Where Are Toyotas Made

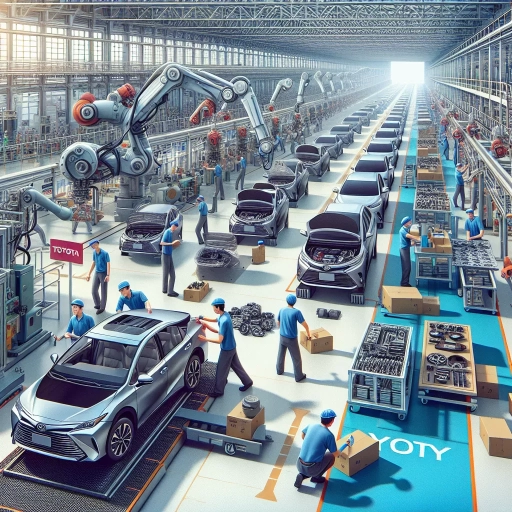
Toyota, one of the world's leading automobile manufacturers, has a rich history and a global presence that spans across multiple continents. The company's commitment to quality and innovation is evident in its extensive network of manufacturing facilities, sophisticated production processes, and cutting-edge technological advancements. This article delves into the intricacies of where Toyotas are made, exploring the global manufacturing facilities that serve as the backbone of Toyota's operations. We will also provide an overview of the production process that ensures each vehicle meets stringent quality standards. Additionally, we will examine the technological innovations that have revolutionized Toyota's manufacturing practices. By understanding these aspects, readers can gain a comprehensive insight into what makes Toyota a leader in the automotive industry. Let us begin by examining the global manufacturing facilities that are pivotal to Toyota's success.
Global Manufacturing Facilities
In the ever-evolving landscape of global manufacturing, facilities around the world are playing a pivotal role in shaping the future of production. From North American plants that leverage advanced technology and robust infrastructure to Asian production hubs known for their efficiency and scalability, each region brings unique strengths to the table. Meanwhile, European manufacturing sites are renowned for their emphasis on innovation and sustainability. This article delves into these diverse yet interconnected facets of global manufacturing facilities, exploring how they collectively drive industry trends and economic growth. By examining these regional powerhouses—North American Plants, Asian Production Hubs, and European Manufacturing Sites—we gain a comprehensive understanding of the complex dynamics at play in modern global manufacturing facilities.
North American Plants
North American plants play a crucial role in Toyota's global manufacturing facilities, contributing significantly to the company's production capacity and innovation. Located strategically across the United States, Canada, and Mexico, these plants leverage advanced technology and skilled workforce to produce a wide range of vehicles. The Toyota Motor Manufacturing Kentucky (TMMK) in Georgetown, Kentucky, for instance, is one of the largest Toyota manufacturing facilities outside Japan. It produces models such as the Camry and Avalon while also serving as a hub for engineering and research. Similarly, the Toyota Motor Manufacturing Indiana (TMMI) in Princeton, Indiana, focuses on producing SUVs like the Highlander and Sequoia. In Canada, Toyota's plant in Cambridge, Ontario, is renowned for its high-quality production of Corolla and Lexus RX models. Mexico's TMMBC (Toyota Motor Manufacturing Baja California) adds to this robust network by manufacturing Tacoma trucks and other key models. These North American plants not only contribute to Toyota's global output but also drive local economies through job creation and community engagement. They adhere to stringent quality standards while incorporating sustainable practices into their operations. For example, many of these facilities have implemented green initiatives such as solar power installations and water conservation programs. Additionally, they foster innovation by integrating cutting-edge technologies like robotics and artificial intelligence into their manufacturing processes. The strategic location of these plants allows for efficient supply chain management and quicker delivery times to regional markets. This proximity also enables closer collaboration with local suppliers which helps in maintaining high-quality standards across all products. Furthermore, these facilities serve as centers for training and development where employees can hone their skills through continuous learning programs. In summary, North American plants are integral components of Toyota's global manufacturing network. They combine technological prowess with environmental responsibility while contributing significantly to regional economic growth. As Toyota continues to expand its operations globally, these North American facilities remain pivotal in ensuring the company's commitment to quality and innovation remains unwavering.
