Why Is My Shipment On Hold Dhl

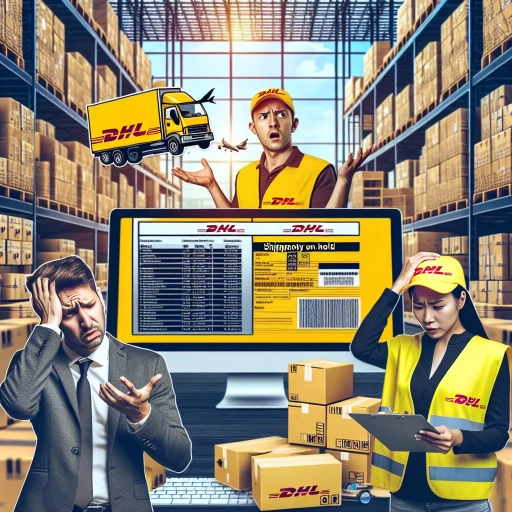
When your shipment is on hold with DHL, it can be frustrating and confusing, especially if you are relying on timely delivery. Understanding the reasons behind such delays is crucial for both senders and recipients. This article delves into the various factors that could cause your DHL shipment to be held up. We will explore the **Common Reasons for DHL Shipment Holds**, which include issues such as customs clearance problems, missing or incorrect documentation, and security concerns. Additionally, we will examine **Logistical and Operational Factors**, such as transportation disruptions, warehouse congestion, and technical glitches that can impact delivery timelines. Finally, we will discuss **Customer and Sender Responsibilities**, highlighting the importance of accurate labeling, proper packaging, and compliance with shipping regulations. By understanding these aspects, you can better navigate the complexities of international shipping and take proactive steps to avoid delays. Let's start by looking at the **Common Reasons for DHL Shipment Holds**.
Common Reasons for DHL Shipment Holds
When shipping goods internationally, delays can be frustrating and costly. For DHL shipments, holds can occur due to several common reasons that are crucial to understand for both senders and recipients. One of the primary causes is **Incomplete or Incorrect Shipping Information**, which can lead to misrouting or failure to deliver the package. Another significant issue is **Customs Clearance Problems**, where shipments may be held up due to non-compliance with customs regulations or missing documentation. Additionally, **Compliance with Regulatory Requirements** is a critical factor, as shipments must adhere to various laws and regulations in both the country of origin and destination. Understanding these key reasons can help mitigate delays and ensure smoother logistics operations. In this article, we will delve into these common reasons for DHL shipment holds, providing insights and solutions to help you navigate the complexities of international shipping efficiently. By exploring these factors, you can better prepare your shipments and avoid unnecessary delays, ensuring your goods reach their destination on time. Here, we will examine the Common Reasons for DHL Shipment Holds.
1. Incomplete or Incorrect Shipping Information
One of the most common reasons for DHL shipment holds is incomplete or incorrect shipping information. This issue can arise from a variety of sources, including errors in the sender's address, recipient's address, or even the details of the shipment itself. When shipping information is incomplete or incorrect, it can lead to significant delays and complications. For instance, if the recipient's address is missing a crucial detail such as a suite number or postal code, DHL may not be able to deliver the package efficiently. Similarly, if the sender's information is inaccurate, it can hinder DHL's ability to contact them for clarification or additional details. Incorrect shipping information can also trigger security checks and compliance reviews. For example, if the customs declaration form contains discrepancies or omissions, it may flag the shipment for further inspection by customs authorities. This not only delays the delivery but also increases the risk of additional fees or even confiscation of the shipment. Furthermore, incorrect information about the contents of the package can lead to issues with customs clearance and compliance with international regulations. To avoid such holds, it is essential to ensure that all shipping details are accurate and complete before submitting the package for shipment. This includes double-checking addresses, verifying contact information, and accurately describing the contents of the package. Additionally, using automated tools and software that validate shipping information can help mitigate these errors. By taking these precautions, senders can significantly reduce the likelihood of their shipments being held due to incomplete or incorrect shipping information, thereby ensuring timely and smooth delivery of their packages. In summary, incomplete or incorrect shipping information is a prevalent cause of DHL shipment holds. It can lead to delays, additional costs, and potential legal issues. Therefore, meticulous attention to detail in preparing shipping documents is crucial to avoid these complications and ensure that shipments reach their destinations without interruption. By understanding and addressing this common issue proactively, senders can enhance their overall shipping experience and maintain customer satisfaction.
