When Performing A Walk Around Where Should You Start

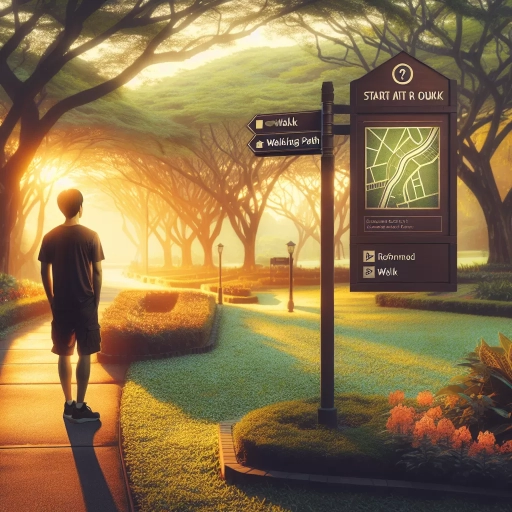
When performing a walk-around, it is crucial to approach the task with a structured and informed mindset. A thorough walk-around is not just a casual inspection; it requires meticulous attention to detail and a clear understanding of its importance. This article will guide you through the essential steps and best practices for conducting an effective walk-around, ensuring that you cover all key areas comprehensively. We will delve into the significance of a thorough walk-around, highlighting why it is indispensable in various contexts. Additionally, we will identify the critical areas that demand your focus during the inspection. Finally, we will provide actionable best practices to enhance your walk-around process. By understanding these elements, you can ensure that your walk-around is both efficient and effective. Let's begin by exploring the importance of a thorough walk-around.
Understanding the Importance of a Thorough Walk-Around
In today's fast-paced and dynamic work environments, maintaining a safe and compliant workplace is paramount. One crucial practice that significantly contributes to achieving this goal is the thorough walk-around. This meticulous inspection process not only helps in identifying potential hazards but also ensures compliance with regulatory standards. Moreover, it plays a pivotal role in enhancing the overall safety culture within an organization. By understanding the importance of a thorough walk-around, businesses can proactively mitigate risks, adhere to legal requirements, and foster a culture of safety awareness among employees. In this article, we will delve into these aspects—identifying potential hazards, ensuring compliance with regulations, and enhancing workplace safety culture—to underscore the significance of integrating thorough walk-arounds into daily operations. Understanding the importance of a thorough walk-around is essential for creating a safer, more efficient work environment.
Identifying Potential Hazards
When performing a walk-around, identifying potential hazards is crucial for ensuring safety and efficiency. Start by thoroughly inspecting the exterior of the vehicle, paying close attention to tires, brakes, and suspension components. Check tire pressure and look for signs of wear or damage such as uneven tread patterns or bulges. Inspect brake pads and rotors for excessive wear or damage that could lead to brake failure. Also, examine suspension components like shock absorbers and springs for any signs of leakage or damage. Next, move on to inspecting the vehicle's body and frame. Look for any dents, rust spots, or other structural damage that could compromise the vehicle's integrity. Check all lights including headlights, taillights, turn signals, and brake lights to ensure they are functioning properly. Make sure mirrors are securely attached and not damaged. Moving inside the vehicle, inspect the dashboard for any warning lights that may indicate issues with systems like oil pressure, temperature control, or electrical systems. Check all gauges to ensure they are within normal operating ranges. Test all controls such as wipers, defrosters, and heating/cooling systems to ensure they are functioning correctly. Finally, inspect under the hood where critical components like batteries, belts (serpentine belt), hoses (coolant/radiator), fluids (oil/coolant/transmission), air filters/cabin filters should be checked regularly. Ensure battery terminals are clean and secure; belts should show no signs of cracking/fraying; hoses should be free from leaks/cracks; fluid levels should be at recommended levels without leaks; air filters should be clean/replaced if necessary. By starting your walk-around with these steps you can systematically identify potential hazards before they become major issues ensuring both safety on roadways as well as prolonging lifespan of your vehicle through proactive maintenance practices.
