When Is Whmis Training Required (check All That Apply)

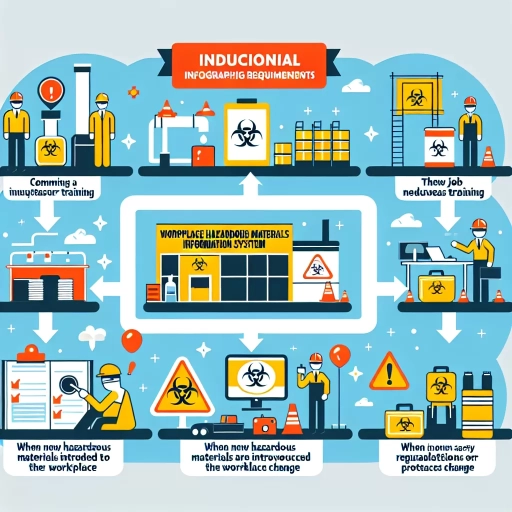
In the modern workplace, ensuring the safety and health of employees is paramount, especially when dealing with hazardous materials. The Workplace Hazardous Materials Information System (WHMIS) is a critical component of this safety framework, providing essential training to mitigate risks associated with chemical handling. WHMIS training is not a one-time requirement but rather an ongoing necessity that adapts to various scenarios. For instance, new employees must undergo WHMIS training to understand the hazards and safe handling practices of the materials they will be working with. Additionally, refresher training is necessary in certain scenarios to keep employees updated on new regulations and hazards. Special circumstances, such as changes in workplace conditions or the introduction of new substances, also demand specific WHMIS training. This article will delve into these critical aspects, starting with the mandatory training requirements for new employees, ensuring that all stakeholders are well-equipped to handle hazardous materials safely and effectively. When WHMIS Training is Mandatory for New Employees will be our first focus, highlighting the importance of initial training in setting a strong foundation for workplace safety.
When WHMIS Training is Mandatory for New Employees
In the modern workplace, ensuring the safety and well-being of employees is paramount, especially when dealing with hazardous materials. The Workplace Hazardous Materials Information System (WHMIS) training is a critical component of this safety protocol. For new employees, understanding when WHMIS training is mandatory is essential to prevent accidents and comply with regulatory standards. This article delves into the specific instances when WHMIS training becomes compulsory for new hires. We will explore three key scenarios: **Upon Initial Hiring**, where the foundation of safety knowledge is laid; **Before Handling Hazardous Materials**, where practical application of WHMIS principles is crucial; and **As Part of Onboarding Process**, integrating WHMIS training seamlessly into the new employee's induction. By understanding these critical junctures, employers can ensure that their new employees are adequately prepared to handle hazardous materials safely and effectively. When WHMIS Training is Mandatory for New Employees is a topic that requires careful consideration to maintain a safe and compliant work environment.
Upon Initial Hiring
Upon initial hiring, ensuring that new employees receive comprehensive WHMIS (Workplace Hazardous Materials Information System) training is paramount for maintaining a safe and compliant work environment. This critical step aligns with the regulatory requirements outlined in the Hazardous Products Act and the Controlled Products Regulations, which mandate that all workers handling hazardous materials must be adequately trained. At the onset of employment, new hires are often unfamiliar with the specific hazards present in their new workplace, making it essential to provide them with detailed information about the chemicals they will be working with. WHMIS training covers key areas such as recognizing and understanding safety data sheets (SDSs), interpreting hazard symbols and labels, and understanding the safe handling, use, and disposal of hazardous products. This training not only protects employees from potential health risks but also ensures that they are equipped to respond effectively in emergency situations. Moreover, it fosters a culture of safety within the organization by emphasizing the importance of proper procedures and protocols. Employers must also ensure that this training is tailored to the specific job duties and hazards associated with each role, thereby enhancing its relevance and effectiveness. By integrating WHMIS training into the onboarding process, employers can mitigate risks, reduce workplace accidents, and comply with legal obligations. Additionally, regular updates and refresher courses should be provided to keep employees informed about any changes in regulations or new hazards introduced into the workplace. This proactive approach to safety training underscores an employer's commitment to protecting their workforce and maintaining a safe, healthy work environment. In summary, incorporating WHMIS training at the point of initial hiring is a crucial step in ensuring that new employees are well-prepared to handle hazardous materials safely and responsibly, thereby contributing to a safer and more compliant workplace.
