When Must A Pfd Be Replaced

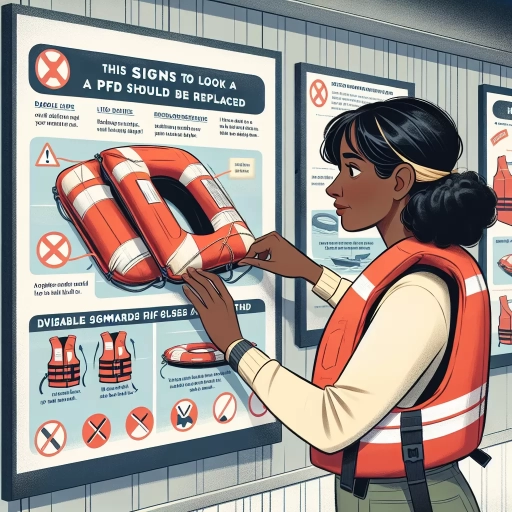
Personal Flotation Devices (PFDs) are crucial safety equipment for water activities, ensuring the well-being of individuals in various aquatic environments. However, their effectiveness is not indefinite; PFDs must be replaced under specific conditions to maintain their life-saving capabilities. This article delves into the critical factors that determine when a PFD needs to be replaced, focusing on three key areas: signs of wear and tear, expiration dates and manufacturer guidelines, and regulatory and safety standards. Understanding these elements is essential for ensuring that your PFD remains reliable and compliant with safety regulations. By examining the visible signs of wear and tear, adhering to expiration dates and manufacturer guidelines, and complying with regulatory and safety standards, you can ensure your PFD continues to provide the necessary protection. Let's begin by exploring the first of these critical factors: **Signs of Wear and Tear**.
Signs of Wear and Tear
When it comes to maintaining and extending the life of your belongings, whether they are everyday items, machinery, or even personal gear, recognizing signs of wear and tear is crucial. Over time, these signs can manifest in various ways, each indicating a different level of deterioration. For instance, visible damage to the fabric of an item can be a clear indicator that it needs attention or replacement. Similarly, a loss of buoyancy in flotation devices or other equipment signals that their functionality is compromised. Additionally, broken or malfunctioning components can render an item useless and pose safety risks if not addressed promptly. Understanding these signs is essential for preventive maintenance, ensuring safety, and optimizing performance. In this article, we will delve into these key indicators of wear and tear, providing insights into how to identify and address them effectively. By recognizing these signs, you can take proactive steps to maintain your belongings and prevent further damage. Here, we explore the critical aspects of **Signs of Wear and Tear**.
Visible Damage to the Fabric
Visible damage to the fabric is a critical indicator that a Personal Flotation Device (PFD) may need to be replaced. Over time, exposure to various environmental factors such as sunlight, saltwater, and mechanical stress can lead to noticeable deterioration of the material. One of the most common signs of visible damage is the appearance of cracks or tears in the fabric. These can range from small fissures to larger rips that compromise the structural integrity of the PFD. Additionally, discoloration or fading of the material can signify degradation of its UV-resistant properties, which are crucial for maintaining the buoyancy and durability of the device. Another key aspect to inspect is the condition of seams and stitching. If threads are frayed or stitches are coming undone, it indicates a weakening of the PFD's overall structure. Similarly, any signs of delamination between layers of fabric or foam can significantly reduce the buoyancy and effectiveness of the device. It is also important to check for any signs of chemical damage, such as oil or fuel stains, which can weaken synthetic materials like nylon or polyester. Furthermore, visible signs of wear on buckles, straps, and other hardware components should not be overlooked. Rusty or corroded metal parts can fail under stress, while worn-out plastic components may break easily. The condition of these elements is vital because they are often the first points of failure in a PFD. Regular inspection for these visible signs of damage is essential to ensure that a PFD remains safe and functional. Manufacturers typically provide guidelines on what constitutes acceptable wear and tear, but it is always better to err on the side of caution when it comes to safety equipment. If any visible damage is detected, it is advisable to replace the PFD immediately to avoid potential risks during use. By paying close attention to these indicators, users can help prevent accidents and ensure their safety while engaging in water activities.