Ensuring Compliance with Regulations
Ensuring compliance with regulations is a critical aspect of performing a thorough walk-around, as it not only helps in maintaining safety standards but also avoids legal repercussions. When starting your walk-around, it's essential to begin at the vehicle's front and systematically work your way around to ensure nothing is overlooked. This structured approach helps in identifying any potential issues early on. Begin by inspecting the front bumper, grille, and headlights for any damage or obstructions. Move on to check the condition of the windshield wipers and ensure they are functioning properly. Next, inspect the tires for adequate tread depth and proper inflation levels; underinflated tires can lead to reduced fuel efficiency and increased risk of accidents. As you proceed to the sides of the vehicle, pay close attention to mirrors, windows, and doors for any signs of damage or wear. Ensure all mirrors are securely attached and provide clear visibility without any obstructions. Check that all windows are free from cracks or chips that could impair vision while driving. The doors should open smoothly without any signs of rust or corrosion. Moving towards the rear section, inspect the taillights, brake lights, and turn signals to ensure they are functioning correctly. A faulty light can lead to serious safety issues on the road. Also, check for any dents or scratches on the rear bumper that might indicate previous accidents. Finally, move underneath the vehicle where you should look for leaks in fluids such as oil, coolant, or brake fluid which could indicate serious mechanical issues if left unchecked. Additionally, inspect suspension components like shock absorbers and springs for signs of wear which could affect handling stability. By following this methodical approach during your walk-around inspection process not only ensures compliance with regulatory requirements but also helps prevent accidents caused by overlooked maintenance issues thereby enhancing overall safety standards while driving on public roads.
Enhancing Workplace Safety Culture
Enhancing Workplace Safety Culture is a multifaceted endeavor that begins with a thorough walk-around. This proactive approach ensures that all aspects of the workplace are scrutinized for potential hazards and areas for improvement. When performing a walk-around, it is essential to start by identifying high-risk zones and critical operations. Begin at the entrance points where employees and visitors first interact with the environment, noting any immediate hazards such as slippery floors or obstructed pathways. Next, move through production areas, observing machinery in operation and ensuring proper guarding and safety protocols are in place. Pay particular attention to storage facilities where chemicals or heavy materials are kept, verifying that they are labeled correctly and stored according to regulations. As you proceed through the facility, engage with employees to gather insights into their daily experiences and concerns. This not only fosters a sense of ownership but also provides valuable firsthand information about potential risks that might otherwise go unnoticed. Additionally, inspect break rooms and restrooms for cleanliness and adherence to health standards. The walk-around should also include reviewing safety signage, emergency exit routes, fire extinguishers, and first aid kits to ensure they are accessible and well-maintained. A thorough walk-around also involves checking for ergonomic issues at workstations; ensuring that employees have adequate lighting, comfortable seating options, and tools designed to reduce strain injuries. Furthermore, it’s crucial to review training records and conduct spot checks on personal protective equipment (PPE) usage compliance. By systematically addressing these areas during your walk-around, you can identify vulnerabilities early on and implement corrective measures before incidents occur. Moreover, leveraging technology such as mobile apps or digital checklists can streamline the process by providing real-time data collection capabilities which help track findings over time. This allows for more effective trend analysis which can inform long-term safety strategies. Ultimately enhancing workplace safety culture requires continuous vigilance combined with proactive measures like regular walk-arounds which serve as both preventive tools against accidents while fostering an environment where employee well-being is paramount thus leading towards higher productivity overall satisfaction among workforce members alike
Key Areas to Focus On During the Walk-Around
Conducting a thorough walk-around is a crucial aspect of maintaining workplace safety and efficiency. This comprehensive process involves meticulously examining various key areas to identify potential hazards, improve practices, and ensure compliance with safety regulations. The walk-around focuses on three primary areas: High-Risk Zones and Equipment, Employee Workstations and Practices, and Environmental Factors and Conditions. By scrutinizing high-risk zones and equipment, organizations can pinpoint mechanical vulnerabilities that could lead to accidents. Evaluating employee workstations and practices helps in identifying unsafe behaviors or inadequate training that might compromise safety standards. Lastly, assessing environmental factors such as lighting, ventilation, and ergonomics ensures a conducive working environment. Understanding the importance of a thorough walk-around is essential for creating a safer workplace where employees can perform their duties without undue risk.
High-Risk Zones and Equipment
When performing a walk-around, it is crucial to focus on high-risk zones and equipment to ensure comprehensive safety and efficiency. High-risk zones are areas where potential hazards are more likely to occur, such as near heavy machinery, electrical panels, or chemical storage facilities. These areas require meticulous inspection for signs of wear and tear, improper use, or environmental factors that could lead to accidents. For instance, in manufacturing plants, areas around presses and cutting machines are high-risk due to the potential for mechanical failure or operator error. Similarly, in chemical plants, zones near storage tanks and processing units demand careful attention due to the risk of leaks or explosions. Equipment inspection is another key area during a walk-around. This includes checking machinery for proper functioning and maintenance records. For example, in construction sites, cranes and hoists must be regularly inspected for structural integrity and operational reliability. In hospitals, medical devices like ventilators and defibrillators need frequent checks to ensure they are in good working order. Additionally, safety equipment such as fire extinguishers and emergency showers should be easily accessible and fully functional. Moreover, high-risk zones often involve specific types of equipment that require specialized knowledge for proper inspection. For instance, electrical equipment like transformers and circuit breakers need to be checked by trained personnel who can identify signs of overheating or electrical stress. In industrial settings with hazardous materials handling systems (HMHS), regular inspections are essential to prevent spills or leaks that could have severe environmental impacts. In summary, focusing on high-risk zones and equipment during a walk-around is paramount for maintaining safety standards and preventing accidents. By identifying these critical areas early on and conducting thorough inspections regularly, organizations can mitigate risks effectively while ensuring operational efficiency remains high.
