches, and other components due to their excellent electrical insulation properties and resistance to heat. This makes them essential for ensuring the reliability and safety of electronic devices. Overall, the versatility of polyamides stems from their robust mechanical properties, chemical resistance, and thermal stability, making them indispensable in a variety of industrial applications. Their ability to be tailored for specific uses through different formulations and processing techniques further expands their utility across diverse sectors.
Properties and Characteristics of Polyamide
Polyamide, a versatile and widely used synthetic polymer, is renowned for its exceptional properties and characteristics that make it a staple in various industries. From textiles and automotive components to medical devices and industrial machinery, polyamide's unique attributes have cemented its place as a material of choice. This article delves into the multifaceted nature of polyamide, exploring its physical properties such as strength, flexibility, and durability, which contribute to its robust performance in demanding applications. Additionally, we will examine its chemical properties, particularly its resistance to solvents and chemicals, highlighting its ability to withstand harsh environments. Finally, we will discuss its thermal properties, including its melting point and thermal stability, which are crucial for understanding its behavior under different temperature conditions. By understanding these key aspects, readers will gain a comprehensive insight into why polyamide remains a preferred material across diverse sectors. This introduction sets the stage for a detailed exploration of polyamide's characteristics, leading us to an in-depth **Introduction to Polyamide**.
Physical Properties: Strength, Flexibility, and Durability
Polyamide, a versatile and widely used synthetic polymer, is renowned for its exceptional physical properties, which include strength, flexibility, and durability. **Strength** is one of the most notable attributes of polyamide. It possesses high tensile strength, making it an ideal material for applications where mechanical robustness is crucial. This inherent strength allows polyamide to withstand significant loads and stresses without compromising its structural integrity, which is why it is often used in industrial textiles, automotive components, and even in medical devices. **Flexibility** is another key characteristic of polyamide. Unlike many other polymers that are brittle or rigid, polyamide exhibits a considerable degree of flexibility. This flexibility enables it to absorb impact and deform without breaking, making it suitable for a variety of dynamic applications such as clothing, carpets, and even in some types of sporting equipment. The ability to bend and recover without losing shape or integrity adds to its versatility and makes it a preferred choice in many industries. **Durability** rounds out the trio of physical properties that make polyamide so valuable. Polyamide materials are highly resistant to wear and tear, as well as environmental factors such as moisture and chemicals. This resistance to degradation ensures that products made from polyamide can withstand harsh conditions over extended periods without significant deterioration. For instance, polyamide fibers used in outdoor clothing and gear remain functional even after repeated exposure to rain, sun, and other environmental stresses. Similarly, in industrial settings, polyamide components can endure the rigors of continuous use without losing their performance capabilities. The combination of these physical properties—strength, flexibility, and durability—makes polyamide an indispensable material across various sectors. From the manufacturing of high-performance textiles to the production of durable engineering plastics, polyamide's unique blend of attributes ensures that it meets the demands of diverse applications. Its ability to balance rigidity with flexibility and resilience with durability has cemented its place as a cornerstone material in modern technology and everyday life. Whether it's in the form of nylon fibers in clothing or as engineering plastics in machinery, polyamide's physical properties make it an essential component that enhances the performance and longevity of countless products.
Chemical Properties: Resistance to Solvents and Chemicals
Polyamide, a versatile and widely used synthetic polymer, exhibits a range of chemical properties that make it highly valuable in various applications. One of the most significant chemical properties of polyamide is its resistance to solvents and chemicals. This resistance is primarily due to the strong hydrogen bonding between the amide linkages in the polymer chain, which creates a robust and stable molecular structure. As a result, polyamide materials are less prone to dissolution or degradation when exposed to many common solvents such as water, alcohols, and hydrocarbons. The inherent chemical stability of polyamide also extends to its resistance against acidic and alkaline substances. While it is not entirely impervious to all chemicals, polyamide generally shows good resistance to mild acids and bases, making it suitable for use in environments where exposure to such substances is likely. However, it is important to note that concentrated acids or bases can still cause degradation over time. In addition to solvent resistance, polyamide's chemical inertness makes it an excellent choice for applications requiring minimal interaction with other substances. For instance, in textile manufacturing, polyamide fibers like nylon are preferred for their ability to withstand various chemical treatments without losing their integrity. Similarly, in engineering plastics, polyamides are used in components that need to endure exposure to fuels, lubricants, and other chemicals without compromising their mechanical properties. The resistance of polyamide to chemicals also plays a crucial role in its use in food packaging and medical devices. Here, the material's non-reactive nature ensures that it does not leach harmful substances into food or biological tissues, thereby maintaining safety standards. Furthermore, this property allows polyamide to be sterilized using various methods such as autoclaving or gamma radiation without undergoing significant degradation. In summary, the chemical resistance of polyamide is a key characteristic that underpins its widespread utility across diverse industries. Whether in textiles, engineering plastics, packaging materials, or medical devices, this property ensures that polyamide-based products can perform reliably under a variety of chemical conditions. This robustness not only enhances the durability and lifespan of these products but also contributes to their safety and reliability in critical applications.
