Where Are Subarus Made

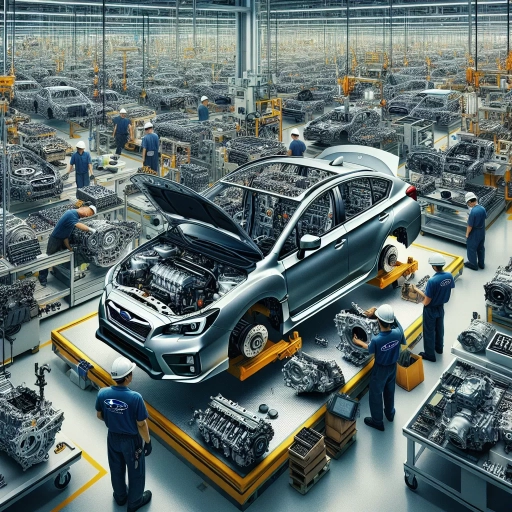
Subaru, known for its all-wheel-drive vehicles and commitment to quality, has a rich history of manufacturing excellence. The company's dedication to producing high-performance cars that are both reliable and environmentally friendly has garnered a loyal following worldwide. But where are these iconic vehicles made? This article delves into the global manufacturing facilities of Subaru, exploring the extensive network of production sites that span across continents. We will also provide an overview of the meticulous production process that ensures every Subaru meets stringent quality standards. Additionally, we will examine the technological innovations that have revolutionized Subaru's manufacturing processes, making them more efficient and sustainable. By understanding these facets, readers will gain a comprehensive insight into what makes Subaru stand out in the automotive industry. Let's begin by exploring Subaru's global manufacturing facilities.
Global Manufacturing Facilities
In today's interconnected world, global manufacturing facilities play a pivotal role in shaping the economic landscape. These facilities are not only hubs of industrial activity but also drivers of innovation and technological advancement. The article delves into the significance of global manufacturing facilities by examining three key regions: Japan, known for its cutting-edge technology and precision engineering; the United States, a leader in diverse manufacturing sectors; and other countries that are rapidly emerging as major players in the global manufacturing arena. By exploring these regions, we gain insights into how different approaches to manufacturing can influence global supply chains, economic growth, and technological progress. This comprehensive overview aims to provide readers with a deeper understanding of the complex dynamics at play within global manufacturing facilities.
Japan
Japan is renowned for its cutting-edge manufacturing facilities, particularly in the automotive sector. Subaru, a prominent Japanese automaker, leverages the country's advanced technology and meticulous craftsmanship to produce high-quality vehicles. Japan's manufacturing prowess is rooted in its robust infrastructure, highly skilled workforce, and stringent quality control measures. The nation's commitment to innovation is evident in its state-of-the-art factories equipped with the latest machinery and automation systems. Subaru's manufacturing facilities in Japan are exemplary models of this excellence, where precision engineering meets rigorous testing protocols to ensure every vehicle meets the highest standards of performance and reliability. Additionally, Japan's strategic location facilitates efficient global supply chain management and export logistics, making it an ideal hub for international automotive production. The synergy between technological advancements and traditional Japanese attention to detail has positioned Subaru as a leader in the global automotive industry.
United States
The United States is a pivotal hub for global manufacturing facilities, particularly in the automotive sector. Subaru, a renowned Japanese automaker, has significantly invested in its U.S. operations to cater to the growing demand for its vehicles. The Subaru of Indiana Automotive (SIA) plant in Lafayette, Indiana, serves as the company's sole manufacturing facility outside of Japan. Established in 1989, this state-of-the-art facility has undergone several expansions and modernizations to enhance its production capacity and efficiency. SIA produces a range of popular models including the Ascent, Impreza, Legacy, and Outback. The strategic location of the Indiana plant allows Subaru to leverage the region's robust logistics infrastructure and skilled workforce. The facility employs thousands of workers and contributes substantially to the local economy through job creation and community development initiatives. Subaru's commitment to quality and innovation is evident in its rigorous testing processes and adherence to stringent safety standards at SIA. Moreover, Subaru's U.S. operations are deeply intertwined with its global supply chain network. The company sources components from various suppliers across North America while also exporting vehicles produced at SIA to international markets. This integration underscores the critical role that U.S.-based manufacturing plays within Subaru's broader global strategy. In addition to its manufacturing prowess, Subaru's presence in the United States reflects its dedication to environmental sustainability. The Indiana plant has been recognized for achieving zero landfill status since 2004—a testament to Subaru's commitment to reducing waste and promoting eco-friendly practices throughout its operations. Overall, Subaru's investment in U.S.-based manufacturing underscores the country's importance as a hub for global automotive production. By combining advanced technology with a skilled workforce and strong logistical support systems, Subaru continues to thrive in an increasingly competitive market while contributing positively to both local communities and the environment at large.
