Where Is Subaru Made

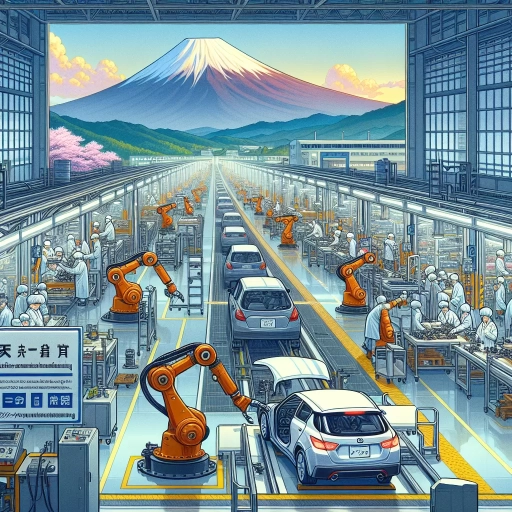
Subaru, a name synonymous with reliability and performance, has a rich history that spans decades. From its humble beginnings to its current status as a global automotive leader, Subaru's journey is marked by innovation and dedication to quality. This article delves into the fascinating story of where Subaru is made, exploring the company's evolution through its manufacturing history, its extensive network of global facilities, and its unwavering commitment to quality control and innovation. We begin by tracing the roots of Subaru's manufacturing prowess in our first section: History of Subaru Manufacturing.
History of Subaru Manufacturing
Subaru, a name synonymous with reliability and innovation in the automotive world, has a rich and fascinating history that spans over a century. From its humble beginnings as a small aircraft manufacturer to its current status as a global leader in the automotive industry, Subaru's journey is marked by significant milestones and groundbreaking innovations. This article delves into the early beginnings and founding of Subaru, tracing its roots back to the early 20th century when it first ventured into aircraft production. It then explores the expansion and growth of the company as it transitioned from aircraft to automobiles, highlighting key decisions and strategies that propelled Subaru forward. Finally, it examines some of the most pivotal milestones and innovations that have defined Subaru's success, including its pioneering work in all-wheel drive technology and commitment to safety. Join us as we explore the history of Subaru manufacturing, uncovering how this Japanese company evolved from a modest start-up to an international powerhouse in the automotive sector.
Early Beginnings and Founding
The early beginnings and founding of Subaru are deeply intertwined with the history of Japan's automotive industry. In 1953, five Japanese companies—Fuji Heavy Industries, Fuji Kogyo, Omiya Fuji Kogyo, Utsunomiya Sharyo, and Tokyo Fuji Sangyo—merged to form Fuji Heavy Industries (FHI). This consolidation was a strategic move to create a robust entity capable of competing in the burgeoning automotive market. The name "Subaru" itself is derived from the Japanese term for the Pleiades star cluster, symbolizing unity and strength among the merged companies. Under the leadership of Kenji Kita, who served as the first president of FHI, Subaru embarked on an ambitious journey to produce vehicles that would not only meet but exceed global standards. The company's initial focus was on manufacturing aircraft parts during World War II; however, post-war economic conditions necessitated a shift towards civilian products. In 1954, Subaru launched its first car model—the P-1—a passenger car designed for comfort and reliability. The 1960s marked a significant turning point for Subaru with the introduction of the Sambar mini-truck in 1961 and the 360 mini-car in 1958. These models were instrumental in establishing Subaru as a major player in Japan's automotive sector. The 360 became particularly popular due to its fuel efficiency and affordability during an era when gasoline was scarce. Subaru continued to innovate throughout the decades. In 1972, it introduced its first all-wheel-drive (AWD) vehicle—the Leone—which revolutionized driving capabilities by providing better traction on various terrains. This technological advancement positioned Subaru uniquely in the market and set it apart from competitors. Throughout its history, Subaru has remained committed to quality manufacturing processes while embracing technological advancements. Today, as part of Subaru Corporation after rebranding from Fuji Heavy Industries in 2017, it continues to produce vehicles known for their reliability and performance across diverse markets worldwide. In summary, Subaru's early beginnings were marked by strategic mergers that laid down a solid foundation for future growth. From humble origins producing aircraft parts to becoming a leading manufacturer of AWD vehicles globally today—Subaru's journey is one of innovation and resilience that has shaped not only its own history but also contributed significantly to Japan's automotive landscape.
