When Does Whmis Expire

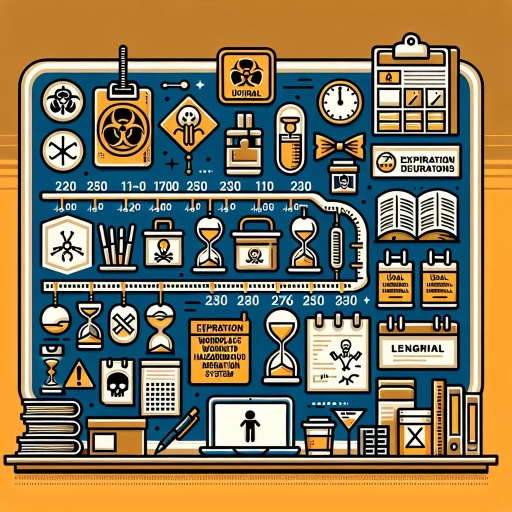
The Workplace Hazardous Materials Information System (WHMIS) is a critical component of workplace safety in Canada, ensuring that workers are informed about the hazards of chemicals they use. However, with ongoing updates and transitions, it can be challenging to keep track of when WHMIS requirements expire or change. This article aims to provide clarity on these issues by delving into three key areas: Understanding WHMIS and Its Regulatory Framework, Transition Periods and Implementation Phases, and Current Status and Future Updates. By grasping the foundational principles of WHMIS and its regulatory framework, readers will better comprehend the system's evolution. The discussion on transition periods and implementation phases will highlight the timelines and milestones that have shaped WHMIS over the years. Finally, an examination of the current status and future updates will equip readers with the latest information necessary for compliance. Let's begin by Understanding WHMIS and Its Regulatory Framework, which forms the bedrock of this essential workplace safety system.
Understanding WHMIS and Its Regulatory Framework
In the realm of workplace safety, few regulations are as critical as the Workplace Hazardous Materials Information System (WHMIS). Designed to protect workers from the dangers of hazardous materials, WHMIS is a comprehensive framework that ensures employers and employees are well-informed about the risks associated with chemical substances. This article delves into the intricacies of WHMIS, beginning with an **Overview of WHMIS and Its Purpose**, which explores how this system was established to safeguard health and safety in Canadian workplaces. We will then examine the **Key Components of WHMIS Regulations**, detailing the essential elements such as classification, labeling, and safety data sheets that form the backbone of this regulatory framework. Finally, we will discuss the **Role of Health Canada in WHMIS Enforcement**, highlighting the agency's responsibilities in ensuring compliance and maintaining a safe working environment. By understanding these facets, readers will gain a thorough grasp of WHMIS and its regulatory framework, equipping them to navigate the complexities of hazardous material management effectively. Understanding WHMIS and Its Regulatory Framework is crucial for any organization handling hazardous substances, and this article aims to provide a clear, informative guide to achieve that understanding.
Overview of WHMIS and Its Purpose
The Workplace Hazardous Materials Information System (WHMIS) is a comprehensive regulatory framework designed to ensure the safe handling, use, and disposal of hazardous materials in Canadian workplaces. Implemented to protect workers from the dangers associated with hazardous substances, WHMIS mandates that employers provide their employees with essential information about the chemicals they work with. This system is built around three key components: labels, safety data sheets (SDSs), and worker training. **Labels** are critical for immediate hazard identification. They must be affixed to containers of hazardous products and include pictograms, hazard statements, precautionary statements, and supplier information. These visual cues alert workers to potential dangers at a glance, enabling them to take appropriate precautions. **Safety Data Sheets (SDSs)** provide detailed information about each hazardous product. These documents outline the chemical composition, physical and chemical properties, fire-fighting measures, accidental release measures, handling and storage procedures, exposure controls/personal protection, stability and reactivity data, toxicological information, ecological information, disposal considerations, transport information, regulatory information, and other relevant details. SDSs serve as a reference guide for safe handling practices and emergency response procedures. **Worker Training** is the cornerstone of WHMIS compliance. Employers are required to educate their employees on how to safely handle hazardous materials through comprehensive training programs. This includes understanding the hazards associated with specific chemicals, how to read labels and SDSs, and the proper use of personal protective equipment (PPE). Effective training ensures that workers can recognize hazards and take necessary steps to mitigate risks. The purpose of WHMIS is multifaceted. It aims to prevent injuries and illnesses by providing workers with the knowledge they need to handle hazardous materials safely. By standardizing labeling and SDS formats, WHMIS facilitates easier communication of critical safety information across different workplaces and industries. Additionally, WHMIS aligns Canada with international standards for chemical safety, such as those set by the United Nations' Globally Harmonized System of Classification and Labelling of Chemicals (GHS). This alignment enhances global trade while ensuring consistent safety protocols. In summary, WHMIS is an integral part of workplace safety in Canada, ensuring that workers are well-informed about the hazards they encounter daily. Through its robust framework of labels, SDSs, and worker training, WHMIS plays a crucial role in preventing accidents and promoting a safer work environment. Understanding WHMIS is essential for compliance with regulatory requirements and for maintaining a culture of safety within any organization that handles hazardous materials.
