A Workplace Label Is Used When A Hazardous Material Is:

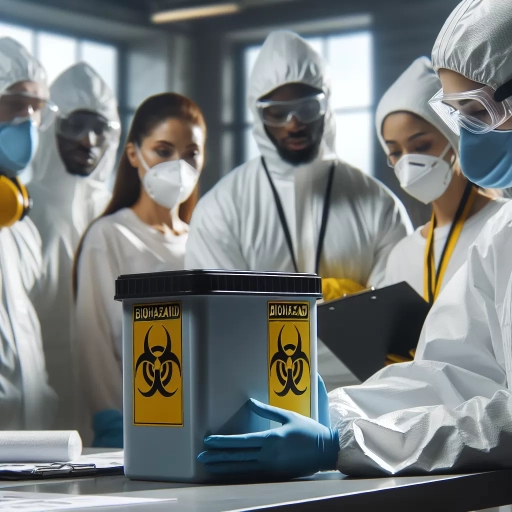
In the modern workplace, ensuring the safety and well-being of employees is paramount, especially when dealing with hazardous materials. A crucial tool in this endeavor is the workplace label, which serves as a vital communication device to alert workers about potential dangers. This article delves into the importance and implementation of these labels, starting with the critical task of **Identifying Hazardous Materials in the Workplace**. Understanding what constitutes a hazardous material is the first step in creating a safe environment. We will also explore **Regulations and Standards for Workplace Labels**, highlighting the legal and industry guidelines that govern their use. Finally, we will discuss **Best Practices for Implementing Hazardous Material Labels**, providing practical advice on how to effectively integrate these labels into your workplace safety protocol. By understanding these key aspects, businesses can significantly reduce risks and enhance overall workplace safety. Let's begin by examining the process of identifying hazardous materials in the workplace.
Identifying Hazardous Materials in the Workplace
In the modern workplace, ensuring the safety and health of employees is paramount. One critical aspect of workplace safety is the identification of hazardous materials, which can pose significant risks if not properly recognized and managed. This article delves into the essential strategies for identifying hazardous materials, focusing on three key areas: recognizing chemical hazards, detecting physical hazards, and understanding biological hazards. Chemical hazards, such as toxic substances and flammable liquids, require specific protocols for handling and storage to prevent accidents. Physical hazards, including electrical and mechanical dangers, need to be identified and mitigated to avoid injuries. Biological hazards, such as pathogens and allergens, also demand careful attention to protect workers from infection and illness. By understanding these different types of hazards, employers and employees can take proactive steps to create a safer work environment. In this article, we will explore each of these areas in depth to provide a comprehensive guide on identifying hazardous materials in the workplace.
Recognizing Chemical Hazards
Recognizing chemical hazards is a critical component of maintaining a safe and healthy work environment. When a hazardous material is present in the workplace, it is imperative to use appropriate labeling to alert employees of potential dangers. This labeling serves as a visual warning system, providing essential information about the nature of the hazard and necessary precautions to take. The Globally Harmonized System of Classification and Labeling of Chemicals (GHS) is widely adopted for this purpose, ensuring consistency and clarity in hazard communication. Under GHS, labels must include specific elements such as the product identifier, supplier information, hazard statements, precautionary statements, and pictograms. Pictograms are particularly important as they convey hazard information quickly and universally, transcending language barriers. For instance, the "flame" pictogram indicates flammable substances, while the "skull and crossbones" pictogram signifies toxic substances. Hazard statements describe the nature of the hazard, such as "toxic if inhaled," while precautionary statements provide advice on safe handling, use, and storage. In addition to labeling, recognizing chemical hazards involves understanding the classification of substances. GHS categorizes chemicals based on their physical, health, and environmental hazards. For example, flammable liquids are classified based on their flash points and boiling points, while toxic substances are categorized based on their acute toxicity levels. This classification system helps in assessing the severity of potential risks and implementing appropriate control measures. Training employees to recognize and interpret these labels is crucial. Workers should be educated on how to read and understand the information provided on labels, as well as how to handle different types of hazardous materials safely. Regular training sessions and drills can help ensure that employees are prepared to respond effectively in case of emergencies. Moreover, recognizing chemical hazards extends beyond labeling; it involves a comprehensive approach to workplace safety. This includes conducting regular risk assessments, maintaining proper ventilation systems, using personal protective equipment (PPE) when necessary, and ensuring that all employees follow established safety protocols. By integrating these measures into daily operations, workplaces can significantly reduce the risk of accidents and ensure a safer environment for everyone. In summary, recognizing chemical hazards through proper labeling and classification is essential for workplace safety. By adhering to standards like GHS and providing thorough training, employers can protect their employees from potential dangers associated with hazardous materials. This proactive approach not only complies with regulatory requirements but also fosters a culture of safety and responsibility within the organization.
