What Happens To Metal Pipe When Heated With 100c Liquid

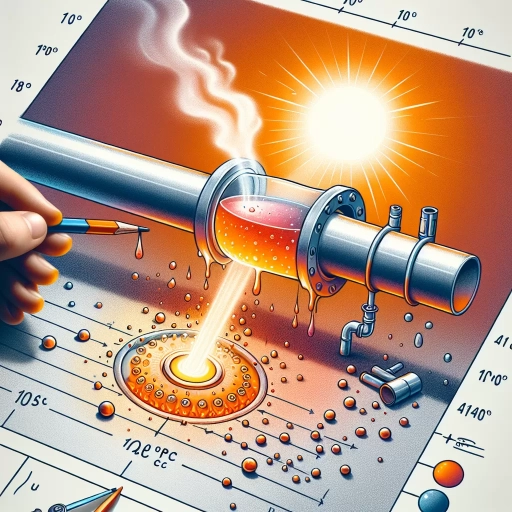
When a metal pipe is subjected to a 100°C liquid, several critical phenomena occur that are essential to understand for both theoretical and practical purposes. The interaction between the metal and the heated liquid triggers a series of physical changes that can significantly impact the pipe's structure and functionality. This article delves into three key aspects of this process: Thermal Expansion and Deformation, Material Properties and Phase Changes, and Practical Implications and Safety Considerations. First, we will explore how the heat causes the metal to expand and potentially deform, affecting its dimensions and integrity. Next, we will examine the changes in material properties and phase transitions that occur as the metal absorbs heat. Finally, we will discuss the practical implications of these changes and the safety considerations that must be taken into account when working with heated metal pipes. Understanding these dynamics is crucial for ensuring the safe and efficient operation of various industrial and engineering systems. Let's begin by examining the initial effects of heat on metal pipes, specifically focusing on Thermal Expansion and Deformation.
Thermal Expansion and Deformation
Thermal expansion and deformation are fundamental concepts in physics and engineering, governing how materials respond to changes in temperature. This phenomenon is crucial in various fields, including construction, manufacturing, and infrastructure development. When metals are subjected to temperature variations, they undergo linear expansion, which can significantly impact their dimensions and structural integrity. For instance, the linear expansion of metal components can lead to changes in pipe diameter and length, affecting the overall performance and safety of systems such as plumbing and HVAC. Moreover, these changes can potentially introduce structural instability, compromising the durability and reliability of buildings and machinery. Understanding thermal expansion and deformation is essential for designing and maintaining robust structures that can withstand thermal stresses. In this article, we will delve into the specifics of linear expansion of metal, changes in pipe diameter and length, and the potential for structural instability, ultimately shedding light on the broader implications of thermal expansion and deformation.
Linear Expansion of Metal
When a metal pipe is subjected to heating, such as being immersed in a 100°C liquid, it undergoes a phenomenon known as linear expansion. This process is a fundamental aspect of thermal expansion and deformation, where the metal's dimensions change in response to temperature variations. At the atomic level, metals are composed of atoms arranged in a crystalline structure. When heat is applied, these atoms gain kinetic energy and start vibrating more vigorously. As a result, the interatomic distances increase, causing the metal to expand. The linear expansion of metal can be quantified using the coefficient of linear thermal expansion (α), which is specific to each material. This coefficient represents how much the length of the metal changes per degree Celsius of temperature increase. For instance, if a metal pipe has a coefficient of linear thermal expansion of 10^-5 per degree Celsius and its original length is 1 meter, it will expand by 0.001 meters (or 1 mm) when heated from 20°C to 100°C. This expansion is not uniform and can lead to significant deformation if not properly managed. In practical applications, such as in plumbing or engineering, understanding and accommodating this expansion is crucial to prevent damage or failure. For example, in piping systems, expansion joints are often used to allow for the increased length of pipes due to heating, thereby preventing excessive stress and potential ruptures. Moreover, the rate at which metals expand varies significantly among different materials. Some metals like aluminum have higher coefficients of thermal expansion compared to others like steel, meaning they expand more with the same temperature increase. This variability necessitates careful material selection based on the specific thermal conditions a structure will encounter. In addition to material properties, the geometry of the metal also plays a role in its expansion behavior. For instance, a thin metal rod will expand more noticeably than a thick one under the same heating conditions due to its lower thermal mass and higher surface-to-volume ratio. Understanding linear expansion is essential for designing and maintaining systems that involve heating metals. It ensures that structures can withstand thermal stresses without compromising their integrity or functionality. By accounting for these changes in dimension, engineers can create more resilient and reliable systems that perform optimally across various temperature ranges. In summary, the linear expansion of metal when heated is a critical consideration in engineering and construction. It involves the increase in length due to increased atomic vibrations, quantified by the coefficient of linear thermal expansion. Properly managing this expansion through material selection, design accommodations like expansion joints, and understanding geometric factors ensures the longevity and performance of metal structures under thermal stress.