Key Components of WHMIS Regulations
The Workplace Hazardous Materials Information System (WHMIS) is a critical component of workplace safety in Canada, and understanding its key components is essential for compliance and effective risk management. At the heart of WHMIS are three primary elements: **Classification**, **Labels**, and **Safety Data Sheets (SDSs)**. **Classification** involves categorizing hazardous products based on their physical and health hazards. This process ensures that products are identified and communicated accurately, allowing employers and workers to take appropriate precautions. The classification criteria are aligned with the Globally Harmonized System of Classification and Labelling of Chemicals (GHS), ensuring international consistency and clarity. **Labels** are another crucial aspect of WHMIS. These labels provide immediate visual information about the hazards associated with a product. They must include specific elements such as the product identifier, hazard statements, precautionary statements, and pictograms that visually represent the hazards. This standardized labeling system ensures that workers can quickly identify potential dangers and take necessary safety measures. **Safety Data Sheets (SDSs)** are detailed documents that provide comprehensive information about a hazardous product. Each SDS must follow a standardized format and include sections such as identification, hazard identification, composition/information on ingredients, first aid measures, fire-fighting measures, accidental release measures, handling and storage, exposure controls/personal protection, physical and chemical properties, stability and reactivity, toxicological information, ecological information, disposal considerations, transport information, regulatory information, and other information. SDSs serve as a resource for employers to develop safe work practices and for workers to understand how to handle hazardous materials safely. In addition to these core components, WHMIS also mandates **Training and Education** for workers who handle hazardous materials. Employers are required to provide training that includes general WHMIS awareness, workplace-specific procedures for handling hazardous products, and how to access and interpret labels and SDSs. This training is essential for ensuring that workers can recognize hazards and respond appropriately in emergency situations. Furthermore, **Regulatory Compliance** is a key component of WHMIS. The regulations are enforced by Health Canada and provincial/territorial authorities. Employers must ensure that all hazardous products in their workplace comply with WHMIS requirements, including proper labeling and SDS availability. Non-compliance can result in significant fines and penalties. In summary, understanding the key components of WHMIS—classification, labels, SDSs, training, and regulatory compliance—is vital for maintaining a safe workplace environment. By adhering to these elements, employers can protect their workers from the risks associated with hazardous materials and ensure compliance with Canadian regulations. This comprehensive approach to workplace safety underscores the importance of WHMIS in preventing injuries and illnesses related to chemical exposure.