Detecting Physical Hazards
Detecting physical hazards in the workplace is a critical component of ensuring a safe and healthy environment for all employees. Physical hazards encompass a wide range of potential dangers, including tripping hazards, falling objects, electrical hazards, and ergonomic issues. To effectively identify these hazards, employers and employees must be vigilant and proactive. One key strategy involves conducting regular workplace inspections to spot potential risks before they become incidents. For instance, ensuring that walkways are clear of clutter, cords are properly secured, and ladders are in good condition can significantly reduce the risk of tripping or falling. Additionally, implementing proper lighting in all areas of the workplace can help prevent accidents by making obstacles more visible. Another crucial aspect is the proper use and maintenance of equipment. Ensuring that machinery is regularly inspected and maintained according to manufacturer guidelines can prevent mechanical failures that could lead to injuries. Electrical safety is also paramount; this includes checking for frayed cords, ensuring that electrical equipment is grounded, and avoiding overloading circuits. Ergonomic hazards, which can lead to musculoskeletal disorders, should also be addressed by providing ergonomic training and ensuring that workstations are designed to minimize strain on employees. Training programs play a significant role in detecting physical hazards. Educating employees on how to identify and report potential hazards empowers them to take an active role in workplace safety. This includes teaching them how to use personal protective equipment (PPE) correctly and understanding the importance of adhering to safety protocols. Moreover, fostering a culture of safety encourages open communication where employees feel comfortable reporting any concerns without fear of reprisal. Technology can also be leveraged to enhance hazard detection. Advanced tools such as sensors and monitoring systems can alert management to potential hazards in real-time, allowing for swift action to mitigate risks. For example, sensors can detect changes in environmental conditions like temperature or humidity that might indicate a potential hazard. In conjunction with these measures, clear labeling of hazardous materials and areas is essential. When a hazardous material is present in the workplace, it must be labeled clearly according to regulatory standards such as those set by OSHA (Occupational Safety and Health Administration). These labels serve as visual warnings that alert employees to potential dangers and provide critical information about the nature of the hazard and necessary precautions. By combining these strategies—regular inspections, proper equipment maintenance, employee training, technological monitoring, and clear labeling—employers can create a robust system for detecting physical hazards in the workplace. This proactive approach not only protects employees from harm but also enhances overall productivity and compliance with safety regulations.