Changes in Pipe Diameter and Length
When a metal pipe is subjected to heating, particularly with a 100°C liquid, significant changes in its physical dimensions can occur due to thermal expansion and deformation. One of the most critical aspects to consider is the alteration in pipe diameter and length. As the metal absorbs heat, its atoms gain kinetic energy and start vibrating more vigorously, causing them to move further apart. This increased atomic spacing results in the expansion of the material. The change in pipe diameter is often less pronounced compared to the change in length but is still crucial for engineering and design purposes. When heated, the circumference of the pipe increases, leading to an expansion of its diameter. This radial expansion can affect the fit and sealing of connections, potentially leading to leaks or other operational issues if not properly accounted for. For instance, in piping systems where precise fits are required, such as in flanged connections or threaded joints, even a slight increase in diameter can compromise the integrity of the seal. The change in length is more significant and often more critical in terms of structural integrity and system performance. As the pipe expands longitudinally, it can exert additional stresses on supports, anchors, and other components of the piping system. This longitudinal expansion must be accommodated through the use of expansion joints or flexible connections to prevent damage or failure. Failure to account for this expansion can lead to buckling, bending, or even rupture of the pipe under extreme conditions. In practical applications, understanding these changes is essential for ensuring the safe and efficient operation of piping systems. Engineers must calculate the expected thermal expansion based on the material properties of the pipe and the temperature differential it will experience. This involves using formulas such as the linear thermal expansion equation, which relates the change in length to the coefficient of thermal expansion, original length, and temperature change. By accurately predicting these dimensional changes, engineers can design systems that mitigate potential risks associated with thermal expansion and deformation, thereby enhancing reliability and longevity. Moreover, different materials exhibit varying degrees of thermal expansion due to their unique coefficients of thermal expansion. For example, copper pipes expand more than steel pipes when subjected to the same temperature increase. This material-specific behavior must be considered during the design phase to ensure compatibility and performance across different components within a piping system. In summary, the changes in pipe diameter and length due to heating are critical factors that must be addressed in the design and operation of piping systems. By understanding and accommodating these dimensional changes through appropriate engineering practices, we can ensure that metal pipes remain functional and safe even when exposed to high temperatures. This knowledge is fundamental in various industries such as chemical processing, power generation, and HVAC systems where thermal management is paramount.