Role of Health Canada in WHMIS Enforcement
Health Canada plays a pivotal role in the enforcement of the Workplace Hazardous Materials Information System (WHMIS), ensuring that hazardous materials are handled, used, and disposed of safely in Canadian workplaces. As part of its broader mandate to protect public health and safety, Health Canada is responsible for developing and enforcing the regulations under WHMIS. This includes setting standards for the classification of hazardous products, labeling requirements, and the provision of safety data sheets (SDSs). Health Canada collaborates closely with other federal, provincial, and territorial authorities to ensure a harmonized approach across Canada. One of the key functions of Health Canada in WHMIS enforcement is the development and updating of regulations. The Hazardous Products Regulations (HPR) and the Hazardous Products Act (HPA) are central to this effort, providing the legal framework that governs how hazardous products are classified, labeled, and communicated to workers. Health Canada also issues guidelines and interpretations to help employers and suppliers comply with these regulations. In addition to regulatory development, Health Canada conducts inspections and investigations to ensure compliance with WHMIS requirements. This involves monitoring workplaces to verify that employers are providing appropriate training to employees, maintaining accurate SDSs, and ensuring that hazardous products are properly labeled. Non-compliance can result in enforcement actions, including fines and other penalties. Health Canada also engages in public education and outreach efforts to raise awareness about WHMIS among employers, workers, and suppliers. This includes providing educational resources, conducting workshops, and collaborating with other stakeholders such as labor unions and industry associations. By fostering a culture of safety and compliance, Health Canada aims to reduce the risks associated with hazardous materials in the workplace. Furthermore, Health Canada works internationally to align Canadian WHMIS standards with global best practices. The adoption of the Globally Harmonized System of Classification and Labelling of Chemicals (GHS) has been a significant initiative in this regard, ensuring that Canadian regulations are consistent with international standards. This alignment facilitates trade while maintaining high safety standards. In summary, Health Canada's role in WHMIS enforcement is multifaceted and critical. Through regulatory development, compliance monitoring, public education, and international collaboration, Health Canada ensures that hazardous materials are managed safely in Canadian workplaces, protecting the health and well-being of workers and the broader public. This comprehensive approach underscores the importance of WHMIS as a cornerstone of workplace safety in Canada.
Transition Periods and Implementation Phases
Transition periods and implementation phases are critical components in the evolution of regulatory standards, particularly in the realm of workplace safety. The shift from WHMIS 1988 to WHMIS 2015, for instance, marked a significant transformation in how hazardous materials are classified, labeled, and communicated within Canadian workplaces. This transition was not merely a change in regulations but also involved stringent deadlines for compliance, ensuring that all stakeholders were aligned with the new standards. The impact of these changes extends beyond mere compliance; it fundamentally alters workplace safety protocols and training methodologies, necessitating a comprehensive understanding of the new framework. As we delve into the specifics of this transition, it becomes clear that grasping the intricacies of these implementation phases is essential for maintaining a safe and compliant work environment. This article will explore the transition from WHMIS 1988 to WHMIS 2015, the deadlines for compliance with new standards, and the profound impact on workplace safety and training, ultimately leading to a deeper understanding of WHMIS and its regulatory framework.
Transition from WHMIS 1988 to WHMIS 2015
The transition from WHMIS 1988 to WHMIS 2015 marked a significant shift in Canada's workplace hazardous materials information system, aligning with the Globally Harmonized System of Classification and Labelling of Chemicals (GHS). This transition was not an overnight process but rather a phased implementation to ensure a smooth and effective adaptation. The transition period, which spanned several years, was divided into distinct phases to accommodate various stakeholders, including manufacturers, distributors, and employers. **Phase 1: Manufacturer and Importer Transition (2015-2017)** During this initial phase, manufacturers and importers were required to classify their hazardous products according to the new GHS standards and prepare Safety Data Sheets (SDSs) and labels that comply with WHMIS 2015. This phase allowed these entities to adapt their systems and ensure compliance with the new regulations before the broader implementation. **Phase 2: Distributor Transition (2017-2018)** In the second phase, distributors were given a grace period to sell off existing stock labeled under WHMIS 1988 while also starting to receive and distribute products labeled under WHMIS 2015. This phase helped in managing inventory and reducing potential disruptions in the supply chain. **Phase 3: Employer Transition (2018)** The final phase focused on employers, who were required to update their workplace procedures, train employees on the new SDSs and labels, and ensure that all hazardous products in the workplace were compliant with WHMIS 2015 by June 1, 2018. Employers had to conduct thorough hazard assessments, update their chemical inventories, and provide comprehensive training to employees on the new classification system. Throughout these phases, Health Canada provided extensive guidance and resources to support the transition. This included updated regulations, training materials, and compliance tools to help stakeholders understand and implement the changes effectively. The phased approach allowed for a gradual transition, minimizing disruptions and ensuring that all parties were adequately prepared for the full implementation of WHMIS 2015. In summary, the transition from WHMIS 1988 to WHMIS 2015 was a well-orchestrated process that involved multiple stakeholders and phases. By staggering the implementation, Canada ensured a seamless integration of GHS standards into its workplace safety protocols, enhancing the overall safety and health of workers handling hazardous materials. This structured approach not only facilitated compliance but also underscored Canada's commitment to aligning with international best practices in chemical safety.
