When Was Tinfoil Invented

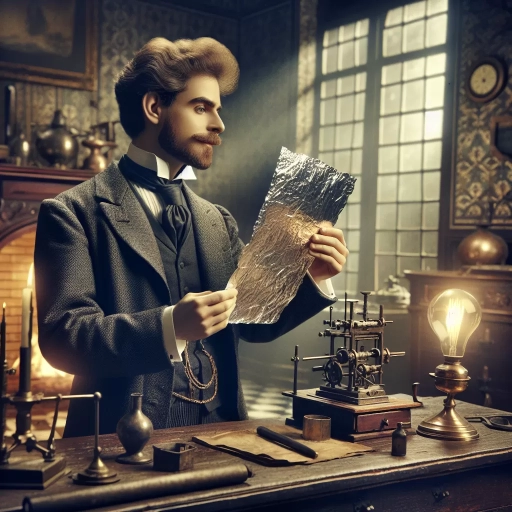
Tinfoil, a ubiquitous material in modern kitchens and industries, has a rich and fascinating history that spans centuries. From its early origins in ancient times to its mass production during the Industrial Revolution, tinfoil has evolved significantly over the years. This article delves into the intriguing story of tinfoil, exploring its early beginnings, its transformation during the Industrial Revolution, and its modern uses and evolution. We will start by examining the **Early Origins of Tinfoil**, tracing back to when this versatile material first emerged and how it was initially used. This foundational understanding will set the stage for a deeper exploration of how tinfoil became a staple in various industries and households, particularly during **The Industrial Revolution and Mass Production**. Finally, we will discuss **Modern Uses and Evolution of Tinfoil**, highlighting its diverse applications and the technological advancements that have shaped its contemporary form. By uncovering these pivotal moments in the history of tinfoil, we gain a comprehensive insight into its enduring significance. Let us begin our journey through time with the **Early Origins of Tinfoil**.
Early Origins of Tinfoil
The history of tinfoil, a material often overlooked yet ubiquitous in modern life, is deeply rooted in the ancient use of tin. From its early applications in ancient civilizations to the development of sophisticated extraction techniques, the journey of tinfoil is a fascinating tale of innovation and necessity. Historical records reveal that tin was highly valued in ancient societies for its durability and versatility, leading to its widespread use in various forms. The evolution of tin extraction techniques marked a significant milestone, enabling mass production and paving the way for new applications. One of the earliest and most impactful uses of tin was in the form of foil, which revolutionized packaging and preservation methods. This article delves into the early origins of tinfoil, exploring its historical use in ancient civilizations, the development of tin extraction techniques, and its initial applications that laid the groundwork for its modern-day ubiquity. By examining these pivotal aspects, we uncover the rich history behind a material that has become an integral part of our daily lives, tracing back to the early origins of tinfoil.
Historical Use of Tin in Ancient Civilizations
Tin has been a cornerstone of human innovation since ancient times, playing a pivotal role in the development and advancement of various civilizations. The historical use of tin dates back to the Bronze Age, around 3000 BCE, when it was first alloyed with copper to create bronze. This durable and versatile metal alloy revolutionized tool-making, enabling the creation of stronger, more resilient implements that significantly improved agricultural productivity and warfare capabilities. The early use of tin was widespread across ancient Mesopotamia, Egypt, and the Indus Valley Civilization, where it was highly valued for its ability to enhance the strength and durability of copper. In ancient Egypt, tin was used not only for tools but also in decorative arts and jewelry. Egyptian craftsmen incorporated tin into their bronze works, creating intricate statues and other artifacts that showcased their advanced metallurgical skills. Similarly, in the Indus Valley Civilization, tin was integral to the production of sophisticated bronze artifacts, including seals, figurines, and other household items. The Phoenicians and other Mediterranean traders facilitated the global distribution of tin, establishing trade routes that connected Europe, Asia, and Africa. The Romans further expanded the use of tin, employing it in various applications such as soldering, plating, and even coinage. Roman engineers used tin to coat iron pipes to prevent corrosion, a practice that laid the groundwork for modern plumbing systems. Additionally, the Romans developed techniques for alloying tin with other metals to create pewter, a malleable and corrosion-resistant material ideal for tableware and other household items. The significance of tin extended beyond its practical applications; it also held cultural and symbolic value. In many ancient societies, tin was associated with wealth and status due to its rarity and the difficulty involved in extracting it from ore. This cultural significance is evident in the elaborate burial sites of ancient leaders, where tin artifacts were often included as symbols of power and prestige. The historical use of tin in these ancient civilizations laid the foundation for its continued importance in later periods. As metallurgical techniques evolved, so did the applications of tin, eventually leading to the development of tinfoil in the 19th century. Tinfoil, initially made from tinplate (a tin-coated iron sheet), was first used as a wrapping material for food and other products, marking a new era in packaging technology. The early origins of tinfoil are thus deeply rooted in the ancient civilizations that first harnessed the potential of tin, setting the stage for its enduring impact on human history.
