Where Is Hyundai Made

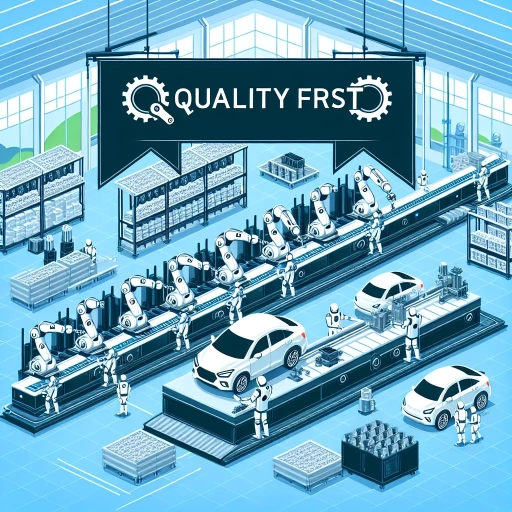
Hyundai, one of the world's leading automotive manufacturers, has a rich history and a global footprint that spans across multiple continents. The company's success is not just attributed to its innovative designs and technological advancements but also to its strategic production facilities located around the globe. In this article, we will delve into the intricacies of Hyundai's manufacturing process, exploring its global manufacturing facilities, technological innovations, and the impact of globalization on its production strategy. By understanding where Hyundai is made and how it leverages technology and global resources, we can gain insights into what drives this automotive giant's continued success. Let's start by examining the Global Manufacturing Facilities of Hyundai.
Global Manufacturing Facilities of Hyundai
Hyundai, one of the world's leading automotive manufacturers, has established a robust global presence through its extensive network of manufacturing facilities. From its origins in South Korea to strategic expansions in the United States and India, Hyundai's commitment to quality and innovation is evident in every production hub. This article delves into the heart of Hyundai's global manufacturing prowess, exploring how these key locations contribute to the company's success. We begin by examining South Korea: The Birthplace of Hyundai, where the company's legacy and technological advancements set the stage for its international growth. Next, we look at United States: Hyundai's American Production Hubs, highlighting how these facilities have become integral to meeting regional demand and fostering local economic development. Finally, we explore India: A Key Market for Hyundai's Global Expansion, discussing how this market has played a crucial role in driving the company's global ambitions. Together, these regions form the backbone of Hyundai's Global Manufacturing Facilities.
South Korea: The Birthplace of Hyundai
South Korea, the birthplace of Hyundai, is a nation that has transformed itself from a war-torn country to a global economic powerhouse. The journey of Hyundai, one of South Korea's most iconic brands, mirrors this transformation. Founded in 1967 by Chung Ju-yung, Hyundai Motor Company began as a small manufacturer but quickly expanded its operations to become one of the world's leading automobile manufacturers. The company's name, "Hyundai," translates to "modernity" in Korean, reflecting its commitment to innovation and progress. South Korea's strategic location on the Asian continent and its highly educated workforce have been instrumental in Hyundai's success. The country's robust infrastructure and favorable business environment have attracted significant foreign investment, enabling Hyundai to establish state-of-the-art manufacturing facilities both domestically and internationally. Hyundai's flagship plant in Ulsan, South Korea, is one of the largest automobile manufacturing plants in the world, producing over 600,000 vehicles annually. The synergy between South Korea's government policies and private sector initiatives has fostered an ecosystem conducive to industrial growth. Initiatives such as tax incentives for R&D investments and subsidies for export-oriented industries have supported Hyundai's expansion plans. Additionally, South Korea's emphasis on education has provided Hyundai with a skilled workforce capable of driving technological advancements. Hyundai's global reach is evident through its extensive network of manufacturing facilities across continents. From China to India, the United States to Europe, Hyundai has established itself as a major player in the automotive industry. However, its roots remain firmly planted in South Korea where it continues to innovate and push boundaries in automotive technology. In conclusion, South Korea's dynamic economy and supportive environment have been crucial factors in Hyundai's ascent as a global manufacturing giant. As Hyundai continues to expand its operations worldwide while maintaining its core values rooted in South Korean ingenuity and resilience, it stands as a testament to the nation's remarkable journey from humble beginnings to international prominence.