2. Customs Clearance Issues
Customs clearance issues are a common reason for DHL shipment holds, often causing frustration and delays for both senders and recipients. These issues arise when shipments fail to comply with the regulatory requirements of the destination country, leading to a halt in the delivery process. One of the primary reasons for customs clearance issues is **inaccurate or incomplete documentation**. If the commercial invoice, bill of lading, or other necessary documents are missing, contain errors, or do not match the contents of the shipment, customs officials may detain the package until the discrepancies are resolved. This can include incorrect product descriptions, missing Harmonized System (HS) codes, or insufficient information about the shipper and consignee. Another significant factor is **non-compliance with import regulations**. Each country has its own set of rules and restrictions on what can be imported, and failure to adhere to these regulations can result in shipment holds. For instance, certain products may require special permits or licenses, while others might be subject to specific labeling requirements or health and safety standards. If these requirements are not met, customs authorities will hold the shipment until compliance is achieved. **Duty and tax issues** also frequently contribute to customs clearance problems. If the duties and taxes associated with the shipment are not properly calculated or paid, it can lead to delays. Additionally, if the shipment's value is misdeclared or if there are discrepancies in the payment of duties and taxes, customs officials may flag the shipment for further review. Furthermore, **restricted or prohibited items** can cause significant delays. Certain goods, such as hazardous materials, firearms, or controlled substances, are subject to strict regulations and may require special permits. If these items are not properly declared or if they are prohibited in the destination country, the shipment will be held until the issue is resolved. To mitigate these issues, it is crucial for shippers to ensure that all documentation is accurate and complete before sending a package. Conducting thorough research on import regulations and ensuring compliance with all relevant laws and regulations can also help avoid delays. Regular communication with DHL and customs authorities can facilitate quicker resolution of any issues that arise, minimizing the impact on delivery times. By understanding and addressing these common customs clearance issues proactively, shippers can reduce the likelihood of their shipments being held and ensure smoother, more efficient delivery processes.
3. Compliance with Regulatory Requirements
Compliance with regulatory requirements is a critical factor that can lead to shipment holds at DHL. International shipping involves navigating a complex web of laws, regulations, and standards set by various countries and international bodies. Non-compliance can result in delays, fines, or even the seizure of shipments. For instance, customs regulations vary significantly from one country to another, and failure to adhere to these rules can cause shipments to be held until the necessary documentation is provided or corrected. This includes ensuring that all required permits and licenses are in place, accurate and complete customs forms are submitted, and that goods are properly classified according to the Harmonized System (HS) codes. Additionally, shipments may be held if they do not meet specific safety and security standards. For example, hazardous materials must be properly labeled and packaged according to international standards such as those set by the International Air Transport Association (IATA) and the International Maritime Organization (IMO). Similarly, shipments containing restricted or prohibited items, such as certain chemicals or electronics, may be detained until they comply with relevant regulations. Moreover, trade compliance is another area where non-adherence can lead to shipment holds. Export controls and sanctions imposed by governments can restrict the movement of certain goods to specific countries or entities. DHL must ensure that all shipments comply with these restrictions to avoid legal repercussions. This includes verifying the identity of the shipper and recipient, checking against denied party lists, and ensuring that the goods being shipped are not subject to export restrictions. In some cases, shipments may also be held due to discrepancies in documentation related to regulatory compliance. This could include missing or incorrect commercial invoices, bills of lading, or certificates of origin. Ensuring that all documentation is accurate and complete is crucial for smooth customs clearance. To mitigate these issues, shippers should work closely with DHL to ensure that all regulatory requirements are met before the shipment is dispatched. This includes providing detailed information about the contents of the shipment, ensuring compliance with local and international regulations, and maintaining accurate records of all documentation. By doing so, shippers can minimize the risk of their shipments being held due to non-compliance with regulatory requirements, thereby ensuring timely delivery and avoiding unnecessary delays and costs.
