When Did Whmis Come Into Effect

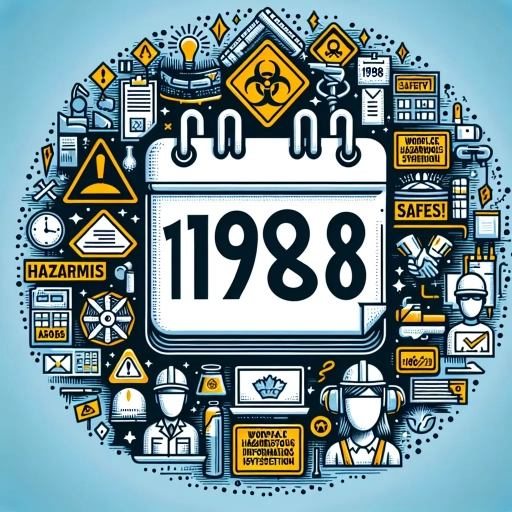
The Workplace Hazardous Materials Information System (WHMIS) is a cornerstone of occupational health and safety in Canada, designed to protect workers from the dangers of hazardous materials. Since its inception, WHMIS has undergone significant transformations to ensure it remains effective and relevant. This article delves into the critical aspects of WHMIS, starting with an **Introduction to WHMIS**, where we explore the fundamental principles and objectives of this system. We then examine the **Implementation Timeline of WHMIS**, detailing the key milestones and phases that have shaped its evolution. Finally, we discuss the **Impact and Evolution of WHMIS**, highlighting how it has influenced workplace safety and adapted to new challenges over time. By understanding these elements, readers will gain a comprehensive insight into the history, development, and ongoing importance of WHMIS in safeguarding Canadian workplaces. Let us begin by exploring the foundational aspects of WHMIS in our **Introduction to WHMIS**.
Introduction to WHMIS
In the realm of workplace safety, few regulations have had as profound an impact as the Workplace Hazardous Materials Information System (WHMIS). This comprehensive system is designed to ensure that workers are fully informed about the hazards associated with the chemicals they use, thereby reducing the risk of injury and illness. To understand WHMIS fully, it is essential to delve into its **Definition and Purpose**, which outlines the core objectives and mechanisms of the system. Additionally, examining the **Historical Context Leading to WHMIS** provides valuable insights into the legislative and societal factors that drove its creation. Finally, understanding the **Key Components of WHMIS** is crucial for implementing and adhering to its guidelines effectively. By exploring these aspects, we can gain a thorough appreciation for how WHMIS functions and why it remains a cornerstone of occupational health and safety. This article will introduce you to WHMIS, providing a detailed overview of its definition, historical context, and key components, ensuring you are well-equipped to navigate this critical aspect of workplace safety. **Introduction to WHMIS**.
Definition and Purpose of WHMIS
**Definition and Purpose of WHMIS** The Workplace Hazardous Materials Information System (WHMIS) is a comprehensive safety standard designed to protect workers from the hazards associated with hazardous materials in the workplace. Implemented to ensure that workers are aware of the potential dangers posed by chemicals and other hazardous substances, WHMIS mandates the proper classification, labeling, and communication of these hazards. The system is built around three key components: classification, labeling, and Safety Data Sheets (SDSs), along with worker training and education. **Classification** involves categorizing hazardous products based on their physical and health hazards, as well as environmental hazards. This classification is crucial for identifying the risks associated with each substance. **Labeling** requires that all hazardous products be marked with standardized labels that include pictograms, hazard statements, and precautionary statements to alert workers to potential dangers. **Safety Data Sheets (SDSs)** provide detailed information about the safe handling, use, storage, and emergency procedures for each hazardous product. These documents are essential for ensuring that workers have access to critical safety information. The primary purpose of WHMIS is to provide workers with the knowledge and tools necessary to safely handle hazardous materials. By standardizing the way hazards are communicated, WHMIS helps prevent injuries, illnesses, and fatalities resulting from exposure to hazardous substances. It also promotes a culture of safety within workplaces by ensuring that all stakeholders—employers, workers, and suppliers—are informed about the risks and necessary precautions. Additionally, WHMIS aligns Canada with international standards for chemical safety, facilitating trade and ensuring consistency in safety practices across different jurisdictions. Overall, WHMIS serves as a cornerstone of occupational health and safety in Canada, empowering workers to make informed decisions about their safety and the safety of their colleagues. Its implementation has significantly reduced workplace accidents and health issues related to hazardous materials, making it an indispensable component of workplace safety protocols. As part of an integrated approach to occupational health and safety, WHMIS continues to play a vital role in protecting workers and promoting a safe working environment.
