Where Is Mazda Made

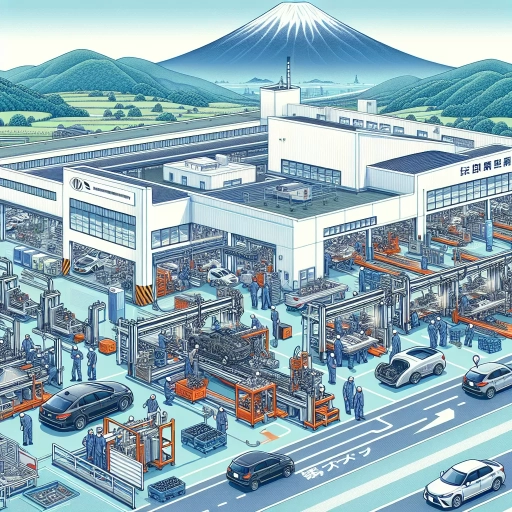
Mazda, a renowned Japanese automaker, has established itself as a leader in the global automotive industry through its commitment to innovation and quality. The company's success is deeply rooted in its extensive network of manufacturing facilities around the world. From Japan to Mexico, China, and Thailand, Mazda's global footprint ensures that its vehicles meet the highest standards of performance and reliability. This article delves into the intricacies of Mazda's manufacturing operations, exploring the key production processes that set it apart from competitors. Additionally, we examine the significant impact these facilities have on local economies, contributing to job creation and economic growth. By understanding where Mazda is made and how it operates globally, we gain insight into what drives this iconic brand forward. Let's begin by exploring Mazda's global manufacturing facilities.
Global Manufacturing Facilities
In the ever-evolving landscape of global manufacturing, facilities around the world are playing a pivotal role in shaping the future of industry. From cutting-edge technology to innovative production methods, these facilities are not only driving economic growth but also setting new standards for efficiency and sustainability. This article delves into three key regions that have emerged as leaders in global manufacturing: Japan, known for its precision and technological advancements; China, with its vast scale and rapid development; and Thailand, recognized for its strategic location and cost-effective operations. By examining these regions' unique strengths and contributions, we gain a comprehensive understanding of how they collectively influence the broader landscape of global manufacturing facilities.
Japan
Japan is renowned for its cutting-edge manufacturing facilities, which have been instrumental in establishing the country as a global leader in automotive production. Mazda, one of Japan's most iconic automobile brands, leverages these advanced facilities to produce high-quality vehicles that are celebrated worldwide for their innovative design and exceptional performance. Located primarily in Hiroshima and Hofu, Mazda's manufacturing plants are equipped with state-of-the-art technology and adhere to stringent quality control standards. These facilities not only ensure the production of reliable and efficient vehicles but also contribute significantly to Japan's robust economy. The integration of advanced robotics, artificial intelligence, and lean manufacturing techniques allows Mazda to maintain a competitive edge while continuously improving its products. Additionally, Japan's highly skilled workforce plays a crucial role in the success of these facilities by bringing expertise and dedication to every stage of the production process. The synergy between technological advancements and human ingenuity has enabled Mazda to consistently deliver vehicles that meet the evolving demands of the global market. As a result, Japan remains at the forefront of automotive manufacturing, with brands like Mazda serving as exemplary models of innovation and excellence.
China
China has emerged as a pivotal player in the global manufacturing landscape, particularly in the automotive industry. The country's vast industrial infrastructure, coupled with its highly skilled workforce and favorable economic policies, makes it an attractive destination for multinational corporations like Mazda. China's manufacturing prowess is underscored by its extensive network of state-of-the-art facilities that adhere to stringent quality standards. These facilities are equipped with cutting-edge technology and innovative production methods, ensuring high efficiency and precision in every stage of the manufacturing process. Additionally, China's strategic location facilitates seamless logistics and supply chain management, enabling rapid delivery of goods to both domestic and international markets. Mazda's decision to establish significant manufacturing operations in China reflects the country's ability to support complex production requirements while maintaining competitive costs. This synergy between technological advancement and economic viability positions China as a cornerstone in Mazda's global production strategy, underscoring its role as a leading hub for automotive manufacturing on the world stage.
