Where Is Nissan Made

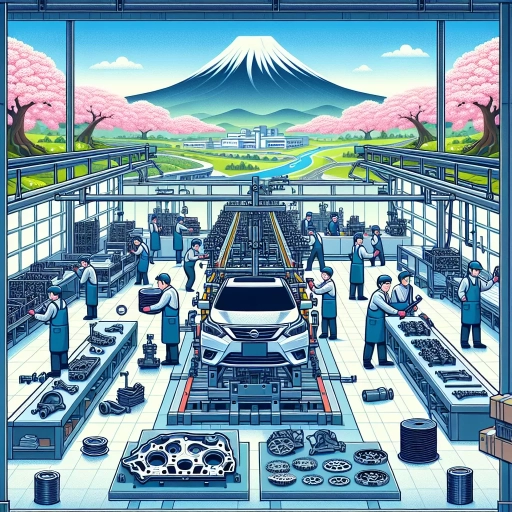
Nissan, one of the world's leading automotive manufacturers, has a rich history and a global footprint that spans across multiple continents. The company's journey from its humble beginnings in Japan to becoming a multinational giant is a testament to its commitment to innovation and quality. This article delves into the various facets of Nissan's manufacturing prowess, starting with an overview of its extensive global manufacturing facilities. We will explore how these facilities operate and contribute to the company's global presence. Additionally, we will delve into the historical development of Nissan's manufacturing processes, tracing the evolution from its early days to the present. Finally, we will examine the rigorous quality control measures and innovative practices that set Nissan apart in the automotive industry. By understanding these aspects, readers can gain a comprehensive insight into what makes Nissan a leader in car production. Let us begin by exploring Nissan's global manufacturing facilities.
Global Manufacturing Facilities
In today's interconnected world, global manufacturing facilities play a pivotal role in the production and distribution of goods. These facilities are not just operational hubs but also strategic centers that drive economic growth and innovation. This article delves into the intricacies of global manufacturing by focusing on Nissan's extensive presence across the globe. We begin with an overview of Nissan's global presence, highlighting its history, expansion strategies, and market influence. Next, we explore key manufacturing plants around the world, detailing their capabilities and contributions to Nissan's overall production output. Finally, we examine regional specialization and production volumes, shedding light on how different regions specialize in specific types of vehicles and components. By understanding these aspects of Nissan's operations, we gain valuable insights into the broader landscape of global manufacturing facilities.
1. Overview of Nissan's Global Presence
Nissan's global presence is a testament to its commitment to innovation and customer satisfaction. With a rich history spanning over a century, Nissan has evolved from a small Japanese automaker into a multinational corporation with operations in nearly every corner of the globe. The company's extensive network includes manufacturing facilities, research and development centers, and sales offices across six continents. In North America, Nissan operates major manufacturing plants in Tennessee and Mississippi, producing popular models like the Altima and Titan. In Europe, facilities in the UK and Spain contribute significantly to the region's automotive industry. Asia remains a crucial hub for Nissan, with Japan being home to several key plants that produce both domestic and export models. Additionally, China has emerged as a significant market for Nissan, with joint ventures such as Dongfeng Nissan contributing to the country's burgeoning automotive sector. The company also maintains a strong presence in Latin America through its Mexican operations. This widespread global footprint not only allows Nissan to cater to diverse regional preferences but also enables it to leverage local expertise and resources effectively. By integrating global best practices with regional insights, Nissan ensures that its products meet the highest standards of quality while addressing specific market needs efficiently. This strategic approach has been instrumental in establishing Nissan as one of the world's leading automakers, known for its reliability, performance, and innovative design.