Logistical and Operational Factors
In the intricate world of logistics and operations, numerous factors can significantly impact the efficiency and reliability of supply chains. These factors, often interlinked and multifaceted, can lead to delays, increased costs, and reduced customer satisfaction. This article delves into three critical logistical and operational factors that frequently disrupt the smooth flow of goods: weather conditions and natural disasters, traffic and congestion delays, and warehouse and facility constraints. Each of these elements can independently or collectively hinder the operational prowess of logistics companies, leading to unforeseen challenges. Understanding these factors is crucial for mitigating risks and optimizing supply chain performance. By examining these common obstacles, we can better appreciate why shipments often experience holds, a phenomenon that affects even major logistics providers like DHL. This insight is particularly relevant when considering common reasons for DHL shipment holds, highlighting the importance of proactive planning and robust contingency strategies in the logistics industry.
1. Weather Conditions and Natural Disasters
Weather conditions and natural disasters are significant logistical and operational factors that can cause shipments to be held up, particularly when dealing with international courier services like DHL. Severe weather events such as hurricanes, typhoons, blizzards, and floods can disrupt transportation networks, including air, land, and sea routes. For instance, a hurricane might force the closure of airports, making it impossible for planes to take off or land, while a blizzard could render roads impassable for trucks. Similarly, floods can damage infrastructure like bridges and roads, halting ground transportation. These disruptions not only delay shipments but also pose risks to the safety of both the cargo and the personnel involved in its transit. Natural disasters also impact warehouse operations and storage facilities. Earthquakes, for example, can cause structural damage to buildings, necessitating temporary closures for safety inspections and repairs. This can lead to a backlog of shipments as operations are suspended until the facilities are deemed safe for use. Additionally, extreme weather conditions such as heatwaves or cold snaps can affect the integrity of certain types of cargo, particularly perishable goods or sensitive electronics, which may require specific temperature-controlled environments to maintain their quality. The unpredictability of weather conditions and natural disasters makes it challenging for logistics companies to maintain consistent delivery schedules. Advanced weather forecasting helps mitigate some risks by allowing for proactive measures such as rerouting shipments or securing cargo in anticipation of adverse weather. However, even with these precautions, unforeseen events can still occur, leading to delays. Moreover, regulatory responses to natural disasters can further complicate logistics. Governments may impose emergency restrictions on travel and transportation to ensure public safety, which can include curfews, roadblocks, or airspace closures. These measures are essential for protecting lives but inevitably impact the flow of goods. In summary, weather conditions and natural disasters are critical factors that can significantly impact logistical operations and cause shipments to be held up. Understanding these risks is crucial for both shippers and recipients as it allows them to plan accordingly and manage expectations regarding delivery times. DHL, like other logistics providers, must navigate these challenges while ensuring the safety of their personnel and the integrity of the cargo they handle. By being aware of these potential disruptions, customers can better understand why their shipments might be delayed and appreciate the efforts made by logistics companies to overcome such obstacles.
2. Traffic and Congestion Delays
Traffic and congestion delays are significant logistical and operational factors that can cause shipments to be held up, particularly when using services like DHL. These delays can arise from various sources, including heavy traffic conditions, road construction, accidents, and inclement weather. In urban areas, peak hour traffic congestion is a common issue, where dense populations and limited road infrastructure lead to prolonged travel times. For instance, a shipment scheduled to move through a major city during rush hour may experience substantial delays due to the sheer volume of vehicles on the road. Additionally, unforeseen events such as accidents or natural disasters can suddenly disrupt traffic flow, causing unexpected delays. Road closures due to maintenance or construction projects also contribute to congestion, as they force traffic to reroute through alternative paths that may not be as efficient. Weather conditions like heavy rain, snowstorms, or extreme temperatures can further exacerbate these issues by reducing visibility and making roads hazardous. The impact of these delays is multifaceted. From a logistical standpoint, they can disrupt the entire supply chain by causing missed delivery deadlines and affecting the timely arrival of goods. This can lead to increased costs for both the shipping company and the recipient, as well as potential penalties for late delivery. Operationally, traffic and congestion delays require real-time adjustments in routing and scheduling to mitigate their effects. DHL and other logistics providers must invest in advanced tracking systems and dynamic routing algorithms to navigate through congested areas efficiently. Moreover, these delays highlight the importance of contingency planning in logistics operations. Companies must have flexible strategies in place to handle unexpected disruptions, such as alternative routes or backup transportation options. This not only helps in managing customer expectations but also ensures that business operations remain as smooth as possible despite external challenges. In conclusion, traffic and congestion delays are critical factors that can significantly impact shipment timelines. Understanding these challenges allows logistics providers like DHL to implement proactive measures such as real-time monitoring, flexible routing, and contingency planning to minimize their impact. By addressing these issues effectively, companies can enhance their operational efficiency and maintain high levels of customer satisfaction despite the complexities of modern transportation networks.