Thermal Properties: Melting Point and Thermal Stability
Thermal properties, particularly melting point and thermal stability, are crucial characteristics of polyamides that significantly influence their applications and performance. The melting point of a polyamide is the temperature at which it transitions from a solid to a liquid state, and this value varies depending on the specific type of polyamide. For instance, nylon 6, one of the most common polyamides, has a melting point around 215-220°C, while nylon 6,6 melts at approximately 260-265°C. These high melting points make polyamides suitable for use in high-temperature environments and applications such as automotive parts, electrical components, and industrial textiles. Thermal stability, on the other hand, refers to the ability of a polyamide to resist degradation when exposed to heat over time. Polyamides generally exhibit good thermal stability due to their strong intermolecular hydrogen bonding between amide groups. This stability is essential for maintaining the material's mechanical properties and structural integrity under various thermal conditions. For example, in injection molding processes, polyamides can withstand the high temperatures involved without significant degradation, ensuring consistent product quality. The combination of high melting points and good thermal stability makes polyamides versatile materials for diverse industries. In textiles, polyamide fibers like nylon are used in clothing and carpets because they retain their shape and strength even when exposed to heat from washing or drying. In engineering applications, such as gears and bearings, the thermal properties of polyamides allow them to operate efficiently under continuous mechanical stress and elevated temperatures. Moreover, the thermal properties of polyamides can be further enhanced through various modifications. For instance, incorporating additives or fillers can improve thermal stability by reducing the material's susceptibility to oxidative degradation. Additionally, blending different types of polyamides or combining them with other polymers can tailor their melting points and thermal stability to meet specific application requirements. In summary, the melting point and thermal stability of polyamides are key factors that contribute to their widespread use across various sectors. These properties enable polyamides to perform reliably under a range of thermal conditions, making them an indispensable material in modern manufacturing and engineering. Understanding these thermal properties is essential for optimizing the use of polyamides in different applications and ensuring the longevity and performance of products made from these versatile polymers.
Manufacturing and Processing of Polyamide
Polyamide, a versatile and widely used synthetic polymer, plays a crucial role in various industries including textiles, automotive, and consumer goods. The manufacturing and processing of polyamide involve several key steps that determine its final properties and applications. This article delves into the intricate processes behind polyamide production, focusing on three critical aspects: **Production Methods: Polymerization Processes**, which explore the chemical reactions that form the polymer chain; **Raw Materials and Monomers Used**, highlighting the essential components that contribute to polyamide's unique characteristics; and **Post-Production Treatments and Modifications**, discussing how the material is refined and tailored for specific uses. Understanding these elements is essential for appreciating the complexity and versatility of polyamide. As we navigate through these critical stages, we will gain a comprehensive insight into what makes polyamide such a valuable material in modern manufacturing. This journey begins with an **Introduction to Polyamide**, setting the stage for a detailed exploration of its production and processing.
Production Methods: Polymerization Processes
Polymerization processes are the cornerstone of polyamide production, involving the chemical reaction of monomers to form long-chain polymers. There are several key methods employed in the manufacturing of polyamides, each with its own set of advantages and applications. **Condensation Polymerization** is one of the most common techniques, where two monomers react to form a polymer chain and a small molecule, typically water or methanol, is released as a byproduct. This method is widely used for producing nylon 6,6, a popular polyamide known for its high strength, elasticity, and resistance to abrasion. The process involves the reaction of adipic acid and hexamethylene diamine, which are combined in a reactor under controlled conditions of temperature and pressure. Another significant method is **Ring-Opening Polymerization**, which is particularly useful for producing nylon 6. In this process, caprolactam—a cyclic monomer—is heated to initiate ring-opening, leading to the formation of a linear polymer chain. This technique allows for precise control over molecular weight and polymer structure, making it ideal for producing high-quality polyamides with specific properties. **Anionic Polymerization** is another advanced method that offers excellent control over polymer architecture and molecular weight distribution. This process involves the use of an initiator to start the polymerization reaction, which proceeds rapidly under controlled conditions. Anionic polymerization is often used for producing specialty polyamides with tailored properties for specific applications. In addition to these chemical processes, **Melt Polymerization** is also employed, particularly for producing high-molecular-weight polyamides. This method involves heating the monomers to their melting points, allowing them to react and form the polymer chain without the need for solvents. Melt polymerization is energy-efficient and environmentally friendly, as it minimizes waste and reduces the need for post-polymerization treatments. Each of these polymerization processes can be tailored to produce polyamides with diverse properties, making them versatile materials for various industries. For instance, polyamides produced through condensation polymerization are often used in textiles and engineering plastics due to their excellent mechanical properties. On the other hand, those produced via ring-opening polymerization find applications in automotive parts and industrial components due to their high impact resistance and thermal stability. Understanding these polymerization processes is crucial for optimizing polyamide production, ensuring consistent quality, and meeting the demands of different end-use applications. By selecting the appropriate polymerization method, manufacturers can control the molecular structure and properties of the resulting polyamide, thereby enhancing its performance and suitability for various uses. This precision in production underscores the importance of polymerization processes in the manufacturing and processing of polyamides.