Asian Production Hubs
Asian production hubs have emerged as pivotal in the global manufacturing landscape, particularly for multinational corporations like Toyota. Countries such as China, Japan, South Korea, and Thailand have become hotspots for industrial activity due to their strategic locations, favorable economic policies, and highly skilled workforces. In China, for instance, cities like Shanghai and Guangzhou host numerous manufacturing facilities that leverage the country's vast market and extensive supply chain networks. Japan remains a cornerstone of automotive production with Toyota's headquarters in Toyota City serving as a hub for innovation and quality control. South Korea's industrial belt around Seoul is home to giants like Hyundai and Kia, while Thailand's Eastern Economic Corridor (EEC) has attracted significant investment from automotive manufacturers due to its competitive labor costs and robust infrastructure. These hubs offer a blend of modern technology and traditional craftsmanship that ensures high-quality output while maintaining cost efficiency. The presence of comprehensive logistics systems facilitates smooth supply chain operations, enabling companies to meet global demand promptly. Additionally, these regions often benefit from government incentives aimed at fostering economic growth through industrial development. For example, Thailand's Board of Investment (BOI) provides tax breaks and other benefits to encourage foreign investment in key sectors including automotive manufacturing. The concentration of production facilities in these areas also fosters an ecosystem where suppliers can easily integrate into the manufacturing process. This proximity allows for real-time collaboration between component manufacturers and final assembly lines, enhancing overall efficiency and product reliability. Furthermore, these hubs are often supported by extensive research and development (R&D) capabilities which drive innovation within the industry. Toyota itself has capitalized on this trend by establishing major production bases across Asia. Its operations in Japan are complemented by significant investments in China where it partners with local companies such as FAW Group Corporation to produce vehicles tailored for the Chinese market. Similarly, Toyota’s presence in Thailand includes both passenger car assembly plants as well as engine manufacturing facilities that serve regional markets. In summary, Asian production hubs play a crucial role in global manufacturing by offering a unique combination of strategic advantages that support high-volume production with precision quality standards. As companies continue to expand their operations within this region, it is clear that Asia will remain at the forefront of industrial production for years to come.
European Manufacturing Sites
Toyota's European manufacturing sites are a cornerstone of the company's global production strategy, showcasing cutting-edge technology and operational excellence. Located in key markets across the continent, these facilities not only produce a wide range of Toyota models but also serve as hubs for innovation and sustainability. The Toyota Manufacturing UK (TMUK) plant in Burnaston, Derbyshire, is one of the most prominent sites, producing models such as the Corolla and Avensis. This facility has been at the forefront of adopting advanced manufacturing techniques and has received numerous awards for its commitment to quality and environmental responsibility. In France, Toyota's Valenciennes plant specializes in producing the Yaris model, leveraging local expertise to ensure high standards of craftsmanship. This site has been instrumental in integrating new technologies into production processes, enhancing efficiency while maintaining Toyota's renowned quality standards. Similarly, the Toyota Motor Manufacturing Poland (TMMP) facility in Jelcz-Laskowice focuses on engine production, supplying units to various Toyota plants across Europe. This site exemplifies Toyota's commitment to regional specialization and supply chain optimization. Germany hosts several significant Toyota operations, including logistics centers that play a crucial role in managing the flow of parts and finished vehicles throughout Europe. These centers utilize sophisticated inventory management systems to ensure timely deliveries and minimize environmental impact through efficient transportation practices. In addition to these manufacturing hubs, Toyota's European network includes numerous research and development centers where engineers work tirelessly to innovate new technologies that will shape the future of automotive manufacturing. For instance, the Toyota Technical Centre Europe (TTCE) in Zaventem, Belgium, focuses on developing advanced powertrain technologies and improving vehicle safety features. Overall, Toyota's European manufacturing sites embody the company's vision for sustainable growth and technological advancement while contributing significantly to local economies through job creation and community engagement initiatives. As part of Toyota's global manufacturing facilities network, these European operations underscore the company's dedication to producing high-quality vehicles that meet diverse market needs while adhering to stringent environmental standards.