Expansion and Growth
Expansion and growth have been pivotal in the history of Subaru manufacturing, transforming the company from a modest beginning to a global automotive powerhouse. In the early years, Subaru focused on producing aircraft parts during World War II, but post-war, it shifted its focus to automotive manufacturing. The first Subaru car, the P-1, was introduced in 1954, marking the beginning of an era that would see rapid expansion and innovation. By the 1960s, Subaru had already established itself as a leader in all-wheel-drive technology with models like the Subaru 360 and Sambar. This technological edge allowed Subaru to expand its market reach beyond Japan. The 1970s saw significant growth with the introduction of iconic models such as the Leone and Brat. These vehicles not only gained popularity domestically but also started making waves internationally. Subaru's commitment to quality and reliability earned it a loyal customer base worldwide. The 1980s brought further expansion with strategic partnerships and investments in new manufacturing facilities both within Japan and abroad. The establishment of Subaru of America in 1968 was a crucial step towards tapping into the lucrative North American market. In the 1990s, Subaru continued its aggressive growth strategy by launching high-performance models like the Impreza WRX and STI variants, which appealed to enthusiasts globally. This period also saw significant investments in research and development leading to advancements in safety features such as Symmetrical All-Wheel Drive (AWD) and EyeSight driver-assist systems. The new millennium brought about even more ambitious plans for expansion. Subaru expanded its manufacturing footprint by opening new plants in countries like China and Thailand while also enhancing existing facilities in Japan and North America. The introduction of crossover SUVs such as Forester and Outback further diversified their product lineup catering to changing consumer preferences towards larger vehicles. Today, Subaru is recognized for its commitment to environmental sustainability through initiatives like zero-landfill manufacturing facilities and eco-friendly production processes. This forward-thinking approach has resonated well with environmentally conscious consumers contributing significantly towards their continued growth trajectory. In conclusion, Subaru's history is a testament to strategic planning, innovative spirit, and relentless pursuit of excellence driving their expansion across decades transforming them into one of world’s leading automobile manufacturers today.
Key Milestones and Innovations
Subaru's manufacturing history is marked by several key milestones and innovations that have shaped the company into what it is today. One of the earliest significant events was the establishment of Fuji Heavy Industries (FHI) in 1953, which would later become the parent company of Subaru. This marked the beginning of a journey that would see Subaru evolve from a small manufacturer to a global automotive brand. In 1954, FHI produced its first car, the P-1, which was a passenger car designed for the Japanese market. This initial foray into automotive manufacturing laid the groundwork for future innovations. The 1960s saw significant advancements with the introduction of the Subaru 360 in 1958, Japan's first mass-produced kei car. This tiny vehicle was designed to meet Japan's strict regulations on size and fuel efficiency, showcasing Subaru's ability to innovate within constraints. The decade also witnessed the launch of the Sambar mini-truck in 1961 and the introduction of all-wheel drive (AWD) technology in 1972 with the Subaru Leone 4WD Estate Wagon. This pioneering use of AWD technology set Subaru apart from competitors and became a hallmark feature of its vehicles. In the 1980s, Subaru continued its innovative streak with advancements in boxer engine technology. The introduction of turbocharged engines further enhanced performance capabilities while maintaining fuel efficiency. The decade also saw significant expansion globally as Subaru began exporting vehicles to North America and Europe. The 1990s were pivotal for Subaru as it introduced models like the Impreza WRX STI, which gained international acclaim for its rally performance capabilities. This period also saw improvements in safety features with advancements in crash testing and airbag technology. In recent years, Subaru has continued to innovate with advancements in hybrid technology and electric vehicles (EVs). The introduction of models like the Crosstrek Hybrid has demonstrated commitment to sustainability while maintaining performance standards. Additionally, investments in autonomous driving technologies are positioning Subaru for future growth in an increasingly tech-driven automotive landscape. Throughout its history, Subaru has remained committed to innovation while staying true to its core values such as safety, reliability, and environmental responsibility. These key milestones not only highlight significant achievements but also underscore how continuous innovation has driven Subaru's success both domestically and internationally.