Historical Context Leading to WHMIS
The historical context leading to the implementation of the Workplace Hazardous Materials Information System (WHMIS) is rooted in a series of legislative and regulatory developments aimed at enhancing workplace safety in Canada. Prior to WHMIS, the handling and use of hazardous materials in Canadian workplaces were governed by a patchwork of provincial and federal regulations, which often lacked uniformity and comprehensive coverage. The 1970s and 1980s saw a significant increase in public awareness about the dangers of chemical substances, driven by high-profile industrial accidents and growing environmental concerns. This heightened awareness prompted calls for more stringent safety standards. In response, the Canadian government initiated a collaborative effort involving federal, provincial, and territorial authorities to develop a standardized system for managing hazardous materials. This collaboration led to the establishment of WHMIS in 1988, with the goal of providing workers with essential information about the hazards associated with the chemicals they handle. WHMIS was designed to ensure that all workers have access to critical safety data sheets (SDSs), labels, and training programs, thereby reducing the risk of chemical-related injuries and illnesses. The implementation of WHMIS was also influenced by international standards and best practices. The United Nations' Globally Harmonized System of Classification and Labelling of Chemicals (GHS) played a pivotal role in shaping WHMIS. Canada's adoption of GHS principles ensured that WHMIS aligned with global standards, facilitating trade and enhancing safety across borders. The integration of GHS into WHMIS has continued to evolve, with updates in 2015 aligning Canadian regulations more closely with international norms. Throughout its development, WHMIS has been supported by robust legislative frameworks. The Hazardous Products Act and the Controlled Products Regulations provided the legal foundation for WHMIS, mandating that suppliers of hazardous products provide SDSs and labels that meet specific standards. These regulations have been periodically updated to reflect new scientific knowledge and changing workplace conditions. In summary, the historical context leading to WHMIS reflects a concerted effort by Canadian authorities to address growing concerns about workplace safety and environmental protection. By standardizing the management of hazardous materials through WHMIS, Canada has significantly improved occupational health and safety, aligning with international best practices while ensuring a safer working environment for all Canadians. This foundational system continues to evolve, adapting to new challenges and advancements in chemical safety.
Key Components of WHMIS
The Workplace Hazardous Materials Information System (WHMIS) is a comprehensive safety standard designed to protect workers from the hazards of chemicals in the workplace. Key components of WHMIS include **Classification**, **Labels**, **Safety Data Sheets (SDS)**, and **Training**. **Classification** is the foundation of WHMIS, where hazardous products are categorized based on their physical and health hazards. This process ensures that products are identified and managed according to their specific risks. The classification criteria are aligned with the Globally Harmonized System of Classification and Labelling of Chemicals (GHS), enhancing international consistency and safety. **Labels** provide critical information about the hazards of a product and are required on all containers of hazardous materials. These labels must include a product identifier, hazard statements, precautionary statements, and pictograms that visually represent the hazards. This visual and textual information helps workers quickly identify potential dangers and take necessary precautions. **Safety Data Sheets (SDS)** are detailed documents that provide comprehensive information about a hazardous product. Each SDS includes sections on product identification, hazard identification, composition, first aid measures, fire-fighting measures, accidental release measures, handling and storage, exposure controls/personal protection, physical and chemical properties, stability and reactivity, toxicological information, ecological information, disposal considerations, transport information, regulatory information, and other relevant data. This extensive documentation ensures that workers have access to all necessary information to safely handle and manage hazardous materials. **Training** is an essential component of WHMIS, as it equips workers with the knowledge and skills needed to handle hazardous materials safely. Employers are required to provide education and training programs that cover the WHMIS system, the hazards of the products used in the workplace, and the procedures for safe handling, use, storage, and disposal of these products. Effective training also includes how to read and understand labels and SDSs, which is crucial for maintaining a safe working environment. By integrating these key components—classification, labels, SDSs, and training—WHMIS ensures that workers are well-informed and equipped to manage chemical hazards effectively. This holistic approach to workplace safety has significantly reduced the risks associated with hazardous materials since its implementation. Understanding these components is vital for any organization looking to comply with WHMIS regulations and maintain a safe and healthy work environment.