Production Process Overview
In the dynamic landscape of modern manufacturing, understanding the production process is crucial for efficiency, innovation, and quality. This article provides a comprehensive overview of the key phases involved in transforming raw materials into finished products. We delve into the Design and Prototyping Phase, where creativity meets precision to create initial product designs and test prototypes. Next, we explore Assembly Line Operations, highlighting how streamlined workflows and advanced machinery ensure consistent production. Finally, we discuss Quality Control Measures that safeguard product reliability and customer satisfaction. By examining these critical stages, manufacturers can optimize their processes to meet global standards. This knowledge is particularly relevant for Global Manufacturing Facilities, where maintaining high standards is essential for success in a competitive market.
Design and Prototyping Phase
In the Design and Prototyping Phase of Toyota's production process, meticulous attention to detail and innovative thinking come to the forefront. This critical stage is where conceptual ideas transform into tangible, functional designs that meet stringent quality and performance standards. The journey begins with thorough market research and customer feedback analysis to identify emerging trends and consumer needs. Designers then leverage advanced computer-aided design (CAD) software to create detailed digital models, ensuring precision in every aspect of the vehicle's architecture. Collaboration between cross-functional teams—comprising engineers, designers, and manufacturing specialists—is paramount during this phase. Regular brainstorming sessions foster a culture of continuous improvement, allowing for the integration of cutting-edge technologies and sustainable practices. Prototyping involves the creation of scale models or mock-ups that undergo rigorous testing for aerodynamics, structural integrity, and user experience. These prototypes are often subjected to simulated real-world conditions in state-of-the-art testing facilities to validate their performance. Toyota's commitment to quality is evident in its rigorous testing protocols. The company employs advanced simulation tools such as computational fluid dynamics (CFD) for aerodynamic analysis and finite element analysis (FEA) for structural assessments. Additionally, human-centered design principles guide the development process to ensure that vehicles are not only aesthetically pleasing but also intuitive and comfortable for users. The iterative nature of prototyping allows for continuous refinement based on feedback from both internal stakeholders and external partners. This iterative cycle ensures that any design flaws or inefficiencies are addressed early on, reducing potential issues during mass production. By combining traditional craftsmanship with modern technological advancements, Toyota maintains its reputation for producing high-quality vehicles that excel in both form and function. Ultimately, the Design and Prototyping Phase sets the foundation for a seamless transition into subsequent stages of production. It is here that visionary concepts take shape as practical solutions tailored to meet evolving market demands while adhering to Toyota's unwavering commitment to excellence.
Assembly Line Operations
Assembly line operations are a cornerstone of modern manufacturing, particularly in the automotive industry. This method, pioneered by Henry Ford in the early 20th century, revolutionized production by breaking down complex tasks into simpler, repetitive steps that workers could perform efficiently. In Toyota's manufacturing process, assembly lines are meticulously organized to ensure maximum productivity and quality control. Each station along the line is equipped with specialized tools and machinery designed to handle specific tasks such as welding, painting, and engine installation. Workers at each station are trained to perform their tasks with precision and speed, allowing for a smooth flow of production. The efficiency of Toyota's assembly lines is further enhanced by their commitment to continuous improvement through the Kaizen philosophy. This approach encourages employees at all levels to identify areas for improvement and implement changes that can streamline processes or enhance product quality. Additionally, Toyota employs advanced technologies like robotics and automation to handle tasks that require high precision or repetitive labor, freeing human workers to focus on more complex tasks that require creativity and problem-solving skills. Quality control is another critical aspect of Toyota's assembly line operations. The company implements rigorous inspection protocols at various stages of production to ensure that every vehicle meets stringent quality standards before it leaves the factory. This includes both automated systems that check for defects in real-time and manual inspections conducted by experienced quality control specialists. Moreover, Toyota's just-in-time (JIT) inventory system plays a crucial role in maintaining the efficiency of their assembly lines. By ordering components just in time for their use in production, Toyota minimizes inventory costs and reduces waste while ensuring that all necessary parts are available when needed. This approach also allows for greater flexibility in responding to changes in demand or supply chain disruptions. In summary, Toyota's assembly line operations exemplify a blend of traditional manufacturing techniques with modern technological advancements and innovative management philosophies. By combining specialized labor with advanced machinery and emphasizing continuous improvement and quality control, Toyota maintains its position as a leader in automotive manufacturing efficiency and product reliability.