Deadlines for Compliance with New Standards
When navigating the complexities of compliance with new standards, understanding the deadlines for implementation is crucial. These deadlines are often part of a broader transition period, which allows organizations to gradually adapt to the new requirements without disrupting their operations. For instance, in the context of WHMIS (Workplace Hazardous Materials Information System), transition periods are designed to ease the shift from one standard to another, ensuring that all stakeholders have sufficient time to update their processes and materials. During these transition periods, organizations typically go through several implementation phases. The first phase involves awareness and planning, where companies must educate their staff about the upcoming changes and develop strategies for compliance. This includes updating safety data sheets, labels, and training programs to align with the new standards. The second phase focuses on the actual implementation, where the updated materials and procedures are rolled out across the organization. This phase requires meticulous attention to detail to ensure that all aspects of the new standard are met. The final phase involves ongoing monitoring and evaluation to ensure sustained compliance. Here, companies must continuously review their practices to identify any gaps or areas for improvement. Regular audits and feedback mechanisms are essential during this phase to maintain high standards of safety and compliance. Deadlines for compliance are set to ensure that all organizations adhere to the new standards within a reasonable timeframe. These deadlines can vary depending on the nature of the changes and the industry involved. For example, in the case of WHMIS, the transition from WHMIS 1988 to WHMIS 2015 included specific deadlines for different aspects of compliance, such as the phase-in periods for supplier labels and safety data sheets. Meeting these deadlines is not just about avoiding penalties but also about ensuring a safe and healthy work environment. Non-compliance can lead to serious consequences, including fines, legal action, and most importantly, risks to employee safety. Therefore, it is imperative for organizations to prioritize these deadlines and manage their transition periods effectively. In summary, understanding and adhering to deadlines for compliance with new standards is vital for any organization. By breaking down the transition into manageable phases—awareness, implementation, and ongoing monitoring—companies can ensure a smooth transition that maintains high levels of safety and regulatory compliance. This structured approach not only helps in avoiding potential penalties but also fosters a culture of continuous improvement and adherence to best practices.
Impact on Workplace Safety and Training
During transition periods and implementation phases, the impact on workplace safety and training is multifaceted and critical. As new regulations or standards, such as those related to WHMIS (Workplace Hazardous Materials Information System), are introduced or updated, it is essential to ensure that all employees are adequately trained to handle the changes. This involves comprehensive training programs that cover the identification, handling, and use of hazardous materials, as well as the proper use of personal protective equipment (PPE) and emergency response procedures. Effective training during these periods helps in mitigating risks associated with the introduction of new substances or processes. It ensures that workers understand the updated safety data sheets (SDSs), labels, and other critical information necessary for safe handling practices. Moreover, continuous training reinforces a culture of safety within the workplace, encouraging employees to report any hazards or near-miss incidents promptly. This proactive approach not only enhances compliance with regulatory requirements but also reduces the likelihood of accidents and injuries. The implementation phase is particularly crucial as it sets the foundation for long-term safety practices. Employers must allocate sufficient resources to develop and deliver high-quality training sessions, which may include hands-on training, simulations, and regular refresher courses. Additionally, engaging with employees through feedback mechanisms helps in identifying gaps in training and making necessary adjustments to ensure that all workers feel confident and competent in their roles. Technology can also play a significant role in enhancing workplace safety training during transition periods. Utilizing digital platforms for training can provide accessible and flexible learning opportunities, allowing employees to complete modules at their own pace. Interactive tools such as virtual reality simulations can further enhance the learning experience by providing realistic scenarios that mimic real-world situations. Ultimately, the success of workplace safety and training during transition periods hinges on a well-planned implementation strategy. This includes clear communication of changes, regular monitoring of compliance, and continuous evaluation of training effectiveness. By prioritizing these elements, organizations can navigate transition phases smoothly while maintaining a safe and healthy work environment for all employees. This proactive approach not only ensures regulatory compliance but also fosters a resilient and adaptable workforce capable of handling future changes with confidence.
