Who Is Responsible For Whmis

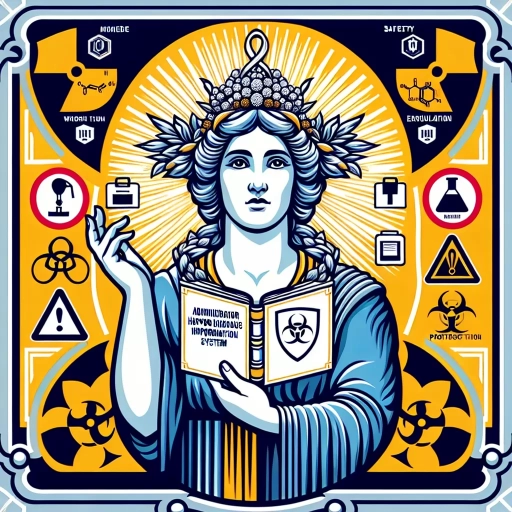
The Workplace Hazardous Materials Information System (WHMIS) is a critical component of workplace safety in Canada, designed to protect workers from the dangers of hazardous materials. Understanding who is responsible for WHMIS is essential for ensuring its effective implementation. This article delves into the key aspects of WHMIS responsibility, starting with an **Overview of WHMIS and Its Importance**, which sets the foundation by explaining the system's purpose and significance. We then explore the **Roles and Responsibilities of Employers Under WHMIS**, highlighting their obligations in providing a safe work environment. Finally, we examine **Employee Responsibilities and Contributions to WHMIS Compliance**, emphasizing the crucial role employees play in maintaining workplace safety. By understanding these interconnected responsibilities, we can better appreciate the comprehensive approach required to ensure WHMIS compliance and safeguard workers' health. Let's begin by examining the overview of WHMIS and its importance.
Overview of WHMIS and Its Importance
The Workplace Hazardous Materials Information System (WHMIS) is a cornerstone of occupational health and safety in Canada, designed to protect workers from the dangers of hazardous materials. Since its inception, WHMIS has undergone significant transformations, reflecting both legislative changes and advancements in safety protocols. This article provides an overview of WHMIS and its importance, delving into three critical aspects: the historical context and evolution of WHMIS, which highlights how the system has adapted over time; the key components and requirements of WHMIS, detailing the essential elements that make it effective; and the impact on workplace safety and health, demonstrating how WHMIS has improved working conditions and reduced risks. By understanding these facets, readers will gain a comprehensive insight into why WHMIS remains a vital tool for ensuring a safe and healthy work environment. This overview will underscore the significance of WHMIS in modern workplaces, emphasizing its role in safeguarding employees and promoting a culture of safety.
Historical Context and Evolution of WHMIS
The Historical Context and Evolution of WHMIS (Workplace Hazardous Materials Information System) are pivotal in understanding its significance and impact on workplace safety. WHMIS was first introduced in Canada in 1988 as a response to the growing concern over the handling and use of hazardous materials in the workplace. This initiative was a collaborative effort between the federal, provincial, and territorial governments, along with labor and industry stakeholders. The primary goal was to ensure that workers were adequately informed about the hazards associated with the chemicals they used, thereby reducing occupational injuries and illnesses. Initially, WHMIS focused on providing standardized labels and material safety data sheets (MSDS) for controlled products. These labels and MSDSs contained critical information such as hazard symbols, risk phrases, and safety precautions. Over the years, WHMIS has undergone significant transformations to align with international standards and address emerging safety concerns. One of the most notable updates was the transition to WHMIS 2015, which harmonized Canada's system with the Globally Harmonized System of Classification and Labelling of Chemicals (GHS). This change introduced new hazard classification criteria, updated label formats, and revised safety data sheets (SDS) to replace MSDS. The evolution of WHMIS has also been influenced by technological advancements and changes in workplace environments. For instance, the rise of digital platforms has facilitated easier access to safety data sheets and training resources. Additionally, there has been an increased emphasis on worker training programs to ensure that employees are equipped with the knowledge necessary to handle hazardous materials safely. Regulatory updates have continued to refine WHMIS, ensuring it remains a robust and effective system. For example, amendments have been made to include new hazard classes and categories, reflecting a more comprehensive understanding of chemical hazards. These updates underscore the commitment to continuous improvement in workplace safety standards. In summary, the historical context and evolution of WHMIS highlight a proactive approach to addressing workplace hazards through standardized information and training. From its inception to its current form, WHMIS has played a crucial role in protecting workers from chemical hazards, making it an indispensable component of occupational health and safety policies in Canada. This ongoing evolution ensures that WHMIS remains relevant and effective in safeguarding the well-being of workers in an ever-changing work environment.
