Where Are Mazdas Made

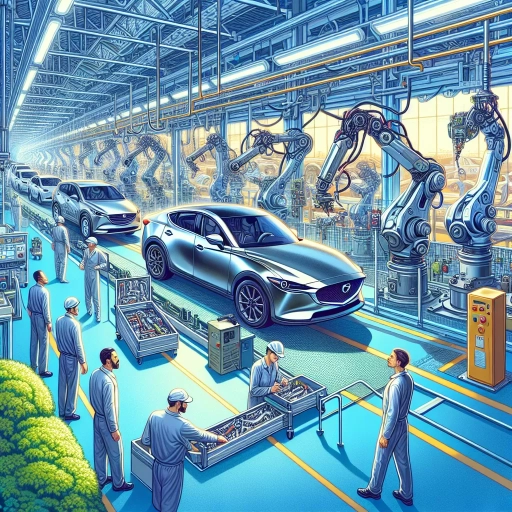
Mazda, a renowned Japanese automaker, has established a global presence with its extensive network of manufacturing facilities. The company's commitment to quality and innovation is reflected in the meticulous production process that ensures each vehicle meets the highest standards. Beyond its operational efficiency, Mazda's manufacturing activities have a significant impact on local economies, contributing to job creation and economic growth. This article delves into the intricacies of Mazda's global manufacturing facilities, providing an overview of the production process and exploring the economic benefits that arise from these operations. By understanding where Mazdas are made and how they are produced, we can appreciate the complexity and value added by this automotive giant. Let's begin by examining Mazda's global manufacturing facilities.
Global Manufacturing Facilities
In the ever-evolving landscape of global manufacturing, several countries have emerged as pivotal hubs for industrial production. Japan, renowned for its cutting-edge technology and precision engineering, has long been a leader in automotive and electronics manufacturing. China, with its vast workforce and strategic economic policies, has become the world's largest manufacturing nation, producing everything from textiles to high-tech gadgets. Thailand, meanwhile, has carved out a niche in the automotive and food processing sectors, leveraging its favorable business environment and skilled labor force. These countries not only drive innovation but also set global standards in efficiency and quality. As we delve into the specifics of each nation's contributions to the global manufacturing landscape, it becomes clear that their unique strengths collectively shape the future of Global Manufacturing Facilities.
Japan
Japan is renowned for its cutting-edge manufacturing facilities, which play a pivotal role in the global automotive industry. Mazda, one of Japan's leading automobile manufacturers, leverages the country's advanced infrastructure and innovative technologies to produce high-quality vehicles. Located primarily in Hiroshima and Hofu, Mazda's state-of-the-art factories are equipped with sophisticated machinery and adhere to stringent quality control standards. These facilities benefit from Japan's highly skilled workforce, rigorous training programs, and a culture of continuous improvement known as "kaizen." The strategic location of these plants allows for efficient supply chain management and access to key markets both domestically and internationally. Additionally, Japan's robust research and development sector ensures that Mazda stays at the forefront of automotive innovation, incorporating advanced technologies such as hybrid engines and autonomous driving systems into their models. The synergy between technological prowess, skilled labor, and strategic positioning makes Japan an ideal hub for Mazda's global manufacturing operations. This combination not only enhances productivity but also contributes significantly to the country's economic growth while maintaining its reputation as a leader in global manufacturing excellence.
China
China has emerged as a pivotal player in the global manufacturing landscape, particularly in the automotive sector. As one of the world's largest economies, China offers a unique blend of advanced infrastructure, skilled workforce, and favorable business policies that attract major international brands like Mazda. The country's extensive network of high-tech manufacturing facilities ensures efficient production processes and stringent quality control measures. For instance, Mazda's partnership with FAW Group in Changchun has enabled the production of models such as the Mazda3 and CX-5, leveraging China's robust supply chain and logistics capabilities to meet both domestic and international demand. Additionally, China's commitment to innovation is evident through its investments in cutting-edge technologies like robotics and artificial intelligence, further enhancing manufacturing efficiency and precision. The strategic location of these facilities also facilitates seamless export operations to other regions, making China an indispensable hub for global automotive manufacturing. As Mazda continues to expand its footprint in China, it is clear that this partnership will drive future growth and innovation in the industry.
