Where Are Milwaukee Tools Made

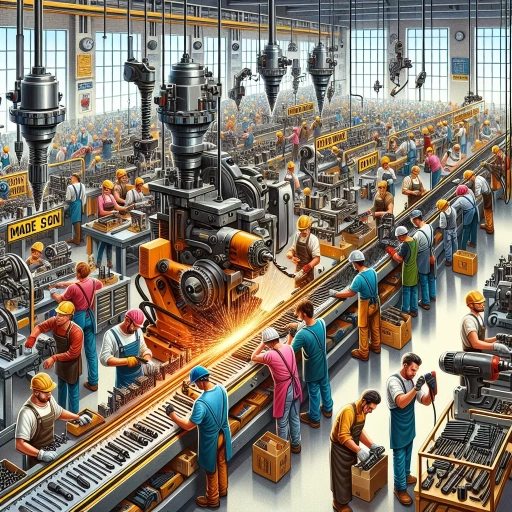
Milwaukee Tools, a name synonymous with durability and excellence in the world of power tools, has a rich history that spans over a century. Founded in 1924 by A.H. Petersen, the company has evolved from its humble beginnings to become a global leader in tool manufacturing. But where are these iconic tools made? This article delves into the fascinating journey of Milwaukee Tools, exploring their history, current manufacturing locations, and the rigorous quality control processes that ensure every product meets the highest standards. We will start by uncovering the History of Milwaukee Tools Manufacturing, tracing back to its early days and pivotal moments that shaped the brand into what it is today.
History of Milwaukee Tools Manufacturing
Milwaukee Tools, a name synonymous with quality and reliability in the power tool industry, has a rich history that spans over a century. From its humble beginnings to its current status as a global leader, Milwaukee Tools' journey is marked by innovation, perseverance, and a commitment to excellence. This article delves into the fascinating history of Milwaukee Tools Manufacturing, exploring its early beginnings and founding, the evolution over the years, and key milestones and innovations that have shaped the company into what it is today. By examining these pivotal aspects of its history, we gain insight into how Milwaukee Tools has consistently set standards in the industry while remaining true to its core values. Join us as we uncover the compelling story behind one of the most trusted names in power tools: The History of Milwaukee Tools Manufacturing.
Early Beginnings and Founding
The early beginnings and founding of Milwaukee Tools are a testament to innovation and perseverance. In 1924, A.H. Petersen, a skilled mechanic, and Henry Siebert, an entrepreneur, joined forces to establish the Milwaukee Electric Tool Corporation in Milwaukee, Wisconsin. Their vision was to create tools that would meet the demanding needs of the rapidly growing automotive industry. The company's first product was a portable drill known as the "Hole-Shooter," which quickly gained popularity for its durability and efficiency. This initial success laid the groundwork for what would become a legacy of producing high-quality power tools. In the 1930s, Milwaukee Tools continued to expand its product line with the introduction of sanders, grinders, and saws. The company's commitment to quality and innovation led to significant advancements in tool design and functionality. During World War II, Milwaukee Tools played a crucial role in supporting the war effort by manufacturing tools for the U.S. military. This period marked a significant turning point for the company as it solidified its reputation as a reliable supplier of essential equipment. The post-war era saw Milwaukee Tools continue on an upward trajectory with technological advancements that further enhanced tool performance. The introduction of new products such as impact wrenches and rotary hammers catered to emerging industries like construction and manufacturing. By the mid-20th century, Milwaukee Tools had established itself as a leader in the power tool industry, known for its robust products that could withstand rigorous use. Throughout its history, Milwaukee Tools has remained true to its founding principles of quality, innovation, and customer satisfaction. Today, as part of Techtronic Industries (TTI), one of the world's largest power tool manufacturers, Milwaukee continues to innovate with cutting-edge technology such as lithium-ion batteries and advanced motor designs. Despite global expansion and technological advancements over nearly a century since its inception, Milwaukee remains deeply rooted in its hometown legacy—continuing to produce tools that are synonymous with reliability and excellence. This rich history underscores why Milwaukee remains at the forefront of tool manufacturing today—its early beginnings were marked by visionary leadership and an unwavering commitment to excellence that has endured through generations.