Global Manufacturing Facilities
In the ever-evolving landscape of global manufacturing, facilities play a pivotal role in driving innovation, efficiency, and quality. This article delves into the world of high-quality manufacturing facilities, highlighting their significance in modern industry. We explore three key aspects: Main Production Plants in Japan, which serve as the backbone of many multinational corporations; International Manufacturing Sites, which underscore the importance of global reach and adaptability; and Specialized Facilities for Specific Models, demonstrating how tailored production can enhance product excellence. By examining these facets, we gain insight into the strategic decisions behind facility placement and specialization. This journey through contemporary manufacturing practices seamlessly transitions into a deeper exploration of the History of Subaru Manufacturing, providing a comprehensive understanding of how one iconic brand has navigated the complexities of global production over time.
Main Production Plants in Japan
Japan is home to several key production plants that are integral to Subaru's global manufacturing operations. The main production facilities in Japan include the Yajima Plant, located in Ota City, Gunma Prefecture, and the Otakita Plant, situated in Ota City as well. These plants are renowned for their advanced manufacturing technologies and rigorous quality control processes. The Yajima Plant is one of Subaru's largest and most technologically advanced facilities. It serves as a primary site for the production of various Subaru models, including the popular Forester and Impreza. The plant boasts state-of-the-art machinery and employs cutting-edge manufacturing techniques to ensure high-quality output. Additionally, it houses extensive research and development (R&D) facilities where engineers continuously innovate and improve Subaru's products. The Otakita Plant complements the Yajima Plant by focusing on the production of other key models such as the Legacy and Outback. This facility is equally equipped with modern machinery and adheres to stringent quality standards. Both plants operate under Subaru's commitment to environmental sustainability, incorporating eco-friendly practices into their operations to minimize environmental impact. Subaru's Japanese production plants are not only significant for their role in manufacturing but also for their contribution to local economies. They provide substantial employment opportunities and stimulate regional economic growth through procurement from local suppliers. Furthermore, these facilities serve as hubs for training programs that enhance the skills of workers, ensuring a highly skilled workforce capable of meeting the demands of modern automotive manufacturing. In summary, Subaru's main production plants in Japan are pivotal components of its global manufacturing strategy. These facilities combine advanced technology with a strong focus on quality and sustainability, making them essential contributors to Subaru's reputation for producing reliable and innovative vehicles.
International Manufacturing Sites
Subaru's global manufacturing facilities are strategically located to meet the demands of a diverse and expanding market. The company's international manufacturing sites play a crucial role in ensuring that high-quality vehicles are produced efficiently and delivered promptly to customers worldwide. In Japan, Subaru's primary manufacturing base is at the Gunma Manufacturing Plant, which serves as the central hub for producing key models such as the Impreza and Legacy. This facility is renowned for its advanced technology and rigorous quality control measures, setting the standard for all other production sites. In addition to its Japanese operations, Subaru has established significant manufacturing presence in other regions. The Subaru of Indiana Automotive (SIA) plant in Lafayette, Indiana, USA, is one of the company's most important international facilities. This plant produces several popular models including the Outback, Legacy, and Impreza. The SIA facility is notable not only for its high production capacity but also for its commitment to environmental sustainability; it was the first automotive assembly plant in the United States to achieve zero landfill status. Subaru also maintains a strong presence in Asia through partnerships with local manufacturers. For instance, the company collaborates with Tan Chong Group in Malaysia to produce vehicles tailored to regional preferences. This strategic partnership allows Subaru to tap into growing markets while leveraging local expertise and resources. Moreover, Subaru's global network extends into Europe where it works closely with European distributors to ensure timely delivery of vehicles across the continent. This collaborative approach enables Subaru to adapt quickly to changing market conditions and consumer preferences. The success of Subaru's international manufacturing sites can be attributed to several factors including advanced production techniques, stringent quality assurance protocols, and a deep understanding of regional market dynamics. By maintaining high standards across all facilities while adapting to local needs, Subaru ensures that every vehicle bearing its name meets the same level of excellence regardless of where it is produced. In summary, Subaru's international manufacturing sites are integral components of its global strategy aimed at delivering top-tier vehicles efficiently and effectively worldwide. Through strategic partnerships and state-of-the-art facilities located in key regions around the globe—whether it be Japan or Indiana—Subaru continues to uphold its reputation as a leader in automotive innovation and quality manufacturing practices.