Key Components and Requirements of WHMIS
The Workplace Hazardous Materials Information System (WHMIS) is a critical component of workplace safety in Canada, and understanding its key components and requirements is essential for ensuring compliance and protecting workers. At the heart of WHMIS are three main elements: labels, safety data sheets (SDSs), and worker education and training. **Labels** are affixed to containers of hazardous products and provide immediate information about the hazards associated with the product, including pictograms, hazard statements, and precautionary statements. These labels must adhere to the Globally Harmonized System of Classification and Labelling of Chemicals (GHS) standards, ensuring consistency and clarity. **Safety Data Sheets (SDSs)** are detailed documents that provide comprehensive information about a hazardous product, including its chemical composition, physical and chemical properties, first aid measures, fire-fighting measures, accidental release measures, handling and storage, exposure controls/personal protection, stability and reactivity, toxicological information, ecological information, disposal considerations, transport information, regulatory information, and other relevant data. Employers must ensure that SDSs are readily accessible to workers who handle or are exposed to hazardous products. **Worker Education and Training** is perhaps the most crucial aspect of WHMIS. Employers are responsible for providing workers with training on the safe handling, use, and storage of hazardous products. This training must include how to read and understand labels and SDSs, how to handle spills and emergencies, and the use of personal protective equipment. Regular updates and refresher training are also necessary to ensure that workers remain informed about new hazards and changes in procedures. In addition to these core components, there are several other requirements that employers must fulfill. For instance, employers must conduct hazard assessments to identify which products in their workplace are hazardous and ensure that all such products are properly labeled and have an SDS available. They must also maintain an inventory of hazardous products and ensure that workers are aware of the hazards associated with each product they handle. Furthermore, employers are mandated to review and update their WHMIS program annually or whenever there are changes in the workplace that could affect the safety of workers. This includes reviewing SDSs, updating training programs, and ensuring that all new employees receive the necessary training before they start working with hazardous materials. Compliance with WHMIS regulations is enforced by federal, provincial, and territorial authorities, each having their own set of rules and guidelines. Employers who fail to comply with WHMIS requirements can face significant fines and penalties, highlighting the importance of adhering strictly to these regulations. In summary, the key components and requirements of WHMIS—labels, SDSs, worker education and training—form a robust framework designed to protect workers from the hazards associated with chemical substances in the workplace. By understanding and adhering to these requirements, employers can ensure a safer working environment and comply with legal obligations.
Impact on Workplace Safety and Health
The implementation of the Workplace Hazardous Materials Information System (WHMIS) has a profound impact on workplace safety and health, significantly enhancing the overall well-being of employees and the operational efficiency of organizations. By providing comprehensive information about hazardous materials, WHMIS ensures that workers are adequately informed and trained to handle these substances safely. This system mandates the use of standardized labels and safety data sheets (SDSs) for hazardous products, which helps in identifying potential risks and taking necessary precautions. As a result, workplaces experience a reduction in chemical-related accidents and injuries, leading to a safer working environment. Moreover, WHMIS fosters a culture of safety awareness among employees. By requiring employers to provide regular training and updates on hazardous materials, WHMIS ensures that workers are equipped with the knowledge needed to recognize and mitigate risks. This proactive approach not only protects employees from immediate dangers but also promotes long-term health by minimizing exposure to harmful substances. Additionally, WHMIS compliance often leads to improved housekeeping practices and better storage and disposal methods for hazardous materials, further reducing the risk of accidents and environmental contamination. The impact of WHMIS extends beyond individual safety to influence organizational performance as well. Companies that adhere to WHMIS regulations tend to have lower rates of absenteeism and turnover due to work-related injuries or illnesses. This stability in the workforce contributes to increased productivity and reduced costs associated with worker compensation and medical care. Furthermore, compliance with WHMIS standards can enhance an organization's reputation and credibility, attracting top talent and fostering trust among clients and stakeholders. In summary, the implementation of WHMIS is crucial for maintaining a safe and healthy work environment. By ensuring that workers are well-informed about hazardous materials, WHMIS reduces the risk of accidents, promotes a culture of safety awareness, and contributes to organizational efficiency. As such, it is imperative for employers to take responsibility for implementing and maintaining WHMIS protocols to protect their employees and uphold their commitment to workplace safety and health.