Loss of Buoyancy
**Loss of Buoyancy** One of the most critical signs indicating that a Personal Flotation Device (PFD) needs to be replaced is the loss of buoyancy. This can occur due to various factors, including wear and tear, improper storage, or exposure to harsh environmental conditions. Over time, the materials used in PFDs can degrade, leading to a reduction in their ability to provide adequate flotation. For instance, foam-filled PFDs may lose buoyancy if the foam becomes waterlogged or if it breaks down due to chemical reactions with seawater or other substances. Similarly, inflatable PFDs can suffer from leaks or damage to their bladders, which compromises their buoyant capacity. The loss of buoyancy is particularly dangerous because it can happen gradually and may not be immediately noticeable. Users might not realize their PFD is no longer functioning properly until it is too late. Regular inspections are crucial to detect any signs of degradation. Check for visible signs such as cracks, tears, or waterlogging in foam-filled models. For inflatable PFDs, perform routine inflation tests to ensure they hold air as expected. Additionally, look for any signs of corrosion on metal components or deterioration of fabric and straps. It is also important to consider the usage history of the PFD. If it has been involved in a rescue operation or exposed to extreme conditions like high temperatures, intense sunlight, or chemical spills, it may have suffered unseen damage that affects its buoyancy. Manufacturers often provide guidelines on the lifespan and maintenance requirements for their products; adhering to these recommendations can help prevent unexpected failures. In summary, loss of buoyancy is a critical indicator that a PFD needs replacement. It can result from material degradation over time or due to specific incidents involving harsh conditions. Regular inspections and adherence to manufacturer guidelines are essential to ensure that your PFD remains reliable and effective in emergency situations. Ignoring these signs can lead to serious safety risks, making it imperative to replace any PFD showing signs of reduced buoyancy promptly.
Broken or Malfunctioning Components
When assessing the need to replace a Personal Flotation Device (PFD), one critical aspect to consider is the presence of broken or malfunctioning components. These defects can significantly compromise the safety and effectiveness of the PFD, making it imperative to identify and address them promptly. Broken or malfunctioning components can manifest in various ways, such as cracks in the plastic or fiberglass parts, frayed or severed straps, and damaged buckles or zippers. Additionally, inflatable PFDs may have issues with their inflation mechanisms, such as faulty CO2 cartridges or leaking bladders, which could fail to deploy properly in an emergency situation. Similarly, foam PFDs might show signs of waterlogging or compression, reducing their buoyancy and overall performance. The importance of inspecting these components cannot be overstated. For instance, a cracked plastic part may seem minor but could lead to a catastrophic failure under stress. Similarly, a frayed strap might appear to be holding together but could snap at the worst possible moment. Regular inspections are crucial to catch these issues early on. Users should meticulously check each component for any signs of wear and tear, ensuring that all parts are functioning correctly and securely attached. If any defects are found, the PFD should be replaced immediately to avoid any risk of failure when it is needed most. Moreover, it is essential to follow the manufacturer's guidelines for maintenance and inspection. Many manufacturers provide detailed instructions on how to inspect their products and what signs to look for that indicate a need for replacement. Adhering to these guidelines helps ensure that the PFD remains in good working condition and continues to provide the necessary safety protection. In some cases, even if no visible defects are present, certain components may have a limited lifespan and need to be replaced periodically as part of routine maintenance. In conclusion, identifying and addressing broken or malfunctioning components is a vital step in determining whether a PFD needs to be replaced. By conducting thorough inspections and adhering to manufacturer recommendations, users can ensure their PFDs remain reliable and effective. Ignoring these signs of wear and tear could lead to serious safety risks, making it crucial to prioritize regular checks and timely replacements when necessary. This proactive approach not only enhances personal safety but also contributes to a culture of safety and responsibility among water users.