3. Warehouse and Facility Constraints
Warehouse and facility constraints are critical logistical and operational factors that can significantly impact the efficiency and timeliness of shipments, including those handled by DHL. These constraints often arise from a combination of physical limitations, operational inefficiencies, and resource shortages. For instance, inadequate storage space can lead to congestion within the warehouse, slowing down the processing and dispatch of shipments. This congestion can result in delays as packages are held up while waiting for available space or processing capacity. Additionally, outdated or insufficient equipment can hinder the speed and accuracy of sorting, packaging, and loading operations. For example, if a facility lacks automated sorting systems or has limited forklift capacity, manual handling becomes necessary, which is not only slower but also more prone to errors. Another significant constraint is the availability of skilled labor. Warehouses require a workforce with specific skills to manage inventory, operate machinery, and ensure compliance with safety and regulatory standards. Shortages in qualified personnel can lead to bottlenecks in the handling process, causing shipments to be held up until adequate staffing levels are restored. Furthermore, facilities must adhere to strict safety protocols and regulatory requirements, which can sometimes limit operational capacity. Compliance with these regulations is essential but may necessitate temporary shutdowns or reduced operations during inspections or maintenance activities. Seasonal fluctuations in demand also play a crucial role in warehouse and facility constraints. During peak periods such as holidays or special events, warehouses may experience overwhelming volumes of shipments that exceed their normal capacity. This surge in demand can strain resources, leading to delays as facilities struggle to keep up with the increased workload. In such scenarios, DHL and other logistics providers might implement temporary measures like extended working hours or additional staffing to mitigate these constraints. However, even with these measures, some delays are inevitable due to the sheer volume of shipments being processed. In summary, warehouse and facility constraints are multifaceted challenges that can cause shipments to be held up due to various factors including physical space limitations, equipment inadequacies, labor shortages, regulatory compliance issues, and seasonal demand surges. Addressing these constraints requires careful planning, investment in modern technology, efficient workforce management strategies, and proactive measures to handle peak periods effectively. By understanding these constraints better, logistics providers like DHL can work towards optimizing their operations to minimize delays and ensure smoother shipment processing.
Customer and Sender Responsibilities
In the intricate world of logistics, understanding the responsibilities of both customers and senders is crucial for ensuring smooth and efficient transactions. This article delves into the key areas that can significantly impact the success of a shipment, highlighting three critical aspects: **Proper Packaging and Labeling**, **Accurate Declaration of Goods**, and **Payment and Billing Issues**. Proper packaging and labeling are essential to prevent damage during transit and ensure that shipments reach their destinations correctly. Accurate declaration of goods is vital to comply with customs regulations and avoid delays or penalties. Meanwhile, addressing payment and billing issues promptly can prevent unnecessary holds and ensure timely delivery. By grasping these responsibilities, individuals can mitigate common pitfalls that often lead to shipment holds. This knowledge is particularly relevant when considering **Common Reasons for DHL Shipment Holds**, as understanding these factors can help navigate potential issues and ensure that shipments proceed without interruption.
1. Proper Packaging and Labeling
Proper packaging and labeling are crucial elements in ensuring that shipments are processed efficiently and reach their destinations without delays or issues. When sending a package, it is the sender's responsibility to ensure that the item is adequately packaged to withstand the rigors of transit. This includes using sturdy materials, such as corrugated cardboard boxes, bubble wrap, or foam inserts, to protect the contents from damage. Additionally, the package should be sealed securely with packing tape to prevent it from opening during transit. Labeling is equally important as it provides critical information necessary for the shipment's journey. The sender must affix clear and legible labels that include the recipient's address, return address, and any relevant handling instructions (e.g., "Fragile" or "This Side Up"). Ensuring that all required documentation, such as customs forms for international shipments, is accurately completed and attached to the package is also vital. Inaccurate or missing information can lead to delays or even the return of the shipment. Moreover, adhering to specific carrier guidelines can prevent hold-ups. For instance, DHL has its own set of packaging and labeling standards that must be followed to avoid any complications during transit. Failure to comply with these standards can result in additional processing time or even rejection of the shipment. From a customer perspective, understanding these responsibilities can significantly reduce the likelihood of their shipment being held up. By taking the time to properly package and label their items, customers can help ensure a smooth delivery process. This not only saves time but also reduces stress and potential additional costs associated with re-routing or re-labeling packages. In summary, proper packaging and labeling are fundamental aspects of ensuring timely and successful delivery. Senders must take care in preparing their packages with appropriate materials and clear labels while adhering to carrier-specific guidelines. By doing so, they can mitigate risks of delays and contribute to a seamless shipping experience for both themselves and the recipients. This proactive approach aligns with broader customer and sender responsibilities outlined in understanding why shipments may be held up by carriers like DHL.