Understanding Biological Hazards
Understanding biological hazards is crucial for maintaining a safe and healthy work environment, particularly when identifying hazardous materials in the workplace. Biological hazards, also known as biohazards, are substances that can cause harm to humans, animals, or the environment through exposure to pathogens such as bacteria, viruses, fungi, and other microorganisms. These hazards can be found in various settings, including laboratories, healthcare facilities, agricultural workplaces, and even offices where contaminated materials may be present. When a hazardous material is identified in the workplace, proper labeling is essential to alert employees of potential dangers. A workplace label is used when a hazardous material is present to provide critical information about the nature of the hazard and necessary precautions. For biological hazards, this includes details on the type of pathogen involved, the level of risk associated with exposure, and specific handling and disposal procedures to minimize risk. Effective identification and labeling of biological hazards involve several key steps. First, it is important to conduct a thorough risk assessment to determine if biological agents are present and to evaluate their potential impact on workers. This may involve testing samples or reviewing existing data on the materials being handled. Once identified, these hazards must be classified according to their risk level, which can range from low-risk (e.g., certain types of bacteria) to high-risk (e.g., highly infectious viruses like Ebola). Proper labeling involves using standardized symbols and language that are easily recognizable by all employees. The Biohazard Symbol, a distinctive orange and black emblem, is widely recognized and should be prominently displayed on containers holding biohazardous materials. Additionally, labels should include clear instructions on personal protective equipment (PPE) requirements, such as gloves, masks, and eye protection, as well as any specific safety protocols for handling and disposing of these materials. Training is another critical component in managing biological hazards effectively. Employees who handle or may be exposed to biohazardous materials must receive comprehensive training on safe handling practices, emergency procedures in case of spills or exposure incidents, and proper use of PPE. Regular updates and refresher courses ensure that knowledge remains current and that new employees are adequately informed. In summary, understanding biological hazards is vital for workplace safety. By accurately identifying these hazards through risk assessments and proper labeling with clear instructions and symbols like the Biohazard Symbol, workplaces can significantly reduce the risk of exposure to harmful pathogens. Coupled with thorough employee training programs focused on safe handling practices and emergency procedures, workplaces can create a safer environment for everyone involved. This proactive approach not only protects workers but also ensures compliance with regulatory standards aimed at preventing biohazard-related incidents.
Regulations and Standards for Workplace Labels
In the modern workplace, ensuring the safety and health of employees is paramount, and one crucial aspect of this is the proper labeling of hazardous materials. Regulations and standards for workplace labels are designed to provide clear, consistent, and comprehensive information about potential dangers, enabling workers to take necessary precautions. This article delves into the critical guidelines and standards that govern workplace labeling, focusing on three key areas: OSHA Guidelines for Hazardous Material Labeling, which outline the mandatory requirements for labeling hazardous substances; GHS Compliance and Label Requirements, which align global standards for chemical labeling; and Industry-Specific Labeling Standards, which cater to the unique needs of different sectors. By understanding these regulations, employers can ensure compliance and create a safer work environment. Ultimately, this knowledge is essential for identifying hazardous materials in the workplace, a critical step in preventing accidents and protecting employee well-being.
OSHA Guidelines for Hazardous Material Labeling
When a hazardous material is present in the workplace, adhering to OSHA guidelines for labeling is crucial to ensure the safety and well-being of all employees. The Occupational Safety and Health Administration (OSHA) mandates specific standards for labeling hazardous materials to prevent accidents and exposures. Under the Hazard Communication Standard (HCS), employers must label containers of hazardous chemicals with information that clearly identifies the substance, its hazards, and necessary safety precautions. This includes using standardized labels that feature pictograms, signal words, hazard statements, precautionary statements, and the name, address, and contact information of the manufacturer or distributor. OSHA's HCS also requires that labels be legible, in English, and prominently displayed on the container. The Globally Harmonized System of Classification and Labeling of Chemicals (GHS) has been adopted by OSHA to standardize these labels, making it easier for workers to understand the risks associated with each chemical. For instance, pictograms such as the skull and crossbones or the flame symbol quickly convey severe hazards like toxicity or flammability. Signal words like "Danger" or "Warning" indicate the level of severity, while hazard statements describe the nature of the hazard and precautionary statements provide advice on how to minimize or prevent adverse effects. Additionally, OSHA requires that secondary containers used in the workplace be labeled with the same information as the original container unless the chemical is used within the work shift and is under the control of the employee who transferred it. This ensures that even when chemicals are transferred into smaller containers, they remain properly identified and their hazards are communicated effectively. Employers must also maintain a Safety Data Sheet (SDS) for each hazardous chemical in the workplace, which provides detailed information about the chemical's properties, handling procedures, and emergency response measures. Compliance with these guidelines is not only a legal requirement but also a critical component of a robust workplace safety program. Proper labeling helps prevent misunderstandings and misuses of hazardous materials, reducing the risk of injuries, illnesses, and fatalities. By adhering to OSHA's standards for hazardous material labeling, employers can create a safer work environment where employees are well-informed and equipped to handle chemicals safely. Regular training sessions and audits should be conducted to ensure that all employees understand the significance of these labels and can identify potential hazards at a glance. This proactive approach not only protects workers but also helps businesses avoid costly fines and legal repercussions associated with non-compliance.