Expiration Dates and Manufacturer Guidelines
Expiration dates and manufacturer guidelines are crucial elements in ensuring the safety, quality, and effectiveness of various products, particularly those related to personal protective equipment (PPE) and food items. Understanding these concepts is essential for consumers to make informed decisions about the products they use. This article delves into three key aspects: **Checking the Expiration Date**, which highlights the importance of verifying the shelf life of products; **Following Manufacturer Recommendations**, which emphasizes adhering to guidelines provided by manufacturers for optimal use; and **Understanding Different Types of PFDs (Product Freshness Dates)**, which explains the various types of expiration dates and their implications. By grasping these concepts, individuals can better navigate the complexities of product longevity and safety. This knowledge is particularly relevant when transitioning to discussions on **Signs of Wear and Tear**, as it helps in distinguishing between normal degradation and critical safety issues, ensuring that products are used within their safe and effective lifespan.
Checking the Expiration Date
When it comes to ensuring the safety and efficacy of personal protective equipment (PPE), particularly personal flotation devices (PFDs), checking the expiration date is a critical step that cannot be overlooked. Expiration dates are not merely arbitrary markers but are based on rigorous testing and guidelines set by manufacturers to guarantee that the PFD will perform as intended in emergency situations. These dates reflect the period during which the device is expected to maintain its structural integrity, buoyancy, and overall functionality. Manufacturers conduct extensive research and testing to determine the lifespan of their PFDs, taking into account factors such as material degradation, exposure to environmental elements, and wear and tear from use. The expiration date serves as a clear indicator of when a PFD may no longer meet safety standards, even if it appears to be in good condition. Ignoring this date could lead to a false sense of security, potentially endangering lives in situations where the PFD is relied upon for survival. Moreover, regulatory bodies and industry standards often mandate compliance with these expiration dates to ensure uniform safety protocols across different sectors. For instance, the U.S. Coast Guard and other maritime authorities have strict guidelines regarding the inspection and replacement of PFDs, emphasizing the importance of adhering to manufacturer-specified expiration dates. In practice, checking the expiration date involves a simple yet meticulous process. Users should locate the date printed on the PFD, usually found on a label or stamped directly onto the device. This date may be represented in various formats but typically includes the month and year of expiration. It is also advisable to inspect the PFD for any visible signs of damage or deterioration, such as cracks, tears, or discoloration, which could necessitate replacement regardless of the expiration date. By diligently checking and adhering to the expiration dates of PFDs, individuals can significantly reduce the risk of equipment failure during critical moments. This proactive approach not only aligns with manufacturer guidelines but also contributes to a broader culture of safety and responsibility. In essence, the expiration date on a PFD is more than just a piece of information; it is a vital safeguard that ensures the device remains reliable and effective when it matters most.
Following Manufacturer Recommendations
Following manufacturer recommendations is crucial when it comes to ensuring the safety and efficacy of personal flotation devices (PFDs). These guidelines are meticulously crafted based on rigorous testing, material analysis, and real-world performance data. By adhering to these recommendations, users can maximize the lifespan of their PFDs while maintaining their reliability in critical situations. Manufacturer guidelines typically include detailed instructions on usage, maintenance, storage, and inspection protocols. For instance, they may specify how often a PFD should be inspected for signs of wear and tear, such as cracks in the plastic or fraying of the straps. They also provide guidance on proper cleaning and drying techniques to prevent damage from exposure to harsh chemicals or excessive moisture. Additionally, manufacturers often outline specific conditions under which a PFD should be replaced, such as after a significant impact or if certain components show signs of degradation. Ignoring these recommendations can lead to compromised performance and potentially life-threatening consequences. For example, a PFD that has been improperly stored or neglected during maintenance may fail to inflate correctly in an emergency, putting the wearer at risk. Furthermore, many manufacturers offer warranties that are contingent upon adherence to their guidelines, providing an added incentive for users to follow best practices. By prioritizing these recommendations, individuals can ensure that their PFDs remain in optimal condition, thereby enhancing their overall safety on the water. In essence, following manufacturer guidelines is not just a suggestion but a necessity for anyone relying on a PFD for protection and survival. This proactive approach not only extends the life of the device but also guarantees that it will perform as intended when it matters most. Therefore, it is imperative to treat manufacturer recommendations with the seriousness they deserve and integrate them into regular PFD maintenance routines to ensure continuous reliability and safety.