Evolution Over the Years
Evolution Over the Years Milwaukee Tools' journey is a testament to innovation and resilience. Founded in 1924 by A.H. Petersen, the company started as a small manufacturer of electric drills. Over the years, Milwaukee Tools has evolved significantly, driven by technological advancements and a commitment to quality. In the early days, the company focused on producing high-quality electric drills that quickly gained popularity among professionals. The 1950s saw the introduction of the Hole-Shooter, a portable drill that revolutionized the industry with its lightweight design and powerful performance. The 1970s marked a significant turning point for Milwaukee Tools as it began expanding its product line to include saws, sanders, and other power tools. This diversification was instrumental in establishing the brand as a leader in the power tool market. The introduction of the Sawzall reciprocating saw in 1951 further solidified Milwaukee's reputation for producing durable and reliable tools. This period also saw significant investments in research and development, leading to numerous patents that enhanced tool performance and user safety. In recent decades, Milwaukee Tools has continued its trajectory of innovation with advancements in battery technology. The introduction of lithium-ion batteries has enabled longer runtime and lighter tools without compromising power. This shift has been particularly evident with the launch of their M12 and M18 cordless systems, which offer a wide range of compatible tools designed for various applications from drilling to cutting. Moreover, Milwaukee Tools has embraced digital technology to enhance tool functionality. Features like One-Key technology allow users to track their tools digitally, monitor battery health, and even customize performance settings via an app. This integration of smart technology into traditional power tools reflects the company's forward-thinking approach. Throughout its history, Milwaukee Tools has remained committed to manufacturing excellence while adapting to changing market demands. Today, with facilities around the world including those in Brookfield and Mukwonago Wisconsin USA; Europe; Asia; Australia; Canada; Mexico among others - they continue producing top-tier products that meet or exceed industry standards ensuring they remain at forefront within this competitive landscape.
Key Milestones and Innovations
Milwaukee Tools, a leading manufacturer of power tools and equipment, has a rich history marked by numerous key milestones and innovations. Founded in 1924 by A.H. Petersen, the company initially focused on producing portable electric drills. A significant early innovation was the introduction of the Hole-Shooter drill in 1931, which revolutionized the industry with its lightweight and powerful design. This was followed by the development of the Sawzall reciprocating saw in 1951, a tool that became synonymous with Milwaukee's commitment to quality and durability. The 1960s saw further advancements with the introduction of the first cordless drill in 1963, showcasing Milwaukee's forward-thinking approach to tool technology. The company continued to innovate through the decades, introducing new products such as rotary hammers and impact wrenches that set industry standards for performance and reliability. In 2005, Milwaukee launched its V28 lithium-ion battery system, significantly enhancing tool performance and runtime. In recent years, Milwaukee has continued its tradition of innovation with advancements like ONE-KEY technology introduced in 2015. This digital platform allows users to track their tools via Bluetooth connectivity and customize performance settings via an app. Additionally, Milwaukee's M12 and M18 cordless systems have expanded to include a wide range of tools from compact drills to heavy-duty saws, all designed for seamless integration within these ecosystems. Throughout its history, Milwaukee Tools has remained committed not only to producing high-quality products but also to fostering a culture of innovation that drives industry progress. Today, as part of Techtronic Industries (TTI), Milwaukee continues to push boundaries in tool technology while maintaining its reputation as a trusted brand among professionals worldwide.
Current Manufacturing Locations
In the ever-evolving landscape of manufacturing, understanding current production locations is crucial for businesses and consumers alike. This article delves into the contemporary manufacturing landscape, highlighting key areas where production thrives. We explore primary facilities in the United States, which serve as the backbone of domestic manufacturing. Additionally, we examine international manufacturing sites that have become integral to global supply chains. Specialized production centers also play a significant role in this narrative, focusing on niche industries that require unique expertise and infrastructure. By examining these three facets of modern manufacturing, we gain a comprehensive view of how goods are produced today. This insight is particularly relevant when considering the history of Milwaukee Tools Manufacturing, a company that has navigated these shifts over decades to remain a leader in its field.
Primary Facilities in the United States
Primary facilities in the United States play a pivotal role in the manufacturing landscape, particularly for renowned brands like Milwaukee Tools. These facilities are strategically located to optimize production efficiency, logistical operations, and market accessibility. In the context of Milwaukee Tools, primary facilities are crucial for maintaining high-quality standards and meeting the demand for their extensive range of power tools and equipment. The company's commitment to domestic manufacturing ensures that products are crafted with precision and reliability, adhering to stringent quality control measures that have become synonymous with the brand. These facilities are equipped with state-of-the-art machinery and technology, enabling the production of complex tool designs that cater to both professional contractors and DIY enthusiasts. The presence of skilled labor forces within these primary facilities further enhances product quality by ensuring that each tool undergoes rigorous testing before it reaches the market. Additionally, being based in the United States allows Milwaukee Tools to respond swiftly to market trends and consumer feedback, facilitating continuous innovation and improvement in their product lines. Moreover, primary facilities contribute significantly to local economies by creating employment opportunities and stimulating economic growth through investments in infrastructure and community development projects. This not only benefits the immediate vicinity but also has a ripple effect on broader regional economies. By maintaining a strong presence in domestic manufacturing, Milwaukee Tools reinforces its reputation as a leader in the industry while contributing positively to societal well-being. In summary, primary facilities in the United States are essential for brands like Milwaukee Tools as they ensure high-quality production, support local economies, and facilitate continuous innovation. These facilities serve as the backbone of manufacturing operations by leveraging advanced technology, skilled workforce, and strategic locations to meet consumer demands effectively.