Other Countries
Subaru's global manufacturing facilities extend beyond Japan, reflecting the company's strategic expansion to meet growing demand and leverage local markets. In the United States, Subaru operates a major plant in Lafayette, Indiana, which has been producing vehicles since 1989. This facility is known for its high-quality production standards and has been recognized for its environmental sustainability efforts. The Indiana plant primarily manufactures models such as the Outback, Legacy, and Impreza, catering to both domestic and international markets. In addition to its U.S. operations, Subaru also has a significant presence in other countries. For instance, in China, Subaru partners with local manufacturers to produce select models tailored to the Chinese market. This collaboration allows Subaru to tap into one of the world's largest automotive markets while adhering to local regulations and consumer preferences. Subaru's global footprint also includes Thailand, where it has established a manufacturing base that serves Southeast Asia and other regions. This strategic location enables efficient distribution and caters to the growing demand for vehicles in emerging economies. The Thai facility focuses on producing popular models like the Forester and XV (Crosstrek), ensuring that these vehicles meet regional specifications and regulatory requirements. Furthermore, Subaru's international reach extends into Europe through partnerships with local manufacturers. In the UK, for example, Subaru works closely with retailers who import vehicles from Japan or other global facilities. This approach allows Subaru to maintain a strong presence in European markets without needing large-scale local production facilities. The expansion of Subaru's manufacturing facilities across different countries underscores its commitment to global market penetration while ensuring quality control and adaptability to regional needs. By diversifying its production bases geographically, Subaru can better respond to changing market conditions and consumer preferences worldwide. This strategic approach not only enhances operational efficiency but also positions Subaru as a competitive player in the global automotive industry. Overall, Subaru’s diverse network of global manufacturing facilities is integral to its success as a multinational automaker. By leveraging local resources and expertise while maintaining high standards of quality and innovation, Subaru continues to grow its presence globally while delivering reliable vehicles that meet diverse customer needs around the world.
Production Process Overview
In the modern era of industrial production, understanding the intricacies of the production process is crucial for maintaining efficiency, quality, and competitiveness. This article provides a comprehensive overview of the key stages involved in transforming raw materials into finished products. We delve into three critical components: Design and Prototyping, where innovative ideas are conceptualized and tested; Assembly Line Operations, where precision and speed come together to build products on a large scale; and Quality Control Measures, ensuring that every product meets stringent standards before reaching consumers. By examining these essential phases, manufacturers can optimize their workflows and enhance overall performance. This knowledge is particularly vital for Global Manufacturing Facilities, where consistent excellence is paramount in meeting global demands.
Design and Prototyping
Design and prototyping are pivotal stages in the production process of Subaru vehicles, ensuring that every car meets the highest standards of quality, performance, and safety. The design phase begins with conceptual sketches and computer-aided design (CAD) models, where engineers and designers collaborate to create a blueprint for the vehicle. This stage involves meticulous planning to incorporate innovative features, ergonomic design elements, and aesthetic appeal. Once the design is finalized, it moves into the prototyping phase. Prototyping involves creating physical models of the vehicle to test its functionality, durability, and overall performance. Subaru employs advanced technologies such as 3D printing and simulation software to create detailed prototypes that can be subjected to various tests. These tests include crash simulations, aerodynamic assessments in wind tunnels, and rigorous environmental testing to ensure that the vehicle can withstand extreme conditions. The feedback from these tests is then used to refine the design further. Throughout this iterative process, Subaru's commitment to quality is evident through its adherence to stringent quality control measures. Each prototype undergoes a series of evaluations by a team of experts who scrutinize every aspect from engine performance to interior comfort. This meticulous approach ensures that any potential issues are identified and addressed before mass production begins. Moreover, Subaru's design philosophy emphasizes all-wheel drive capability and boxer engine technology—features that set their vehicles apart in terms of stability and power delivery. The integration of these technologies requires precise engineering during both design and prototyping stages. In summary, Subaru's design and prototyping process is a testament to their dedication towards producing high-quality vehicles that not only meet but exceed customer expectations. By combining cutting-edge technology with rigorous testing protocols, Subaru ensures that every car rolling off their assembly lines is ready for real-world challenges while providing unparalleled driving experiences.