Employee Workstations and Practices
When performing a walk-around, one of the key areas to focus on is Employee Workstations and Practices. This involves a thorough examination of the physical workspace and the daily routines of employees to ensure they are aligned with safety protocols and efficiency standards. Start by observing the layout of workstations, ensuring that they are well-organized, clutter-free, and ergonomically designed to prevent injuries. Check for proper lighting, ventilation, and temperature control to create a comfortable working environment. Next, assess the tools and equipment being used. Are they in good condition? Are they properly maintained? Ensure that all machinery is regularly serviced and that employees have access to necessary personal protective equipment (PPE). Additionally, evaluate how tasks are being performed. Are there any unsafe practices or shortcuts that could lead to accidents? Encourage open communication with employees to understand their challenges and gather feedback on potential improvements. Another critical aspect is adherence to company policies and procedures. Verify if employees are following established guidelines for handling materials, operating machinery, and performing tasks. This includes checking for proper labeling of hazardous materials, correct usage of safety signs, and compliance with emergency response plans. Moreover, observe how employees interact with each other during their duties. A positive work culture can significantly impact productivity and safety; therefore, it's important to foster an environment where teamwork is encouraged but also where individual responsibilities are clearly defined. Finally, consider implementing continuous training programs aimed at enhancing both technical skills and safety awareness among employees. Regular training sessions can help identify gaps in knowledge or practice that might otherwise go unnoticed until an incident occurs. By focusing on these aspects during your walk-around inspections—workstation layout, tool maintenance, task execution adherence to policies—and fostering a supportive work culture while providing ongoing training—you can significantly improve workplace safety while boosting overall efficiency.
Environmental Factors and Conditions
When performing a walk-around, one of the key areas to focus on is environmental factors and conditions. This encompasses a broad range of elements that can significantly impact the safety, efficiency, and overall quality of operations. Environmental factors include weather conditions such as temperature, humidity, wind speed, and precipitation. These elements can affect equipment performance, worker comfort, and the integrity of materials. For instance, extreme temperatures can cause machinery to malfunction or degrade faster than usual. Similarly, high humidity levels can lead to corrosion in metal components or moisture accumulation in electrical systems. Another critical aspect is lighting conditions. Adequate lighting is essential for visibility and safety; insufficient lighting can lead to accidents or errors in judgment. Natural light should be maximized during daytime operations by ensuring windows are clean and unobstructed. Artificial lighting should be well-maintained with regular bulb replacements and proper positioning to avoid glare or shadows. Noise levels also fall under environmental conditions that need careful consideration. High noise levels not only pose a risk to hearing health but also create distractions that could lead to accidents. Implementing noise-reducing measures such as soundproofing materials or personal protective equipment (PPE) like earplugs is crucial. Additionally, air quality is another vital factor that affects both human health and equipment longevity. Poor air quality due to dust particles, chemical fumes, or other pollutants can cause respiratory issues among workers and damage machinery over time. Regular monitoring of air quality through sensors or periodic inspections helps in maintaining a safe working environment. Furthermore, ground conditions play an important role in ensuring stability and preventing slips/trips/falls hazards. Uneven surfaces, oil spills, or water puddles must be addressed promptly by cleaning up spills immediately and using warning signs until the area is safe again. Lastly, biological factors such as pest infestations (e.g., rodents) need attention as they can contaminate products or spread diseases among workers. Regular pest control measures along with maintaining cleanliness standards are essential for preventing these issues. In summary, focusing on environmental factors during a walk-around ensures that all potential risks are identified early on so appropriate actions can be taken promptly thereby enhancing workplace safety & efficiency while protecting assets from damage caused by adverse environmental conditions
Best Practices for Conducting an Effective Walk-Around
Conducting an effective walk-around is a crucial aspect of maintaining a safe, efficient, and productive work environment. This practice involves systematically inspecting the workplace to identify potential hazards, assess operational efficiency, and ensure compliance with regulations. To achieve these goals, it is essential to employ best practices that enhance the thoroughness and impact of the walk-around process. Utilizing checklists and documentation tools helps ensure that all critical areas are examined consistently and that findings are accurately recorded. Engaging employees in the process not only fosters a culture of safety and responsibility but also leverages their unique insights into daily operations. Finally, following up on identified issues ensures that corrective actions are implemented promptly, preventing minor problems from escalating into major concerns. By understanding these best practices, organizations can conduct thorough walk-arounds that contribute significantly to their overall success. Understanding the importance of a thorough walk-around is key to implementing these strategies effectively.