Implementation Timeline of WHMIS
The Implementation Timeline of the Workplace Hazardous Materials Information System (WHMIS) is a critical component in understanding the evolution and enforcement of this vital safety standard. WHMIS, designed to protect workers from hazardous materials, has undergone a meticulous process from its inception to full implementation. This article delves into the key phases of WHMIS's development, starting with the **Initial Legislation and Drafting Phase**, where the foundational framework was established. It then transitions to the **Finalization and Approval Process**, highlighting the collaborative efforts and regulatory approvals necessary for its adoption. Finally, it concludes with the **Official Date of Implementation**, marking the point at which WHMIS became a mandatory standard across Canadian workplaces. By examining these stages, readers will gain a comprehensive understanding of how WHMIS came to be an integral part of workplace safety protocols. This detailed exploration sets the stage for a deeper **Introduction to WHMIS**, providing context and clarity on its significance and application.
Initial Legislation and Drafting Phase
The Initial Legislation and Drafting Phase of the Workplace Hazardous Materials Information System (WHMIS) marks a pivotal period in the development of this critical safety standard. This phase, which began in the late 1970s, was characterized by extensive collaboration between government agencies, industry stakeholders, and labor organizations. The need for a comprehensive system to manage hazardous materials in the workplace became increasingly evident as workplace injuries and illnesses related to chemical exposure continued to rise. In response, the Canadian government initiated a thorough review of existing regulations and best practices, leading to the formation of a national task force dedicated to developing WHMIS. This task force, comprising representatives from Health Canada, Environment and Climate Change Canada, and the Canadian Standards Association (CSA), among others, worked diligently to draft legislation that would ensure the safe handling, use, and disposal of hazardous materials. Key components of this phase included the establishment of clear definitions for hazardous materials, the development of standardized labeling and safety data sheets (SDS), and the creation of training requirements for workers. The drafting process involved rigorous consultations with various stakeholders to ensure that the legislation was both effective and feasible to implement across diverse industries. One of the significant milestones during this phase was the publication of the first draft of the WHMIS regulations in 1985. This draft outlined the framework for classifying hazardous materials, the content and format of SDSs, and the requirements for workplace labeling and training programs. Following extensive feedback and revisions, the final version of the WHMIS legislation was enacted in 1988, setting the stage for its implementation across Canada. The successful completion of this initial legislation and drafting phase laid the groundwork for WHMIS to become a cornerstone of workplace safety in Canada, ensuring that workers have access to critical information about the hazards they encounter on the job. This foundational work has since been built upon through subsequent updates and amendments, reflecting ongoing efforts to enhance workplace safety and align with evolving international standards. The meticulous planning and coordination during this phase were instrumental in establishing WHMIS as a model for hazardous materials management that has been adopted by other countries around the world.
Finalization and Approval Process
The finalization and approval process is a critical phase in the implementation timeline of the Workplace Hazardous Materials Information System (WHMIS). This process ensures that all necessary steps are taken to align with regulatory requirements, industry standards, and stakeholder expectations. Following the development of WHMIS guidelines and training materials, the finalization stage involves a thorough review by subject matter experts, regulatory bodies, and key stakeholders. This review aims to verify that the information is accurate, comprehensive, and compliant with federal and provincial regulations. Once the review is complete, the approval process commences. Here, regulatory authorities such as Health Canada and provincial labor departments scrutinize the materials to ensure they meet all legal and safety standards. This includes verifying that hazard classifications, safety data sheets (SDS), and labels conform to the Globally Harmonized System of Classification and Labelling of Chemicals (GHS) standards adopted by WHMIS. During this phase, feedback from various stakeholders, including employers, workers, and industry associations, is also considered to ensure practical applicability and effectiveness. The approval process may involve multiple iterations to address any concerns or discrepancies identified during the review. Upon receiving final approval, the WHMIS implementation team can proceed with the dissemination of approved materials and training programs across workplaces. This includes updating existing policies, procedures, and training modules to reflect the new standards. Employers are then required to ensure that all employees receive the necessary training on the new WHMIS standards within a specified timeframe. The finalization and approval process is not just about compliance; it also ensures that workers have access to reliable information to handle hazardous materials safely. By engaging in a rigorous review and approval process, WHMIS implementation can effectively reduce workplace hazards and promote a safer working environment. This meticulous approach underscores the commitment to protecting worker health and safety, which is at the core of WHMIS's mission since its inception in 1988 and subsequent updates to align with GHS standards. The thoroughness of this process guarantees that WHMIS remains an effective tool in managing workplace hazards, thereby enhancing overall occupational health and safety in Canada.