Thailand
Thailand, often referred to as the "Detroit of Asia," has emerged as a pivotal hub for global manufacturing facilities, particularly in the automotive sector. The country's strategic location at the heart of Southeast Asia, coupled with its well-developed infrastructure and favorable business environment, makes it an attractive destination for multinational corporations like Mazda. Thailand's robust supply chain and extensive network of ports facilitate efficient logistics and transportation, ensuring that components and finished products can be swiftly moved both domestically and internationally. Additionally, the Thai government has implemented various incentives to attract foreign investment, including tax breaks, subsidies, and streamlined regulatory processes. These measures have encouraged companies to establish large-scale manufacturing facilities in Thailand, contributing significantly to the country's economic growth. Mazda's decision to set up operations in Thailand underscores the nation's reputation as a reliable partner in global manufacturing. The company benefits from Thailand's skilled workforce and competitive labor costs while leveraging local expertise in automotive production. Furthermore, Thailand's commitment to innovation is evident through initiatives such as the Eastern Economic Corridor (EEC), which aims to transform the region into a high-tech industrial hub by investing heavily in advanced technologies and infrastructure development. This forward-thinking approach aligns perfectly with Mazda's vision of integrating cutting-edge technology into its vehicles. As a result, Thailand continues to play a crucial role in Mazda's global strategy, serving not only as a production base but also as a key player in driving innovation within the automotive industry.
Production Process Overview
In today's fast-paced industrial landscape, the production process is a multifaceted and intricate journey that transforms raw materials into finished products. This article provides an in-depth overview of the production process, highlighting three critical components: Design and Development, Manufacturing Techniques, and Quality Control Measures. The Design and Development phase lays the groundwork by conceptualizing and refining product ideas through rigorous research and prototyping. Manufacturing Techniques then bring these designs to life using advanced machinery and innovative methods to ensure efficiency and precision. Finally, Quality Control Measures are implemented to guarantee that every product meets stringent standards of excellence. Understanding these elements is essential for maintaining high-quality output in global manufacturing facilities.
Design and Development
In the realm of automotive manufacturing, design and development are pivotal stages that precede the production process. At Mazda, these phases are meticulously executed to ensure that every vehicle embodies the brand's philosophy of "Jinba Ittai," or the harmony between horse and rider. The design process begins with conceptual sketches and computer-aided design (CAD) models, where designers blend aesthetics with functionality. This stage is crucial as it sets the foundation for the vehicle's overall look and feel, including its aerodynamics, ergonomics, and brand identity. Once the design is finalized, it transitions into the development phase. Here, engineers conduct rigorous testing and simulation to validate performance metrics such as speed, fuel efficiency, safety features, and durability. Prototypes are built for real-world testing under various conditions to identify any potential issues before mass production begins. This iterative process ensures that every Mazda model meets stringent quality standards while delivering exceptional driving experiences. Mazda's commitment to innovation is evident in its use of advanced technologies like Skyactiv-X engines and i-ACTIV AWD systems. These technologies not only enhance performance but also contribute to a more sustainable future by improving fuel efficiency and reducing emissions. The integration of cutting-edge materials like ultra-high-strength steel further enhances structural integrity while minimizing weight. Throughout both design and development stages, Mazda collaborates closely with suppliers to source high-quality components that align with their vision for excellence. This collaborative approach ensures consistency across all models produced globally—from Hiroshima in Japan to Salamanca in Mexico—maintaining a uniform standard of quality regardless of where they are manufactured. Ultimately, Mazda's meticulous attention to detail during these initial stages lays the groundwork for a seamless production process. By combining visionary design with rigorous development protocols, Mazda creates vehicles that not only captivate visually but also deliver unparalleled driving experiences. This holistic approach underscores why Mazda stands out in an increasingly competitive automotive landscape.