International Manufacturing Sites
Milwaukee Tools, a renowned brand in the power tool industry, operates a network of international manufacturing sites that play a crucial role in its global success. These facilities are strategically located to optimize production efficiency, reduce logistics costs, and ensure timely delivery to customers worldwide. In China, Milwaukee Tools has established multiple manufacturing plants that leverage the country's extensive supply chain and skilled workforce. These sites produce a wide range of products, from cordless drills and saws to specialized tools for various industries. The Chinese operations are complemented by facilities in Europe, particularly in Germany and Poland, where high-quality standards are maintained through rigorous quality control processes. These European sites focus on producing precision-engineered tools tailored for the demanding European market. In addition to its Asian and European presence, Milwaukee Tools also has significant manufacturing capabilities in North America. The company's U.S.-based facilities are known for their innovative production techniques and commitment to quality. These plants not only cater to domestic demand but also export products globally. Furthermore, Milwaukee Tools has expanded its footprint into Latin America with operations in countries like Mexico, where favorable trade agreements enhance export opportunities while maintaining competitive pricing. The international manufacturing strategy of Milwaukee Tools is underpinned by a robust supply chain management system that ensures consistent material quality and timely delivery of components across all locations. This integrated approach allows the company to maintain uniform product standards regardless of where the tools are produced. Moreover, each site adheres strictly to environmental regulations and labor laws, reflecting Milwaukee Tools' commitment to sustainability and ethical practices. Investing heavily in research and development at these international sites enables Milwaukee Tools to stay ahead of technological advancements in the industry. Collaborative efforts between engineers from different regions facilitate the exchange of ideas and best practices, leading to continuous innovation in tool design and functionality. This global R&D network supports the development of specialized tools that meet specific regional needs while maintaining universal appeal. Overall, Milwaukee Tools' extensive network of international manufacturing sites is a testament to its dedication to quality, innovation, and customer satisfaction on a global scale. By leveraging diverse regional strengths while maintaining uniform standards across all locations, the company continues to solidify its position as a leader in the power tool industry.
Specialized Production Centers
Specialized Production Centers are integral to the manufacturing process of Milwaukee Tools, ensuring that each product meets the highest standards of quality and performance. These centers are strategically located around the world, leveraging local expertise and resources to optimize production efficiency. In the United States, for instance, Milwaukee Tools operates state-of-the-art facilities in Wisconsin and Mississippi. The Brookfield, Wisconsin facility serves as a global headquarters and innovation hub, where cutting-edge research and development drive the creation of new tools and technologies. Meanwhile, the Jackson, Mississippi plant focuses on high-volume production, utilizing advanced machinery and rigorous quality control measures to produce a wide range of power tools and accessories. Globally, Milwaukee Tools has established specialized production centers in Europe and Asia to cater to regional markets effectively. The company's European operations are centered in Germany and Poland, where skilled labor forces contribute to the manufacturing of precision-engineered tools tailored for European market demands. In Asia, particularly in China and Taiwan, Milwaukee Tools leverages local manufacturing capabilities while maintaining stringent quality standards through rigorous testing protocols. These specialized centers not only enhance operational efficiency but also foster innovation by bringing together diverse teams of engineers, designers, and production experts. By integrating local knowledge with global best practices, Milwaukee Tools ensures that its products are both relevant to regional needs and consistent in quality across all markets. This approach allows the company to maintain its competitive edge while continuously improving its product offerings. Moreover, these production centers play a crucial role in supporting Milwaukee Tools' commitment to sustainability. By locating facilities near key markets and suppliers, the company reduces transportation costs and environmental impact associated with long-distance shipping. Additionally, many of these centers incorporate green technologies such as solar power systems and energy-efficient machinery into their operations. In summary, Specialized Production Centers are vital components of Milwaukee Tools' manufacturing strategy. They enable the company to produce high-quality products efficiently while fostering innovation and sustainability across different regions. This strategic approach ensures that Milwaukee Tools remains a leader in the power tool industry by delivering exceptional performance and reliability to users worldwide.
