When Must A Personal Flotation Device (pfd) Or Lifejacket Be Replaced?

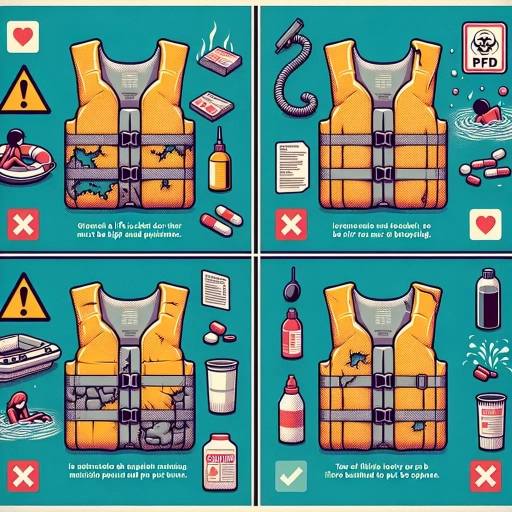
When it comes to ensuring safety on the water, a personal flotation device (PFD) or lifejacket is an indispensable piece of equipment. However, these devices are not invincible and must be replaced periodically to maintain their effectiveness. The decision to replace a PFD involves several critical factors, each of which plays a significant role in determining its usability. First, there are the visible signs of wear and tear that can compromise the device's integrity. Additionally, expiration dates and certification standards must be adhered to, as they are set by regulatory bodies to ensure safety. Lastly, usage patterns and environmental factors can also impact the lifespan of a PFD. Understanding these elements is crucial for making informed decisions about when to replace your life-saving gear. In this article, we will delve into these key considerations, starting with the often-overlooked yet critical aspect of signs of wear and tear.
Signs of Wear and Tear
When it comes to maintaining and extending the life of your belongings, whether they are furniture, clothing, or equipment, recognizing signs of wear and tear is crucial. Over time, even the most durable items can show signs of deterioration that, if ignored, can lead to significant damage or complete failure. This article will delve into three key indicators of wear and tear that you should be aware of: visible damage to the fabric, loss of buoyancy, and broken or corroded hardware. By understanding these signs, you can take proactive steps to address issues before they escalate, ensuring your possessions remain in good condition for longer. Whether you're a homeowner, an outdoor enthusiast, or someone who values longevity in their belongings, being able to identify these signs is essential for effective maintenance and preservation. In this article, we will explore each of these indicators in detail, providing you with the knowledge you need to recognize and respond to signs of wear and tear effectively.
Visible Damage to the Fabric
Visible damage to the fabric of a personal flotation device (PFD) or lifejacket is a critical indicator that it may no longer provide the necessary safety and buoyancy in emergency situations. When inspecting your PFD, it is essential to look for any signs of wear and tear that could compromise its integrity. Visible damage can manifest in various forms, such as tears, cuts, or punctures in the fabric. These breaches can allow water to penetrate the flotation material, reducing its ability to keep you afloat. Additionally, fraying or unraveling of seams can weaken the structural integrity of the PFD, making it more susceptible to further damage during use. Another significant aspect of visible damage is discoloration or fading of the fabric. While these changes might seem cosmetic, they can indicate exposure to harmful UV rays or chemicals that could degrade the material over time. Furthermore, any signs of mold, mildew, or staining should be taken seriously as they can weaken the fabric and create an environment conducive to further deterioration. It is also crucial to inspect the hardware components attached to the PFD, such as buckles, straps, and zippers. Corrosion on metal parts or cracks in plastic components can render these essential elements dysfunctional, making it difficult or impossible to secure the PFD properly. Any visible signs of wear on these components should prompt immediate attention and potentially necessitate replacement. In addition to these physical inspections, it is important to consider the age of your PFD. Even if no visible damage is apparent, older models may have undergone internal degradation due to prolonged exposure to environmental factors. Manufacturers often provide guidelines on the lifespan of their products; adhering to these recommendations ensures that your PFD remains reliable and effective. Ultimately, visible damage to the fabric of a PFD is a clear signal that it may no longer be safe for use. Given the critical role these devices play in ensuring survival during water emergencies, it is imperative to replace any PFD showing signs of visible damage promptly. Regular inspections and adherence to manufacturer guidelines are key steps in maintaining the reliability and effectiveness of your personal flotation device. By staying vigilant about these signs of wear and tear, you can ensure your safety and the safety of others when engaging in water activities.