Manufacturing Techniques
Manufacturing techniques play a pivotal role in the production process, ensuring that products meet stringent quality standards while maintaining efficiency and cost-effectiveness. At Mazda, these techniques are meticulously refined to produce vehicles that are not only aesthetically pleasing but also technologically advanced and environmentally friendly. The journey begins with Computer-Aided Design (CAD) and Computer-Aided Manufacturing (CAM), where precise digital models are created and simulated to optimize design elements such as aerodynamics, structural integrity, and performance. This digital blueprint is then translated into physical prototypes using advanced 3D printing technologies, allowing for rapid iteration and refinement. Once the design is finalized, the manufacturing process shifts to the assembly line. Here, Mazda employs a blend of traditional craftsmanship and cutting-edge automation. Robots equipped with artificial intelligence (AI) handle tasks requiring precision and speed, such as welding and painting, while skilled technicians focus on more complex operations like engine assembly and quality control checks. The use of Industry 4.0 technologies—such as Internet of Things (IoT) sensors and machine learning algorithms—enables real-time monitoring of production processes, allowing for immediate adjustments to maintain optimal performance. Sustainability is another key aspect of Mazda's manufacturing techniques. The company has implemented various eco-friendly practices throughout its facilities worldwide. For instance, Mazda's Hiroshima plant in Japan features extensive solar panel installations that generate a significant portion of the plant's energy needs. Additionally, water recycling systems minimize waste by reusing water from various stages of production. Innovative materials also play a crucial role in Mazda's manufacturing techniques. The company has developed lightweight yet robust materials like Skyactiv-X technology for engines and advanced high-strength steel for body structures. These innovations not only enhance vehicle performance but also contribute to reduced emissions by improving fuel efficiency. Quality assurance is an integral part of every stage in Mazda's production process. Rigorous testing protocols ensure that each vehicle meets or exceeds industry standards before it leaves the factory floor. From crash tests to performance evaluations on state-of-the-art dynamometers, every aspect is meticulously scrutinized to guarantee customer satisfaction and safety. In conclusion, Mazda's commitment to advanced manufacturing techniques underscores its dedication to producing high-quality vehicles that combine style with substance. By leveraging technology alongside traditional craftsmanship—and prioritizing sustainability—Mazda continues to set benchmarks within the automotive industry while delivering exceptional driving experiences for its customers around the world.
Quality Control Measures
Quality control measures are an integral part of the production process at Mazda, ensuring that every vehicle meets the highest standards of performance, safety, and reliability. From the initial design phase to the final assembly line, Mazda employs a rigorous quality control framework that involves multiple checkpoints and inspections. At the outset, stringent design verification tests are conducted to validate the engineering specifications and performance criteria of new models. This includes simulations, prototype testing, and feedback from test drivers to identify any potential issues before mass production begins. Once production commences, quality control measures are implemented at every stage. Raw materials and components undergo thorough inspections upon arrival to ensure they meet Mazda's stringent quality standards. During manufacturing, continuous monitoring systems track production processes in real-time, allowing for immediate intervention if any deviations are detected. Skilled technicians perform regular checks on machinery and equipment to prevent malfunctions that could affect product quality. On the assembly line itself, each vehicle undergoes a series of rigorous inspections. These include visual checks for defects or irregularities in paintwork and bodywork as well as functional tests to verify that all systems—from electrical to mechanical—are operating correctly. Additionally, random sampling is used to conduct more detailed inspections on select vehicles to ensure consistency across the entire production run. Mazda also incorporates advanced technology into its quality control processes. For instance, automated inspection systems equipped with high-resolution cameras and sensors can detect even minute imperfections that might be missed by human inspectors. Furthermore, data analytics play a crucial role in identifying trends or patterns that could indicate potential quality issues before they become major problems. Customer feedback is another critical component of Mazda's quality control strategy. Post-sales data collection helps identify any recurring issues or areas for improvement which are then addressed through continuous improvement initiatives within the manufacturing process. This proactive approach ensures that Mazda vehicles not only meet but exceed customer expectations in terms of reliability and performance. In summary, Mazda's commitment to quality control is evident throughout its entire production process—from initial design through final assembly and beyond into post-sales monitoring. By combining traditional inspection methods with cutting-edge technology and leveraging customer feedback for ongoing improvement initiatives, Mazda consistently delivers high-quality vehicles that stand out in the automotive market for their excellence in performance and reliability.
Impact on Local Economies
The impact of local economies is a multifaceted topic that encompasses various dimensions, each contributing to the overall health and growth of a community. This article delves into three critical areas: Employment Opportunities, Local Supply Chain Integration, and Community Development Initiatives. By examining these aspects, we can understand how local economies thrive and evolve. Employment Opportunities highlight the creation of jobs and the role they play in stabilizing communities. Local Supply Chain Integration explores how businesses can source materials and services from within their region, fostering economic interdependence. Community Development Initiatives focus on projects that enhance public services, infrastructure, and quality of life for residents. These elements collectively shape the economic landscape of a region. Understanding their dynamics is essential for policymakers, business leaders, and community members alike. As we explore these topics in depth, we will also consider how they can be leveraged to support the transition to Global Manufacturing Facilities.