Potential for Structural Instability
When metal pipes are subjected to heating with a 100°C liquid, one of the critical concerns is the potential for structural instability. This instability arises due to thermal expansion and deformation, which can significantly alter the pipe's mechanical properties and integrity. As the metal absorbs heat, it expands in all directions, leading to an increase in both length and diameter. This expansion can cause several issues, particularly if the pipe is constrained or if there are significant temperature gradients along its length. For instance, if the pipe is fixed at both ends, the thermal expansion can lead to compressive stresses that may cause buckling or bending. In extreme cases, this could result in catastrophic failure, especially if the material's yield strength is exceeded. Additionally, uneven heating can induce thermal stresses due to differential expansion rates across different sections of the pipe. These stresses can lead to warping or distortion, compromising the structural stability and potentially causing leaks or ruptures. Moreover, repeated cycles of heating and cooling can induce fatigue in the material, further weakening its structural integrity over time. The material's microstructure may also undergo changes due to thermal cycling, such as grain growth or phase transformations, which can affect its mechanical properties. For example, some metals may undergo a reduction in ductility or an increase in brittleness when heated above certain temperatures, making them more susceptible to cracking under stress. To mitigate these risks, engineers often employ various strategies such as using expansion joints or flexible connections to accommodate thermal expansion. Selecting materials with lower coefficients of thermal expansion or higher thermal conductivity can also help minimize the effects of heating. Furthermore, ensuring uniform heating and cooling rates, as well as implementing regular maintenance and inspection protocols, are crucial for maintaining the structural stability of metal pipes under thermal stress. In summary, the potential for structural instability in metal pipes heated with a 100°C liquid is a significant concern that must be addressed through careful material selection, design considerations, and operational practices. Understanding and managing thermal expansion and deformation are essential for ensuring the safe and reliable operation of these critical components in various industrial applications.
Material Properties and Phase Changes
Material properties and phase changes are fundamental concepts in understanding the behavior of materials under various conditions. These phenomena are crucial in engineering, physics, and materials science, as they determine how materials respond to different temperatures and environmental stresses. This article delves into three key aspects: **Temperature-Dependent Mechanical Properties**, which explores how the mechanical characteristics of materials change with temperature; **Possible Phase Transitions in Metals**, which examines the transformations metals undergo as they transition between solid, liquid, and gas states; and **Impact on Material Strength and Durability**, which discusses how these changes affect the overall performance and lifespan of materials. By understanding these principles, we can better predict and manage material behavior, ensuring optimal performance in diverse applications. This knowledge is particularly important when considering **Thermal Expansion and Deformation**, as it directly influences the structural integrity and functionality of materials in various thermal environments.
Temperature-Dependent Mechanical Properties
Temperature-dependent mechanical properties are a critical aspect of understanding how materials, particularly metals, behave under varying thermal conditions. When a metal pipe is exposed to a 100°C liquid, several key changes occur that impact its mechanical performance. Initially, the increase in temperature causes the metal atoms to gain kinetic energy and move more rapidly, leading to an expansion of the material. This thermal expansion can result in an increase in the pipe's dimensions, which may affect its fit and functionality in certain applications. As the temperature rises, the yield strength and ultimate tensile strength of the metal typically decrease. This reduction in strength is due to the increased mobility of dislocations within the crystal structure of the metal, making it easier for plastic deformation to occur. Consequently, the metal becomes more ductile but less resistant to stress and strain. For instance, in engineering contexts where high-temperature resistance is crucial, such as in power plants or chemical processing facilities, selecting materials with stable mechanical properties over a wide temperature range is essential. Additionally, the elastic modulus of metals generally decreases with increasing temperature. This means that the metal becomes less stiff and more prone to deformation under load. In practical terms, this could lead to a reduction in the pipe's ability to withstand external pressures without deforming excessively. However, some metals exhibit unique properties at elevated temperatures; for example, certain alloys may undergo phase changes that can temporarily enhance their mechanical properties before eventually degrading. Understanding these temperature-dependent mechanical properties is vital for designing and operating systems that involve heating or cooling processes. Engineers must consider these factors to ensure the structural integrity and performance reliability of components like metal pipes. For instance, in piping systems used in high-temperature applications, materials selection and design must account for thermal expansion, reduced strength, and potential phase changes to prevent failures and ensure safe operation. In summary, when a metal pipe is heated with a 100°C liquid, it undergoes significant changes in its mechanical properties due to thermal effects. These changes include expansion, reduced strength, increased ductility, and decreased stiffness. By comprehending these temperature-dependent properties, engineers can make informed decisions about material selection and system design to ensure optimal performance and safety across various thermal conditions. This knowledge is fundamental in fields such as mechanical engineering, materials science, and industrial processes where temperature plays a critical role in material behavior.
