Which Two Groups Does Whmis 2015 Classify Hazards Into

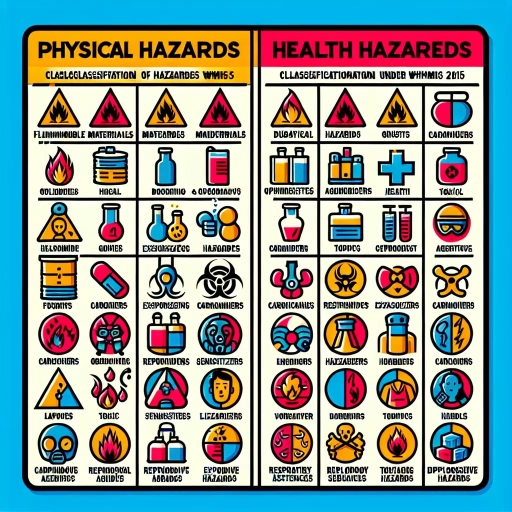
Understanding WHMIS 2015 And Its Primary Objectives
The Essence of WHMIS 2015
The Workplace Hazardous Materials Information System (WHMIS) 2015 is the standard Hazard Communication System in Canada. The WHMIS 2015 system is designed to provide vital information about hazardous products to workers, employers, and suppliers. This information is crucial in ensuring everyone comprehends the potential dangers or hazards, the protective measures to implement, and the possible adverse health effects a product may cause.
The Transition from WHMIS 1988 to WHMIS 2015
Initially, WHMIS was introduced in 1988 as a vital measure to protect Canadian workers from hazardous workplace materials. The original WHMIS, also known as WHMIS 1988, was modified and updated to align with the international hazard communication systems. The transition to WHMIS 2015 included adherence to the Globally Harmonized System (GHS) for classifying and communicating hazards. This change was done in stages, with the final transition period ending in 2018. The adherence to GHS means that labelling and safety data sheet formats have changed and hazard classes have been updated.
Key Objectives of WHMIS 2015
The essential objectives of WHMIS 2015 include creating a system for classifying hazards, standardising the communication of hazards, enhancing the comprehension of hazards, and increasing the safety of workers. The updated system helps workers to clearly understand the hazards associated with various materials, enabling them to take appropriate preventative measures and handle the materials securely and safely.
The Two Hazard Classification Groups in WHMIS 2015
Physical Hazards Group
WHMIS 2015 classifies hazards into two major groups: physical hazards and health hazards. The Physical Hazards group pertains to substances or chemicals that present risks and dangerous properties, aside from human health hazards. These can include being combustible, reactive or explosive. Physical hazards can lead to physical harm such as explosions, fires or corrosive damage to materials. Examples under this category include flammable liquids, gases under pressure, oxidising liquids or solids, and self-reactive substances.
Health Hazards Group
The second category in WHMIS 2015 classification is the Health Hazards group. This classification refers to chemicals or substances that pose significant risks to health upon exposure. The exposure might lead to acute or chronic health effects like skin irritation, carcinogenicity, mutagenicity, reproductive toxicity, or aspiration toxicity. It is essential to note that the risks presented by these hazardous substances can manifest immediately after exposure or can take a while to become evident. These hazards are further subdivided based on the exact health hazard they cause.
How WHMIS 2015 Enhances Workplace Safety
The Role of Pictograms in WHMIS 2015
WHMIS 2015 utilises pictograms to easily and globally communicate the dangers posed by various hazardous substances. Pictograms consist of a distinctive symbol inside a red bordered diamond. Each pictogram represents a different hazard classification. Pictograms offer a visual way to swiftly communicate dangers, even before a worker has read the label or safety data sheet. This encourages workers to take the necessary precautions reducing workplace accidents.
Proper Use and Handling of Hazardous Materials
By educating workers about the specific hazards of materials through the WHMIS 2015, employers ensure that everyone is armed with the necessary information to handle such substances appropriately. This knowledge helps workers to use, store, and dispose of hazardous materials correctly, reducing their exposure risk. Being informed about the potential hazards in their work environment, workers can take immediate action in case of accidental exposure, thereby reducing the potential harm.
Creating a Safe and Healthy Work Environment
WHMIS 2015 forms the genesis of creating a safer and healthier work environment. By identifying the hazards and how to handle them, it aids in preventing workplace accidents. This build-up to a safer workplace contributes to increased productivity as workers are healthier and more comfortable in their work environment. Employers can also potentially save costs that could have otherwise been used in handling accidents, illnesses, or compensation.