2. Key Manufacturing Plants Around the World
Nissan's global manufacturing footprint is a testament to the company's commitment to quality and innovation. Two key manufacturing plants around the world that exemplify this dedication are the Sunderland Plant in the UK and the Smyrna Plant in Tennessee, USA. The Sunderland Plant, located in northeast England, is one of Nissan's most successful and efficient facilities. Established in 1986, it has produced over 10 million vehicles to date, making it one of the largest car plants in Europe. This plant is renowned for its high productivity and has been recognized with numerous awards for quality and environmental sustainability. It currently produces models such as the Qashqai and Juke, which are popular not only in Europe but also globally. In contrast, the Smyrna Plant in Tennessee has been a cornerstone of Nissan's North American operations since its inception in 1983. This facility has undergone significant expansions over the years to meet growing demand for Nissan vehicles. It is known for producing a wide range of models including Altima, Maxima, Leaf (the world's best-selling electric vehicle), Pathfinder, and Rogue. The Smyrna Plant stands out for its innovative manufacturing processes and commitment to community engagement. It has implemented advanced technologies like robotic assembly lines and energy-efficient systems to enhance production efficiency while minimizing environmental impact. Both plants reflect Nissan's strategy of locating production close to key markets while leveraging local talent and resources. They serve as hubs for research and development as well as training centers for employees across different regions. By maintaining high standards of quality control and investing heavily in technology upgrades at these facilities, Nissan ensures that its products meet stringent global standards while also contributing positively to local economies through job creation and community development initiatives. The success of these plants underscores Nissan's ability to adapt to changing market conditions while maintaining a strong focus on innovation and customer satisfaction. As part of Nissan's broader global manufacturing network, these facilities play a crucial role in ensuring that the company remains competitive on an international scale by delivering high-quality vehicles that meet diverse consumer needs worldwide.
3. Regional Specialization and Production Volumes
Nissan's global manufacturing strategy is characterized by regional specialization and production volumes, ensuring efficiency and quality across its diverse product lineup. This approach allows Nissan to leverage local expertise, reduce costs, and cater to regional market preferences effectively. For instance, the company's Sunderland plant in the UK specializes in producing models like the Qashqai and Juke, which are highly popular in Europe. This focus on regional demand enables Nissan to maintain high production volumes while tailoring its offerings to meet specific consumer needs. In Japan, Nissan's facilities are dedicated to producing high-performance vehicles such as the GT-R and advanced electric cars like the Leaf. These models benefit from Japan's cutting-edge technology and skilled workforce, ensuring they meet the highest standards of innovation and quality. The Japanese plants also serve as hubs for research and development, driving technological advancements that are then integrated into other global facilities. In North America, Nissan's manufacturing footprint includes significant operations in Tennessee and Mississippi. The Smyrna plant in Tennessee is one of the largest automotive manufacturing facilities in North America, producing a range of models including the Altima, Maxima, and Pathfinder. This plant benefits from proximity to major markets and access to a large workforce with extensive automotive experience. Similarly, Nissan's Mexican facilities focus on producing smaller vehicles such as the Versa and Sentra for both domestic consumption and export to other regions. By concentrating on these models in Mexico, Nissan can take advantage of favorable labor costs while maintaining high production volumes that meet growing demand for compact cars globally. Overall, Nissan's strategy of regional specialization combined with optimized production volumes ensures that each facility operates at peak efficiency while delivering products that resonate with local consumers. This balanced approach not only enhances operational efficiency but also fosters innovation by leveraging regional strengths in technology, labor expertise, and market understanding.
Historical Development of Nissan's Manufacturing
Nissan, one of the world's leading automobile manufacturers, has a rich and dynamic history that spans over a century. From its humble beginnings in Japan to its current status as a global automotive powerhouse, Nissan's journey is marked by significant milestones and strategic transformations. This article delves into the historical development of Nissan's manufacturing, exploring three pivotal phases: Early Beginnings and Expansion in Japan, Post-War Rebuilding and International Expansion, and Modernization and Technological Advancements. Each phase highlights key events, innovations, and decisions that have shaped the company's trajectory. By examining these critical periods, we gain insight into how Nissan evolved from a domestic player to a global leader with extensive manufacturing facilities around the world.