Development of Tin Extraction Techniques
The development of tin extraction techniques has been a pivotal factor in the evolution of various industries, including the production of tinfoil. The journey began with ancient civilizations, where tin was first extracted around 3500 BCE in the Middle East. Early methods involved smelting cassiterite, a tin oxide ore, in simple furnaces. As civilizations advanced, so did the techniques. The Romans, for instance, refined these processes by using larger furnaces and more efficient ventilation systems, significantly increasing tin production. The Industrial Revolution marked a significant turning point in tin extraction. New technologies such as the reverberatory furnace and the Bessemer process allowed for mass production and higher purity levels. The introduction of electrolytic refining in the late 19th century further enhanced the quality of extracted tin, making it suitable for a wider range of applications. This period also saw the development of more sophisticated mining techniques, including open-pit mining and underground mining methods, which increased accessibility to tin deposits. In the 20th century, advancements in metallurgy led to the development of more efficient extraction processes. The use of flotation and magnetic separation techniques improved the recovery rates of tin from ores. Additionally, the introduction of hydrometallurgical processes allowed for the extraction of tin from lower-grade ores, reducing waste and increasing overall efficiency. These advancements in tin extraction have had a direct impact on the production of tinfoil. With higher purity levels and more consistent supply chains, manufacturers could produce tinfoil that was stronger, more durable, and less prone to corrosion. This quality improvement was crucial for tinfoil's widespread adoption in food packaging, electrical applications, and other industries. The early origins of tinfoil, which date back to the early 19th century when it was first used as a wrapping material for food and other products, were thus significantly influenced by these evolving extraction techniques. Today, tin extraction continues to evolve with technological innovations. Modern processes incorporate environmental considerations, such as recycling and waste management, to ensure sustainability. The integration of advanced technologies like automation and data analytics also enhances operational efficiency and reduces costs. These ongoing improvements in tin extraction not only support the continued production of high-quality tinfoil but also contribute to broader industrial development and environmental stewardship.
Initial Applications of Tin Foil
The initial applications of tin foil, which date back to ancient China and later to Europe in the 17th and 18th centuries, were multifaceted and reflective of the material's unique properties. Initially, tin foil was used for decorative purposes, such as gilding and ornamentation. In China, it was employed to create intricate designs and patterns on various objects, including furniture and ceremonial items. This aesthetic use was later adopted in Europe, where tin foil became a popular choice for embellishing picture frames, mirrors, and other household items due to its malleability and ability to mimic the appearance of gold. Beyond its decorative uses, tin foil also found practical applications. One of the earliest significant uses was in the production of hats and other clothing items. In the 18th century, hatters began using tin foil to create felt hats that were more durable and resistant to weather conditions. The tin foil was beaten into thin sheets and then incorporated into the felt-making process, enhancing the overall quality of the hats. Another critical application of tin foil emerged in the realm of food preservation. Before the widespread use of aluminum foil, tin foil was used to wrap food items to prevent spoilage. This practice was particularly important for preserving delicate foods like chocolates and candies, as well as for storing other perishable goods. The impermeable nature of tin foil made it an ideal material for this purpose, helping to keep food fresh for longer periods. In addition to these uses, tin foil played a role in early scientific experiments. For instance, it was used by inventors like Michael Faraday in his groundbreaking work on electromagnetic induction. Faraday utilized tin foil to create insulated containers that could store electric charges without leakage, contributing significantly to our understanding of electricity. The versatility of tin foil also extended into the realm of medicine. It was used in various medical applications, including the creation of surgical instruments and as a component in some early medical devices. Its non-reactive nature made it suitable for use in environments where other metals might cause adverse reactions. In summary, the initial applications of tin foil were diverse and impactful, ranging from decorative arts to practical uses in clothing, food preservation, scientific research, and medicine. These early uses not only highlighted the material's unique properties but also paved the way for its continued development and eventual replacement by aluminum foil in many modern applications. The legacy of tin foil's early uses remains an important part of understanding its evolution and the broader history of metallurgy and material science.