Understanding Different Types of PFDs
Understanding different types of Personal Flotation Devices (PFDs) is crucial for ensuring safety on the water. PFDs are designed to keep individuals afloat in emergency situations, but their effectiveness depends on the type and condition of the device. There are several categories of PFDs, each with specific uses and characteristics. **Type I PFDs**, also known as offshore life jackets, are the most buoyant and are designed for use in open waters where rescue may be delayed. They are capable of turning an unconscious person face-up and are typically used by commercial vessels and in situations where the wearer may be exposed to rough seas. **Type II PFDs**, or near-shore buoyant vests, are less bulky than Type I but still provide good flotation. They are suitable for calm waters and are often used by recreational boaters. However, they may not turn an unconscious person face-up as reliably as Type I. **Type III PFDs**, or flotation aids, offer the most comfort and mobility while still providing adequate buoyancy. These are commonly used for water sports and activities where the wearer is likely to be conscious and able to help themselves stay afloat. **Type IV PFDs**, or throwable devices, include items like life rings and seat cushions. These are designed to be thrown to someone in distress rather than worn. They are typically used on boats where there is a high likelihood of quick rescue. **Type V PFDs**, or special-use devices, are designed for specific activities such as kayaking, sailing, or fishing. These often combine elements from other types but are tailored to meet the unique needs of their intended use. Regardless of the type, all PFDs must be inspected regularly to ensure they remain in good condition. This includes checking for signs of wear, damage, or degradation that could compromise their buoyancy. Following manufacturer guidelines and adhering to expiration dates is essential; expired or damaged PFDs should be replaced immediately to maintain their lifesaving capabilities. Proper maintenance and adherence to these guidelines can significantly enhance water safety and reduce the risk of accidents. By understanding the different types of PFDs and their appropriate uses, individuals can make informed decisions about which device best suits their needs, thereby enhancing their overall safety on the water.
Regulatory and Safety Standards
In today's complex and interconnected world, adherence to regulatory and safety standards is paramount for ensuring the well-being of individuals, the integrity of operations, and the sustainability of businesses. These standards serve as the backbone of safe and compliant practices, guiding organizations through a myriad of local and international regulations. Compliance with these regulations is not merely a legal necessity but a moral obligation, as it directly impacts public health, environmental safety, and economic stability. Meeting specific safety standards is another critical aspect, as it ensures that products, services, and environments are free from hazards and risks. Regular inspection requirements further reinforce these standards by providing ongoing monitoring and enforcement mechanisms. By understanding and adhering to these regulatory and safety standards, organizations can mitigate risks, enhance trust, and maintain operational excellence. However, even with stringent standards in place, signs of wear and tear can still emerge, highlighting the need for continuous vigilance and proactive maintenance to prevent potential issues. This article delves into the intricacies of regulatory and safety standards, exploring their importance and implications in depth.
Compliance with Local and International Regulations
Compliance with local and international regulations is a cornerstone of ensuring safety and adherence to standards, particularly in the context of Personal Flotation Devices (PFDs). Regulatory bodies such as the U.S. Coast Guard, Transport Canada, and the International Maritime Organization (IMO) set stringent guidelines to guarantee that PFDs meet specific safety criteria. These regulations dictate various aspects including design, material, buoyancy, and testing protocols to ensure that PFDs can effectively save lives in emergency situations. For instance, the U.S. Coast Guard mandates that PFDs must be Coast Guard-approved and meet specific performance standards, such as providing a minimum of 22.5 pounds of buoyancy for adult life jackets. Similarly, international standards like those set by the IMO require PFDs to be durable, easy to use, and capable of keeping a person afloat with their head above water. Regular inspections and maintenance are crucial to ensure ongoing compliance. PFDs must be checked for signs of wear, damage, or degradation that could compromise their effectiveness. This includes examining the fabric for tears or holes, ensuring that all straps and buckles are intact and functional, and verifying that the buoyant material has not been compromised. Additionally, many regulations specify the frequency of inspections and the criteria for when a PFD must be replaced. For example, if a PFD shows significant signs of wear or has been involved in a rescue operation, it may need to be replaced immediately to maintain compliance and ensure safety. Moreover, compliance extends beyond the physical condition of the PFD; it also involves proper usage and training. Users must be educated on how to correctly don and use their PFDs, as well as understand the limitations and capabilities of these devices. Training programs often include simulations and drills to prepare individuals for real-life scenarios where they might need to rely on their PFDs. In summary, adherence to local and international regulations is paramount for ensuring that PFDs are safe, reliable, and effective. By following these guidelines, individuals can trust that their PFDs will perform as expected in critical situations, thereby enhancing overall safety and reducing the risk of accidents. Regular inspections, proper maintenance, and comprehensive training further reinforce this compliance, making it an integral part of any safety protocol involving PFDs.