Thailand
Thailand, known as the "Land of Smiles," is a vibrant and culturally rich nation that has emerged as a significant player in the global manufacturing landscape. Strategically located in Southeast Asia, Thailand offers a unique blend of economic stability, favorable business policies, and an extensive network of trade agreements. These factors have made it an attractive destination for multinational corporations seeking to establish or expand their manufacturing facilities. Mazda, one of the world's leading automobile manufacturers, has recognized Thailand's potential and established a robust presence in the country. The Mazda Manufacturing (Thailand) Co., Ltd., located in the Rayong Province, serves as a critical hub for producing vehicles that are not only sold domestically but also exported to various markets around the globe. This facility leverages Thailand's skilled workforce and advanced infrastructure to ensure high-quality production standards. Thailand's well-developed logistics network is another key advantage for manufacturers like Mazda. The country boasts several major ports and airports that facilitate efficient transportation of raw materials and finished goods. Additionally, its proximity to other major markets in Asia makes it an ideal location for regional distribution. The Thai government has also been proactive in supporting industrial growth through initiatives such as the Eastern Economic Corridor (EEC) project. This ambitious development plan aims to transform three eastern provinces into a modern industrial hub by investing heavily in infrastructure improvements and offering attractive incentives to investors. Moreover, Thailand's diverse economy ensures a stable supply chain with access to a wide range of raw materials and components necessary for automotive manufacturing. The country is home to numerous suppliers of automotive parts and accessories, further enhancing its appeal as a manufacturing base. In conclusion, Thailand's combination of favorable business conditions, skilled labor force, advanced infrastructure, and strategic location makes it an ideal choice for global manufacturing facilities like those operated by Mazda. As the automotive industry continues to evolve with technological advancements and changing consumer preferences, Thailand remains poised to play a pivotal role in meeting these demands while driving economic growth both domestically and internationally.
Key Production Processes
In the realm of modern manufacturing, several key production processes play a crucial role in ensuring the efficiency, quality, and reliability of goods. At the heart of these processes are Design and Engineering, where innovative ideas are transformed into tangible products through meticulous planning and technical expertise. Once designs are finalized, Assembly Line Operations take over, streamlining production to maximize output while maintaining precision. However, no manufacturing process is complete without rigorous Quality Control Measures that guarantee every product meets stringent standards. These interconnected processes not only drive local industries but also have a profound impact on Global Manufacturing Facilities, shaping the future of international trade and economic development.
Design and Engineering
Design and engineering are the foundational pillars of Mazda's production processes, ensuring that every vehicle that rolls off the assembly line is a testament to innovation and excellence. At Mazda, the design phase is where creativity meets functionality. The company's designers meticulously craft each model with a focus on aesthetics, ergonomics, and performance. Inspired by the concept of "Kodo: Soul of Motion," Mazda's designs aim to capture the dynamic movement and energy of living creatures in motion. This philosophy translates into sleek lines, aerodynamic shapes, and an overall sense of fluidity that not only enhances visual appeal but also improves aerodynamics and handling. Engineering at Mazda is equally rigorous and forward-thinking. The company invests heavily in research and development to stay at the forefront of automotive technology. From advanced materials like ultra-high-strength steel for enhanced safety and durability to cutting-edge powertrains such as Skyactiv-X engines that combine efficiency with powerful performance, Mazda's engineers continually push boundaries. They leverage sophisticated simulation tools and real-world testing to optimize every component—from suspension systems designed for smooth ride quality to advanced driver-assistance systems (ADAS) that enhance safety without compromising driving pleasure. The integration of design and engineering is seamless at Mazda. Prototypes undergo extensive testing under various conditions to ensure they meet stringent quality standards before entering mass production. This meticulous approach ensures that every Mazda vehicle delivers on its promise of exceptional driving experience while maintaining reliability over time. Additionally, Mazda's commitment to sustainability is evident in its efforts towards reducing environmental impact through eco-friendly manufacturing processes and fuel-efficient technologies. In summary, Mazda's design and engineering processes are integral components of its key production processes. By combining artistic vision with technological prowess, Mazda creates vehicles that are both beautiful and functional—a true reflection of its dedication to excellence in automotive manufacturing.