Specialized Facilities for Specific Models
Subaru's commitment to excellence is exemplified through its specialized facilities dedicated to specific models. These state-of-the-art manufacturing plants are designed to optimize production efficiency and quality, ensuring that each vehicle meets the highest standards. For instance, the Yajima Plant in Ota, Gunma Prefecture, Japan, is renowned for its focus on producing high-performance models such as the WRX and WRX STI. This facility leverages advanced robotics and precision engineering to craft vehicles that embody Subaru's legacy of performance and reliability. In addition to performance-oriented models, Subaru also operates facilities tailored for its family-friendly and eco-conscious offerings. The Ota North Plant, also located in Gunma Prefecture, specializes in manufacturing the Forester and Impreza models. This plant incorporates cutting-edge technology to enhance fuel efficiency and reduce environmental impact while maintaining exceptional safety features—a hallmark of Subaru's design philosophy. Moreover, Subaru's global manufacturing footprint includes facilities outside Japan that cater to regional market demands. The Subaru of Indiana Automotive (SIA) plant in Lafayette, Indiana, USA, is a prime example of this strategic approach. SIA produces a range of popular models including the Outback, Legacy, and Impreza for North American markets. This facility not only adheres to stringent quality control measures but also integrates local supply chains to ensure timely delivery and reduced carbon footprint. The integration of specialized facilities within Subaru's global manufacturing network allows for a more agile response to market trends and consumer preferences. By focusing on specific model lines within dedicated plants, Subaru can refine its production processes continuously. This specialization enables the company to maintain its competitive edge by delivering vehicles that are both technologically advanced and tailored to meet diverse customer needs worldwide. In summary, Subaru's specialized facilities for specific models underscore the company's dedication to innovation and customer satisfaction. By leveraging advanced technology and strategic plant allocation globally, Subaru ensures that every vehicle rolling off its assembly lines embodies the brand's core values of performance, safety, and sustainability—qualities that have earned Subaru a loyal following across continents.
Quality Control and Innovation
In the ever-evolving landscape of modern manufacturing, Quality Control and Innovation stand as the twin pillars that ensure the production of high-quality products while driving technological advancements. This article delves into the intricate relationship between these two concepts, exploring how they shape the manufacturing industry. We will examine the rigorous standards and processes that underpin quality control, highlighting how adherence to these benchmarks ensures consistency and excellence in every product. Additionally, we will discuss the technological advancements that are revolutionizing production processes, enabling faster, more efficient, and precise manufacturing techniques. Finally, we will delve into the quality assurance measures that companies implement to guarantee customer satisfaction and product reliability. By understanding these elements, we can appreciate their impact on industries such as automotive manufacturing—particularly evident in the history of Subaru Manufacturing.
Manufacturing Processes and Standards
Manufacturing processes and standards play a crucial role in ensuring the quality and reliability of Subaru vehicles. At Subaru, adherence to rigorous manufacturing protocols is paramount, reflecting the company's commitment to excellence. The production process begins with meticulous design and engineering, where every detail is scrutinized to meet stringent performance and safety criteria. This phase involves advanced computer-aided design (CAD) systems and simulations to optimize vehicle performance, fuel efficiency, and safety features. Once the design is finalized, the manufacturing process transitions into precision engineering. Subaru employs state-of-the-art machinery and robotics to maintain consistency and accuracy in every component produced. The assembly line is meticulously organized with quality checkpoints at each stage to ensure that every part meets or exceeds industry standards. This includes rigorous testing for durability, reliability, and environmental impact. Quality control is an integral part of Subaru's manufacturing process. Each vehicle undergoes multiple inspections throughout its production cycle. From raw material inspection to final vehicle testing, quality control teams verify that all components meet specified standards. Additionally, Subaru adheres to international quality management systems such as ISO 9001, which provides a framework for continuous improvement in processes and products. Innovation is also a key driver in Subaru's manufacturing processes. The company invests heavily in research and development (R&D), focusing on cutting-edge technologies like all-wheel drive systems and advanced safety features such as EyeSight driver-assist technology. These innovations not only enhance vehicle performance but also contribute significantly to safety improvements. Moreover, Subaru emphasizes sustainability in its manufacturing practices. The company has implemented various initiatives aimed at reducing environmental impact through energy-efficient production methods and waste reduction programs. This commitment aligns with global environmental standards such as ISO 14001 for environmental management systems. In summary, Subaru's manufacturing processes are characterized by a relentless pursuit of excellence through rigorous design protocols, precision engineering, stringent quality control measures, continuous innovation efforts, and sustainable practices. These standards ensure that every Subaru vehicle leaving the factory meets high levels of performance, reliability, and safety while minimizing environmental footprint—qualities that have earned Subaru its reputation for producing exceptional automobiles trusted by drivers worldwide.