Possible Phase Transitions in Metals
When metals are subjected to varying temperatures, they can undergo significant phase transitions that alter their physical and mechanical properties. These transitions are crucial in understanding the behavior of metal pipes when exposed to heat, such as being immersed in a 100°C liquid. One of the primary phase transitions in metals is the solid-to-liquid transition, or melting. As a metal pipe is heated, the atoms gain kinetic energy and begin to vibrate more vigorously. At the melting point, these vibrations become so intense that the rigid structure of the solid metal breaks down, and the material transforms into a liquid. This transition is particularly relevant for applications involving high-temperature processes, where maintaining structural integrity is critical. Another important phase transition is the solid-state transformation, which occurs without a change in temperature but involves a change in crystal structure. For example, some metals like iron undergo a phase change from a body-centered cubic (BCC) structure to a face-centered cubic (FCC) structure at specific temperatures. This transformation can affect the metal's strength, ductility, and magnetic properties. In the context of heating a metal pipe, such transformations can lead to changes in its mechanical behavior and potentially impact its performance under stress. Additionally, metals can exhibit allotropic transformations, where different allotropes (forms) of the same element exist at different temperatures. For instance, titanium has two allotropes: alpha-titanium (hexagonal close-packed) and beta-titanium (body-centered cubic), with the latter being stable at higher temperatures. Understanding these allotropes is essential for predicting how a metal pipe will behave when heated, as it may transition between these forms and alter its properties accordingly. Furthermore, heating can induce recrystallization in metals, especially those that have been previously deformed or work-hardened. As the metal reaches a certain temperature, the deformed grains can recrystallize into new, stress-free grains, which can significantly affect the material's strength and ductility. This process is often seen in annealing treatments where metals are heated to relieve internal stresses and restore their original properties. In summary, when a metal pipe is heated with a 100°C liquid, several phase transitions can occur depending on the specific metal and its initial state. These transitions include melting, solid-state transformations, allotropic changes, and recrystallization. Each of these transitions can profoundly impact the metal's properties and performance, making it essential to understand and predict these changes for various industrial applications. By recognizing these phase transitions, engineers and materials scientists can better design and optimize metal components to withstand thermal stresses and maintain their desired characteristics under different conditions.
Impact on Material Strength and Durability
When metal pipes are exposed to high temperatures, such as being heated with a 100°C liquid, several critical factors come into play that significantly impact their material strength and durability. The primary concern is the thermal expansion of the metal, which can lead to dimensional changes and potential distortion. Metals generally expand when heated, and this expansion can cause stress within the material, especially if the pipe is constrained or if there are significant temperature gradients. For instance, if one part of the pipe is heated more than another, uneven expansion can result in warping or bending. Moreover, prolonged exposure to elevated temperatures can induce phase changes in the metal's microstructure. Many metals undergo phase transformations at specific temperatures, which can alter their mechanical properties. For example, some steels may undergo austenitization when heated above certain temperatures, leading to changes in their hardness and strength upon cooling. This process can either enhance or degrade the material's properties depending on the cooling rate and the specific alloy composition. Another crucial aspect is the potential for oxidation and corrosion. High temperatures accelerate chemical reactions, including those between the metal and its environment. When heated, metals are more susceptible to forming oxides or reacting with other substances present in the liquid or surrounding air, which can weaken the material over time. Additionally, if the liquid contains corrosive substances, the risk of corrosion increases, further compromising the pipe's integrity. The impact on material strength also extends to the possibility of creep and fatigue. Creep refers to the gradual deformation of a material under constant stress over time, which is exacerbated by high temperatures. Fatigue, on the other hand, involves the weakening of the material due to repeated stress cycles, which can be accelerated by thermal cycling. Both phenomena can lead to premature failure of the metal pipe, especially in applications where reliability and longevity are critical. In summary, heating metal pipes with a 100°C liquid introduces multiple challenges that affect their strength and durability. Understanding these impacts is essential for designing and operating systems that involve high-temperature conditions to ensure safe and efficient performance. By considering thermal expansion, phase changes, oxidation/corrosion risks, and potential for creep and fatigue, engineers can select appropriate materials and implement protective measures to maintain the integrity of metal pipes under various operating conditions. This comprehensive approach ensures that metal pipes continue to perform reliably even in demanding environments.