Employment Opportunities
The establishment of Mazda manufacturing facilities in various regions significantly impacts local economies by creating a plethora of employment opportunities. These opportunities not only benefit the immediate workforce but also have a ripple effect on the broader community. Mazda's commitment to hiring local talent ensures that residents gain access to stable, well-paying jobs that contribute to their economic stability and growth. The influx of skilled and unskilled labor positions caters to a diverse range of professionals, from engineers and technicians to administrative staff and production line workers. This diversity in job offerings helps in reducing unemployment rates, thereby enhancing the overall quality of life for individuals and families within the region. Moreover, the presence of a major automotive manufacturer like Mazda stimulates economic activity through indirect employment opportunities. Local businesses such as suppliers, logistics companies, and service providers experience increased demand for their services, leading to further job creation in these sectors. Additionally, the growth in disposable income among employees often results in higher consumer spending at local shops, restaurants, and other retail establishments. This increased consumer activity boosts local economic activity and fosters a more vibrant community environment. Mazda's investment in employee development programs also plays a crucial role in enhancing local human capital. By providing training and upskilling opportunities, Mazda equips its workforce with advanced skills that are transferable across industries. This not only improves productivity within the company but also contributes to a more skilled labor pool within the region. Furthermore, Mazda's partnerships with educational institutions for apprenticeships and internships help bridge the gap between education and employment by preparing students for real-world challenges. The positive impact on local economies extends beyond direct employment benefits; it influences broader societal dynamics as well. Stable employment contributes to lower crime rates and improved public health outcomes as individuals have better access to healthcare services due to their employment status. Moreover, with increased financial security comes greater civic engagement as residents become more invested in community development projects and initiatives. In conclusion, Mazda's manufacturing operations serve as a catalyst for economic growth by generating substantial employment opportunities both directly through its facilities and indirectly through supporting industries. By fostering stable employment conditions and investing in workforce development programs, Mazda not only enhances individual livelihoods but also contributes significantly to the prosperity of local communities where its plants are located.
Local Supply Chain Integration
Local supply chain integration is a strategic approach that enhances the efficiency and resilience of businesses by leveraging local resources and partnerships. By focusing on regional suppliers, companies can significantly reduce transportation costs and lead times, thereby improving their overall operational agility. This localized approach also fosters stronger community relationships, as it often involves collaborating with local businesses and supporting regional economic development. For instance, Mazda's manufacturing facilities in Hiroshima, Japan, have been instrumental in integrating local suppliers into their supply chain. This integration not only ensures the quality of components but also contributes to the economic growth of the surrounding area by creating jobs and stimulating local investment. Additionally, local supply chains are more adaptable to market changes and disruptions due to their proximity, allowing for quicker responses to demand fluctuations or supply chain disruptions. This adaptability is particularly beneficial in industries like automotive manufacturing where timely delivery of high-quality parts is crucial for maintaining production schedules. Furthermore, integrating local suppliers can lead to more sustainable practices as it reduces carbon emissions from long-distance transportation. Mazda's commitment to sustainability through its local supply chain initiatives aligns with global trends towards environmentally conscious business practices. Overall, local supply chain integration offers a multifaceted benefit that enhances operational efficiency while contributing positively to the local economy and environment.
Community Development Initiatives
Community development initiatives play a pivotal role in shaping the economic landscape of local communities. These initiatives, often driven by a combination of public, private, and non-profit sectors, aim to enhance the quality of life for residents while fostering sustainable economic growth. By investing in infrastructure projects such as roads, public transportation systems, and community facilities, these initiatives create an environment conducive to business development and job creation. For instance, the construction of new schools and healthcare facilities not only improves access to essential services but also attracts families and professionals who contribute to the local workforce. Moreover, community development initiatives frequently focus on revitalizing urban areas through urban renewal projects. These efforts can transform neglected neighborhoods into vibrant hubs of activity by promoting small businesses, cultural events, and recreational spaces. This transformation not only boosts property values but also stimulates local spending as residents and visitors alike patronize local shops and restaurants. Additionally, community development programs often include training programs that equip residents with skills necessary for employment in emerging industries. This workforce development is crucial for attracting businesses looking for a skilled labor force. Another significant aspect of community development is its impact on social cohesion. Initiatives that promote community engagement through volunteer opportunities or community events help build stronger social bonds among residents. This sense of community can lead to increased civic participation and a more resilient society better equipped to handle economic challenges. Furthermore, many community development projects incorporate environmental sustainability measures such as green spaces or renewable energy installations which not only enhance the aesthetic appeal of an area but also contribute positively towards environmental conservation efforts. In conclusion, community development initiatives are multifaceted strategies that have profound impacts on local economies by creating jobs, stimulating investment in infrastructure and businesses, enhancing social cohesion among residents while promoting environmental sustainability practices. As such they serve as essential tools for fostering inclusive growth that benefits all members within a given locality thereby contributing significantly towards overall economic prosperity at both regional & national levels alike.