The Industrial Revolution and Mass Production
The Industrial Revolution marked a pivotal era in human history, transforming the way goods were produced and consumed on a massive scale. At the heart of this transformation was the advent of mass production, which relied heavily on several key technological advancements. One of the most significant developments was in metalworking technology, where innovations enabled the efficient processing and shaping of metals into various forms. Another crucial innovation was the introduction of rolling mills, which allowed for the production of thin sheets of metal, a critical component in many industrial applications. These technological breakthroughs led to the commercialization and widespread use of mass-produced goods, revolutionizing industries from manufacturing to packaging. As we delve into these advancements, we will see how they laid the groundwork for subsequent innovations, including the early origins of tinfoil, a material that would become ubiquitous in everyday life. This article will explore these pivotal developments and their lasting impact on modern society.
Advancements in Metalworking Technology
The Industrial Revolution and Mass Production were significantly propelled by advancements in metalworking technology, which transformed the manufacturing landscape and paved the way for widespread industrialization. One of the pivotal moments in this evolution was the development of new metalworking techniques and tools. The introduction of the steam engine by James Watt in the late 18th century provided a reliable source of power, enabling the mechanization of metalworking processes. This led to the creation of more sophisticated machinery, such as the power lathe and milling machine, which greatly increased precision and efficiency in metal fabrication. The discovery of new metals and alloys also played a crucial role. For instance, the development of Bessemer steel in the mid-19th century by Sir Henry Bessemer revolutionized the production of steel, making it cheaper and more accessible. This innovation was instrumental in the construction of railways, bridges, and other infrastructure projects that were essential for industrial growth. Additionally, advancements in rolling and forging technologies allowed for the mass production of metal components with uniform quality, further enhancing industrial productivity. Another significant advancement was the introduction of electric arc welding in the early 20th century. This technique allowed for stronger and more durable welds, which were critical for the construction of complex machinery and structures. The advent of computer numerical control (CNC) machines in the latter half of the 20th century brought about a new era of precision and automation in metalworking. CNC machines enabled manufacturers to produce intricate metal parts with high accuracy and speed, significantly reducing production times and costs. Furthermore, recent advancements in additive manufacturing (3D printing) have opened up new possibilities for metalworking. This technology allows for the creation of complex geometries that cannot be produced through traditional methods, offering unprecedented design flexibility and material efficiency. The integration of artificial intelligence and machine learning into metalworking processes is also becoming increasingly prevalent, enabling real-time monitoring and optimization of production lines. In summary, the evolution of metalworking technology has been a cornerstone of industrial progress, from the mechanization driven by steam power to the precision and automation offered by CNC machines and additive manufacturing. These advancements have not only improved the quality and efficiency of metal production but have also enabled the mass production of goods on an unprecedented scale, driving economic growth and transforming industries worldwide. As technology continues to evolve, it is clear that metalworking will remain a vital component of industrial innovation.
Introduction of Rolling Mills for Thin Sheets
The introduction of rolling mills for thin sheets was a pivotal innovation during the Industrial Revolution, significantly contributing to the era of mass production. These mills, which emerged in the late 18th and early 19th centuries, revolutionized the manufacturing process by enabling the efficient production of uniform, thin metal sheets. Prior to this development, metalworking was labor-intensive and often resulted in inconsistent thicknesses, limiting the scalability and quality of metal products. Rolling mills transformed this landscape by utilizing a series of rollers to flatten and stretch metal into precise, uniform sheets. This technology allowed for the mass production of tin foil, among other metals, which had profound implications for various industries. Tin foil, in particular, became a crucial material in food packaging, electrical applications, and even decorative arts. The ability to produce thin, flexible sheets of tin on a large scale made it an indispensable commodity. The impact of rolling mills extended beyond tin foil to other metals like steel and aluminum. These mills enabled the production of thin sheets that were essential for the construction of machinery, vehicles, and consumer goods. The consistency and precision offered by rolling mills also improved product quality, reducing waste and increasing efficiency in manufacturing processes. Moreover, the advent of rolling mills spurred further technological advancements. Innovations in rolling techniques and machinery design continued to evolve, leading to more sophisticated rolling processes such as cold rolling and hot rolling. These advancements not only enhanced the properties of the metal sheets but also expanded their applications across diverse sectors. In the context of mass production, rolling mills were instrumental in achieving economies of scale. By producing large quantities of uniform metal sheets quickly and efficiently, manufacturers could meet growing demand while reducing costs. This scalability was a cornerstone of the Industrial Revolution, enabling industries to expand rapidly and fuel economic growth. In conclusion, the introduction of rolling mills for thin sheets was a transformative event in the history of industrial manufacturing. It facilitated the mass production of high-quality metal sheets, including tin foil, which had far-reaching impacts on various industries and contributed significantly to the technological and economic advancements of the Industrial Revolution. This innovation remains a cornerstone of modern manufacturing, underpinning many contemporary industrial processes and continuing to shape the world of mass production today.