Quality Control and Production Process
In the realm of industrial manufacturing, Quality Control and Production Process are paramount for ensuring the delivery of high-quality products. This article delves into the critical phases that underpin successful production, starting with the Design and Prototyping Phase, where meticulous planning and testing lay the foundation for product excellence. Next, we explore Manufacturing Techniques and Technologies, highlighting advancements that streamline production while maintaining precision. Finally, we examine Quality Assurance Measures, detailing how rigorous checks and standards safeguard against defects. By understanding these interconnected processes, manufacturers can optimize their operations to produce superior products consistently. This comprehensive approach has been exemplified by companies like Milwaukee Tools, whose commitment to quality has shaped their manufacturing history.
Design and Prototyping Phase
The Design and Prototyping Phase is a crucial step in the Quality Control and Production Process of Milwaukee Tools, ensuring that every product meets the highest standards of performance, durability, and user satisfaction. This phase begins with meticulous research and analysis to identify market needs and trends, followed by conceptual design where innovative ideas are brainstormed and refined. Engineers utilize advanced computer-aided design (CAD) software to create detailed models that can be tested virtually for functionality, ergonomics, and aesthetics. Prototypes are then fabricated using state-of-the-art 3D printing technology or traditional methods like machining or casting. These prototypes undergo rigorous testing under various conditions to validate their design assumptions. Feedback from both internal teams and external stakeholders is collected to make necessary adjustments before moving forward. The iterative nature of this phase ensures that any flaws or inefficiencies are addressed early on, minimizing potential issues during mass production. Additionally, environmental impact assessments are conducted to ensure sustainability in material selection and manufacturing processes. By investing heavily in this phase, Milwaukee Tools can guarantee that their products not only meet but exceed customer expectations while maintaining their reputation for quality and reliability.
Manufacturing Techniques and Technologies
Manufacturing techniques and technologies play a crucial role in ensuring the quality and efficiency of the production process. In the context of Milwaukee Tools, these advancements are pivotal in maintaining the high standards that the brand is known for. One key technique is Computer Numerical Control (CNC) machining, which allows for precise and consistent cutting, drilling, and shaping of materials. This technology ensures that every tool component meets exact specifications, reducing variability and enhancing overall product reliability. Another significant technology is 3D printing, which enables rapid prototyping and production of complex parts with intricate designs. This method not only speeds up the development phase but also allows for the creation of customized components that can be integrated into various tool models. Additionally, robotic assembly lines are increasingly being utilized to streamline production processes. These robots can perform repetitive tasks with high accuracy and speed, thereby improving productivity while minimizing human error. Quality control measures are also heavily reliant on advanced technologies such as machine vision systems and automated inspection tools. Machine vision systems use cameras and software to detect defects or irregularities in real-time during production, ensuring that only flawless products reach the market. Automated inspection tools further enhance this process by conducting thorough checks at multiple stages of manufacturing. Moreover, data analytics plays a crucial role in optimizing production processes. By leveraging data from sensors and other sources along the manufacturing line, companies can identify bottlenecks, predict maintenance needs, and make informed decisions to improve efficiency. This integration of Industry 4.0 technologies not only enhances quality control but also contributes to a more sustainable and cost-effective production environment. In summary, the combination of CNC machining, 3D printing, robotic assembly lines, machine vision systems, automated inspection tools, and data analytics forms a robust framework for manufacturing techniques and technologies at Milwaukee Tools. These innovations collectively contribute to maintaining stringent quality standards while driving operational excellence throughout the production process.
Quality Assurance Measures
Quality Assurance Measures are integral to the production process of Milwaukee Tools, ensuring that every product meets the highest standards of performance, reliability, and safety. These measures are meticulously implemented at various stages of production to guarantee that each tool not only meets but exceeds customer expectations. From raw material inspection to final product testing, Milwaukee Tools employs rigorous quality control protocols. This includes thorough testing for durability and functionality under diverse conditions, as well as adherence to strict manufacturing guidelines. Additionally, continuous monitoring and feedback loops allow for real-time adjustments in the production line, ensuring any defects or inefficiencies are promptly addressed. The company also invests heavily in employee training programs to enhance their skills and knowledge, thereby maintaining a workforce capable of producing top-tier products consistently. Furthermore, Milwaukee Tools collaborates with external auditors who conduct regular audits to verify compliance with international quality standards such as ISO 9001. This commitment to excellence is reflected in the company's reputation for delivering high-quality tools that stand the test of time and heavy use. By integrating these robust Quality Assurance Measures into their production process, Milwaukee Tools ensures that every tool leaving their facilities is a testament to their dedication to quality and customer satisfaction.