Assembly Line Operations
Assembly line operations are a cornerstone of modern manufacturing, particularly in the automotive industry. This method, pioneered by Henry Ford in the early 20th century, revolutionized production by breaking down complex tasks into simpler, repetitive steps that workers could perform with greater efficiency and accuracy. In Subaru's assembly lines, this principle is meticulously applied to ensure high-quality vehicles are produced consistently. The process begins with meticulous planning and design stages where engineers and technicians map out every detail of the vehicle's construction. Once the blueprint is finalized, raw materials and components are sourced from trusted suppliers to ensure reliability and durability. The actual assembly process involves a series of stations along a moving conveyor belt where workers specialize in specific tasks such as welding, painting, engine installation, and final inspections. Each station is equipped with state-of-the-art machinery and tools designed to optimize productivity while minimizing errors. For instance, robotic arms handle delicate tasks like welding and painting with precision that human hands cannot match. Meanwhile, quality control checks are integrated at various stages to catch any defects early on before they become major issues. Subaru's commitment to quality is evident in its rigorous testing protocols. Vehicles undergo thorough inspections for both mechanical integrity and aesthetic appeal before they are deemed ready for market. Additionally, Subaru incorporates lean manufacturing principles to eliminate waste and streamline processes further. The assembly line also fosters a collaborative work environment where teamwork is essential for smooth operations. Workers are trained not only in their specific roles but also encouraged to contribute ideas for continuous improvement—a practice known as Kaizen in Japanese manufacturing culture. Moreover, Subaru has embraced technological advancements such as Industry 4.0 technologies which integrate digital tools like AI and IoT into their production lines enhancing efficiency even more significantly than traditional methods alone could achieve. In summary; Subaru’s assembly line operations exemplify how combining innovative technology with skilled labor can result in producing high-quality vehicles efficiently while maintaining stringent standards throughout each stage from initial design through final delivery ensuring customer satisfaction globally
Quality Control Measures
Quality control measures are an integral part of the production process at Subaru, ensuring that every vehicle meets the highest standards of performance, safety, and reliability. From the initial design phase to the final assembly line, rigorous quality checks are implemented to guarantee that each component and system functions flawlessly. Subaru's commitment to quality begins with meticulous supplier selection and material inspection. The company only partners with suppliers who adhere to stringent quality criteria, ensuring that all parts are of superior quality before they even reach the manufacturing floor. Once components arrive at the factory, they undergo a series of inspections and tests. This includes visual checks for defects, dimensional verification using advanced metrology tools, and functional testing to ensure proper operation. For instance, engine components are subjected to rigorous performance tests in controlled environments to simulate real-world conditions. Similarly, electronic systems are thoroughly tested for reliability and compatibility. During assembly, quality control technicians monitor every stage of production. They conduct random sampling inspections on finished units as well as continuous monitoring of production lines using advanced technologies like machine vision systems and robotic inspection tools. These technologies enable real-time detection of any anomalies or defects during assembly. Subaru also employs a robust Total Quality Management (TQM) framework that involves all employees in maintaining high standards. Through ongoing training programs and continuous improvement initiatives (Kaizen), workers are empowered to identify areas for improvement and implement changes that enhance overall product quality. Additionally, Subaru adheres strictly to international standards such as ISO 9001 for quality management systems and ISO 14001 for environmental management systems. These certifications underscore the company's dedication not only to producing high-quality vehicles but also to minimizing its environmental footprint. Finally, before any vehicle leaves the factory floor, it undergoes a comprehensive final inspection that includes road tests under various conditions—such as different terrains and weather—to ensure it meets Subaru's stringent performance criteria. This multi-layered approach ensures that every Subaru vehicle delivered to customers is reliable, safe, and performs optimally over its lifespan. In summary, Subaru's rigorous quality control measures are woven into every aspect of its production process—from supplier selection through final inspection—ensuring that each vehicle embodies excellence in engineering and manufacturing. This unwavering commitment to quality has earned Subaru a reputation for producing some of the most reliable cars on the market today.
Technological Innovations in Manufacturing
The advent of technological innovations has revolutionized the manufacturing sector, transforming traditional production methods into highly efficient and sustainable processes. At the forefront of this transformation are Automated Production Systems, which leverage advanced robotics and artificial intelligence to streamline operations and enhance productivity. Concurrently, Sustainable Manufacturing Practices are gaining prominence as companies adopt eco-friendly technologies to reduce their environmental footprint. Additionally, the integration of Advanced Material Usage is enabling the creation of lighter, stronger, and more versatile products. These advancements are not only improving manufacturing outcomes but also setting new standards for global competitiveness. As these innovations continue to shape the industry, their impact will be felt across Global Manufacturing Facilities.