Roles and Responsibilities of Employers Under WHMIS
In the realm of workplace safety, the Workplace Hazardous Materials Information System (WHMIS) plays a crucial role in ensuring that employers and employees are well-equipped to handle hazardous materials safely. Under WHMIS, employers bear significant responsibilities that are pivotal to maintaining a safe and healthy work environment. This article delves into the key roles and responsibilities of employers, focusing on three critical areas: the provision of training and education to ensure that employees are knowledgeable about the hazards they encounter; the maintenance of Safety Data Sheets (SDSs) and labels, which provide essential information about chemical hazards; and the implementation of hazard control measures, which are vital for mitigating risks associated with hazardous materials. By understanding these responsibilities, employers can better comply with WHMIS regulations and foster a culture of safety within their organizations. This comprehensive overview will transition seamlessly into an exploration of WHMIS and its importance, highlighting why these employer responsibilities are fundamental to workplace safety.
Provision of Training and Education
The provision of training and education is a critical component of the roles and responsibilities of employers under the Workplace Hazardous Materials Information System (WHMIS). Employers are mandated to ensure that all workers who handle or are exposed to hazardous materials in the workplace receive comprehensive training. This training must cover the safe handling, use, storage, and disposal of these substances, as well as emergency procedures in case of spills or other incidents. The education program should include detailed information about the hazards associated with each chemical, how to read and understand safety data sheets (SDSs), and how to interpret the information on labels. Employers must also provide training on the use of personal protective equipment (PPE) and ensure that workers understand their roles in maintaining a safe work environment. The training should be tailored to the specific needs of the workplace and the types of hazardous materials present. It is essential that this training is not a one-time event but rather an ongoing process, with regular updates and refresher courses to ensure that workers remain knowledgeable and compliant with WHMIS regulations. Moreover, employers are responsible for ensuring that new employees receive WHMIS training as part of their onboarding process. This initial training should be followed by periodic reviews and updates to reflect any changes in workplace procedures or the introduction of new hazardous materials. Employers must also maintain records of all training provided, including dates, topics covered, and the names of employees who have received the training. Effective training programs under WHMIS not only protect workers from potential health risks but also contribute to a culture of safety within the organization. By investing in thorough education and training, employers can reduce the likelihood of accidents, improve compliance with regulatory requirements, and enhance overall workplace safety. Additionally, well-trained employees are more likely to identify potential hazards and take proactive steps to mitigate risks, thereby contributing to a safer and more efficient work environment. In summary, the provision of training and education is a fundamental responsibility of employers under WHMIS. It involves delivering comprehensive, ongoing training that equips workers with the knowledge and skills necessary to handle hazardous materials safely. By fulfilling this obligation, employers can safeguard their workforce, comply with legal requirements, and foster a workplace culture that prioritizes safety and health.
Maintenance of Safety Data Sheets (SDSs) and Labels
The maintenance of Safety Data Sheets (SDSs) and labels is a critical component of the roles and responsibilities of employers under the Workplace Hazardous Materials Information System (WHMIS). Employers must ensure that all hazardous materials in the workplace are properly identified, labeled, and accompanied by up-to-date SDSs. This involves several key steps. First, employers must verify that each hazardous product has a compliant SDS and label provided by the supplier. These documents must adhere to the strict formatting and content requirements outlined in WHMIS regulations, including detailed information on the product's hazards, safe handling practices, and emergency procedures. Employers are also responsible for ensuring that SDSs are readily accessible to all workers who may be exposed to the hazardous materials. This typically involves maintaining a centralized database or physical file where workers can easily access the SDSs. Additionally, employers should regularly review and update SDSs to reflect any changes in product formulations, new hazard information, or updates in regulatory requirements. Labels on containers must also be checked regularly to ensure they remain legible and compliant with WHMIS standards. Training is another crucial aspect of SDS and label maintenance. Employers must educate workers on how to read and understand SDSs and labels, as well as how to handle and store hazardous materials safely. This training should be part of a comprehensive WHMIS program that includes regular updates and refresher courses to keep workers informed about new hazards and procedures. Furthermore, employers are required to conduct regular audits to ensure compliance with WHMIS regulations. This includes verifying that all hazardous products are properly labeled and that SDSs are current and accessible. Any discrepancies or non-compliance issues must be addressed promptly to maintain a safe working environment. In summary, maintaining accurate and accessible SDSs and labels is a fundamental duty of employers under WHMIS. By ensuring these documents are up-to-date, readily available, and understood by workers, employers can significantly reduce the risks associated with hazardous materials in the workplace. This proactive approach not only helps in preventing accidents but also fosters a culture of safety and compliance within the organization.