Assembly Line Operations
Assembly line operations are a cornerstone of modern manufacturing, particularly in the automotive industry where Mazda excels. This highly efficient production method, pioneered by Henry Ford, involves breaking down complex tasks into simpler, repetitive steps that are performed by workers or machines along a continuous flow of production. At Mazda's state-of-the-art facilities, assembly lines are meticulously designed to optimize productivity and quality. Each station on the line is equipped with specialized tools and trained personnel who focus on specific tasks such as engine installation, body welding, and final inspections. The synchronized movement of components and workers ensures that every vehicle moves through the process in a consistent and predictable manner. The assembly line process begins with raw materials and ends with a fully assembled vehicle ready for quality control checks. Mazda's commitment to innovation is evident in its use of advanced robotics and automation technologies that enhance precision and speed while reducing labor costs. For instance, robotic arms can perform delicate tasks like painting and welding with unparalleled accuracy, minimizing human error. Additionally, Mazda incorporates lean manufacturing principles to eliminate waste and maximize efficiency throughout the production cycle. Quality control is an integral part of assembly line operations at Mazda. At various stages along the line, vehicles undergo rigorous inspections using advanced diagnostic tools to ensure they meet stringent quality standards. This includes checks for mechanical performance, safety features, and aesthetic appeal. Any defects or issues identified during these inspections are promptly addressed before the vehicle proceeds further down the line. Moreover, Mazda's emphasis on continuous improvement means that feedback from both employees and customers is regularly incorporated into the production process. This collaborative approach fosters a culture of innovation where new ideas can be tested and implemented swiftly. Training programs for employees also play a crucial role in maintaining high levels of skill proficiency and adaptability as new technologies emerge. In summary, Mazda's assembly line operations exemplify best practices in modern manufacturing by combining traditional efficiency with cutting-edge technology and a relentless pursuit of excellence. By streamlining processes while maintaining rigorous quality standards, Mazda ensures that every vehicle rolling off its assembly lines meets the highest expectations for performance, reliability, and design aesthetics—qualities that have earned Mazda its reputation as a leader in the automotive world.
Quality Control Measures
Quality control measures are integral to the key production processes at Mazda, ensuring that every vehicle meets the highest standards of performance, safety, and reliability. From the initial design phase to the final assembly line, Mazda employs a rigorous quality control framework that encompasses multiple layers of inspection and testing. At the outset, stringent checks are conducted on raw materials and components to ensure they meet precise specifications. This includes thorough examinations for defects and adherence to quality benchmarks set by industry standards. During the manufacturing process, continuous monitoring is implemented through advanced technologies such as automated inspection systems and real-time data analytics. These tools enable immediate detection of any deviations from quality norms, allowing for swift corrective actions to be taken. Additionally, regular audits are conducted by both internal teams and external third-party assessors to validate compliance with international quality standards like ISO 9001. Mazda also places significant emphasis on employee training programs aimed at enhancing their skills in identifying potential issues early in the production cycle. This proactive approach not only helps in maintaining consistency but also fosters a culture of excellence among workers who take pride in their craftsmanship. Furthermore, customer feedback is meticulously analyzed to identify areas for improvement and implement necessary enhancements. The final stages of production involve comprehensive testing protocols including dynamic performance tests on test tracks and static inspections under controlled conditions. These tests simulate various driving scenarios to ensure that vehicles can withstand diverse environmental conditions while delivering optimal performance. By integrating these multifaceted quality control measures into its key production processes, Mazda guarantees that each vehicle rolling off its assembly lines is a testament to its commitment to excellence and customer satisfaction.
Impact on Local Economies
The impact of local economies is a multifaceted topic that encompasses various dimensions, each contributing to the overall health and prosperity of a region. This article delves into three critical areas: Job Creation and Employment, Local Supply Chain Development, and Community Engagement Initiatives. By examining these aspects, we can understand how local economies thrive and grow. Job Creation and Employment are fundamental as they provide financial stability for individuals and families, stimulating consumer spending and economic activity. Local Supply Chain Development is equally important as it fosters innovation, reduces costs, and enhances efficiency by leveraging local resources. Community Engagement Initiatives play a vital role in fostering social cohesion and ensuring that economic growth benefits all members of the community. These elements collectively form the backbone of a robust local economy. As we explore these topics in depth, we will also consider their implications for Global Manufacturing Facilities, highlighting how these local economic dynamics can influence broader industrial strategies on an international scale.
