Why Is Whmis Important

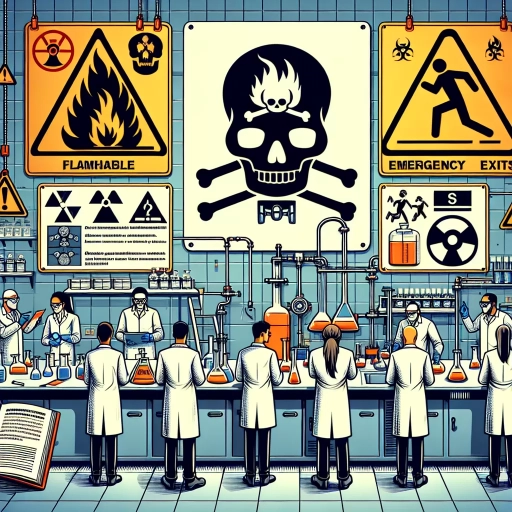
The Workplace Hazardous Materials Information System (WHMIS) is a critical component of occupational health and safety in Canada, playing a multifaceted role that extends beyond the workplace. This comprehensive system ensures that workers are adequately informed about the hazards associated with the chemicals they handle, thereby safeguarding their health and well-being. However, the importance of WHMIS does not stop there; it also significantly enhances public health and environmental protection by regulating the use and handling of hazardous materials. Additionally, WHMIS supports economic stability and growth by reducing workplace injuries and illnesses, which in turn minimizes downtime and boosts productivity. In this article, we will delve into these crucial aspects, starting with the foundational importance of WHMIS in ensuring workplace safety. By understanding how WHMIS protects workers from chemical hazards, we can appreciate its broader impact on public health, environmental sustainability, and economic vitality. Ensuring workplace safety is the cornerstone of WHMIS's effectiveness, and it is here that we begin our exploration.
Ensuring Workplace Safety
Ensuring workplace safety is a multifaceted and critical aspect of any organization, impacting not only the well-being of employees but also the overall productivity and reputation of the company. In today's dynamic work environments, several key factors must be addressed to maintain a safe and healthy workplace. One crucial element is **Preventing Chemical Accidents**, which involves stringent protocols and training to handle hazardous materials safely. Another vital aspect is **Protecting Employee Health**, encompassing measures to prevent injuries, manage stress, and promote a culture of wellness. Additionally, **Compliance with Regulations** is essential, as adhering to legal standards ensures that workplaces meet minimum safety requirements and avoid potential legal repercussions. By focusing on these three areas, organizations can significantly enhance their safety standards. This article will delve into each of these critical components, providing insights and strategies for ensuring workplace safety.
Preventing Chemical Accidents
Preventing chemical accidents is a critical component of ensuring workplace safety, and it underscores the importance of WHMIS (Workplace Hazardous Materials Information System). Chemical accidents can result in severe injuries, fatalities, and significant environmental damage, making proactive measures essential. To prevent such incidents, employers must implement robust safety protocols and ensure that all employees are adequately trained and informed about the hazards associated with the chemicals they handle. Firstly, proper labeling and signage are crucial. Under WHMIS, hazardous materials must be labeled with standardized symbols and information that clearly indicate their potential dangers. This includes the use of Safety Data Sheets (SDSs) which provide detailed information on handling, storage, and emergency procedures. Ensuring that these labels and SDSs are readily available and understood by all workers is vital for preventing misunderstandings that could lead to accidents. Secondly, regular training programs are indispensable. Employees should receive comprehensive training on the safe handling of chemicals, including how to use personal protective equipment (PPE), follow safety procedures, and respond to spills or leaks. This training should be ongoing and updated as new chemicals are introduced into the workplace or as procedures change. Thirdly, maintaining a clean and organized workspace is key. Cluttered areas can increase the risk of accidents by making it difficult to access safety equipment or escape in case of an emergency. Regular inspections should be conducted to identify potential hazards and implement corrective actions promptly. Additionally, employers should foster a culture of safety where employees feel empowered to report any concerns or near-miss incidents without fear of reprisal. This encourages a proactive approach to safety where potential risks are identified and mitigated before they escalate into full-blown accidents. Finally, adherence to regulatory standards is paramount. Compliance with WHMIS regulations ensures that workplaces meet minimum safety standards, reducing the likelihood of chemical accidents. Regular audits and compliance checks help in identifying gaps in safety protocols and ensuring that corrective actions are taken. In summary, preventing chemical accidents requires a multifaceted approach that includes proper labeling and signage, comprehensive employee training, a well-maintained workspace, a safety-conscious culture, and strict adherence to regulatory standards. By integrating these measures into their safety protocols, employers can significantly reduce the risk of chemical accidents and create a safer working environment for all employees. This underscores why WHMIS is so important—it provides a structured framework for managing hazardous materials safely and effectively in the workplace.