Before Handling Hazardous Materials
Before handling hazardous materials, it is crucial to understand the importance of proper training and adherence to safety protocols. This knowledge is particularly relevant when considering the mandatory WHMIS (Workplace Hazardous Materials Information System) training for new employees. WHMIS training is designed to equip workers with the necessary skills and information to safely handle, use, and dispose of hazardous substances. When new employees are introduced to a workplace where hazardous materials are present, they must be thoroughly educated on the potential risks associated with these substances. This includes understanding the classification of hazardous materials, recognizing the symbols and labels used on safety data sheets (SDSs), and knowing how to read and interpret this critical information. The training also covers emergency procedures such as spill response, fire safety, and first aid for exposure incidents. Moreover, WHMIS training emphasizes the importance of personal protective equipment (PPE) and how to use it correctly. Employees learn about the different types of PPE required for various tasks involving hazardous materials, ensuring they can protect themselves from chemical splashes, inhalation hazards, and other risks. The training also highlights workplace policies and procedures that are in place to mitigate hazards and ensure a safe working environment. In addition to technical knowledge, WHMIS training fosters a culture of safety awareness within the workplace. It encourages employees to report any hazards or near-miss incidents promptly and to participate actively in maintaining a safe work environment. This proactive approach not only protects individual workers but also contributes to overall workplace safety and compliance with regulatory standards. In summary, before handling hazardous materials, new employees must undergo comprehensive WHMIS training. This training is not just a regulatory requirement but a critical component of ensuring workplace safety and preventing accidents. By equipping employees with the right knowledge and skills from the outset, employers can significantly reduce the risks associated with hazardous materials and create a safer, more compliant work environment. This foundational training sets the stage for ongoing safety practices and continuous improvement in workplace safety protocols.
As Part of Onboarding Process
As part of the onboarding process, ensuring that new employees undergo WHMIS (Workplace Hazardous Materials Information System) training is not just a best practice but a legal requirement in many jurisdictions. This critical training is designed to equip employees with the knowledge and skills necessary to safely handle hazardous materials in the workplace. When new employees join an organization, they are often unfamiliar with the specific hazards present in their new environment. WHMIS training bridges this gap by providing comprehensive information on the classification, labeling, and safe handling of hazardous substances. During the onboarding process, WHMIS training should be integrated as a mandatory component to ensure that all employees are aware of their roles and responsibilities in managing workplace hazards. This includes understanding the Globally Harmonized System (GHS) of classification and labeling, recognizing the hazards associated with different types of chemicals, and knowing how to read and interpret Safety Data Sheets (SDS). By incorporating WHMIS training into the onboarding process, employers can ensure compliance with regulatory standards while fostering a culture of safety and responsibility. Moreover, WHMIS training during onboarding helps in reducing workplace accidents and injuries. New employees who are properly trained are less likely to engage in risky behaviors or overlook critical safety protocols. This proactive approach also enhances employee confidence and competence, allowing them to contribute effectively to the organization from the outset. Additionally, it sets a positive tone for the employee's tenure by emphasizing the importance of safety and well-being. In practice, this means that employers should schedule WHMIS training sessions as part of the initial orientation program. These sessions can be conducted in various formats, including online modules, classroom training, or even on-the-job training, depending on what best suits the organization's needs. It is also crucial to provide ongoing support and refresher training to ensure that employees remain up-to-date with any changes in regulations or workplace procedures. By making WHMIS training an integral part of the onboarding process, employers not only fulfill their legal obligations but also create a safer, more informed workforce. This holistic approach to employee induction ensures that new hires are well-prepared to navigate the workplace safely and efficiently, contributing to a healthier and more productive work environment overall.