1. Early Beginnings and Expansion in Japan
Nissan's journey in Japan began in 1933 when Jidosha-Seizo Co., Ltd. was established in Yokohama. This marked the early beginnings of what would eventually become one of the world's leading automobile manufacturers. The company's name was later changed to Nissan Motor Co., Ltd. in 1934, reflecting its broader ambitions and commitment to innovation. During its formative years, Nissan focused on producing trucks and passenger cars, leveraging advanced technologies from its American partners to enhance quality and efficiency. The post-World War II era saw significant expansion for Nissan as it began to rebuild and modernize its operations. In 1952, the company introduced the Datsun brand, which quickly gained popularity both domestically and internationally for its reliability and affordability. This strategic move not only helped Nissan regain its footing but also paved the way for global market penetration. The 1960s were particularly transformative as Nissan launched several iconic models such as the Datsun 240Z sports car, which became a symbol of Japanese automotive excellence. Throughout the 1970s and 1980s, Nissan continued to expand its manufacturing capabilities by establishing new plants across Japan. This period also saw significant investments in research and development, leading to breakthroughs in fuel efficiency, safety features, and design aesthetics. The introduction of models like the Nissan Sunny (Datsun 210) further solidified Nissan's position as a major player in both domestic and international markets. In addition to technological advancements, Nissan's growth was also driven by strategic partnerships and collaborations. The alliance with Renault in 1999 brought about a new era of cooperation that enhanced Nissan's global reach while fostering innovation through shared resources and expertise. This partnership enabled Nissan to diversify its product lineup with models such as the Qashqai crossover SUV, which appealed to a broader audience worldwide. Today, Nissan remains a cornerstone of Japan's automotive industry with state-of-the-art facilities spread across various regions including Tochigi Prefecture where its flagship plant is located. The company continues to innovate with electric vehicles like the Leaf while maintaining its commitment to quality manufacturing processes that have defined its legacy since its inception nearly a century ago.
2. Post-War Rebuilding and International Expansion
In the aftermath of World War II, Nissan embarked on a transformative journey of post-war rebuilding and international expansion. The company's resilience and strategic vision were pivotal in navigating the challenges posed by the devastation of war. Nissan's manufacturing facilities had been severely damaged, but under the leadership of Yoshisuke Aikawa, who returned to the helm in 1947, the company began a meticulous process of reconstruction. This period saw significant investments in modernizing production lines and adopting advanced technologies to enhance efficiency and quality. Nissan's international expansion was another key focus during this era. Recognizing the importance of global markets, Nissan initiated its first overseas venture with the establishment of Nissan Motor Co., Ltd. in the United States in 1958. This move marked a significant milestone as it not only expanded Nissan's reach but also positioned it as a major player in the global automotive industry. The company continued to expand its international footprint by setting up operations in various regions including Europe and Asia. The 1960s were particularly transformative for Nissan as it introduced several iconic models that would become synonymous with reliability and performance. The Datsun 240Z, launched in 1969, was one such model that garnered international acclaim for its sleek design and powerful engine. This period also saw Nissan strengthen its partnerships with other automotive companies, fostering collaborative efforts that drove innovation and competitiveness. Nissan's commitment to innovation extended beyond vehicle design; it also embraced cutting-edge manufacturing techniques. The introduction of robotics and automation significantly improved production efficiency while maintaining high standards of quality control. Additionally, Nissan invested heavily in research and development (R&D), establishing state-of-the-art facilities that enabled continuous improvement in vehicle technology. The company's dedication to environmental sustainability also became more pronounced during this time. Nissan began exploring alternative fuel sources and developing eco-friendly technologies aimed at reducing carbon emissions from its vehicles. This forward-thinking approach not only aligned with growing global concerns about environmental impact but also positioned Nissan as a leader in sustainable automotive practices. Throughout its post-war rebuilding phase, Nissan remained steadfast in its mission to deliver exceptional products while expanding its global presence. By combining innovative manufacturing practices with strategic international expansion efforts, Nissan successfully transitioned from a domestic Japanese brand into a globally recognized automotive powerhouse. This legacy continues to shape the company's trajectory today as it remains committed to innovation, sustainability, and delivering high-quality vehicles worldwide.