United States: Hyundai's American Production Hubs
Hyundai's American production hubs play a pivotal role in the company's global manufacturing strategy, showcasing its commitment to local markets and innovative production techniques. The Hyundai Motor Manufacturing Alabama (HMMA) facility, located in Montgomery, Alabama, is one of the most significant production centers in the United States. Established in 2005, HMMA has grown to become a cornerstone of Hyundai's North American operations, producing popular models such as the Sonata and Elantra. This state-of-the-art plant not only underscores Hyundai's dedication to quality but also highlights its emphasis on community engagement and economic development within the region. In addition to HMMA, Hyundai has expanded its U.S. footprint with strategic investments aimed at enhancing both production capacity and technological advancements. The company's commitment to innovation is evident through its collaboration with local universities and research institutions, fostering a culture of continuous improvement and technological innovation. Furthermore, Hyundai's investment in American manufacturing has created thousands of jobs directly and indirectly, contributing significantly to regional economies. The success of Hyundai's American production hubs can be attributed to several factors including strategic location advantages, robust supply chain networks, and a highly skilled workforce. By leveraging these strengths, Hyundai ensures that its U.S.-produced vehicles meet stringent quality standards while also catering to the unique preferences of the North American market. This localized approach allows for quicker response times to market demands and better alignment with consumer needs. Moreover, Hyundai's presence in the U.S. extends beyond traditional manufacturing; it includes substantial investments in research and development (R&D). The Hyundai America Technical Center (HATCI) in Superior Township, Michigan serves as a critical R&D hub where engineers focus on developing cutting-edge technologies that drive future mobility solutions. This center plays an integral role in shaping Hyundai’s global product lineup by integrating insights from diverse markets into their design processes. In summary, Hyundai’s American production hubs are integral components of its global manufacturing network. Through HMMA and other strategic investments across the U.S., Hyundai demonstrates its commitment not only to producing high-quality vehicles but also to fostering economic growth and technological advancements within local communities. As part of its broader global strategy aimed at meeting diverse market needs while driving innovation forward, these hubs stand as testament to Hyundai’s vision for a future where mobility is both sustainable and accessible for all.
India: A Key Market for Hyundai's Global Expansion
India has emerged as a pivotal market for Hyundai's global expansion, offering a dynamic and rapidly growing consumer base. The country's large population, coupled with increasing disposable incomes and a rising middle class, presents significant opportunities for automotive manufacturers. Hyundai recognized this potential early on and established its first manufacturing facility in India in 1998 at Sriperumbudur, near Chennai. This strategic move allowed the company to tap into the burgeoning Indian market while also leveraging the country's competitive manufacturing costs and skilled workforce. Hyundai's Indian operations have been instrumental in driving its global growth. The Chennai plant has become one of the company's largest overseas manufacturing facilities, producing popular models such as the i10, i20, and Creta. These vehicles not only cater to domestic demand but are also exported to various international markets, contributing substantially to Hyundai's global sales volume. The success in India has prompted further investments by Hyundai, including the expansion of its production capacity and the introduction of new models tailored specifically for the Indian market. Moreover, India serves as a critical hub for Hyundai's research and development activities. The company has established a state-of-the-art R&D center in Hyderabad, which focuses on developing technologies that meet local consumer preferences while adhering to global standards. This center plays a crucial role in enhancing product quality and innovation, enabling Hyundai to stay competitive both domestically and internationally. In addition to its manufacturing prowess, Hyundai has also made significant strides in terms of sustainability and corporate social responsibility within India. The company has implemented various initiatives aimed at reducing environmental impact through green technologies and sustainable practices across its operations. Furthermore, Hyundai's philanthropic efforts have focused on education, healthcare, and community development programs that benefit local communities around its facilities. Overall, India remains an essential component of Hyundai's global strategy due to its vast market potential, favorable business environment, and strategic location for exports. As the automotive landscape continues to evolve with technological advancements and shifting consumer preferences, Hyundai is well-positioned to capitalize on these trends through its robust presence in India.