Current Status and Future Updates
In the ever-evolving landscape of workplace safety, understanding and adhering to the current status and future updates of regulatory frameworks is paramount. The Workplace Hazardous Materials Information System (WHMIS) stands as a cornerstone in ensuring the safe handling and use of hazardous materials in Canadian workplaces. This article delves into three critical aspects that employers and stakeholders must be aware of: **Current Compliance Requirements for Employers**, which outlines the existing standards and obligations; **Potential Future Changes to WHMIS Regulations**, highlighting anticipated modifications that could impact compliance strategies; and **Importance of Staying Updated with Regulatory Changes**, emphasizing the necessity of continuous awareness to maintain a safe and compliant work environment. By exploring these key areas, this article aims to provide a comprehensive overview that transitions seamlessly into **Understanding WHMIS and Its Regulatory Framework**, equipping readers with the knowledge needed to navigate the complexities of WHMIS effectively.
Current Compliance Requirements for Employers
**Current Compliance Requirements for Employers** In the ever-evolving landscape of workplace safety, employers must remain vigilant and compliant with current regulations to ensure a safe and healthy environment for their employees. As of now, employers are mandated to adhere to a plethora of compliance requirements, each designed to mitigate specific risks and enhance overall workplace safety. One of the cornerstone regulations is the Workplace Hazardous Materials Information System (WHMIS), which dictates how hazardous materials are classified, labeled, and communicated within the workplace. Employers must ensure that all hazardous materials are properly labeled and that Safety Data Sheets (SDSs) are readily available to employees. Additionally, employers are required to provide comprehensive training programs that equip employees with the knowledge to handle these materials safely. Beyond WHMIS, employers must also comply with the Occupational Health and Safety (OHS) regulations, which encompass a broad range of responsibilities including conducting regular risk assessments, implementing control measures, and maintaining accurate records of workplace incidents and injuries. The OHS regulations also mandate that employers establish a health and safety policy and program, which includes procedures for reporting hazards and incidents, conducting investigations, and implementing corrective actions. Furthermore, employers are obligated to comply with accessibility standards under the Accessibility for Ontarians with Disabilities Act (AODA), ensuring that their workplaces are inclusive and barrier-free for employees with disabilities. This includes providing accessible communication formats, training staff on disability awareness, and ensuring that physical spaces are navigable. In terms of employment standards, employers must adhere to the Employment Standards Act (ESA), which governs aspects such as minimum wage, hours of work, vacation time, and termination notice. Compliance with these standards is crucial to maintaining fair labor practices and avoiding legal repercussions. Moreover, employers have a duty to protect employee privacy under the Personal Information Protection and Electronic Documents Act (PIPEDA), ensuring that personal information is collected, used, and disclosed in a manner that respects individual privacy rights. Compliance with these regulations is not merely a legal necessity but also a moral imperative. By adhering to these standards, employers can foster a culture of safety, inclusivity, and respect within their organizations. Regular audits and updates to policies and procedures are essential to ensure ongoing compliance as regulations evolve. As we look towards future updates and potential changes in these compliance requirements, it is imperative for employers to stay informed and proactive in their commitment to workplace safety and legal adherence.