2. Accurate Declaration of Goods
Accurate declaration of goods is a critical responsibility for both customers and senders when shipping with DHL. This aspect is pivotal in ensuring that shipments move smoothly through customs and reach their destinations without unnecessary delays or complications. When goods are not accurately declared, it can lead to a multitude of issues, including shipment holds, fines, and even confiscation of the goods. To avoid such problems, it is essential to provide precise and detailed information about the contents of the shipment. This includes specifying the correct commodity codes (also known as Harmonized System codes), accurate descriptions of the goods, their country of origin, and their value. Inaccurate or incomplete declarations can trigger additional scrutiny from customs authorities, resulting in delays and potential penalties. Moreover, accurate declarations help in compliance with international trade regulations and laws. Different countries have varying regulations regarding the import and export of certain goods, and failure to comply can lead to severe consequences. For instance, under-declaring the value of goods or misclassifying them can be considered fraudulent and may result in legal action. Additionally, accurate declarations facilitate smoother customs clearance processes. When all necessary information is provided correctly upfront, customs officials can process shipments more efficiently, reducing the likelihood of holds or additional inspections. This not only saves time but also minimizes the risk of damage to goods during prolonged inspections. In cases where shipments are held due to inaccurate declarations, DHL may require additional documentation or clarification from the sender. This can involve providing proof of origin, commercial invoices, or other supporting documents to rectify any discrepancies. Therefore, it is crucial for senders to double-check all details before submitting their shipments to ensure compliance and avoid unnecessary delays. In summary, accurate declaration of goods is a fundamental responsibility that both customers and senders must adhere to when using DHL services. By providing precise and complete information about the shipment contents, senders can ensure compliance with regulations, avoid potential penalties, and facilitate efficient customs clearance. This proactive approach not only safeguards against shipment holds but also enhances the overall reliability and efficiency of the shipping process.
3. Payment and Billing Issues
When it comes to understanding why your shipment might be on hold with DHL, one critical area to consider is payment and billing issues. These problems can arise from various sources, including incorrect or incomplete payment information, unpaid invoices, or discrepancies in billing details. For instance, if the sender has not provided accurate payment details or if there are outstanding balances on their account, DHL may place the shipment on hold until these issues are resolved. Similarly, if there are discrepancies between the billing address and the shipping address, it could trigger additional verification steps that delay the shipment. It is essential for both customers and senders to ensure that all payment and billing information is accurate and up-to-date. This includes verifying that credit card details are correct, ensuring that invoices are paid promptly, and confirming that all billing addresses match the shipping addresses. Failure to do so can lead to unnecessary delays and additional costs associated with resolving these issues. Moreover, DHL often has strict policies in place to protect against fraudulent activities, which can sometimes result in legitimate shipments being held for further verification. In such cases, clear communication between DHL and the sender or customer is crucial to resolve any misunderstandings quickly. Senders should regularly check their accounts for any notifications or alerts regarding payment issues and address them promptly to avoid any disruptions in service. To mitigate these issues, it is advisable for senders to maintain open lines of communication with DHL's customer service team. Regularly reviewing account statements and ensuring that all financial obligations are met can help prevent shipments from being placed on hold due to payment-related problems. Additionally, using automated payment systems or setting up recurring payments can help streamline the process and reduce the likelihood of errors. In summary, payment and billing issues are a common reason why shipments may be held by DHL. By ensuring accurate payment information, addressing any discrepancies promptly, and maintaining good communication with DHL's customer service team, both customers and senders can significantly reduce the risk of delays caused by these issues. This proactive approach not only helps in resolving problems efficiently but also enhances the overall shipping experience by minimizing unnecessary hold-ups and ensuring smooth delivery of goods.