Implementation of Hazard Control Measures
The implementation of hazard control measures is a critical component of the roles and responsibilities of employers under the Workplace Hazardous Materials Information System (WHMIS). Employers must ensure that all hazardous materials in the workplace are properly identified, labeled, and communicated to employees through comprehensive training programs. This involves conducting thorough risk assessments to identify potential hazards associated with each material, followed by the development and enforcement of control measures to mitigate these risks. Effective hazard control begins with the classification of hazardous materials according to WHMIS standards, which includes categorizing substances based on their physical and health hazards. Employers must then ensure that all containers holding these substances are correctly labeled with Safety Data Sheets (SDSs) and hazard symbols. These labels serve as immediate warnings to employees about the potential dangers of the materials they are handling. Beyond labeling, employers are responsible for providing detailed training to employees on how to safely handle, store, and dispose of hazardous materials. This training should include information on personal protective equipment (PPE), emergency procedures, and spill response protocols. Employers must also maintain up-to-date SDSs for each hazardous material in the workplace and ensure that these documents are readily accessible to all employees. In addition to training and labeling, employers must implement engineering controls such as ventilation systems, containment structures, and safety barriers to reduce exposure to hazardous substances. Administrative controls, including work procedures and schedules, can also be implemented to minimize the time employees spend handling hazardous materials. For instance, employers might limit the number of employees exposed to a particular substance or restrict access to areas where hazardous materials are used. Regular monitoring and review of hazard control measures are essential to ensure their effectiveness. Employers should conduct periodic inspections to identify any gaps in their safety protocols and make necessary adjustments. This includes reviewing employee feedback and incident reports to continuously improve safety practices. By diligently implementing and maintaining robust hazard control measures, employers not only comply with WHMIS regulations but also create a safer work environment that protects the health and well-being of their employees. This proactive approach to safety underscores the employer's commitment to responsible management of hazardous materials and reinforces their role as guardians of workplace safety under WHMIS.
Employee Responsibilities and Contributions to WHMIS Compliance
In the modern workplace, ensuring compliance with the Workplace Hazardous Materials Information System (WHMIS) is crucial for maintaining a safe and healthy environment. Employee responsibilities play a pivotal role in this compliance, as their actions directly impact the overall safety of the workplace. This article delves into the key contributions employees make to WHMIS compliance, highlighting three critical areas: participation in training programs, adherence to workplace safety protocols, and reporting hazards and incidents. By actively engaging in these aspects, employees not only enhance their own safety but also contribute to a culture of safety that benefits the entire organization. Understanding these responsibilities is essential for fostering a compliant and safe work environment. This introduction sets the stage for a comprehensive overview of WHMIS and its importance, underscoring why employee involvement is indispensable in achieving full compliance.
Participation in Training Programs
Participation in training programs is a crucial aspect of employee responsibilities and contributions to WHMIS (Workplace Hazardous Materials Information System) compliance. Effective training ensures that employees are well-equipped to handle hazardous materials safely, understand the risks associated with these substances, and know how to respond in emergency situations. When employees actively participate in WHMIS training, they gain a comprehensive understanding of the system's key components, including the classification of hazardous products, the interpretation of safety data sheets (SDSs), and the proper use of labels and pictograms. This knowledge empowers them to identify potential hazards, follow safety protocols, and contribute to a safer work environment. Engaged participation in training programs also fosters a culture of safety within the organization. Employees who are committed to learning and adhering to WHMIS guidelines set a positive example for their peers, encouraging a collective responsibility towards workplace safety. Moreover, active participation allows employees to ask questions, share experiences, and provide feedback, which can lead to the continuous improvement of training content and safety practices. This collaborative approach ensures that training is relevant, effective, and tailored to the specific needs of the workplace. Furthermore, employee participation in WHMIS training is not a one-time event but an ongoing process. Regular refresher courses and updates on new regulations or procedures are essential to maintain compliance and ensure that employees remain proficient in handling hazardous materials. By actively participating in these ongoing training sessions, employees demonstrate their commitment to safety and their role in maintaining a compliant workplace. This commitment is critical because it reflects not only individual responsibility but also a broader organizational commitment to safety and compliance. In addition to enhancing individual knowledge and skills, employee participation in WHMIS training contributes significantly to the overall safety culture of the organization. It helps in reducing workplace accidents and injuries related to hazardous materials, thereby protecting both employees and the environment. Employers who encourage and support employee participation in WHMIS training programs also benefit from improved compliance with regulatory requirements, reduced liability, and enhanced operational efficiency. In summary, participation in WHMIS training programs is a fundamental responsibility of employees that underpins their contributions to WHMIS compliance. Through active engagement in these programs, employees acquire essential knowledge, foster a safety-oriented culture, and contribute to a safer and more compliant workplace. This collective effort is indispensable for ensuring that all stakeholders—employees, employers, and the broader community—benefit from a safer and healthier work environment.