Loss of Buoyancy
Loss of buoyancy is a critical indicator that a personal flotation device (PFD) or lifejacket may need to be replaced. Over time, the materials used in these devices can degrade, leading to a reduction in their ability to provide adequate flotation. This degradation can occur due to various factors such as exposure to sunlight, saltwater, and chemicals, which can break down the foam or inflatable components. For instance, UV rays can cause the foam to become brittle and lose its buoyant properties, while saltwater and chemicals can corrode or damage the fabric and seams of the PFD. Additionally, physical wear and tear from frequent use or improper storage can also compromise the integrity of the device. If a PFD no longer meets the required buoyancy standards, it may not be able to keep a person afloat in an emergency situation, posing a significant risk to safety. Therefore, it is essential to regularly inspect PFDs for signs of wear and tear, including cracks in the foam, tears in the fabric, and any visible signs of degradation. If such signs are observed, or if the device fails a buoyancy test, it should be replaced immediately to ensure continued safety on the water. Regular maintenance and adherence to manufacturer guidelines are crucial in extending the lifespan of a PFD while maintaining its effectiveness as a lifesaving device. By being vigilant about loss of buoyancy and other signs of wear and tear, individuals can ensure that their PFDs remain reliable and effective when needed most.
Broken or Corroded Hardware
When assessing whether a personal flotation device (PFD) or lifejacket needs to be replaced, one critical factor to consider is the condition of its hardware. Broken or corroded hardware can significantly compromise the safety and functionality of a PFD, making it imperative to inspect these components meticulously. Hardware includes buckles, straps, zippers, and any other metal or plastic parts that secure the device in place. Over time, exposure to saltwater, sunlight, and repeated use can cause these elements to deteriorate. Corrosion on metal parts can weaken their structural integrity, while broken plastic components may no longer provide the necessary support or security. For instance, if a buckle is rusted or cracked, it may fail under stress, leading to the PFD coming undone in an emergency situation. Similarly, frayed or snapped straps can render the device unusable. It is crucial to check for any signs of wear such as cracks, rust spots, or excessive wear on moving parts. If any of these issues are identified, it is advisable to replace the PFD immediately to ensure safety on the water. Regular maintenance and inspections are key in preventing such failures and ensuring that your PFD remains reliable and effective in its primary function: saving lives. By paying close attention to the condition of hardware and addressing any issues promptly, you can help extend the lifespan of your PFD while maintaining its critical safety features. Always refer to the manufacturer's guidelines for specific inspection and replacement recommendations to guarantee optimal performance and compliance with safety standards. In summary, broken or corroded hardware is a clear indicator that a PFD needs to be replaced, emphasizing the importance of regular inspections to uphold safety standards and prevent potential hazards.
Expiration Dates and Certification
Expiration dates and certification are crucial elements in ensuring the safety, quality, and reliability of products across various industries. These markers not only inform consumers about the shelf life of a product but also provide assurance that the item has met stringent standards set by regulatory bodies. In this article, we will delve into three key aspects: the significance of the manufacturer's expiration date, the importance of certification from regulatory bodies, and the rigorous inspection and testing requirements that products must undergo. Understanding these components is essential for consumers to make informed decisions and for manufacturers to maintain compliance with industry standards. As we explore these topics, it becomes clear that while expiration dates and certifications are vital, they are not the only indicators of a product's condition. Signs of wear and tear, which we will discuss further, can also provide critical insights into a product's usability and longevity. By examining these interconnected factors, we can better appreciate the comprehensive approach needed to ensure product integrity and consumer safety.