Raw Materials and Monomers Used
In the manufacturing and processing of polyamide, the selection and quality of raw materials and monomers are crucial for determining the final product's properties and performance. Polyamides, commonly known as nylons, are synthesized from monomers that can be either amino acids or lactams. For instance, nylon 6 is produced from caprolactam, a cyclic amide monomer, through a ring-opening polymerization process. This process involves heating caprolactam in the presence of a catalyst to initiate the polymerization reaction, resulting in a high-molecular-weight polymer. On the other hand, nylon 6,6 is synthesized from two monomers: adipic acid and hexamethylene diamine. These monomers undergo a condensation polymerization reaction where the acid and amine groups react to form amide linkages, releasing water as a byproduct. The choice between these monomers significantly influences the physical and chemical properties of the polyamide. For example, nylon 6,6 generally has higher melting and crystallization temperatures compared to nylon 6, making it more suitable for applications requiring high thermal stability. The purity and consistency of these raw materials are essential for achieving uniform polymer properties. Impurities can lead to defects in the polymer chain, affecting its mechanical strength, thermal resistance, and overall durability. Additionally, additives such as stabilizers, lubricants, and impact modifiers may be incorporated during the manufacturing process to enhance specific characteristics of the polyamide. These additives can improve processability, reduce wear and tear during use, or enhance resistance to environmental factors like UV light or chemicals. The sourcing and sustainability of these raw materials also play a critical role in modern manufacturing practices. Many manufacturers are shifting towards using bio-based monomers derived from renewable resources such as plant oils or biomass. This trend not only reduces dependence on fossil fuels but also contributes to a more environmentally friendly production process. Furthermore, advancements in recycling technologies have made it possible to recover and reuse polyamide materials at the end of their life cycle, further reducing waste and conserving resources. In summary, the careful selection and processing of raw materials and monomers are fundamental steps in the manufacturing of polyamides. Understanding the chemical nature of these starting materials and their interactions during polymerization is key to producing high-quality polyamides with tailored properties for various applications ranging from textiles and packaging to automotive and industrial components. By focusing on material purity, sustainability, and innovative production techniques, manufacturers can ensure that polyamides continue to meet the evolving demands of diverse industries while minimizing their environmental footprint.
Post-Production Treatments and Modifications
Post-production treatments and modifications are crucial steps in the manufacturing and processing of polyamide, enhancing its properties and suitability for various applications. After the initial production process, polyamide materials can undergo several treatments to improve their mechanical, thermal, and chemical resistance. One common treatment is annealing, which involves heating the polyamide to a specific temperature below its melting point to relieve internal stresses and improve dimensional stability. This process can significantly enhance the material's impact resistance and reduce warping. Another significant modification is the addition of fillers and reinforcements. For instance, incorporating glass fibers or carbon fibers into polyamide can dramatically increase its tensile strength, stiffness, and heat deflection temperature, making it suitable for high-performance applications such as automotive parts and industrial components. Similarly, adding mineral fillers like talc or calcium carbonate can improve the material's rigidity and thermal stability while reducing its cost. Surface treatments are also essential for polyamide products. Chemical treatments like plasma etching or corona treatment can enhance the surface energy of polyamide, improving its adhesion properties for painting, printing, or bonding with other materials. Additionally, physical surface modifications such as sanding or laser engraving can create specific textures or patterns that are beneficial for certain applications. In terms of chemical modifications, polyamides can be compounded with various additives to achieve specific properties. For example, adding UV stabilizers can protect the material from degradation caused by sunlight exposure, while incorporating flame retardants can make polyamide suitable for use in electrical components where fire safety is a concern. Lubricants like silicone or PTFE can be added to reduce friction and wear in moving parts. Furthermore, polyamides can undergo secondary processing techniques such as machining, injection molding, or extrusion to produce complex shapes and geometries. These processes allow for precise control over the final product's dimensions and surface finish, ensuring that it meets the required specifications for its intended use. In summary, post-production treatments and modifications play a vital role in optimizing the performance of polyamide materials. By applying these techniques, manufacturers can tailor polyamide's properties to meet the demands of diverse industries, from automotive and aerospace to consumer goods and medical devices. This flexibility and adaptability make polyamide an invaluable material in modern manufacturing.