Quality Control Measures
Quality control measures are an integral part of Toyota's production process, ensuring that every vehicle meets the highest standards of reliability, performance, and safety. At Toyota, quality control is not just a phase but a continuous process that permeates every stage of manufacturing. From the initial design phase to the final assembly line, rigorous checks and inspections are conducted to identify and rectify any potential issues before they escalate. This proactive approach involves both automated systems and human oversight, leveraging advanced technologies like robotic inspection tools and data analytics to monitor production in real-time. Additionally, Toyota employs the Total Productive Maintenance (TPM) philosophy, which emphasizes preventive maintenance to minimize downtime and ensure that all equipment operates at optimal levels. The company also fosters a culture of continuous improvement through its Kaizen principles, encouraging employees to identify areas for enhancement and implement changes that can improve efficiency and quality. Furthermore, Toyota's supplier network is meticulously vetted to ensure that all components meet stringent quality standards before being integrated into the manufacturing process. This comprehensive approach ensures that every Toyota vehicle rolling off the assembly line is not only reliable but also exceeds customer expectations in terms of performance and durability. By integrating quality control seamlessly into every aspect of production, Toyota maintains its reputation as a leader in automotive manufacturing while consistently delivering high-quality products to its global customer base.
Technological Innovations in Toyota Manufacturing
In the ever-evolving landscape of automotive manufacturing, Toyota stands at the forefront of technological innovation. The company's commitment to excellence is evident in its integration of cutting-edge technologies that enhance efficiency, sustainability, and product quality. This article delves into three pivotal areas where Toyota has made significant strides: Robotics and Automation, Sustainable Production Practices, and Advanced Material Usage. By leveraging robotics and automation, Toyota has streamlined its production processes, ensuring precision and speed while minimizing human error. The company's focus on sustainable production practices not only reduces environmental impact but also fosters a healthier workplace environment. Additionally, the adoption of advanced materials has allowed Toyota to create lighter yet stronger vehicles that meet stringent safety standards while improving fuel efficiency. These innovations are not limited to local facilities; they have a profound impact on global manufacturing facilities as well.
Robotics and Automation
In the realm of technological innovations, Toyota Manufacturing has been at the forefront of integrating robotics and automation to enhance efficiency, precision, and productivity. Robotics and automation play a pivotal role in modern manufacturing processes, enabling companies like Toyota to maintain their competitive edge. By leveraging advanced robotic systems, Toyota can streamline production lines, reduce labor costs, and ensure consistent quality across all products. These robots are equipped with sophisticated sensors and AI algorithms that allow them to perform complex tasks with high accuracy and speed. For instance, robotic arms are used for welding, painting, and assembly operations where precision is paramount. Additionally, autonomous mobile robots (AMRs) navigate through factories to transport parts and materials efficiently without human intervention. The integration of these technologies not only boosts production capacity but also improves workplace safety by minimizing the risk of accidents associated with manual labor. Furthermore, data analytics from these automated systems provide valuable insights into production metrics which can be used for continuous improvement initiatives. Overall, Toyota's embrace of robotics and automation underscores its commitment to innovation and excellence in manufacturing processes.