Manufacturer's Expiration Date
When it comes to ensuring the safety and reliability of personal flotation devices (PFDs) or lifejackets, understanding the concept of the Manufacturer's Expiration Date is crucial. This date, often marked on the device itself, signifies the end of the manufacturer's warranty period and indicates when the PFD or lifejacket may no longer meet safety standards due to potential degradation of materials over time. Unlike food products, where expiration dates are more about freshness and quality, the expiration date on a PFD or lifejacket is primarily about ensuring that the device remains effective in saving lives. Manufacturers conduct rigorous testing to determine how long their products can withstand various environmental conditions without compromising their buoyancy and structural integrity. Factors such as exposure to sunlight, saltwater, and wear and tear are considered in these tests. Once a PFD or lifejacket reaches its expiration date, it is no longer guaranteed to perform as intended in an emergency situation. This is why regulatory bodies and safety guidelines emphasize the importance of adhering to these dates. For instance, the U.S. Coast Guard mandates that PFDs must be in serviceable condition and meet specific standards to be considered compliant. If a PFD has exceeded its manufacturer's expiration date, it does not meet these standards, even if it appears to be in good condition visually. The risk of failure increases significantly after this period, making it imperative for users to replace their PFDs or lifejackets accordingly. In addition to the expiration date, regular inspections are also necessary to ensure that the device remains in good working order. Users should check for signs of damage, such as cracks in the plastic, frayed straps, or any other visible deterioration. However, even if no visible damage is present, the expiration date should still be respected as it reflects the manufacturer's confidence in the product's performance over time. In summary, the Manufacturer's Expiration Date on a PFD or lifejacket is a critical indicator of when the device should be replaced to ensure continued safety and compliance with regulatory standards. Ignoring this date could lead to serious consequences in emergency situations, making it essential for users to prioritize regular inspections and timely replacements based on these guidelines. By doing so, individuals can trust that their PFDs or lifejackets will function as intended when needed most.
Certification from Regulatory Bodies
Certification from regulatory bodies is a crucial aspect when determining the validity and reliability of personal flotation devices (PFDs) or lifejackets. These certifications ensure that the devices meet stringent safety standards, thereby safeguarding users in various aquatic environments. Regulatory bodies such as the U.S. Coast Guard, Transport Canada, and the International Organization for Standardization (ISO) play pivotal roles in setting and enforcing these standards. For instance, the U.S. Coast Guard certifies PFDs under specific categories based on their intended use, such as Type I for offshore use, Type II for near-shore use, and Type III for general use. Each category has its own set of performance requirements, including buoyancy, durability, and visibility. The certification process involves rigorous testing to ensure that PFDs can withstand various conditions and provide the necessary flotation support. This includes tests for buoyancy, impact resistance, and degradation over time. Manufacturers must also adhere to labeling and marking requirements, which include clear instructions on use, maintenance, and inspection. Additionally, certifications often come with expiration dates or specific service life recommendations, indicating when a PFD should be replaced to maintain its effectiveness. For example, inflatable life jackets may have an expiration date for the CO2 cartridges used for inflation, while foam life jackets may have a recommended service life based on wear and tear. These guidelines are essential because PFDs can degrade over time due to exposure to sunlight, saltwater, or mechanical stress, which could compromise their performance in emergency situations. By adhering to these certifications and following the recommended replacement schedules, users can ensure that their PFDs remain in good condition and provide the necessary safety assurance. In summary, certification from regulatory bodies is indispensable for ensuring the safety and efficacy of PFDs. These certifications not only validate the initial quality of the device but also provide clear guidelines for maintenance and replacement, thereby enhancing user safety and compliance with legal requirements. As part of the broader discussion on expiration dates and certification, understanding these regulatory standards is vital for making informed decisions about when a PFD or lifejacket should be replaced to maintain optimal safety standards.