Scenarios Requiring Refresher WHMIS Training
In the dynamic and often hazardous environment of modern workplaces, ensuring that all employees are well-versed in the Workplace Hazardous Materials Information System (WHMIS) is crucial for safety and compliance. However, WHMIS training is not a one-time affair; it requires periodic refreshers to maintain a safe and informed workforce. There are several scenarios that necessitate refresher WHMIS training, each highlighting the importance of ongoing education. Changes in workplace procedures or policies can introduce new risks or alter existing ones, making it essential for employees to be updated on these changes. The introduction of new hazardous materials into the workplace also demands that employees receive refresher training to understand the specific risks and handling procedures associated with these substances. Additionally, employee performance issues related to WHMIS can indicate a need for retraining to ensure that all staff members are adequately equipped to handle hazardous materials safely. Understanding these scenarios underscores the importance of continuous learning and sets the stage for when WHMIS training is mandatory for new employees.
Changes in Workplace Procedures or Policies
Changes in workplace procedures or policies are a critical trigger for refresher WHMIS (Workplace Hazardous Materials Information System) training. As workplaces evolve, new chemicals are introduced, and existing processes are modified, the risk landscape shifts significantly. For instance, if a company adopts new manufacturing techniques or introduces novel hazardous substances, the potential for exposure to harmful materials increases. In such scenarios, it is imperative to update the WHMIS training to ensure that all employees are aware of the new hazards and understand how to handle them safely. Moreover, changes in regulatory requirements or updates to WHMIS standards necessitate refresher training. The Canadian government periodically revises WHMIS regulations to align with international standards or to address emerging hazards. These updates can include new classification criteria, labeling requirements, or safety data sheet formats. Employees must be trained on these changes to comply with legal obligations and maintain a safe working environment. Additionally, organizational changes such as mergers, acquisitions, or restructuring can lead to the introduction of new chemicals and processes. When different departments or facilities are integrated, there may be variations in how hazardous materials are handled. Refresher WHMIS training ensures that all employees, regardless of their background or previous training, are on the same page regarding safety protocols and emergency procedures. Technological advancements also play a role in necessitating refresher training. New equipment and tools may be introduced that require specific handling procedures for hazardous materials. For example, automated dispensing systems or robotic handling equipment can reduce manual exposure but also introduce new operational risks if not used correctly. Training must cover these technological changes to prevent accidents and ensure compliance. Finally, changes in workplace policies related to health and safety can also trigger the need for refresher WHMIS training. If a company adopts a more stringent safety policy or introduces new personal protective equipment (PPE) requirements, employees need to be informed and trained accordingly. This ensures that everyone understands their roles and responsibilities in maintaining a safe workplace. In summary, any significant change in workplace procedures or policies mandates refresher WHMIS training to ensure that employees are equipped with the knowledge and skills necessary to handle hazardous materials safely and comply with regulatory requirements. This proactive approach not only enhances workplace safety but also fosters a culture of continuous learning and improvement.