Technological Innovations in Hyundai's Manufacturing Process
In the ever-evolving landscape of automotive manufacturing, Hyundai has emerged as a pioneer in technological innovations. The company's commitment to integrating cutting-edge advancements into its production processes has not only enhanced efficiency but also set new standards for quality and sustainability. This article delves into three key areas where Hyundai's technological innovations are making a significant impact: Advanced Robotics and Automation, Sustainable Production Practices, and Quality Control and Testing Procedures. By leveraging advanced robotics, Hyundai is streamlining its assembly lines and reducing human error. The adoption of sustainable production practices ensures that environmental impact is minimized while maintaining high productivity levels. Additionally, rigorous quality control measures guarantee that every vehicle meets stringent standards before hitting the market. These innovations are transforming not just Hyundai's domestic operations but also its global manufacturing facilities, positioning the company at the forefront of modern automotive manufacturing.
Advanced Robotics and Automation
Advanced Robotics and Automation play a pivotal role in Hyundai's manufacturing process, significantly enhancing efficiency, precision, and productivity. By integrating cutting-edge robotic systems, Hyundai has revolutionized its production lines to meet the demands of a rapidly evolving automotive industry. These advanced robots are equipped with sophisticated sensors and AI algorithms that enable them to perform complex tasks with unparalleled accuracy. For instance, robotic arms can handle delicate assembly operations such as welding and painting with precision that surpasses human capabilities. Additionally, autonomous mobile robots (AMRs) navigate through the factory floor effortlessly, streamlining material transport and reducing labor costs. The implementation of automation also extends to quality control processes. Advanced vision systems and machine learning algorithms are used to inspect vehicles for defects in real-time, ensuring that every car meets stringent quality standards before it leaves the factory. This not only improves product reliability but also reduces the need for manual inspections, thereby speeding up production cycles. Moreover, Hyundai leverages Industry 4.0 technologies like IoT (Internet of Things) and Big Data analytics to optimize its manufacturing processes further. By connecting all machinery and equipment on the factory floor via IoT networks, real-time data can be collected and analyzed to predict maintenance needs, prevent downtime, and optimize resource allocation. This proactive approach ensures that production runs smoothly without interruptions while continuously improving operational efficiency. Incorporating advanced robotics and automation also enhances workplace safety by taking over hazardous tasks from human workers. Robots can handle dangerous operations such as heavy lifting or working in confined spaces without risking injury or fatigue. This not only protects employees but also fosters a healthier work environment where humans can focus on more strategic roles like innovation and problem-solving. Hyundai’s commitment to technological innovation is evident in its state-of-the-art manufacturing facilities around the world. From South Korea to the United States and Europe, these advanced technologies are being deployed consistently across different locations to maintain uniform quality standards while adapting to local market needs efficiently. In conclusion, Advanced Robotics and Automation are integral components of Hyundai’s technological innovations in manufacturing processes. By embracing these technologies wholeheartedly, Hyundai continues to set benchmarks for efficiency, quality control, workplace safety, and overall productivity within the automotive industry globally.
Sustainable Production Practices
Hyundai's commitment to sustainable production practices is a cornerstone of its manufacturing process, ensuring that technological innovations not only enhance efficiency but also minimize environmental impact. By integrating cutting-edge technologies with eco-friendly strategies, Hyundai has set a new standard in the automotive industry. One key aspect is the implementation of renewable energy sources such as solar and wind power to reduce reliance on fossil fuels. For instance, Hyundai's solar-powered charging stations for electric vehicles (EVs) promote green mobility while lowering carbon emissions. Additionally, advanced water management systems and recycling facilities minimize waste and conserve resources, reflecting Hyundai's dedication to environmental stewardship. The use of advanced materials like recycled plastics and lightweight composites further reduces the ecological footprint of Hyundai's vehicles. These materials not only contribute to better fuel efficiency but also decrease the overall weight of vehicles, leading to lower emissions during production and operation. Moreover, Hyundai's focus on digitalization through Industry 4.0 technologies enables real-time monitoring and optimization of production processes, ensuring minimal waste generation and maximum resource utilization. Hyundai's Smart Factory initiative leverages artificial intelligence (AI), Internet of Things (IoT), and big data analytics to create intelligent manufacturing environments that are both efficient and sustainable. This technological integration allows for predictive maintenance, reducing downtime and energy consumption while enhancing overall productivity. The company's emphasis on circular economy principles means that end-of-life vehicles are systematically dismantled for parts reuse or recycling, significantly reducing landfill waste. Furthermore, Hyundai collaborates with suppliers who adhere to stringent sustainability standards, fostering a culture of responsibility throughout its supply chain. This collaborative approach ensures that every component used in Hyundai vehicles meets high environmental benchmarks from sourcing through production. In conclusion, Hyundai's sustainable production practices are deeply intertwined with its technological innovations. By harnessing the power of renewable energy sources, advanced materials science, digitalization efforts through Industry 4.0 technologies, circular economy principles, and responsible supply chain management—Hyundai continues to lead the automotive industry towards a greener future while maintaining its commitment to quality and innovation in manufacturing processes globally.