Official Date of Implementation
The Official Date of Implementation for the Workplace Hazardous Materials Information System (WHMIS) marks a significant milestone in the history of occupational health and safety in Canada. WHMIS, which came into effect on October 31, 1988, was designed to provide workers with critical information about the hazardous materials they handle, ensuring a safer working environment. This comprehensive system was the result of collaborative efforts between the federal, provincial, and territorial governments, along with input from various stakeholders including employers, workers, and suppliers. The implementation date was crucial as it signaled the beginning of a new era in chemical safety. Prior to WHMIS, there was no standardized system for communicating hazards associated with workplace chemicals, leading to numerous accidents and health issues. The introduction of WHMIS mandated that suppliers of hazardous products provide Material Safety Data Sheets (MSDS) and labels that clearly identify the hazards and necessary precautions. Employers were also required to educate their workers on how to safely handle these substances through training programs. The transition to WHMIS was not immediate; it involved a phased implementation to allow suppliers and employers sufficient time to adapt. This included updating product labels, developing MSDS, and conducting extensive training for workers. The phased approach ensured that the transition was smooth and that all stakeholders were adequately prepared to comply with the new regulations. Since its implementation, WHMIS has undergone several updates and revisions to align with international standards and address emerging issues. For instance, the transition to WHMIS 2015, which aligned with the Globally Harmonized System of Classification and Labelling of Chemicals (GHS), further enhanced the system's effectiveness by introducing new hazard classification criteria and standardized label formats. In summary, the official date of implementation for WHMIS on October 31, 1988, was a pivotal moment in Canadian occupational safety history. It marked the beginning of a structured approach to managing hazardous materials in the workplace, significantly reducing risks and improving worker safety. The ongoing evolution of WHMIS continues to reflect its importance as a cornerstone of workplace safety regulations in Canada.
Impact and Evolution of WHMIS
The Workplace Hazardous Materials Information System (WHMIS) has been a cornerstone of workplace safety in Canada since its inception. Over the years, WHMIS has undergone significant evolution, reflecting advancements in scientific understanding and regulatory standards. This article delves into the impact and evolution of WHMIS, exploring its immediate effects on workplace safety, public reception and compliance, and subsequent updates and revisions. By examining these facets, we can better understand how WHMIS has transformed the way hazardous materials are handled and communicated about in the workplace. The immediate effects on workplace safety highlight the system's role in reducing accidents and improving worker health. Public reception and compliance reveal the challenges and successes in implementing WHMIS across various industries. Finally, subsequent updates and revisions demonstrate the ongoing efforts to align WHMIS with global standards and address emerging hazards. Transitioning seamlessly into an introduction to WHMIS, this article provides a comprehensive overview of the system's history, principles, and ongoing relevance in ensuring a safer work environment for all Canadians.
Immediate Effects on Workplace Safety
The immediate effects on workplace safety following the implementation of the Workplace Hazardous Materials Information System (WHMIS) have been profound and multifaceted. Since its inception in 1988, WHMIS has revolutionized how hazardous materials are handled, stored, and communicated about in Canadian workplaces. One of the most significant impacts has been the standardization of hazard communication. Prior to WHMIS, there was no uniform system for labeling and providing safety data sheets (SDSs) for hazardous substances, leading to confusion and increased risk of accidents. With WHMIS, employers are now mandated to ensure that all hazardous materials are properly labeled with standardized symbols and that SDSs are readily available to workers. This has significantly enhanced workers' ability to identify potential hazards and take necessary precautions. Another critical effect of WHMIS has been the enhancement of worker training programs. Employers are required to educate employees on the safe handling, use, storage, and disposal of hazardous materials. This training includes understanding the information provided on labels and SDSs, recognizing hazards, and knowing how to respond in emergency situations. As a result, workers are better equipped to manage risks associated with their jobs, leading to a reduction in workplace injuries and illnesses. The implementation of WHMIS has also fostered a culture of safety within organizations. By making hazard information more accessible and understandable, WHMIS encourages a proactive approach to safety management. Employers are compelled to conduct regular risk assessments and implement control measures to mitigate hazards. This proactive stance has led to improved overall safety performance across various industries. Moreover, WHMIS has facilitated compliance with other health and safety regulations. The system aligns with broader occupational health and safety standards, ensuring that workplaces adhere to a comprehensive framework for managing hazards. This alignment helps in streamlining safety protocols and reducing the administrative burden on employers while maintaining high safety standards. In addition, WHMIS has promoted a collaborative environment between employers, employees, and regulatory bodies. The system encourages open communication about hazards and fosters a shared responsibility for workplace safety. This collaborative approach has led to better reporting of incidents and near-misses, which in turn helps in identifying and addressing potential hazards before they result in serious consequences. Overall, the immediate effects of WHMIS on workplace safety have been transformative. By standardizing hazard communication, enhancing worker training, promoting a safety culture, facilitating regulatory compliance, and fostering collaboration, WHMIS has significantly reduced workplace risks and improved the overall safety landscape in Canada. As WHMIS continues to evolve with updates such as GHS (Globally Harmonized System of Classification and Labelling of Chemicals), its impact on workplace safety is expected to remain robust and beneficial.