Technological Advancements in Production
Technological advancements in production have revolutionized the manufacturing landscape, significantly enhancing efficiency, precision, and innovation. In the context of Subaru's operations, these advancements play a crucial role in maintaining high-quality standards and driving continuous improvement. One notable example is the integration of Industry 4.0 technologies such as artificial intelligence (AI) and machine learning (ML). These technologies enable real-time monitoring and predictive maintenance, allowing for proactive identification and resolution of potential issues before they impact production. Additionally, advanced robotics and automation systems streamline processes, reduce human error, and increase productivity by performing tasks with greater speed and accuracy than manual labor. Another significant technological advancement is the use of data analytics. By leveraging big data and advanced analytics tools, Subaru can analyze vast amounts of information from various stages of production to identify trends, optimize workflows, and make informed decisions. This data-driven approach not only improves quality control but also fosters a culture of continuous innovation by providing insights that can lead to new product features or manufacturing techniques. Furthermore, advancements in digital twin technology allow Subaru to create virtual replicas of their production lines. This enables them to simulate different scenarios without disrupting actual operations, thereby testing new processes or equipment virtually before implementing them physically. This reduces the risk associated with introducing new technologies or methods while ensuring that any changes made are well-optimized for maximum efficiency. Moreover, advancements in materials science have led to the development of lighter yet stronger materials such as carbon fiber reinforced polymers (CFRP). These materials not only contribute to better fuel efficiency but also enhance vehicle safety by providing superior crashworthiness while reducing overall weight. In conclusion, technological advancements in production are pivotal for Subaru’s commitment to quality control and innovation. By embracing cutting-edge technologies like AI, ML, advanced robotics, data analytics, digital twins, and innovative materials science solutions; Subaru ensures that its vehicles meet stringent quality standards while continuously pushing the boundaries of what is possible in automotive manufacturing.
Quality Assurance Measures
Quality Assurance Measures are integral to Subaru's commitment to excellence, ensuring that every vehicle that rolls off the assembly line meets stringent standards of performance, safety, and reliability. Subaru's rigorous quality control processes begin at the design stage, where engineers meticulously plan and test each component to guarantee optimal functionality. This proactive approach involves conducting thorough simulations and physical tests to identify potential issues before they reach production. Once in production, Subaru employs a multi-layered inspection system that includes both automated and manual checks at various stages of assembly. Advanced technologies such as robotic vision systems are utilized to detect even the slightest defects, while trained quality control specialists perform detailed inspections to ensure compliance with industry benchmarks. Subaru also fosters a culture of continuous improvement through employee empowerment and training programs. Workers are encouraged to report any discrepancies or suggestions for process enhancements, fostering an environment where quality is everyone's responsibility. Additionally, Subaru collaborates closely with suppliers to ensure that all materials meet their high standards, conducting regular audits and providing feedback for improvement. The company's dedication to innovation is evident in its adoption of cutting-edge manufacturing techniques such as lean production methods and Industry 4.0 technologies, which streamline processes while maintaining precision. Moreover, Subaru's commitment extends beyond the factory floor; it includes rigorous testing protocols for finished vehicles. Each car undergoes comprehensive testing under various conditions—ranging from extreme weather scenarios to rigorous performance tests—to validate its durability and reliability. This holistic approach ensures that every Subaru model not only meets but exceeds customer expectations in terms of quality and performance. In summary, Subaru's Quality Assurance Measures are a cornerstone of its success story. By integrating advanced technology with meticulous human oversight at every stage—from design through delivery—Subaru consistently delivers vehicles that embody excellence in engineering and craftsmanship. This unwavering focus on quality underscores why Subaru remains a trusted name in the automotive industry worldwide.