3. Modernization and Technological Advancements
Modernization and technological advancements have been pivotal in the historical development of Nissan's manufacturing processes. The company's journey into modernization began in the post-war era, where it embraced cutting-edge technologies to revamp its production lines. Nissan introduced the first robotic welding line in 1968, significantly enhancing efficiency and precision. This early adoption of automation set a precedent for future innovations, such as the implementation of advanced computer-aided design (CAD) systems and computer-aided manufacturing (CAM) processes. In the 1980s, Nissan further accelerated its modernization efforts by establishing state-of-the-art manufacturing facilities. The introduction of flexible manufacturing systems (FMS) allowed for greater versatility in production, enabling the company to produce multiple models on a single line efficiently. This flexibility was crucial during periods of fluctuating market demands and helped Nissan maintain competitive edge. The advent of the 21st century saw Nissan diving deeper into digital transformation with the integration of Industry 4.0 technologies. The company leveraged artificial intelligence (AI), machine learning (ML), and big data analytics to optimize production workflows and improve quality control. For instance, AI-powered predictive maintenance systems were implemented to detect potential equipment failures before they occurred, thereby reducing downtime and increasing overall plant productivity. Moreover, Nissan has been at the forefront of adopting sustainable technologies aimed at reducing environmental impact while enhancing operational efficiency. The introduction of solar power generation at several plants worldwide exemplifies this commitment towards green manufacturing practices. Additionally, advancements in electric vehicle technology have positioned Nissan as a leader in sustainable mobility solutions with models like the Leaf becoming benchmarks for eco-friendly automotive innovation. In conclusion, modernization and technological advancements have played a transformative role in shaping Nissan's manufacturing prowess over decades. From early robotics to current AI-driven processes, these innovations have not only improved production efficiency but also aligned with global trends towards sustainability and digitalization—solidifying Nissan’s position as a forward-thinking leader within the automotive industry.
Quality Control and Innovation in Manufacturing
In the dynamic landscape of modern manufacturing, quality control and innovation are paramount for maintaining competitive edge and ensuring customer satisfaction. This article delves into the cutting-edge strategies employed by leading manufacturers to achieve these goals. We explore advanced manufacturing technologies used by Nissan, which have revolutionized production processes and significantly enhanced product quality. Additionally, we examine the rigorous quality assurance processes implemented across various facilities to ensure consistency and excellence in every product. Finally, we discuss continuous improvement initiatives that foster a culture of ongoing enhancement, driving manufacturers towards unparalleled quality standards. These insights are crucial for global manufacturing facilities seeking to adopt best practices and stay ahead in the industry.
1. Advanced Manufacturing Technologies Used by Nissan
Nissan, a pioneer in the automotive industry, has consistently embraced advanced manufacturing technologies to enhance quality control and drive innovation. At the heart of their production process lies a robust integration of cutting-edge technologies that ensure precision, efficiency, and sustainability. One such technology is the use of Industry 4.0 principles, which involves the deployment of smart sensors and IoT devices to monitor every stage of production in real-time. This allows for immediate detection and rectification of any anomalies, thereby maintaining high standards of quality. Another significant advancement is Nissan's adoption of robotic automation. Advanced robots equipped with AI capabilities are used for tasks ranging from welding and assembly to painting and inspection. These robots not only increase productivity but also reduce human error, ensuring that every vehicle meets stringent quality benchmarks. Additionally, Nissan has invested heavily in 3D printing technology for rapid prototyping and production of complex parts. This not only accelerates the development cycle but also enables the creation of customized components with unprecedented precision. Furthermore, Nissan leverages data analytics and machine learning algorithms to optimize manufacturing processes. By analyzing vast amounts of data generated during production, these systems can predict potential issues before they arise, allowing for proactive maintenance and minimizing downtime. The company also employs virtual reality (VR) and augmented reality (AR) tools for training purposes as well as for simulating production scenarios without physical prototypes. Sustainability is another key focus area where advanced technologies play a crucial role. Nissan has implemented energy-efficient solutions such as solar panels and wind turbines at its facilities to reduce carbon footprint. Moreover, the company is exploring innovative materials like recycled plastics and bioplastics for vehicle components. In summary, Nissan's commitment to advanced manufacturing technologies underscores its dedication to quality control and innovation. By integrating Industry 4.0 principles, robotic automation, 3D printing, data analytics, VR/AR tools, and sustainable practices into its production processes, Nissan continues to set industry standards while ensuring that each vehicle rolling off the assembly line meets the highest levels of quality and reliability.