Public Reception and Compliance
Public reception and compliance have been pivotal in the impact and evolution of the Workplace Hazardous Materials Information System (WHMIS). Since its inception in 1988, WHMIS has undergone significant transformations, largely driven by public feedback and the need for enhanced compliance. Initially, the system faced challenges in terms of awareness and understanding among workers and employers. However, through continuous education and training programs, there has been a marked improvement in compliance rates. The introduction of WHMIS 2015, which aligned Canada's standards with the Globally Harmonized System of Classification and Labelling of Chemicals (GHS), further streamlined the process, making it easier for workers to identify and manage hazardous materials. Public reception has been instrumental in shaping these changes. Feedback from various stakeholders, including workers, employers, and regulatory bodies, has led to refinements in the system. For instance, the inclusion of pictograms and standardized labels has significantly improved the recognition and understanding of hazards. This shift has not only enhanced workplace safety but also facilitated better compliance with regulatory requirements. Employers have found it more manageable to implement WHMIS protocols, leading to a reduction in workplace injuries and illnesses related to hazardous materials. Moreover, technological advancements have played a crucial role in enhancing compliance. Digital platforms and mobile applications now provide easy access to safety data sheets (SDSs) and training resources, making it simpler for workers to stay informed. This digital integration has also enabled real-time updates and notifications, ensuring that workplaces remain compliant with the latest regulations. The collaborative effort between government agencies, industry leaders, and public advocacy groups has been essential in driving these improvements. The evolution of WHMIS is a testament to the power of public engagement and the importance of continuous improvement. As new challenges arise, such as the introduction of new chemicals or changes in workplace environments, the system remains adaptable. This adaptability ensures that WHMIS continues to serve its primary purpose: protecting the health and safety of Canadian workers. By fostering a culture of compliance and ongoing education, WHMIS has become a cornerstone of occupational health and safety in Canada, reflecting a commitment to safeguarding the well-being of all workers who handle hazardous materials.
Subsequent Updates and Revisions
The evolution of the Workplace Hazardous Materials Information System (WHMIS) has been marked by significant subsequent updates and revisions, reflecting ongoing efforts to enhance worker safety and align with international standards. Since its initial implementation in 1988, WHMIS has undergone several key transformations. One of the most substantial updates was the transition to WHMIS 2015, which aligned Canada's system with the Globally Harmonized System of Classification and Labelling of Chemicals (GHS). This change introduced new classification criteria, standardized label elements, and safety data sheet formats, ensuring greater consistency and clarity in hazard communication. The GHS alignment also facilitated international trade by harmonizing chemical classification and labelling practices across borders. In addition to the GHS alignment, subsequent revisions have focused on improving compliance and enforcement. For instance, Health Canada has issued various updates to the Hazardous Products Regulations (HPR) and the Hazardous Products Act (HPA), which govern WHMIS. These updates have clarified requirements for supplier labels, safety data sheets, and workplace training programs. Furthermore, provinces and territories have also played a crucial role in enforcing WHMIS through their occupational health and safety regulations, ensuring that employers adhere to the updated standards. Another critical aspect of WHMIS revisions involves ongoing stakeholder engagement and feedback. Health Canada regularly consults with industry stakeholders, labour organizations, and other interested parties to gather insights on the effectiveness of WHMIS and identify areas for improvement. This collaborative approach has led to targeted amendments that address specific challenges and enhance the overall efficacy of the system. Moreover, technological advancements have been integrated into WHMIS updates to leverage digital tools for better hazard communication. For example, electronic safety data sheets (e-SDS) have become more prevalent, allowing for quicker access to critical information and reducing the burden on employers to maintain physical records. This shift towards digital solutions aligns with broader trends in occupational health and safety, emphasizing the importance of accessible and up-to-date information in preventing workplace injuries and illnesses. In conclusion, the subsequent updates and revisions to WHMIS reflect a commitment to continuous improvement in workplace safety. By aligning with international standards, enhancing compliance mechanisms, engaging stakeholders, and embracing technological innovations, WHMIS remains a robust framework for protecting workers from hazardous materials. These updates underscore the dynamic nature of WHMIS as it evolves to meet emerging challenges and ensure a safer working environment for all Canadians.