Introduction of New Hazardous Materials
The introduction of new hazardous materials into a workplace necessitates immediate attention and action to ensure the safety and well-being of all employees. This scenario is a critical trigger for refresher WHMIS (Workplace Hazardous Materials Information System) training, as it presents a significant change in the workplace environment that could pose new risks. When new hazardous materials are introduced, it is essential that all workers understand the specific hazards associated with these substances, including their chemical properties, potential health effects, and necessary safety precautions. Refresher WHMIS training in this context must cover the updated Safety Data Sheets (SDSs) and labels for the new materials, as these documents provide crucial information on handling, storage, and emergency procedures. Employees need to be aware of the Personal Protective Equipment (PPE) required when working with these substances and how to properly use it. Additionally, training should emphasize safe work practices and emergency response protocols specific to the new materials. Effective refresher training also involves hands-on demonstrations and practical exercises to reinforce understanding and build confidence among workers. This includes simulations of spill responses, fire drills, and other emergency scenarios that could arise from the introduction of new hazardous materials. Moreover, supervisors and trainers must be available to answer questions and provide ongoing support to ensure that all employees feel comfortable and competent in their ability to handle these new substances safely. Regular refresher training sessions are not just a compliance requirement but also a proactive measure to prevent accidents and reduce the risk of injuries and illnesses. By keeping employees informed and up-to-date on the latest hazards and safety protocols, organizations can foster a culture of safety and responsibility, ultimately protecting both their workforce and their operations. Therefore, the introduction of new hazardous materials serves as a compelling reason for refresher WHMIS training, ensuring that all employees are equipped with the knowledge and skills necessary to work safely in an evolving workplace environment.
Employee Performance Issues Related to WHMIS
Employee performance issues related to the Workplace Hazardous Materials Information System (WHMIS) can have significant implications for workplace safety and compliance. WHMIS training is crucial for ensuring that employees understand the hazards associated with chemical products, how to handle them safely, and how to respond in emergency situations. However, if employees are not adequately trained or if their training is outdated, it can lead to a range of performance issues. For instance, employees may not properly label hazardous materials, fail to use personal protective equipment (PPE) as required, or misinterpret safety data sheets (SDSs), all of which can increase the risk of accidents and injuries. Moreover, lack of knowledge about WHMIS protocols can result in non-compliance with regulatory standards, potentially leading to legal repercussions and fines for the organization. Furthermore, inadequate training can also affect employee confidence and morale, as they may feel uncertain about their ability to handle hazardous materials safely. This uncertainty can lead to decreased productivity and increased turnover rates. Therefore, it is essential for employers to identify scenarios where refresher WHMIS training is necessary, such as when new chemicals are introduced into the workplace, when there are changes in job responsibilities, or when there have been incidents indicating a need for retraining. By providing regular and comprehensive WHMIS training, employers can mitigate these performance issues, enhance workplace safety, and ensure compliance with regulatory requirements. This proactive approach not only protects employees but also contributes to a more efficient and compliant work environment. In scenarios requiring refresher WHMIS training, employers should prioritize updating employees' knowledge to align with current standards and best practices, thereby fostering a culture of safety and responsibility within the organization.
Special Circumstances That Demand WHMIS Training
In the dynamic and often hazardous world of workplaces involving chemical substances, staying informed and compliant with safety regulations is paramount. The Workplace Hazardous Materials Information System (WHMIS) training is a critical component of ensuring employee safety and adherence to legal standards. However, WHMIS training is not a one-time requirement; it becomes mandatory under specific circumstances that demand continuous updating and reinforcement. For instance, when an employee transfers to a new job role involving hazardous materials, they must undergo WHMIS training to understand the unique risks associated with their new responsibilities. Similarly, returning to work after an extended leave may necessitate refresher training to ensure familiarity with current protocols and materials. Additionally, regulatory updates or changes in WHMIS standards can render previous training obsolete, requiring employees to undergo updated training sessions. Understanding these special circumstances highlights the importance of ongoing WHMIS education, which ultimately leads to the conclusion that **When WHMIS Training is Mandatory for New Employees**.