Commercialization and Widespread Use
The Industrial Revolution marked a pivotal era in human history, transforming the way goods were produced and consumed. One of the key drivers of this transformation was the commercialization and widespread use of new technologies and materials. As mass production techniques became more sophisticated, industries began to scale up their operations, leading to a significant increase in output and a decrease in costs. This shift enabled goods that were once luxury items to become more accessible to the general population. Tinfoil, for instance, was one such material that benefited from these advancements. Invented in the early 19th century, tinfoil initially found niche applications due to its high cost and limited availability. However, with the advent of mass production techniques during the Industrial Revolution, tinfoil became cheaper and more widely available. Its use expanded beyond decorative purposes to include packaging and other industrial applications. The widespread adoption of tinfoil was further facilitated by innovations in rolling and cutting machinery, which allowed for the efficient production of thin sheets of tin. The commercialization of tinfoil had far-reaching impacts on various sectors. In the food industry, tinfoil packaging revolutionized food preservation by providing a durable and airtight seal that prevented spoilage. This innovation extended the shelf life of perishable goods, enabling their transportation over longer distances and contributing to the growth of global trade. Additionally, tinfoil's use in electrical applications, such as insulation for wires, supported the development of modern electrical systems. The widespread use of tinfoil also had cultural and social implications. As it became more affordable, tinfoil began to feature prominently in everyday life. It was used in household items like baking pans and decorative ornaments, reflecting a broader trend of increased consumerism and material comfort. The accessibility of tinfoil symbolized the democratization of luxury goods, where items once reserved for the wealthy became staples in middle-class households. In conclusion, the commercialization and widespread use of tinfoil during the Industrial Revolution exemplify how technological advancements can drive economic growth and societal change. By making previously expensive materials more accessible, mass production facilitated a broader distribution of goods, transforming both industries and daily life. This era set the stage for future innovations, demonstrating how industrial progress can lead to widespread benefits across various sectors of society.
Modern Uses and Evolution of Tinfoil
Tinfoil, once a ubiquitous material in everyday life, has undergone significant transformations over the years. From its early origins as a luxury item in the 18th century to its widespread use in the 19th and 20th centuries, tinfoil has evolved to meet the changing needs of modern society. Today, while aluminum foil has replaced tinfoil in some applications due to its lighter weight and lower cost, tinfoil still holds specialized uses in various industries where its unique properties are invaluable. Additionally, as sustainability and environmental impact become increasingly important considerations, the use of tinfoil is being reevaluated in light of these concerns. This article delves into the modern uses and evolution of tinfoil, exploring its replacement by aluminum foil in some applications, its specialized uses in modern industries, and the sustainability and environmental impact considerations surrounding its use. By understanding these contemporary aspects, we can better appreciate the early origins of tinfoil and its enduring relevance in our world.
Replacement by Aluminum Foil in Some Applications
In the modern era, aluminum foil has increasingly replaced traditional tin foil in various applications, marking a significant evolution in the use of these materials. This shift is largely driven by the superior properties of aluminum, which offer several advantages over tin. Aluminum foil is lighter, more malleable, and less expensive to produce than tin foil. Additionally, aluminum has a higher thermal conductivity, making it an excellent choice for cooking and packaging where heat transfer is crucial. For instance, in the food industry, aluminum foil is widely used for wrapping leftovers, baking, and even as a lining for barbecues due to its ability to distribute heat evenly and prevent food from sticking. Another key area where aluminum foil has supplanted tin foil is in pharmaceutical packaging. Aluminum's impermeability to light and moisture makes it an ideal material for protecting sensitive medications from environmental factors that could degrade their potency. This is particularly important for drugs that require strict storage conditions to maintain their efficacy. Furthermore, aluminum foil's non-reactive nature ensures that it does not contaminate the contents, which is a critical consideration in the pharmaceutical industry. The construction industry also benefits from the use of aluminum foil. It is often used as a reflective insulation material due to its high reflectivity, which helps in reducing energy consumption by reflecting radiant heat rather than absorbing it. This application not only enhances energy efficiency but also contributes to a more sustainable building practice. Moreover, aluminum foil's versatility extends to industrial applications such as electrical shielding and capacitors. Its high electrical conductivity makes it suitable for these uses, where tin foil would be less effective or more expensive. The automotive sector also utilizes aluminum foil in various components, including catalytic converters and heat shields, leveraging its thermal and electrical properties. The environmental impact of this replacement is also noteworthy. Aluminum is more recyclable than tin, which reduces waste and conserves natural resources. This sustainability aspect aligns with contemporary environmental concerns and regulations, making aluminum foil a preferred choice for many industries. In conclusion, the replacement of tin foil by aluminum foil in various applications reflects a broader trend towards using materials that are more efficient, cost-effective, and environmentally friendly. As technology continues to evolve, it is likely that aluminum foil will remain a staple in many industries due to its unique combination of physical and chemical properties. This transition underscores the dynamic nature of material science and the ongoing quest for better solutions in modern applications.