Job Creation and Employment
Creating jobs and fostering employment are crucial components of economic development, particularly in local communities. When a company like Mazda establishes or expands its operations in a region, it generates a ripple effect that benefits the entire local economy. The direct creation of jobs within the company itself is just the beginning; these positions not only provide income for individuals but also stimulate consumer spending, which in turn boosts local businesses such as retail stores, restaurants, and service providers. Additionally, job creation attracts new residents to the area, increasing demand for housing and contributing to real estate growth. This influx of new residents can also lead to an expansion of community services and infrastructure improvements. Moreover, the presence of a major employer like Mazda often encourages other businesses to set up shop nearby. Suppliers and vendors may relocate or establish new facilities to be closer to their primary client, further increasing employment opportunities and economic activity. This clustering effect can transform a region into an industrial hub with diverse sectors contributing to its prosperity. Furthermore, companies often invest in training programs for their employees, enhancing skill levels and making the local workforce more attractive for other potential employers. The impact on local economies extends beyond immediate job creation; it also influences long-term economic stability and growth. As more people gain employment and earn higher incomes, they are more likely to invest in education and healthcare for themselves and their families. This investment in human capital can lead to a more educated and healthier workforce over time, making the region even more appealing for future investments. In summary, job creation by companies such as Mazda has profound effects on local economies by generating direct employment opportunities, stimulating consumer spending, attracting new residents, encouraging business growth through supplier networks, enhancing workforce skills through training programs, and contributing to long-term economic stability through investments in education and healthcare. These multifaceted benefits underscore why fostering job creation remains a cornerstone strategy for promoting vibrant local economies.
Local Supply Chain Development
Local supply chain development is a pivotal strategy for fostering economic growth and resilience in regional communities. By focusing on the cultivation of local suppliers, businesses can significantly enhance the overall efficiency and sustainability of their operations. This approach not only reduces logistical costs and lead times but also promotes economic diversification, as local businesses are empowered to contribute to the production process. The impact on local economies is multifaceted; it stimulates job creation, increases local spending, and fosters innovation. For instance, Mazda's commitment to sourcing materials from nearby suppliers has not only streamlined their manufacturing process but also injected capital into the local economy. This investment in turn supports other businesses and services within the community, creating a ripple effect that bolsters economic stability. Furthermore, local supply chains often lead to better quality control and more agile responses to market demands due to closer proximity between suppliers and manufacturers. This synergy can result in higher-quality products that meet consumer needs more effectively. Additionally, supporting local suppliers aligns with broader sustainability goals by reducing carbon footprints associated with long-distance transportation. In essence, local supply chain development is a win-win strategy that benefits both businesses like Mazda and the communities they operate within by fostering economic vitality and environmental responsibility.
Community Engagement Initiatives
Community engagement initiatives play a pivotal role in fostering positive relationships between businesses and local communities, ultimately contributing to the economic vitality of the region. These initiatives not only enhance corporate social responsibility but also create mutually beneficial outcomes. For instance, Mazda's community engagement programs in Hiroshima, Japan, where the company is headquartered, have significantly impacted local economies. Mazda collaborates with local schools to provide educational resources and vocational training, ensuring that future generations are equipped with the skills needed to contribute to the workforce. Additionally, Mazda supports various community development projects such as infrastructure improvements and cultural events, which help in attracting tourists and boosting local businesses. By investing in these initiatives, Mazda not only strengthens its reputation as a responsible corporate citizen but also stimulates economic growth by creating jobs and increasing consumer spending within the community. Furthermore, these efforts foster a sense of community pride and loyalty among residents who are more likely to support local businesses that contribute positively to their environment. Overall, community engagement initiatives like those undertaken by Mazda serve as a model for how businesses can effectively integrate into their local ecosystems while driving sustainable economic development.