GHS Compliance and Label Requirements
In the realm of workplace safety, compliance with the Globally Harmonized System of Classification and Labelling of Chemicals (GHS) is paramount. GHS compliance and label requirements are designed to ensure that hazardous materials are identified, classified, and communicated effectively to all stakeholders, thereby reducing the risk of accidents and injuries. When a hazardous material is present in the workplace, it is crucial to adhere to GHS standards for labeling. These labels must include specific elements such as the product identifier, supplier information, and hazard statements that describe the nature of the hazard. Additionally, precautionary statements outlining measures to mitigate risks and pictograms that visually represent hazards are mandatory. For instance, pictograms like the skull and crossbones symbol for toxicity or the flame symbol for flammability provide immediate visual cues about the dangers associated with a substance. The GHS system categorizes chemicals into different hazard classes and categories based on their physical, health, and environmental hazards. This classification determines the specific information that must be included on the label. For example, substances classified as highly toxic will have more stringent labeling requirements compared to those that are less hazardous. The labels must also be legible and durable enough to withstand the conditions in which they are used. This ensures that critical safety information remains accessible over time. Regulatory bodies such as the Occupational Safety and Health Administration (OSHA) in the United States enforce GHS compliance through standards like the Hazard Communication Standard (HCS). Employers are required to ensure that all hazardous chemicals in their workplaces are properly labeled according to GHS guidelines. This includes ensuring that employees are trained to understand the information on these labels and how to handle hazardous materials safely. Moreover, GHS compliance extends beyond labeling; it also involves maintaining Safety Data Sheets (SDSs) for each hazardous chemical. These SDSs provide detailed information about the chemical's properties, safe handling practices, emergency procedures, and first aid measures. By adhering to GHS standards for both labels and SDSs, workplaces can significantly enhance their safety protocols and protect employees from potential hazards. In summary, GHS compliance and label requirements are essential components of a comprehensive workplace safety strategy. By accurately classifying hazardous materials and ensuring that labels and SDSs meet GHS standards, employers can foster a safer working environment where employees are well-informed about potential risks and equipped with the knowledge to handle them effectively. This not only complies with regulatory requirements but also contributes to a culture of safety that benefits everyone involved.