Specialized Uses in Modern Industries
In modern industries, tinfoil, or more accurately, aluminum foil, has evolved to serve a multitude of specialized uses that leverage its unique properties. One of the most significant applications is in the food industry, where aluminum foil is used extensively for packaging due to its excellent barrier properties against moisture, light, and oxygen. This makes it ideal for preserving the freshness and quality of food products such as meats, vegetables, and baked goods. Additionally, aluminum foil's high thermal conductivity and malleability make it a preferred material for cooking and baking. It is often used in grilling and roasting to distribute heat evenly and prevent sticking. Beyond the culinary realm, aluminum foil plays a critical role in pharmaceutical packaging. Its impermeable nature ensures the integrity of medications by protecting them from environmental factors like humidity and light, which can degrade active ingredients. In the aerospace industry, aluminum foil is utilized in various components due to its lightweight yet strong properties. It is used in insulation materials to maintain temperature stability within aircraft and spacecraft. The automotive sector also benefits from aluminum foil's versatility. It is incorporated into catalytic converters to enhance the efficiency of exhaust systems by facilitating chemical reactions that reduce harmful emissions. Furthermore, aluminum foil is used in electrical applications such as capacitors and transformers due to its high electrical conductivity and resistance to corrosion. In construction and building insulation, aluminum foil serves as a reflective barrier that helps regulate indoor temperatures by reflecting radiant heat rather than absorbing it. This not only improves energy efficiency but also reduces the need for heating and cooling systems. The medical field also employs aluminum foil in certain procedures; for instance, it is used in radiation shielding during X-ray examinations to protect sensitive areas from unnecessary exposure. Moreover, aluminum foil's recyclability makes it an environmentally friendly choice across various industries. Its ability to be reused multiple times without losing its properties contributes significantly to sustainable practices. In summary, the modern uses of tinfoil or aluminum foil are diverse and critical, reflecting its adaptability and the ongoing innovation in materials science that continues to expand its applications across different sectors.
Sustainability and Environmental Impact Considerations
As we delve into the modern uses and evolution of tinfoil, it is crucial to consider the sustainability and environmental impact of this versatile material. Tinfoil, primarily made from aluminum, has been a staple in various industries since its invention in the early 20th century. However, its widespread use raises significant environmental concerns. The extraction and processing of aluminum require substantial amounts of energy, often derived from non-renewable sources, contributing to greenhouse gas emissions and climate change. Additionally, the mining of bauxite, the primary ore used in aluminum production, can lead to deforestation and habitat destruction. Moreover, the disposal of tinfoil poses another challenge. While aluminum is recyclable, much of the tinfoil used in packaging ends up in landfills or incinerators due to inadequate recycling infrastructure. This not only wastes a valuable resource but also contributes to pollution and waste management issues. To mitigate these impacts, there has been a growing emphasis on sustainable practices within the aluminum industry. Many companies are now adopting more energy-efficient production methods and investing in renewable energy sources to reduce their carbon footprint. Consumers also play a critical role in minimizing the environmental impact of tinfoil. Proper recycling of aluminum products can significantly reduce the need for primary aluminum production, thereby conserving natural resources and lowering emissions. Furthermore, choosing products with minimal or biodegradable packaging can help reduce overall waste. Innovations in packaging materials, such as bioplastics and compostable alternatives, are also gaining traction as more sustainable options. In the context of modern uses, tinfoil continues to evolve with technological advancements aimed at enhancing its sustainability. For instance, some manufacturers are developing thinner, lighter tinfoil that requires less material while maintaining its functionality. This reduction in material usage can lead to lower energy consumption during production and transportation. Additionally, research into new recycling technologies is improving the efficiency and accessibility of aluminum recycling, making it easier for consumers to participate in sustainable practices. In conclusion, while tinfoil remains an indispensable material in various sectors, its environmental impact cannot be overlooked. By adopting sustainable production methods, improving recycling infrastructure, and promoting responsible consumer behavior, we can minimize the ecological footprint of tinfoil and ensure its continued use aligns with our commitment to environmental stewardship. As we look to the future of tinfoil and its applications, integrating sustainability considerations will be essential for a more environmentally conscious and responsible approach to this versatile material.