2. Quality Assurance Processes Across Facilities
Quality Assurance Processes Across Facilities In the realm of manufacturing, particularly in the automotive industry, quality assurance (QA) is a cornerstone that ensures products meet stringent standards. For Nissan, a global leader in vehicle production, maintaining uniform quality across all facilities is paramount. This involves implementing robust QA processes that are meticulously designed and rigorously enforced. At Nissan's manufacturing plants worldwide, from Japan to the United States and Europe, these processes are integrated into every stage of production. The journey begins with supplier quality management where Nissan scrutinizes its suppliers to ensure they adhere to the highest standards of material quality. This includes regular audits and performance evaluations to guarantee that all components meet or exceed specifications. Once materials are sourced, they undergo rigorous testing at various checkpoints throughout the production line. This includes both manual inspections by trained personnel and automated systems equipped with advanced sensors and AI algorithms capable of detecting even minor defects. Nissan also employs a Total Productive Maintenance (TPM) strategy to maintain equipment efficiency and reliability. Regular maintenance schedules prevent downtime and reduce the likelihood of defects caused by machinery malfunctions. Additionally, continuous improvement initiatives such as Kaizen encourage employees at all levels to identify areas for improvement and implement changes that enhance overall quality. Another critical aspect is employee training and development. Nissan invests heavily in comprehensive training programs that equip workers with the skills necessary to perform their roles effectively while adhering strictly to QA protocols. This not only enhances product quality but also fosters a culture of excellence within the organization. Furthermore, Nissan leverages technology extensively in its QA processes. Advanced data analytics tools monitor production metrics in real-time, providing insights that help identify trends or potential issues before they become major problems. The use of Industry 4.0 technologies like IoT sensors further enhances monitoring capabilities by providing real-time feedback on equipment performance and product integrity. Finally, Nissan's commitment to quality extends beyond the factory floor through rigorous post-production testing and inspection procedures before vehicles are shipped out for distribution. This includes both static inspections where vehicles are checked against a checklist of criteria as well as dynamic tests where cars are driven under various conditions to simulate real-world usage scenarios. In summary, Nissan's dedication to maintaining high-quality standards across all facilities underscores its commitment not just to producing reliable vehicles but also to fostering trust among consumers globally. By integrating cutting-edge technologies with traditional best practices in quality assurance processes throughout every stage of manufacturing—from supplier management through post-production testing—Nissan ensures that each vehicle rolling off its assembly lines meets or exceeds customer expectations consistently worldwide.
3. Continuous Improvement Initiatives for Enhanced Quality
Continuous Improvement Initiatives for Enhanced Quality In the pursuit of excellence, Nissan has implemented a robust framework of continuous improvement initiatives to elevate quality across its manufacturing processes. At the heart of these efforts lies the Total Productive Maintenance (TPM) program, which focuses on maximizing equipment efficiency and reducing downtime. By engaging all employees in proactive maintenance activities, TPM ensures that machinery operates at optimal levels, thereby enhancing product reliability and consistency. Additionally, Nissan employs the Six Sigma methodology to identify and eliminate defects through data-driven decision-making. This approach empowers teams to analyze processes meticulously, pinpoint areas for improvement, and implement corrective measures that significantly reduce variability and errors. Another critical initiative is Nissan's commitment to Kaizen—a Japanese philosophy that encourages ongoing incremental improvements. Through regular workshops and training sessions, employees are encouraged to suggest innovative solutions that can streamline workflows or enhance product features. This collaborative environment fosters a culture of continuous learning and innovation, where every employee feels valued as a contributor to quality enhancement. Furthermore, Nissan leverages advanced technologies such as Industry 4.0 tools—like IoT sensors and AI algorithms—to monitor production lines in real-time. These technologies provide instant feedback on performance metrics, enabling swift interventions when deviations occur. The integration of these initiatives not only ensures that Nissan's products meet stringent quality standards but also drives innovation within the manufacturing ecosystem. By fostering an environment where improvement is both expected and rewarded, Nissan maintains its competitive edge while delivering superior value to customers worldwide. As part of its broader strategy for Quality Control and Innovation in Manufacturing, these continuous improvement initiatives underscore Nissan's dedication to excellence in every aspect of its operations—from design through production—to ultimately create vehicles that embody reliability, performance, and customer satisfaction.