Meeting Specific Safety Standards
Meeting specific safety standards is a critical aspect of ensuring the integrity and effectiveness of Personal Flotation Devices (PFDs). These standards, often mandated by regulatory bodies such as the U.S. Coast Guard or international organizations like the International Organization for Standardization (ISO), are designed to guarantee that PFDs can perform their life-saving function reliably. For instance, PFDs must undergo rigorous testing to meet criteria related to buoyancy, durability, and visibility. The buoyancy test ensures that the device can keep a person afloat in various water conditions, while durability tests assess its ability to withstand environmental factors such as sunlight, saltwater, and mechanical stress. Visibility standards dictate that PFDs must be easily seen in low-light conditions, typically through the use of reflective materials or bright colors. Compliance with these standards involves regular inspections and maintenance checks. Users are advised to inspect their PFDs before each use for signs of wear and tear, such as cracks in the plastic or fraying of straps. Additionally, PFDs should be stored properly to prevent damage from exposure to extreme temperatures or direct sunlight. Manufacturers also play a crucial role by adhering to strict production guidelines and conducting quality control checks to ensure that every PFD meets or exceeds the required safety standards. The importance of adhering to these standards cannot be overstated. Non-compliant PFDs can fail when needed most, resulting in potentially fatal consequences. Therefore, it is imperative for both manufacturers and users to prioritize compliance with regulatory and safety standards. This includes understanding when a PFD needs to be replaced—typically after a certain number of years or if it shows significant signs of deterioration. By doing so, individuals can trust that their PFD will function as intended in emergency situations, providing them with the necessary flotation support to stay safe until help arrives. In summary, meeting specific safety standards for PFDs is essential for ensuring their reliability and effectiveness. Through rigorous testing, regular inspections, proper storage, and adherence to production guidelines, both manufacturers and users can help prevent accidents and save lives. Understanding these standards and knowing when to replace a PFD are key components of maintaining safety on the water.
Regular Inspection Requirements
Regular inspection requirements are a critical component of maintaining regulatory and safety standards, particularly when it comes to personal flotation devices (PFDs). These inspections ensure that PFDs remain in good working condition, thereby safeguarding the lives of individuals who rely on them. According to various maritime and safety regulations, PFDs must undergo periodic inspections to verify their integrity and functionality. For instance, the U.S. Coast Guard mandates that PFDs be inspected before each use to check for signs of wear, damage, or deterioration. This includes examining the fabric for tears or holes, ensuring that all straps and buckles are secure and functional, and verifying that the flotation material has not been compromised. In addition to pre-use inspections, many organizations and regulatory bodies recommend more comprehensive inspections at regular intervals. For example, inflatable PFDs often require annual inspections to ensure that the inflation mechanism is operating correctly and that there are no leaks in the bladder. These inspections may involve inflating the device and leaving it overnight to check for any loss of air pressure. Similarly, inherently buoyant PFDs should be inspected every few months to ensure that they have not absorbed excessive water or suffered any structural damage. The importance of these inspections cannot be overstated. A PFD that fails during an emergency can have catastrophic consequences. Therefore, it is crucial that users adhere strictly to inspection schedules and guidelines provided by manufacturers and regulatory authorities. Furthermore, keeping a record of inspections can help in tracking the maintenance history of each PFD, which is often a requirement for compliance with safety standards. In summary, regular inspection requirements are essential for ensuring the reliability and effectiveness of PFDs. By adhering to these protocols, individuals can significantly reduce the risk of PFD failure and enhance overall safety. Whether it is a pre-use check or a more detailed annual inspection, these practices are vital for maintaining compliance with regulatory standards and safeguarding lives at sea or in other water-based activities. As such, incorporating regular inspections into routine maintenance schedules should be a priority for anyone responsible for the upkeep of PFDs.