Practical Implications and Safety Considerations
In the realm of industrial and engineering applications, understanding the practical implications and safety considerations of thermal expansion and deformation is paramount. This critical aspect affects various components, particularly pipes, which are integral to numerous systems. The effects on pipe integrity and functionality are a primary concern, as thermal changes can alter the structural properties and performance of these vital conduits. Additionally, the risk of leaks or ruptures due to thermal stress poses significant hazards that must be mitigated. To ensure safe operations, stringent safety protocols for handling heated pipes are essential. These considerations collectively underscore the importance of addressing thermal expansion and deformation in a comprehensive manner. By delving into these key areas, we can better navigate the complexities associated with thermal changes and maintain the reliability and safety of our systems. This article will explore these critical aspects in detail, providing insights into the practical implications and safety considerations that arise from thermal expansion and deformation.
Effects on Pipe Integrity and Functionality
When metal pipes are exposed to a 100°C liquid, several critical effects on their integrity and functionality can arise, underscoring the importance of careful consideration in practical applications and safety protocols. Firstly, thermal expansion becomes a significant factor; as the pipe material heats up, it expands, which can lead to increased stress on the pipe's structure and connections. This expansion can cause misalignment or even damage to fittings and joints, potentially leading to leaks or ruptures. Additionally, the thermal gradient across the pipe wall can induce residual stresses that may compromise the pipe's mechanical properties over time. The elevated temperature also accelerates chemical reactions such as corrosion and scaling. For instance, in water-based systems, heating can increase the rate of oxidation and scaling, forming deposits that reduce the pipe's internal diameter and impair fluid flow. Corrosion rates can also increase due to higher kinetic energy of reactants at elevated temperatures, potentially weakening the pipe material and reducing its lifespan. Moreover, prolonged exposure to high temperatures can alter the microstructure of the metal itself. Many metals undergo phase transformations or grain growth at elevated temperatures, which can affect their mechanical strength, ductility, and resistance to fatigue. For example, some steels may undergo tempering or annealing processes that alter their hardness and toughness, impacting their ability to withstand operational stresses. From a practical standpoint, these effects necessitate careful material selection and design considerations. Engineers must choose materials with appropriate thermal properties and resistance to corrosion and scaling at the expected operating temperatures. Regular inspections and maintenance are also crucial to monitor for signs of degradation or damage caused by thermal stress and chemical reactions. In terms of safety considerations, the potential for leaks or ruptures due to thermal stress or material degradation is a critical concern. Leaks can lead to loss of process fluid, which may be hazardous if the fluid is toxic or flammable. Ruptures can result in catastrophic failures with severe consequences including injury, environmental damage, and costly downtime. Therefore, implementing robust safety protocols such as temperature monitoring systems, regular maintenance schedules, and emergency response plans is essential to mitigate these risks and ensure the safe operation of metal pipes under high-temperature conditions. By understanding these effects on pipe integrity and functionality, operators can take proactive measures to maintain system reliability and safety.