Adherence to Workplace Safety Protocols
Adherence to workplace safety protocols is a cornerstone of maintaining a safe and healthy work environment, particularly when it comes to WHMIS (Workplace Hazardous Materials Information System) compliance. Employees play a crucial role in ensuring that these protocols are followed diligently, as their actions directly impact the overall safety culture of the workplace. By adhering to safety protocols, employees not only protect themselves but also their colleagues and the organization as a whole. This involves being well-versed in the handling, storage, and disposal of hazardous materials, as well as understanding the proper use of personal protective equipment (PPE) and emergency response procedures. Employees must take responsibility for reading and understanding the Safety Data Sheets (SDS) provided for each hazardous material they work with. These documents contain critical information about the chemical's properties, hazards, and necessary safety precautions. Additionally, employees should participate actively in training sessions and workshops that focus on WHMIS compliance. These educational opportunities equip them with the knowledge to identify potential hazards and take preventive measures to mitigate risks. Moreover, employees are expected to follow established procedures for labeling and signage of hazardous materials. This includes ensuring that all containers are properly labeled with the required information and that warning signs are posted in areas where hazardous materials are stored or used. Compliance with these labeling requirements helps in quick identification of hazards and facilitates emergency responses. Regular inspections and reporting of any safety issues or near-miss incidents are also integral to maintaining a safe workplace. Employees should be encouraged to report any discrepancies or concerns regarding safety protocols without fear of reprisal. This open communication fosters a culture of transparency and continuous improvement in safety practices. In summary, adherence to workplace safety protocols is a collective responsibility that relies heavily on the active participation of all employees. By staying informed, following established procedures, and contributing to a culture of safety, employees can significantly enhance WHMIS compliance and ensure a safer working environment for everyone. This not only protects individual health but also contributes to the overall well-being and productivity of the organization.
Reporting Hazards and Incidents
Reporting hazards and incidents is a critical component of maintaining a safe and compliant workplace, particularly in the context of WHMIS (Workplace Hazardous Materials Information System) compliance. Employees play a pivotal role in this process, as their vigilance and proactive reporting can prevent accidents, reduce risks, and ensure that all necessary safety measures are implemented. When employees encounter any hazardous situation or incident involving chemicals, they must immediately notify their supervisor or the designated safety officer. This prompt action allows for swift intervention to mitigate potential dangers and initiate an investigation to determine the cause of the incident. Effective reporting involves providing detailed information about the nature of the hazard or incident, including the type of chemical involved, the location, and any injuries or damage sustained. This data is essential for conducting thorough risk assessments and implementing corrective actions to prevent future occurrences. Moreover, accurate and timely reporting helps in updating safety protocols, training programs, and material safety data sheets (MSDS) to reflect new information or emerging risks. Employees' contributions to WHMIS compliance extend beyond mere reporting; they are also responsible for participating in regular training sessions to stay informed about the hazards associated with the chemicals they handle. This knowledge empowers them to identify potential risks proactively and take appropriate precautions. Additionally, employees should be familiar with the labeling system used under WHMIS, which includes pictograms, hazard statements, and precautionary statements that provide crucial information about safe handling practices. By actively engaging in hazard reporting and adhering to WHMIS guidelines, employees contribute significantly to creating a culture of safety within their organization. Their diligence helps in maintaining compliance with regulatory requirements, reducing workplace injuries, and fostering an environment where everyone is committed to preventing accidents and ensuring the well-being of all personnel. Ultimately, the collective responsibility of employees in reporting hazards and incidents is indispensable for achieving comprehensive WHMIS compliance and safeguarding the health and safety of everyone in the workplace.