Automated Production Systems
Automated Production Systems (APS) represent a pivotal technological innovation in manufacturing, significantly enhancing efficiency, precision, and productivity. These systems integrate advanced robotics, artificial intelligence (AI), and machine learning algorithms to streamline production processes. By automating repetitive tasks and complex operations, APS reduces human error while increasing the speed of production. For instance, in the automotive industry, automated assembly lines equipped with robotic arms can perform tasks such as welding, painting, and assembly with unparalleled accuracy and speed. Additionally, AI-driven predictive maintenance within APS ensures that machinery is serviced before potential failures occur, minimizing downtime and optimizing overall plant performance. The integration of Internet of Things (IoT) devices further enhances real-time monitoring and data analytics capabilities, allowing for continuous improvement in manufacturing processes. Overall, Automated Production Systems are transforming the manufacturing landscape by providing scalable solutions that meet the demands of modern production environments while ensuring high-quality output consistently.
Sustainable Manufacturing Practices
Sustainable manufacturing practices are a cornerstone of modern industrial operations, particularly in the automotive sector. As companies like Subaru strive to reduce their environmental footprint, they are increasingly adopting innovative technologies that not only enhance efficiency but also promote sustainability. One key area is the use of renewable energy sources such as solar and wind power to power manufacturing facilities. Subaru's factories in Japan and the United States have integrated these green energy solutions, significantly reducing reliance on fossil fuels and lowering carbon emissions. Another significant advancement is the implementation of circular economy principles. Subaru has embraced recycling and reusing materials in its production processes, minimizing waste and conserving resources. For instance, the company has developed closed-loop systems where materials from end-of-life vehicles are collected and recycled back into new products. This approach not only reduces landfill waste but also decreases the demand for raw materials. Additionally, technological innovations in manufacturing have enabled more precise control over production processes, leading to reduced energy consumption and lower emissions. Advanced robotics and artificial intelligence (AI) are being used to optimize workflows, detect inefficiencies, and predict maintenance needs before they become major issues. These technologies ensure that machinery operates at peak performance levels while minimizing downtime. Water conservation is another critical aspect of sustainable manufacturing practices at Subaru. The company has implemented water-saving technologies such as rainwater harvesting systems and advanced filtration processes that allow for the reuse of water in various stages of production. This not only conserves this precious resource but also reduces wastewater generation. Furthermore, sustainable supply chain management plays a crucial role in Subaru's commitment to environmental stewardship. The company works closely with suppliers who adhere to stringent environmental standards, ensuring that all components used in their vehicles are sourced responsibly. This includes sourcing materials from certified sustainable forests for interior components like wood trim. In conclusion, Subaru's commitment to sustainable manufacturing practices underscores its dedication to both technological innovation and environmental responsibility. By leveraging renewable energy sources, adopting circular economy principles, optimizing production processes through advanced technologies, conserving water resources, and managing supply chains responsibly, Subaru sets a high standard for sustainability within the automotive industry. These efforts not only contribute positively towards mitigating climate change but also enhance operational efficiency and brand reputation.
Advanced Material Usage
Advanced material usage is a pivotal aspect of technological innovations in manufacturing, particularly in the automotive industry. Subaru, known for its commitment to quality and innovation, leverages cutting-edge materials to enhance the performance, safety, and sustainability of its vehicles. One notable example is the use of high-strength steel in their vehicle bodies. This advanced material significantly reduces weight while maintaining structural integrity, thereby improving fuel efficiency and reducing emissions. Additionally, Subaru incorporates advanced composites such as carbon fiber and aluminum alloys into various components to further optimize weight distribution and enhance overall vehicle dynamics. Moreover, Subaru's adoption of advanced materials extends beyond structural components. The company integrates sophisticated materials into engine design to improve thermal efficiency and reduce friction. For instance, the use of ceramic-coated cylinder liners minimizes wear on moving parts, leading to longer engine life and better fuel economy. Furthermore, Subaru's focus on sustainability drives the incorporation of eco-friendly materials in interior design. Recycled plastics and biodegradable polymers are increasingly used in dashboard trim, seat upholstery, and other interior components. The integration of advanced materials also plays a crucial role in enhancing vehicle safety features. Subaru's EyeSight driver-assist system relies on high-resolution cameras made from advanced glass materials that provide clear vision under various lighting conditions. Similarly, the company's use of advanced polymers in airbags ensures rapid deployment while maintaining structural integrity during impact. In conclusion, Subaru's strategic deployment of advanced materials underscores its commitment to technological innovation in manufacturing. By continuously exploring new material technologies and integrating them into their production processes, Subaru not only improves the performance and safety of their vehicles but also contributes significantly to environmental sustainability efforts. This forward-thinking approach positions Subaru at the forefront of automotive manufacturing innovation.