Quality Control and Testing Procedures
Quality Control and Testing Procedures are integral components of Hyundai's manufacturing process, ensuring that every vehicle meets stringent standards of reliability, performance, and safety. Hyundai employs a multi-layered approach to quality control, starting from the design phase where rigorous simulations and virtual testing are conducted to predict potential issues. Once production begins, each component undergoes meticulous inspection at various stages. Advanced technologies such as machine learning algorithms and artificial intelligence are utilized to detect even the slightest deviations from specifications. For instance, AI-powered vision systems can identify defects in real-time during assembly lines, allowing for immediate corrective actions. In addition to automated checks, human inspectors play a crucial role in verifying the quality of finished products. Trained personnel conduct thorough physical inspections and performance tests on vehicles before they leave the factory floor. These tests include dynamic assessments like crash simulations and endurance runs under extreme conditions to ensure durability and resilience. Furthermore, Hyundai collaborates with external auditors who conduct regular audits to maintain transparency and adherence to international quality standards. Hyundai also places significant emphasis on continuous improvement through feedback loops from both internal teams and external stakeholders. Customer feedback is meticulously analyzed to identify areas for enhancement, while internal teams engage in Kaizen practices—continuous improvement methodologies—that foster a culture of innovation within the organization. This holistic approach not only ensures that Hyundai vehicles meet but exceed customer expectations but also drives technological advancements within their manufacturing processes. Moreover, Hyundai's commitment to quality extends beyond the factory walls through rigorous post-production testing protocols. Vehicles are subjected to rigorous field tests under diverse environmental conditions worldwide—from scorching deserts to icy tundras—to validate their performance across different terrains and climates. This comprehensive strategy ensures that every Hyundai model delivered is not just a product but a testament to excellence in engineering and manufacturing prowess. In summary, Hyundai's Quality Control and Testing Procedures are a cornerstone of their technological innovations in manufacturing processes. By integrating cutting-edge technology with rigorous human oversight and continuous improvement practices, Hyundai maintains its reputation for producing high-quality vehicles that stand out globally for their reliability and performance.
Impact of Globalization on Hyundai's Production Strategy
Globalization has profoundly reshaped the automotive industry, compelling companies like Hyundai to adapt their production strategies to remain competitive. This article delves into the multifaceted impact of globalization on Hyundai's manufacturing processes, focusing on three critical areas: Market Adaptation and Localization, Supply Chain Management Across Borders, and Regulatory Compliance in Different Regions. By examining these aspects, we will explore how Hyundai has navigated the complexities of global markets to maintain its position as a leading automaker. The insights gained from this analysis will ultimately highlight the strategic transformations within Hyundai's global manufacturing facilities.