Industry-Specific Labeling Standards
Industry-specific labeling standards play a crucial role in ensuring workplace safety and compliance with regulations. These standards are tailored to address the unique hazards and requirements of various industries, such as chemical manufacturing, healthcare, construction, and transportation. For instance, in the chemical industry, labels must adhere to the Globally Harmonized System of Classification and Labeling of Chemicals (GHS), which includes standardized symbols, hazard statements, and precautionary statements to clearly communicate the risks associated with each chemical. In healthcare settings, labels on medical devices and pharmaceuticals must comply with FDA regulations, including clear instructions for use and warnings about potential side effects. Construction sites require labels that meet OSHA standards, highlighting hazards such as electrical shock, fall risks, and chemical exposure. Similarly, in the transportation sector, labels on hazardous materials must conform to DOT regulations, ensuring that drivers and handlers are aware of the risks involved in transporting these materials. These industry-specific standards not only help in preventing accidents but also facilitate compliance with broader regulatory frameworks. For example, the Occupational Safety and Health Administration (OSHA) mandates that all workplaces use labels that conform to its Hazard Communication Standard (HCS), which aligns with GHS for chemical labeling. This ensures a consistent approach across different industries when dealing with hazardous substances. Additionally, industry-specific labeling standards often include specific formatting requirements, such as color coding, font sizes, and pictograms, which enhance visibility and understanding among workers. Moreover, these standards are regularly updated to reflect new research findings and technological advancements. For instance, updates in medical labeling may include new warnings based on post-market surveillance data or changes in treatment protocols. Similarly, advancements in materials science can lead to new labeling requirements for construction materials or chemicals. In summary, industry-specific labeling standards are essential for maintaining a safe and compliant workplace environment. By adhering to these standards, employers can ensure that their workers are adequately informed about potential hazards and take necessary precautions to mitigate risks. This not only protects employees but also helps organizations avoid legal liabilities and reputational damage associated with non-compliance. As workplaces continue to evolve, the importance of these standards will only grow, underscoring the need for ongoing education and adherence to these critical guidelines.
Best Practices for Implementing Hazardous Material Labels
Implementing hazardous material labels is a critical component of ensuring workplace safety and compliance with regulatory standards. These labels serve as vital communication tools, alerting employees to potential dangers and providing essential information for safe handling and use. To effectively manage hazardous materials, it is crucial to adhere to best practices that encompass several key areas. First, **Proper Placement and Visibility of Labels** ensures that critical safety information is readily accessible and easily seen by all personnel. Second, **Training Employees on Label Interpretation** is essential to guarantee that workers understand the meaning and implications of the labels they encounter. Finally, **Regularly Updating and Maintaining Labels** ensures that the information remains accurate and relevant over time. By focusing on these aspects, organizations can significantly reduce the risk of accidents and ensure a safer working environment. Understanding these best practices is fundamental to identifying hazardous materials in the workplace effectively.
Proper Placement and Visibility of Labels
Proper placement and visibility of labels are crucial components of best practices for implementing hazardous material labels in the workplace. When a hazardous material is present, it is imperative to ensure that labels are strategically positioned to maximize visibility and comprehension. Labels should be affixed to the container or storage area in a manner that prevents them from being obscured by other objects or materials. For instance, labels on chemical drums should be placed on the front and sides to ensure they are easily readable from multiple angles, even when the drums are stacked or stored in tight spaces. Moreover, the placement of labels must adhere to specific standards to avoid confusion. For example, labels should not be placed near other markings or signs that could distract from their importance. The use of clear and concise language, along with internationally recognized symbols and color codes, enhances the effectiveness of these labels. In environments where multiple languages are spoken, bilingual or multilingual labels can significantly improve comprehension among workers. Visibility is also enhanced by ensuring that labels are made from durable materials that can withstand the conditions of the workplace. This includes resistance to chemicals, moisture, and physical wear. Reflective or high-visibility labels can be particularly useful in low-light environments, such as warehouses or storage areas with limited lighting. Additionally, regular inspections should be conducted to ensure that labels remain legible and intact. This involves checking for signs of wear, fading, or damage and replacing labels as necessary. Training programs for employees should also include information on the proper placement and maintenance of hazardous material labels to foster a culture of safety and compliance. In summary, proper placement and visibility of hazardous material labels are essential for maintaining a safe and compliant workplace. By adhering to best practices such as strategic placement, clear communication, durability, and regular maintenance, organizations can significantly reduce the risk of accidents and ensure that all employees are aware of potential hazards. This proactive approach not only protects workers but also helps in complying with regulatory standards, thereby avoiding legal and financial repercussions. By prioritizing the visibility and placement of these critical labels, workplaces can create a safer, more informed environment for everyone involved.