Risk of Leaks or Ruptures
When metal pipes are subjected to heating with a 100°C liquid, several critical risks and safety considerations come into play, particularly the risk of leaks or ruptures. The primary concern is the thermal expansion of the metal, which can lead to increased stress on the pipe material. As metals heat up, they expand, and if this expansion is constrained by fittings, valves, or other structural components, it can result in excessive pressure buildup. This pressure can exceed the pipe's design limits, potentially causing leaks or even catastrophic ruptures. Additionally, thermal cycling—repeated heating and cooling—can accelerate fatigue in the metal, weakening its integrity over time and increasing the likelihood of failure. Another significant factor is the potential for corrosion acceleration. Many metals are more susceptible to corrosion at elevated temperatures, especially when exposed to certain types of liquids. For instance, if the liquid contains corrosive substances or if there is moisture present, the risk of corrosion increases significantly. Corrosion can weaken the pipe wall, reducing its ability to withstand internal pressures and further increasing the risk of leaks or ruptures. Moreover, the heating process can also affect the mechanical properties of the pipe material. Some metals undergo changes in their microstructure when heated, which can alter their strength and ductility. For example, certain alloys may experience a loss of tensile strength or become more brittle at high temperatures, making them more prone to cracking under stress. From a practical standpoint, these risks necessitate careful planning and monitoring during operations involving heated liquids. Regular inspections are crucial to detect any signs of wear, corrosion, or damage before they lead to serious incidents. Proper material selection based on the expected operating conditions is also essential; choosing materials with high thermal stability and resistance to corrosion can mitigate many of these risks. Furthermore, ensuring that all fittings and connections are designed to accommodate thermal expansion without inducing undue stress on the pipe system is vital for maintaining safety and integrity. In summary, the risk of leaks or ruptures when heating metal pipes with a 100°C liquid is multifaceted and demands careful consideration of thermal expansion, corrosion potential, and material properties. By understanding these factors and implementing appropriate safety measures, operators can significantly reduce the likelihood of accidents and ensure reliable operation of their piping systems.
Safety Protocols for Handling Heated Pipes
When handling heated pipes, especially those exposed to 100°C liquids, it is crucial to adhere to stringent safety protocols to prevent injuries and ensure operational integrity. The primary concern is the risk of thermal burns from direct contact with the heated pipe or splashes of hot liquid. To mitigate this, personnel should wear appropriate personal protective equipment (PPE) including heat-resistant gloves, safety glasses, and face shields. Additionally, protective clothing such as flame-resistant coveralls and closed-toe shoes can provide an extra layer of protection. Proper insulation and shielding of the pipes are also essential. Insulation materials like refractory blankets or ceramic fiber can help reduce the surface temperature of the pipes, making them safer to handle. Moreover, using thermal imaging cameras can help identify hot spots and areas where additional insulation may be needed. Another critical aspect is the use of proper tools and equipment. Heat-resistant tongs, pliers, and wrenches should be used when manipulating heated pipes to avoid direct contact. It is also important to ensure that all tools are in good condition and free from any damage that could compromise their heat resistance. Regular maintenance and inspection of the piping system are vital to prevent leaks and ruptures that could lead to scalding liquids being released. This includes checking for signs of wear, corrosion, or damage on the pipes and fittings. Any issues identified should be addressed promptly by trained personnel. Training programs for staff handling heated pipes are indispensable. These programs should cover the safe handling procedures, emergency response protocols, and the importance of adhering to safety guidelines. Regular drills and simulations can help prepare workers for potential hazards and ensure they are equipped to handle emergencies effectively. Finally, clear signage and labeling of heated pipes are necessary to alert workers of potential hazards. Warning signs indicating high temperatures should be prominently displayed near areas where heated pipes are present. This visual reminder can help reinforce the importance of safety protocols and encourage vigilant behavior among workers. By implementing these safety protocols rigorously, organizations can significantly reduce the risk associated with handling heated pipes, ensuring a safer working environment for all personnel involved.