Market Adaptation and Localization
Market adaptation and localization are pivotal strategies for multinational corporations like Hyundai to navigate the complexities of globalization effectively. By adapting their products and services to meet the unique preferences, regulations, and cultural nuances of different markets, companies can significantly enhance their competitive edge. For instance, Hyundai's success in India can be attributed to its ability to tailor its vehicle designs and features according to local tastes and economic conditions. The company's localized production strategy allows it to produce models such as the i10 and i20, which are specifically designed for the Indian market with features like fuel efficiency and affordability that resonate well with local consumers. Localization also extends beyond product design; it encompasses marketing strategies, distribution networks, and even manufacturing processes. Hyundai has established robust partnerships with local suppliers in various regions, ensuring that a substantial portion of its components are sourced domestically. This not only reduces logistical costs but also fosters goodwill by supporting local economies. Additionally, by setting up manufacturing plants in strategic locations such as China, the United States, and India, Hyundai can leverage favorable trade policies and lower production costs while maintaining proximity to key markets. Moreover, market adaptation involves understanding and complying with diverse regulatory environments. In Europe, for example, stringent emissions standards necessitate that vehicles meet specific environmental criteria. Hyundai has responded by developing eco-friendly models like the Kona Electric and Ioniq series, which appeal to environmentally conscious consumers while adhering to regional regulations. Cultural sensitivity is another critical aspect of market adaptation. In some regions such as South Korea or China where brand loyalty is high among domestic brands but less so among foreign ones due to historical reasons or national pride factors; Hyundai must invest heavily in building trust through targeted marketing campaigns that highlight its commitment towards quality & innovation. In conclusion: Market adaptation & localization are essential tools for any global corporation aiming at sustained growth amidst diverse market conditions worldwide especially when considering how they impact production strategies adopted by companies like Hyundai who have successfully navigated these challenges through strategic planning & execution thereby ensuring continued relevance across different geographies globally
Supply Chain Management Across Borders
Supply Chain Management Across Borders is a critical component of Hyundai's global production strategy, enabling the company to efficiently manage its vast network of suppliers, manufacturers, and distributors worldwide. As globalization has expanded Hyundai's reach beyond South Korea, the company has had to adapt its supply chain management to accommodate diverse markets and regulatory environments. This involves coordinating with international suppliers to source high-quality components, managing logistics across multiple borders, and ensuring compliance with local regulations. Hyundai leverages advanced technologies such as blockchain and artificial intelligence to enhance transparency and predictability in its supply chain operations. By optimizing inventory levels, streamlining transportation processes, and fostering strong relationships with global partners, Hyundai can maintain consistent product quality while minimizing costs and lead times. The integration of digital platforms also facilitates real-time communication between stakeholders, allowing for swift responses to market changes or disruptions. Furthermore, Hyundai's commitment to sustainability is reflected in its efforts to reduce carbon footprints throughout the supply chain through green logistics initiatives and ethical sourcing practices. Overall, effective supply chain management across borders has been instrumental in supporting Hyundai's growth into a global automotive leader by ensuring that its products are delivered efficiently and reliably to customers worldwide.
Regulatory Compliance in Different Regions
Regulatory compliance is a critical aspect of Hyundai's global production strategy, as the company operates in diverse regions with varying regulatory frameworks. In the United States, Hyundai must adhere to stringent safety and emissions standards set by the National Highway Traffic Safety Administration (NHTSA) and the Environmental Protection Agency (EPA). These regulations often require significant investments in research and development to ensure compliance with evolving standards. For instance, the Corporate Average Fuel Economy (CAFE) standards necessitate continuous improvements in fuel efficiency, driving Hyundai to innovate in hybrid and electric vehicle technologies. In Europe, Hyundai faces rigorous environmental regulations under the European Union's (EU) emissions standards. The EU's General Safety Regulation mandates advanced safety features such as automatic emergency braking and lane departure warning systems. Additionally, the EU's General Data Protection Regulation (GDPR) imposes strict data privacy requirements that Hyundai must comply with when handling customer information. This necessitates robust data management systems and transparency in data usage practices. In Asia, particularly in China, regulatory compliance involves navigating complex local content requirements and emission standards. China's New Energy Vehicle (NEV) policy incentivizes the production of electric vehicles through subsidies and tax breaks, prompting Hyundai to invest heavily in its electric vehicle lineup for the Chinese market. Furthermore, India's Bharat Stage VI emission norms have compelled Hyundai to upgrade its engine technologies to meet these stringent standards. In South Korea, Hyundai's home market, regulatory compliance is equally demanding. The Korean government has implemented policies aimed at reducing emissions and improving air quality, such as the Low Emission Vehicle Certification System. This system requires vehicles to meet specific emission criteria before they can be certified for sale in the domestic market. The diverse regulatory landscape across these regions underscores the importance of adaptability and innovation for multinational corporations like Hyundai. By investing in research and development tailored to regional requirements, Hyundai not only ensures compliance but also positions itself competitively within each market. This strategic approach allows Hyundai to leverage globalization while maintaining high standards of quality and safety across its global operations.