Transfer to a New Job Role Involving Hazardous Materials
When transitioning to a new job role involving hazardous materials, it is crucial to undergo comprehensive WHMIS (Workplace Hazardous Materials Information System) training. This specialized training is not just a regulatory requirement but a vital component of ensuring workplace safety and compliance. As you step into a role that involves handling, storing, or using hazardous substances, you must be equipped with the knowledge to identify, assess, and mitigate potential risks. WHMIS training provides you with the necessary skills to read and understand Safety Data Sheets (SDSs), recognize hazard symbols on labels, and follow proper procedures for safe handling and emergency response. This training also covers the classification of hazardous materials, which is essential for understanding the specific risks associated with each substance. By understanding these classifications, you can take appropriate precautions to protect yourself and your colleagues from chemical hazards. Moreover, WHMIS training emphasizes the importance of personal protective equipment (PPE) and teaches you how to use it correctly. In the event of an accident or spill, knowing the correct procedures can significantly reduce the risk of injury or environmental damage. Employers are legally mandated to provide WHMIS training to employees who work with hazardous materials, but it is also a moral obligation to ensure that all staff members are adequately prepared to handle these substances safely. Therefore, if you are transferring to a new job role that involves hazardous materials, seeking out WHMIS training should be your top priority to ensure a safe and compliant work environment. This training not only enhances your professional competence but also contributes to a culture of safety within your organization.
Return to Work After Extended Leave
When an employee returns to work after an extended leave, it is crucial to ensure their safe and effective reintegration into the workplace. This period can be particularly challenging, especially if the employee has been away for an extended duration due to health issues, family leave, or other personal reasons. To facilitate a smooth transition, employers must consider several key factors. First, a thorough review of the employee's job duties and any changes that may have occurred during their absence is essential. This includes updating them on new policies, procedures, and any modifications to their role or responsibilities. Additionally, providing refresher training on workplace safety protocols and procedures is vital to prevent accidents and ensure compliance with regulatory standards. For workplaces that handle hazardous materials, WHMIS (Workplace Hazardous Materials Information System) training becomes particularly important upon an employee's return. WHMIS training ensures that employees understand the risks associated with hazardous substances, how to handle them safely, and what to do in case of emergencies. Given the potential for rustiness or lack of familiarity with current safety protocols after an extended leave, it is imperative that returning employees receive comprehensive WHMIS training to bring them up-to-date on all necessary information. Moreover, employers should also consider the psychological and physical well-being of the returning employee. A gradual return-to-work plan may be necessary to help them readjust to the demands of their job without exacerbating any health issues. Open communication between the employer and employee is key during this period to address any concerns or needs that may arise. By combining thorough safety training with a supportive return-to-work strategy, employers can not only ensure compliance with regulatory requirements but also foster a safe and productive work environment for all employees. In summary, returning to work after an extended leave requires a multifaceted approach that includes updating job knowledge, refresher safety training such as WHMIS, and addressing the overall well-being of the employee. This holistic approach not only ensures compliance with safety regulations but also supports the successful reintegration of employees into the workplace.
Regulatory Updates or Changes in WHMIS Standards
Regulatory updates and changes in WHMIS (Workplace Hazardous Materials Information System) standards are crucial for ensuring the safety and health of workers handling hazardous materials. The most significant recent update was the alignment of WHMIS with the Globally Harmonized System of Classification and Labelling of Chemicals (GHS), which has been phased in since 2015. This alignment introduced new classification criteria, hazard communication elements, and standardized labels and safety data sheets (SDSs). For instance, the GHS-based WHMIS 2015 requires that chemical manufacturers and importers classify their products based on specific hazard criteria, leading to more accurate and consistent hazard communication. Additionally, the new SDS format includes 16 sections that provide detailed information about the chemical, its hazards, and safe handling practices. These changes necessitate ongoing training to ensure that workers are familiar with the updated labels, SDSs, and classification systems. Employers must also update their workplace procedures and training programs to reflect these changes, emphasizing the importance of continuous education in maintaining a safe work environment. Furthermore, regulatory bodies such as Health Canada continue to issue updates and clarifications on WHMIS standards, making it essential for employers to stay informed and adapt their training programs accordingly. This dynamic regulatory landscape underscores the need for regular WHMIS training to address special circumstances that arise from these updates and changes, ensuring that all workers are equipped with the knowledge and skills necessary to handle hazardous materials safely and effectively. By staying abreast of these regulatory updates, employers can mitigate risks, comply with legal requirements, and foster a culture of safety within their organizations.