Inspection and Testing Requirements
When it comes to ensuring the safety and reliability of personal flotation devices (PFDs) or lifejackets, adherence to strict inspection and testing requirements is paramount. These protocols are crucial for determining whether a PFD remains in good condition and should be part of regular maintenance routines. Here’s a detailed look at these essential steps: **Visual Inspection:** The first line of defense is a thorough visual inspection. Users should meticulously check for any signs of wear, damage, or degradation. This includes examining the fabric for tears, cuts, or fraying; inspecting the seams for any signs of separation; and checking the straps, buckles, and other hardware for corrosion or breakage. Any visible damage indicates that the PFD may no longer provide adequate buoyancy and should be replaced. **Inflation Test:** For inflatable PFDs, an inflation test is necessary to ensure that the device can hold air properly. This involves inflating the PFD according to the manufacturer’s instructions and then checking for leaks by submerging it in water or using a soapy solution to detect any air escaping. If the PFD fails to hold air or shows significant leakage, it is no longer reliable. **Buoyancy Test:** Conducting a buoyancy test is another critical step. This involves weighing down the PFD with a known weight and then submerging it in water to measure its buoyancy. If the PFD does not provide the required level of buoyancy as specified by the manufacturer or regulatory standards, it should be replaced. **Cleaning and Storage:** Proper cleaning and storage are also vital components of maintaining a PFD’s integrity. Users should follow the manufacturer’s guidelines for cleaning and drying the device to prevent mold and mildew buildup. Improper storage can lead to damage from exposure to sunlight, moisture, or physical impact, all of which can compromise the PFD’s performance. **Certification and Expiration Dates:** Many PFDs come with certification from organizations such as the U.S. Coast Guard or ISO (International Organization for Standardization). These certifications often include expiration dates that indicate when the device is no longer considered safe for use. It is imperative to adhere to these expiration dates and replace the PFD accordingly, even if it appears to be in good condition. In summary, regular inspection and testing of PFDs are essential for ensuring they remain safe and effective. By following these steps diligently, users can identify potential issues before they become critical safety hazards. Remember, a PFD that fails any part of these inspections or tests should be replaced immediately to guarantee optimal performance and user safety. This rigorous approach aligns with the broader theme of expiration dates and certification, emphasizing that safety should never be compromised by neglecting routine maintenance checks.
Usage and Environmental Factors
In the modern world, understanding the usage and environmental factors that influence the longevity and performance of materials and products is crucial. Whether it's frequent use and exposure to elements, exposure to chemicals or extreme temperatures, or the storage conditions and maintenance practices employed, these factors significantly impact the overall durability and functionality of various items. Frequent use and exposure to elements such as sunlight, rain, and wind can lead to wear and tear, while exposure to chemicals or extreme temperatures can accelerate degradation. Additionally, how items are stored and maintained plays a critical role in their lifespan. By examining these key aspects, we can better predict and mitigate signs of wear and tear, ensuring that our belongings and infrastructure remain in optimal condition for longer periods. This article delves into these critical factors, providing insights into how they affect the longevity of materials and products, ultimately leading to a deeper understanding of the signs of wear and tear that arise from these influences.
Frequent Use and Exposure to Elements
Frequent use and exposure to elements significantly impact the lifespan and effectiveness of personal flotation devices (PFDs) or lifejackets. When these devices are regularly used, they are subjected to various environmental factors that can degrade their materials and compromise their performance. For instance, prolonged exposure to sunlight can cause the fabric and straps of a PFD to weaken, leading to potential tears or breaks. Similarly, repeated immersion in water, especially saltwater, can accelerate the deterioration of materials due to corrosion and chemical reactions. Additionally, frequent cleaning and drying cycles can also affect the integrity of the device, particularly if not done according to manufacturer guidelines. Moreover, physical wear and tear from frequent use can lead to visible signs of damage such as fraying, cuts, or broken buckles. These visible signs are clear indicators that the PFD may no longer provide adequate buoyancy or support in emergency situations. Furthermore, even if a PFD appears intact, internal components like foam inserts or inflatable bladders may degrade over time due to repeated compression and expansion cycles. It is crucial to inspect PFDs regularly for any signs of wear or damage. Manufacturers often provide specific guidelines on inspection and maintenance, which should be followed diligently. For example, checking for any signs of mold, mildew, or discoloration is essential as these could indicate underlying material degradation. The buoyancy of the device should also be tested periodically to ensure it still meets safety standards. Given these factors, it is generally recommended that PFDs be replaced every few years depending on usage frequency and environmental conditions. For example, a PFD used frequently in harsh marine environments may need to be replaced more often than one used sporadically in freshwater settings. Some manufacturers specify a maximum lifespan for their products, typically ranging from 5 to 10 years, after which the device should be replaced regardless of its appearance or performance. In summary, frequent use and exposure to elements necessitate regular inspections and timely replacements of PFDs to ensure they remain reliable and effective in emergency situations. Adhering to manufacturer guidelines and conducting thorough inspections are key steps in maintaining the integrity of these critical safety devices. By doing so, users can trust that their PFD will perform as intended when it matters most.