Training Employees on Label Interpretation
Training employees on label interpretation is a critical component of ensuring workplace safety, particularly when dealing with hazardous materials. A workplace label is used when a hazardous material is present, and it serves as a vital communication tool that alerts workers to potential dangers and provides essential information for safe handling. Effective training in label interpretation involves several key elements. First, employees must understand the standardized labeling system, which includes the Globally Harmonized System of Classification and Labeling of Chemicals (GHS). This system uses specific symbols, colors, and phrases to convey hazard information quickly and consistently. For instance, the GHS pictograms such as the skull and crossbones for toxicity or the flame for flammability are universally recognized and must be explained in detail during training. Second, training should cover the different sections of a hazardous material label, including the product identifier, hazard statements, precautionary statements, and supplier information. Employees need to know how to read and interpret these sections accurately to take appropriate actions. For example, understanding the hazard statements helps workers recognize the type and severity of the hazard, while precautionary statements provide guidance on how to mitigate risks. Third, hands-on training and real-world examples are essential for reinforcing theoretical knowledge. This can include practice sessions where employees are given sample labels to interpret and discuss in small groups. Such interactive approaches help ensure that employees can apply their knowledge in practical scenarios. Additionally, ongoing training and regular updates are crucial as labeling standards evolve and new substances are introduced into the workplace. Employers should also consider using visual aids, such as posters and safety videos, to reinforce key points and make the information more accessible. Finally, it is important to assess employee understanding through quizzes or competency tests to ensure that they have grasped the material. This not only helps in identifying areas where additional training may be needed but also reinforces the importance of label interpretation in maintaining a safe work environment. By implementing these best practices in training employees on label interpretation, organizations can significantly reduce the risk of accidents and ensure compliance with regulatory requirements. Well-trained employees are better equipped to handle hazardous materials safely, which ultimately contributes to a safer and more productive workplace.
Regularly Updating and Maintaining Labels
Regularly updating and maintaining labels is a crucial aspect of implementing best practices for hazardous material labeling in the workplace. When a hazardous material is introduced, it is essential to ensure that the labels accurately reflect the latest safety data sheets (SDS) and regulatory requirements. This involves periodic reviews of the labeling system to verify that all information remains current and compliant with standards such as those set by OSHA (Occupational Safety and Health Administration) and GHS (Globally Harmonized System of Classification and Labelling of Chemicals). Outdated labels can lead to confusion, misidentification, and potentially dangerous situations. For instance, if a chemical's classification changes due to new research or updated regulations, the label must be revised accordingly to reflect these changes. Additionally, any changes in the composition of the material or its handling procedures should be promptly reflected on the label to ensure that workers are aware of the latest safety protocols. A systematic approach to label maintenance includes scheduling regular audits of all hazardous materials and their corresponding labels. This can be done quarterly or annually, depending on the frequency of material usage and updates in regulatory standards. During these audits, it is important to check for any signs of wear and tear on the labels themselves, as well as ensuring that they are still legible and securely attached to the containers. Moreover, training programs should be in place to educate employees on the importance of label maintenance and how to identify when a label needs updating. This includes understanding the GHS pictograms, hazard statements, and precautionary statements that are critical for safe handling practices. By fostering a culture of vigilance regarding label accuracy, workplaces can significantly reduce the risk of accidents and ensure compliance with legal requirements. Incorporating technology can also streamline the process of label maintenance. Digital labeling systems allow for quick updates and can automatically notify personnel when changes are made to SDS or regulatory standards. Furthermore, using durable label materials that resist fading or damage can extend the lifespan of labels and reduce the need for frequent replacements. In summary, regularly updating and maintaining labels is a vital component of a comprehensive hazardous material labeling strategy. By ensuring that all labels are current, accurate, and compliant with regulatory standards, workplaces can enhance safety, reduce risks, and maintain a culture of safety awareness among employees. This proactive approach not only protects workers but also helps organizations avoid potential legal liabilities associated with non-compliance.