Potential Future Changes to WHMIS Regulations
As we navigate the evolving landscape of workplace safety, potential future changes to WHMIS (Workplace Hazardous Materials Information System) regulations are on the horizon. The current WHMIS 2015 standard, aligned with the Globally Harmonized System of Classification and Labelling of Chemicals (GHS), has been a cornerstone in ensuring the safe handling and use of hazardous materials in Canadian workplaces. However, regulatory bodies are continually assessing and refining these standards to reflect new scientific findings, technological advancements, and international best practices. One anticipated change involves the integration of more detailed and specific hazard classifications. This could include updates to the criteria for classifying health hazards, such as carcinogenicity and reproductive toxicity, to better align with emerging research. Additionally, there may be enhancements to the labelling requirements, including more comprehensive safety data sheets (SDSs) that provide clearer instructions for safe use and emergency response procedures. These updates would aim to reduce confusion among workers and improve overall compliance. Another area of focus is likely to be the expansion of WHMIS coverage to include new types of hazardous substances that have been identified since the last major update. For instance, nanomaterials and certain biohazards may be brought under the purview of WHMIS, necessitating new guidelines for their handling and disposal. This expansion would ensure that workers are adequately protected from emerging hazards in the workplace. Technological advancements are also expected to play a significant role in future WHMIS updates. Digital platforms and mobile applications could become integral tools for disseminating safety information, allowing for real-time updates and easier access to SDSs. This shift towards digital compliance could streamline training processes and enhance worker engagement with safety protocols. Furthermore, there is a growing emphasis on harmonization with international standards. As global trade increases, ensuring that Canadian WHMIS regulations are aligned with those of other countries will facilitate smoother import and export processes while maintaining high safety standards. This harmonization effort may involve adopting additional GHS revisions or incorporating elements from other countries' regulatory frameworks. In conclusion, the future of WHMIS regulations promises to be dynamic and responsive to the changing needs of workplace safety. By incorporating new scientific data, leveraging technology, and aligning with international standards, these updates will continue to protect workers from hazardous materials while fostering a safer and more compliant work environment. As these changes unfold, it is crucial for employers, workers, and regulatory bodies to remain vigilant and proactive in adapting to these evolving standards.
Importance of Staying Updated with Regulatory Changes
Staying updated with regulatory changes is paramount in today's fast-paced and ever-evolving work environment, particularly when it comes to safety standards like WHMIS (Workplace Hazardous Materials Information System). Regulatory updates often reflect new scientific findings, technological advancements, and lessons learned from past incidents, all aimed at enhancing workplace safety and reducing risks associated with hazardous materials. By keeping abreast of these changes, organizations can ensure compliance with legal requirements, avoid costly fines and penalties, and maintain a positive reputation. Moreover, updated regulations frequently incorporate best practices that have been proven to reduce accidents and improve overall workplace health. For instance, changes in labeling requirements or safety data sheets (SDSs) can provide clearer information about the hazards of specific chemicals, enabling workers to handle them more safely. Additionally, staying informed about regulatory updates helps organizations adapt their training programs to include the latest safety protocols and procedures, which is crucial for maintaining a competent and safe workforce. From a business perspective, being proactive about regulatory compliance can also offer competitive advantages. Companies that are ahead of the curve in terms of regulatory adherence are often seen as more reliable and responsible partners by clients and stakeholders. This can lead to increased trust and loyalty, ultimately driving business growth. Furthermore, regulatory updates can impact various aspects of an organization's operations beyond just safety protocols. They may influence procurement decisions, inventory management, and even environmental policies. For example, changes in regulations might necessitate the adoption of more sustainable practices or the use of less hazardous materials, which can have broader environmental benefits. In the context of WHMIS specifically, staying updated is critical as it ensures that workers are adequately informed about the hazards they may encounter on the job. The transition from WHMIS 1988 to WHMIS 2015, for instance, aligned Canadian standards with the Globally Harmonized System of Classification and Labelling of Chemicals (GHS), providing a more consistent and internationally recognized framework for chemical safety. As future updates are anticipated, remaining vigilant will be essential for seamless integration and continued compliance. In summary, staying updated with regulatory changes is not merely a legal obligation but a strategic imperative for any organization committed to safety, compliance, and long-term success. It fosters a culture of safety, enhances operational efficiency, and positions businesses for future growth by aligning them with the latest standards and best practices in workplace safety. As the landscape of regulatory requirements continues to evolve, staying informed will remain a key factor in ensuring that workplaces remain safe, compliant, and competitive.