Exposure to Chemicals or Extreme Temperatures
Exposure to chemicals or extreme temperatures is a critical factor in determining the lifespan and effectiveness of a personal flotation device (PFD) or lifejacket. Prolonged exposure to harsh chemicals, such as those found in cleaning products, fuels, or industrial environments, can degrade the materials used in PFDs. These chemicals can break down the fabric, foam, or other components, compromising the buoyancy and structural integrity of the device. For instance, exposure to petroleum-based products can cause the foam in a PFD to disintegrate over time, significantly reducing its ability to provide adequate flotation. Similarly, extreme temperatures can have detrimental effects on PFDs. High temperatures can cause the materials to degrade faster, leading to cracks in the plastic components or the breakdown of synthetic fibers. Conversely, low temperatures can make materials brittle and prone to cracking. For example, leaving a PFD in direct sunlight for extended periods or storing it in freezing conditions without proper protection can accelerate wear and tear. Additionally, exposure to repeated cycles of freezing and thawing can cause internal components to become compromised, affecting the overall performance of the device. It is essential to inspect PFDs regularly for signs of chemical or temperature-related damage. Visible signs such as discoloration, cracks, or softening of materials indicate that the device may no longer be reliable. Manufacturers often provide guidelines on how to store and maintain PFDs to minimize exposure risks. Following these guidelines and conducting regular inspections are crucial steps in ensuring that a PFD remains in good condition and continues to provide the necessary safety protection. If any damage is detected, it is imperative to replace the PFD immediately to avoid any potential risks during use. By understanding and mitigating these environmental factors, users can extend the lifespan of their PFDs and ensure they remain effective in emergency situations. Therefore, when considering whether a PFD or lifejacket must be replaced, it is vital to take into account any exposure to chemicals or extreme temperatures as part of the overall assessment.
Storage Conditions and Maintenance Practices
When considering the longevity and effectiveness of a personal flotation device (PFD) or lifejacket, it is crucial to adhere to stringent storage conditions and maintenance practices. Proper storage and regular maintenance are pivotal in ensuring that these lifesaving devices remain in optimal condition, ready for use when needed. Storage conditions should be dry, cool, and away from direct sunlight, which can degrade the materials over time. Avoid exposing PFDs to extreme temperatures or moisture, as this can compromise the integrity of the fabric, foam, or other components. Additionally, PFDs should be stored in a clean environment, free from contaminants such as oil, grease, or chemicals that could damage the materials. Regular inspections are a cornerstone of maintenance practices. Users should check for signs of wear and tear, such as cracks in the plastic components, fraying of straps, or degradation of the buoyant material. Any visible damage necessitates immediate replacement to ensure safety. Furthermore, it is essential to follow the manufacturer's guidelines for cleaning and drying PFDs after use. This includes rinsing with fresh water to remove salt or other substances that could cause corrosion or damage. The frequency of inspections also plays a critical role. PFDs should be inspected before each use and at least annually if they are not frequently used. This involves checking all components, including buckles, zippers, and straps, to ensure they are functioning correctly. The buoyancy of the device should also be tested periodically according to the manufacturer's instructions. Moreover, environmental factors significantly impact the lifespan of a PFD. Exposure to harsh marine environments, such as saltwater or high UV radiation, can accelerate degradation. Therefore, users must consider these factors when determining the replacement schedule for their PFDs. For instance, devices used in saltwater environments may need more frequent inspections and potentially shorter lifespans compared to those used in freshwater settings. In summary, adhering to proper storage conditions and rigorous maintenance practices is essential for extending the life of a PFD while ensuring its reliability in emergency situations. By storing devices under optimal conditions and conducting regular inspections, users can help prevent premature degradation and ensure their PFDs remain effective when needed most. This proactive approach not only enhances safety but also aligns with regulatory requirements and manufacturer recommendations, ultimately safeguarding lives on the water.