Using Checklists and Documentation Tools
When performing a walk-around, it is essential to start with a structured approach to ensure thoroughness and efficiency. Utilizing checklists and documentation tools is a best practice that can significantly enhance the effectiveness of your walk-around. A checklist serves as a comprehensive guide, outlining all critical areas and items that need to be inspected. This helps in maintaining consistency and prevents overlooking important details. For instance, if you are conducting a walk-around in an industrial setting, your checklist might include items such as machinery condition, safety equipment availability, and environmental hazards. Documentation tools are equally vital as they provide a record of findings and actions taken during the walk-around. These tools can range from simple paper-based forms to sophisticated digital apps that allow real-time data entry and photo documentation. Digital tools often offer additional features like GPS tagging for location-specific notes and automated reporting capabilities that streamline the process of generating reports post-inspection. Moreover, checklists and documentation tools facilitate better communication among team members involved in the walk-around process. They ensure that everyone is on the same page regarding what needs to be inspected and what has been observed. This collaborative aspect is particularly beneficial when multiple stakeholders are involved or when there is a need for follow-up actions based on initial findings. Incorporating these tools into your walk-around routine also aids in compliance with regulatory requirements by providing an auditable trail of inspections conducted. This not only helps in maintaining legal standards but also contributes to building trust with clients or customers who may require evidence of regular maintenance or safety checks. Additionally, using checklists and documentation tools can lead to continuous improvement over time. By analyzing historical data from past inspections, you can identify recurring issues or trends that may indicate underlying problems requiring more substantial interventions. This proactive approach helps in preventing potential failures or accidents before they occur. In summary, starting your walk-around with well-structured checklists and leveraging advanced documentation tools sets the foundation for an effective inspection process. These practices ensure thoroughness, enhance communication among team members, support compliance efforts, and contribute to ongoing improvement initiatives—all crucial elements for conducting successful walk-arounds that yield actionable insights and drive operational excellence.
Engaging Employees in the Process
Engaging employees in the process is a crucial aspect of conducting an effective walk-around. This involves not only observing and noting conditions but also actively involving staff members to gather insights and foster a sense of ownership. Start by communicating the purpose and benefits of the walk-around clearly, ensuring that employees understand how their participation contributes to improving workplace safety and efficiency. Encourage open dialogue by asking questions about their daily tasks, challenges they face, and suggestions for improvement. This not only provides valuable firsthand information but also boosts morale as employees feel valued and heard. Additionally, consider involving a diverse group of employees from different departments to ensure comprehensive perspectives. By doing so, you can identify potential issues before they escalate into major problems and implement solutions that are practical and effective. Furthermore, recognize and reward employee contributions during the walk-around process to reinforce positive behaviors and encourage continued engagement. This collaborative approach not only enhances the effectiveness of your walk-around but also cultivates a culture of continuous improvement within your organization.
Following Up on Identified Issues
When performing a walk-around, it is crucial to start by identifying potential issues. This involves meticulously observing the environment, equipment, and processes to pinpoint any discrepancies or areas of concern. Once these issues are identified, following up on them is essential to ensure that corrective actions are taken promptly and effectively. Effective follow-up involves documenting each issue with detailed descriptions and photographs for future reference. This documentation should include the date, time, location, and a clear description of the problem along with any relevant images or videos. Next, prioritize the identified issues based on their severity and potential impact on safety, productivity, and overall operations. High-priority issues that pose immediate risks should be addressed first. Communicate these findings clearly to relevant stakeholders such as supervisors, maintenance teams, or safety officers. Ensure that each issue is assigned to a responsible person who will oversee its resolution. Regularly review the status of each issue during subsequent walk-arounds to track progress. Use checklists or digital tools to keep track of ongoing actions and deadlines for completion. Provide feedback and support where necessary to ensure that corrective actions are implemented correctly. Additionally, foster a culture of continuous improvement by encouraging employees to report any new issues they encounter during their daily activities. Recognize and reward employees who contribute significantly to identifying and resolving problems. Finally, incorporate lessons learned from addressing these issues into future walk-around protocols to enhance their effectiveness over time. By systematically following up on identified issues during walk-arounds, organizations can maintain high standards of safety and efficiency while fostering a proactive approach towards problem-solving within their workforce.