Sustainable Production Practices
Sustainable production practices are a cornerstone of Toyota's manufacturing philosophy, aligning with the company's commitment to environmental stewardship and social responsibility. At Toyota, sustainability is not merely a buzzword but an integral part of their operational DNA. The company has implemented various innovative technologies and processes to minimize its ecological footprint while maintaining high standards of quality and efficiency. One notable example is the use of renewable energy sources such as solar and wind power in their facilities, significantly reducing reliance on fossil fuels and lowering greenhouse gas emissions. Additionally, Toyota has adopted advanced water conservation techniques, including rainwater harvesting systems and efficient irrigation methods, to ensure responsible water management. Toyota's commitment to sustainability extends beyond energy and water conservation. The company has also made substantial investments in waste reduction and recycling programs. By implementing a "zero waste to landfill" policy at many of its plants, Toyota ensures that all waste materials are either recycled or reused in some form. This not only reduces landfill waste but also fosters a culture of resourcefulness among employees. Moreover, Toyota's focus on sustainable production practices includes the development and use of eco-friendly materials in vehicle manufacturing. The company has been at the forefront of researching and integrating recycled materials into their products without compromising performance or safety standards. For instance, Toyota's hybrid vehicles feature components made from recycled plastics, reducing the demand for virgin raw materials and contributing to a circular economy. Another significant aspect of Toyota's sustainable production practices is their emphasis on reducing emissions throughout the entire lifecycle of their vehicles—from design through end-of-life recycling. This includes optimizing manufacturing processes to reduce energy consumption during production phases as well as designing vehicles with recyclability in mind from the outset. Furthermore, technological innovations play a crucial role in enhancing sustainability at Toyota's manufacturing facilities. Advanced robotics and automation systems help streamline production processes while minimizing human error and reducing waste generation. Data analytics tools enable real-time monitoring of energy usage patterns across different departments within a plant, allowing for swift identification and rectification of inefficiencies. In conclusion, Toyota's dedication to sustainable production practices underscores their vision for a greener future where technological advancements harmonize with environmental stewardship without compromising on quality or efficiency. By integrating cutting-edge technologies into every facet of their operations—from renewable energy sources to eco-friendly materials—Toyota sets a high standard for responsible manufacturing practices that other industries can aspire to emulate.
Advanced Material Usage
In the realm of technological innovations, Toyota's manufacturing processes have been significantly enhanced by the strategic integration of advanced materials. These cutting-edge materials not only improve the performance and efficiency of vehicles but also contribute to sustainability and environmental responsibility. For instance, Toyota has embraced the use of lightweight yet robust materials such as carbon fiber and advanced high-strength steel in their vehicle designs. These materials reduce overall weight while maintaining structural integrity, leading to better fuel efficiency and reduced emissions. Additionally, Toyota has incorporated advanced composites in various components, which provide superior durability and resistance to corrosion compared to traditional materials. The use of advanced ceramics is another notable innovation in Toyota's manufacturing arsenal. These materials are utilized in components like engine parts and exhaust systems due to their exceptional heat resistance and wear properties. This results in improved engine performance, longer component lifespan, and reduced maintenance costs for consumers. Furthermore, Toyota has been at the forefront of integrating nanomaterials into their manufacturing processes. Nanomaterials enhance the properties of conventional materials by improving their strength-to-weight ratio and thermal conductivity. Moreover, Toyota's commitment to sustainability is evident through their adoption of eco-friendly materials such as bioplastics derived from renewable resources like corn starch or sugarcane molasses. These bioplastics are used in interior components like dashboards and trim pieces, offering a more environmentally friendly alternative without compromising on quality or aesthetics. The integration of advanced materials also extends beyond vehicle production itself; it influences the entire lifecycle management approach adopted by Toyota. For example, recyclable materials are increasingly being used across various models to ensure that end-of-life vehicles can be efficiently recycled or repurposed with minimal environmental impact. In summary, Toyota's innovative use of advanced materials represents a pivotal aspect of their technological advancements in manufacturing. By leveraging these cutting-edge resources effectively across different stages—from design through production—to end-of-life management, Toyota continues to set industry benchmarks for both performance excellence and environmental stewardship.